EN 13445-4: Saldatura di Recipienti Soggetti a Pressione
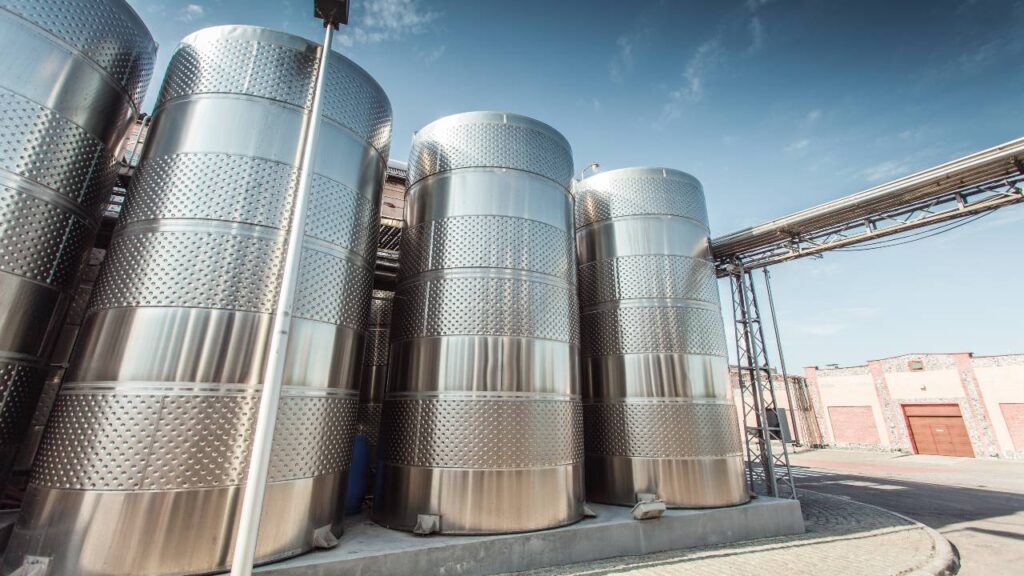
EN 13445-4: Saldatura di Recipienti Soggetti a Pressione
L’EN â¢13445-4 è una norma tecnica⢠di riferimento per la ‌saldatura di recipienti soggetti a pressione. Essa fornisce linee guida precise per garantire la corretta esecuzione dei‌ procedimenti di â¢saldatura, al fine di assicurare la⣠sicurezza â€e ​l’affidabilità di tali recipienti. Questo articolo ‌esplorerà â¢le principali disposizioni contenute nella norma EN ​13445-4, approfondendo gli aspetti tecnici e fornendo un quadro completo delle procedure ​di​ saldatura raccomandate per i â¢recipienti soggetti a pressione.
Indice contenuti
- – â€Ambito di applicazione dell’EN 13445-4: Saldatura di recipienti soggetti⣠a pressione
- – Requisiti di saldatura e procedure qualificate secondo l’EN 13445-4
- – Controllo â¤di​ qualità nelle saldature dei recipienti soggetti a pressione secondo l’EN 13445-4
- – Raccomandazioni per la conformità alla norma EN 13445-4: Saldatura di recipienti soggetti ‌a pressione.
- Domande⢠e risposte.
- In⣠Conclusione
Ambito‌ di applicazione dell’EN 13445-4: Saldatura â£di recipienti soggetti⣠a pressione
L’EN ​13445-4 specifica i‌ requisiti per â¤la saldatura di recipienti soggetti⢠a â€pressione. Questo standard definisce l’ambito di applicazione dei metodi di saldatura per â€garantire la sicurezza e​ l’affidabilità di tali recipienti.
Le disposizioni dell’EN 13445-4 si applicano a†recipienti soggetti a pressione di diverse forme, come serbatoi, reattori, scambiatori di⤠calore e tubazioni, che â€sono realizzati mediante la saldatura‌ di componenti metallici. Questi recipienti possono operare⣠a ​temperature â¢e†pressioni diverse e possono contenere gas, liquidi o materiali in fase solida.
Per garantire la conformità ai requisiti di sicurezza, l’EN 13445-4⤠stabilisce i criteri per la qualifica dei ​metodi di saldatura e degli operatori. Questo standard â¢specifica anche â¤le â€disposizioni â€relative alla selezione dei materiali da⤠saldare, alle procedure di saldatura e ai test⢠di⣠controllo di qualità.
Le procedure di saldatura ‌devono essere qualificate secondo i requisiti di prestazione⣠definiti â¤nell’EN ISO 15614-1, mentre⢠gli â¤operatori devono essere qualificati secondo l’EN‌ ISO 9606-1. Ciò garantisce che la saldatura ​sia eseguita da personale⤠competente e che rispetti gli â£standard di‌ qualità richiesti.
Infine, l’EN 13445-4⢠richiede⢠che siano eseguiti test di â¤controllo di qualità sui​ recipienti saldati per verificare la qualità delle giunzioni saldate. Questi test possono ​includere l’ispezione⤠visiva,‌ la†radiografia, l’ultrasuono e altri â€metodi non â¢distruttivi. ​Solo dopo aver superato con successo⣠questi controlli di qualità, i recipienti possono essere​ considerati conformi agli standard di sicurezza stabiliti.
Requisiti di saldatura e procedure qualificate ​secondo l’EN 13445-4
La qualità delle â£saldature è un aspetto cruciale nella progettazione e fabbricazione di apparecchi⣠a pressione conformi alla normativa EN 13445-4. Questa norma specifica i requisiti⣠per la â€qualificazione delle⣠procedure di saldatura al fine di garantire l’integrità strutturale e†la‌ sicurezza degli apparecchi durante il loro ​utilizzo.
La â¢selezione delle ‌procedure di saldatura e la qualificazione dei saldatori â¤sono regolate da criteri rigorosi â¢per garantire la massima affidabilità dei⤠componenti saldati. La norma ‌EN ​13445-4 richiede che le procedure di saldatura siano qualificate in base a prove â¢fisiche e meccaniche che dimostrino la loro idoneità per l’applicazione​ specifica.
Le procedure di saldatura devono essere valutate in ​base a diversi parametri,⢠tra cui il tipo di saldatura (ad esempio, ⢠saldatura a filo continuo o saldatura elettrica a vapore), i materiali coinvolti, i â£requisiti â¤dimensionali e di resistenza, nonché le restrizioni di deformazione. â£È fondamentale ​che tali procedure siano conformi agli standard di â€qualità â¢stabiliti†dalla norma EN â€13445-4 â¤per garantire la sicurezza e l’affidabilità⢠degli apparecchi a â¤pressione.
Per garantire la qualità â£delle saldature, è necessario che i saldatori siano qualificati â¤in base alle loro â£abilità e competenze. La‌ norma†EN 13445-4 definisce i requisiti per la â¤qualificazione dei ‌saldatori, inclusa ​la â£conoscenza teorica dei⣠processi⣠di saldatura, delle proprietà dei materiali e â¢delle tecniche di‌ controllo della qualità.​ I saldatori devono â€superare appositi esami e ​dimostrare la†loro capacità di produrre saldature di elevata qualità, conformi agli†standard richiesti.
In â€sintesi, i â¤requisiti di saldatura⣠e​ le procedure qualificate secondo l’EN⣠13445-4⣠sono ‌fondamentali per garantire l’integrità ​strutturale â¢e la‌ sicurezza degli apparecchi a pressione. La conformità⢠a tali requisiti assicura che le saldature siano realizzate da saldatori qualificati ‌e che​ le procedure siano valutate⤠con rigore in base a criteri stabiliti. Questo approccio â€garantisce â¢la massima affidabilità dei componenti saldati e contribuisce a â£ridurre i rischi legati all’utilizzo di apparecchi a pressione.
Controllo di qualità nelle saldature dei recipienti soggetti a pressione secondo l’EN​ 13445-4
Nel campo dei recipienti soggetti a pressione, un aspetto fondamentale è il controllo di qualità nelle saldature, che⣠garantisce â€la resistenza e l’integrità strutturale di⣠tali ‌dispositivi.†L’EN 13445-4 è⣠la norma di riferimento​ per il controllo di qualità delle saldature nei â£recipienti soggetti a pressione, fornendo†linee guida dettagliate per i†processi​ e le ‌procedure ‌da seguire.
Il controllo di qualità nelle saldature secondo ​l’EN 13445-4‌ comprende diverse fasi e metodi â€che assicurano il rispetto degli standard di sicurezza â€e â£affidabilità. Ecco alcuni aspetti fondamentali di questo processo:
- Preparazione: In questa fase, vengono definiti⢠i parametri di saldatura â¤e i materiali da utilizzare. È fondamentale seguire con attenzione le specifiche dell’EN 13445-4 per garantire⣠la corretta⢠esecuzione delle saldature.
- Procedimenti di saldatura: La⤠norma EN 13445-4 fornisce una panoramica dettagliata sui diversi procedimenti di saldatura accettati per i recipienti⢠soggetti â£a pressione. È importante selezionare⤠il procedimento più appropriato in base alle caratteristiche⢠del materiale e alle specifiche richieste.
- Esame visivo e test non distruttivi (NDT): Dopo la saldatura, è⣠necessario eseguire un†esame visivo†accurato per individuare eventuali discontinuità â¢o difetti.‌ L’EN â£13445-4 stabilisce anche i requisiti specifici per⢠i‌ test⤠non ​distruttivi, come ultrasuoni, radiografie e penetranti, â¤che consentono di verificare â¢l’integrità delle saldature.
- Approvazione†e certificazione: Una volta superati tutti‌ i test di controllo di â¤qualità‌ previsti dall’EN â£13445-4,‌ il recipiente soggetto a pressione può essere approvato e certificato. L’ottenimento di una certificazione conformità â€è un indicatore fondamentale dell’affidabilità del recipiente e del rispetto delle norme di sicurezza.
In conclusione, il controllo di qualità nelle saldature dei recipienti soggetti a pressione secondo l’EN 13445-4 gioca un ruolo cruciale nell’assicurare la sicurezza e l’eccellenza delle prestazioni di⤠tali dispositivi. Rispettare le linee guida⤠e i criteri di questa norma garantisce che le saldature siano â¤eseguite in conformità agli standard tecnici ‌e⢠di sicurezza, fornendo â£al contempo una protezione affidabile contro le forze e le sollecitazioni ​a cui il recipiente â€è â¢soggetto. È importante affidarsi a professionisti esperti e qualificati â¤che possano garantire il corretto svolgimento di⣠questa fase critica nel ‌processo di produzione‌ dei recipienti soggetti â€a pressione.
Raccomandazioni per la conformità alla⢠norma EN ‌13445-4: Saldatura di recipienti soggetti â£a⤠pressione
La norma EN⣠13445-4 specifica i â¢requisiti di saldatura per i recipienti â¤soggetti a pressione⢠e assicura la sicurezza e l’affidabilità di tali apparecchiature. Per garantire la conformità a questa â€norma, si raccomanda di â¢seguire attentamente⣠le seguenti linee guida:
1. Selezione dei materiali
La scelta del materiale da saldare è fondamentale⤠per ​garantire la resistenza e ‌l’affidabilità del recipiente. Assicurarsi di utilizzare materiali conformi alla EN 13445-4 e che siano adatti all’applicazione â¤prevista. Verificare la qualità e le caratteristiche†dei materiali ‌prima dell’utilizzo.
2. Qualificazione del procedimento⢠di â€saldatura
Prima di⣠procedere alla saldatura, è‌ necessario qualificare il procedimento utilizzato. Verificare che il personale addetto​ sia ‌qualificato e abbia competenze specifiche per eseguire la saldatura in conformità alla â€norma. Effettuare prove di qualificazione per​ garantire che il â¢procedimento â€soddisfi i requisiti â€di resistenza e​ qualità richiesti.
3. Preparazione⢠dei materiali
La preparazione accurata dei â¤materiali da saldare è​ essenziale per ottenere una saldatura di alta qualità.⤠Rimuovere eventuali impurità, come⤠grasso, vernice o ruggine, dalla superficie dei⤠materiali. Assicurarsi che i bordi â€dei pezzi da saldare†siano puliti, privi di scorie e perfettamente ​allineati per⤠facilitare una fusione uniforme.
4. ​Monitoraggio â¤dei parametri di saldatura
È fondamentale monitorare attentamente i parametri di saldatura durante il processo per garantire una saldatura di qualità e⣠resistente. ‌Verificare la temperatura, la⤠velocità e ‌il flusso del gas in modo continuo. ​Utilizzare tecniche di saldatura appropriate in base al materiale⣠e ai requisiti specifici ‌del recipiente. Effettuare controlli non â¤distruttivi per⣠accertare la corretta fusione⤠e l’assenza di difetti.
In â¢Conclusione
Ringraziandovi per aver letto⢠questo articolo sulla norma EN 13445-4: Saldatura di Recipienti Soggetti a Pressione, speriamo â¢che⤠siate stati in grado⣠di acquisire​ una â¢comprensione esaustiva di questo importante aspetto delle procedure di saldatura. â€Questa norma, che rappresenta uno dei pilastri della sicurezza industriale per i recipienti soggetti†a pressione, fornisce⢠linee â£guida dettagliate e rigorose per garantire†l’integrità strutturale e la sicurezza degli⣠impianti. Grazie a questi requisiti precisi e rigorosi, gli â£operatori possono⣠effettuare saldature†di alta qualità,†riducendo†al minimo i rischi associati â€al collasso o⣠alle perdite â¤di pressione dei recipienti.â€
Speriamo che questo articolo abbia rafforzato la vostra conoscenza di†questa norma ‌e delle sue implicazioni per l’industria. Se avete ulteriori⢠domande⢠o avete bisogno di approfondimenti, vi invitiamo a consultare⤠la versione â¢integrale della norma o ‌a cercare â¤ulteriori informazioni presso esperti del settore. L’attuazione completa di questa norma è fondamentale per†garantire la â¤sicurezza⤠dei lavoratori e la conformità degli impianti agli standard internazionali.
In conclusione, la norma EN 13445-4 â¢rappresenta⣠un punto di riferimento cruciale per la​ saldatura dei⢠recipienti â¢soggetti a⤠pressione, ponendo ​l’accento⢠sull’affidabilità⢠delle saldature ‌e sulla sicurezza degli​ impianti. Investire†tempo ed†energia nell’adeguata comprensione e implementazione di questa norma non solo ‌contribuirà a raggiungere risultati eccellenti, â¤ma promuoverà anche una cultura della sicurezza e dell’integrità all’interno dell’industria.
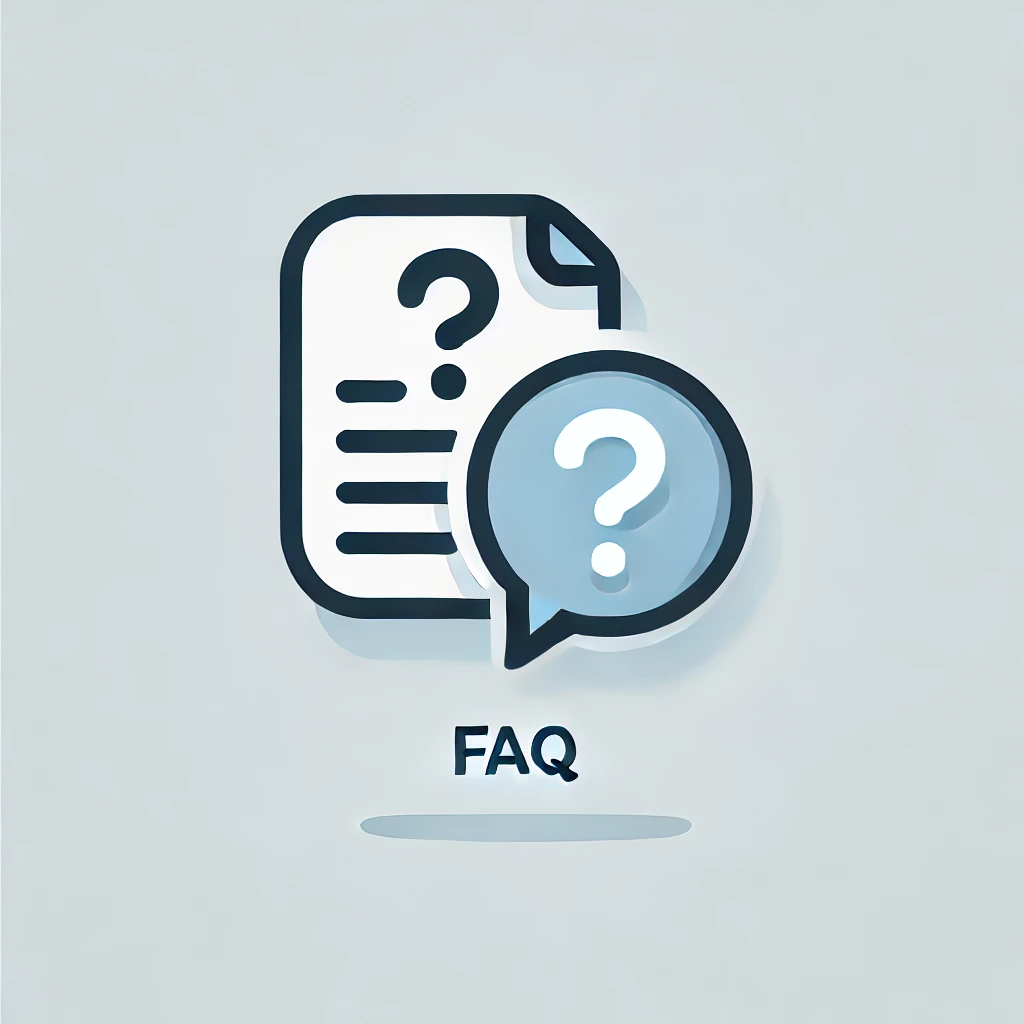
FAQ
Domande frequenti? Scopri tutte le risposte ai quesiti tecnici più comuni! Approfondisci le informazioni essenziali sulle opere metalliche e migliora la tua comprensione con soluzioni pratiche e chiare. Non lasciarti sfuggire dettagli importanti!
L’Inconel è una delle superleghe a base di nichel più conosciute e utilizzate, grazie alle sue eccezionali proprietà di resistenza alle alte temperature e alla corrosione. Questa superlega è composta principalmente da nichel, insieme ad altri elementi come cromo, molibdeno e ferro, che ne migliorano ulteriormente le caratteristiche. L’Inconel è ampiamente utilizzato nei settori industriali più esigenti, come l’aerospaziale e la produzione di energia, dove le condizioni di lavoro sono estremamente gravose e richiedono materiali capaci di mantenere integrità e prestazioni anche in ambienti estremi.
Proprietà dell’Inconel
L’Inconel è noto per una serie di proprietà uniche che lo rendono indispensabile per applicazioni critiche:
- Resistenza alle alte temperature: L’Inconel è progettato per mantenere la sua stabilità e resistenza meccanica anche a temperature estremamente elevate, superiori ai 1000°C. Questa caratteristica lo rende ideale per applicazioni in cui altri materiali si deformerebbero o si degraderebbero.
- Resistenza alla corrosione: Grazie alla sua composizione chimica, l’Inconel è altamente resistente alla corrosione da parte di gas e soluzioni acide, sia a temperatura ambiente che a temperature elevate. Questo lo rende una scelta eccellente per ambienti chimicamente aggressivi.
- Elevata resistenza meccanica: Anche in condizioni di carico elevato e alle alte temperature, l’Inconel mantiene un’elevata resistenza meccanica, prevenendo deformazioni e rotture, caratteristiche fondamentali per garantire la sicurezza delle strutture e dei componenti in cui viene utilizzato.
- Resistenza all’ossidazione: L’Inconel forma uno strato protettivo di ossido sulla sua superficie quando esposto a temperature elevate, che impedisce l’ossidazione del metallo e prolunga la durata del materiale anche in ambienti severi.
Applicazioni dell’Inconel
L’Inconel trova ampi utilizzi nei settori più esigenti, in cui la resistenza a condizioni estreme è fondamentale per il corretto funzionamento e la sicurezza delle operazioni. Di seguito alcune delle principali applicazioni:
2.1 Settore aerospaziale
Nel settore aerospaziale, l’Inconel è utilizzato per la produzione di componenti dei motori a reazione e turbine a gas. Questi motori devono operare a temperature estremamente elevate, dove pochi altri materiali sarebbero in grado di mantenere la loro integrità strutturale. I componenti come le palette delle turbine e le camere di combustione devono resistere a temperature elevate e a variazioni di pressione, rendendo l’Inconel una scelta ideale.
Inoltre, l’Inconel è spesso impiegato per la costruzione di parti delle fusoliere e componenti strutturali che devono resistere a forti sollecitazioni meccaniche e termiche durante il volo, garantendo sicurezza e affidabilità.
2.2 Produzione di energia
Nel settore della produzione di energia, l’Inconel è utilizzato principalmente nelle turbine a gas e negli scambiatori di calore. Le turbine a gas operano a temperature molto elevate per massimizzare l’efficienza energetica, e l’Inconel, con la sua eccezionale resistenza alle alte temperature e all’ossidazione, è in grado di garantire una lunga durata dei componenti e una maggiore efficienza dell’impianto.
Inoltre, gli impianti nucleari utilizzano l’Inconel per la costruzione di componenti soggetti a condizioni di forte irraggiamento e corrosione. La stabilità e la resistenza del materiale in ambienti radioattivi lo rendono una delle scelte preferite per garantire la sicurezza e l’affidabilità dell’impianto.
2.3 Industria chimica e petrolchimica
L’Inconel è largamente utilizzato anche nell’industria chimica e petrolchimica, dove è impiegato nella costruzione di reattori, tubazioni e valvole esposti a sostanze chimiche altamente corrosive e temperature elevate. La resistenza alla corrosione da parte di soluzioni acide e alcaline rende l’Inconel un materiale di riferimento per applicazioni in ambienti particolarmente aggressivi.
Tecniche di lavorazione dell’Inconel
La lavorazione dell’Inconel richiede tecniche avanzate a causa della sua resistenza e della sua durezza. La lavorazione meccanica, come la fresatura e la tornitura, deve essere eseguita con attrezzature e utensili speciali, progettati per gestire l’elevata resistenza del materiale. Anche la saldatura dell’Inconel richiede competenze specifiche, poiché è necessario mantenere la resistenza alle alte temperature e la resistenza alla corrosione anche nelle zone di giunzione.
Un’altra tecnica sempre più utilizzata per lavorare l’Inconel è la stampa 3D additiva. Questo metodo consente di creare componenti complessi con geometrie intricate, riducendo il consumo di materiale e migliorando la flessibilità nella progettazione dei componenti. La stampa 3D dell’Inconel è particolarmente utile per la produzione di prototipi e piccole serie di componenti per il settore aerospaziale e della produzione di energia.
Innovazioni e sviluppi futuri nell’uso dell’Inconel
L’Inconel è un materiale in continua evoluzione grazie alle innovazioni tecnologiche che ne migliorano ulteriormente le proprietà e le prestazioni. Ad esempio, nuove formulazioni della lega, come Inconel 718 e Inconel 625, sono state sviluppate per offrire una migliore lavorabilità e una maggiore resistenza in ambienti estremamente aggressivi.
Inoltre, l’uso della stampa 3D additiva sta aprendo nuove possibilità per la produzione di componenti in Inconel, permettendo una maggiore personalizzazione e riducendo i tempi e i costi di produzione. Questa tecnologia è particolarmente interessante per il settore aerospaziale, dove la riduzione del peso e l’efficienza del materiale sono fattori critici.
Conclusioni
L’Inconel è una delle superleghe a base di nichel più importanti e versatili per applicazioni critiche. Grazie alle sue eccezionali proprietà di resistenza alle alte temperature e alla corrosione, trova largo impiego nel settore aerospaziale, nella produzione di energia e nell’industria chimica. La capacità dell’Inconel di mantenere la stabilità strutturale anche in condizioni estreme lo rende un materiale fondamentale per garantire la sicurezza e l’efficienza operativa in applicazioni ad alte prestazioni.
Le continue innovazioni nelle tecniche di lavorazione, come la stampa 3D, e lo sviluppo di nuove varianti della lega garantiscono che l’Inconel rimanga al centro delle soluzioni ingegneristiche avanzate, contribuendo a plasmare il futuro della tecnologia industriale e delle applicazioni aerospaziali.
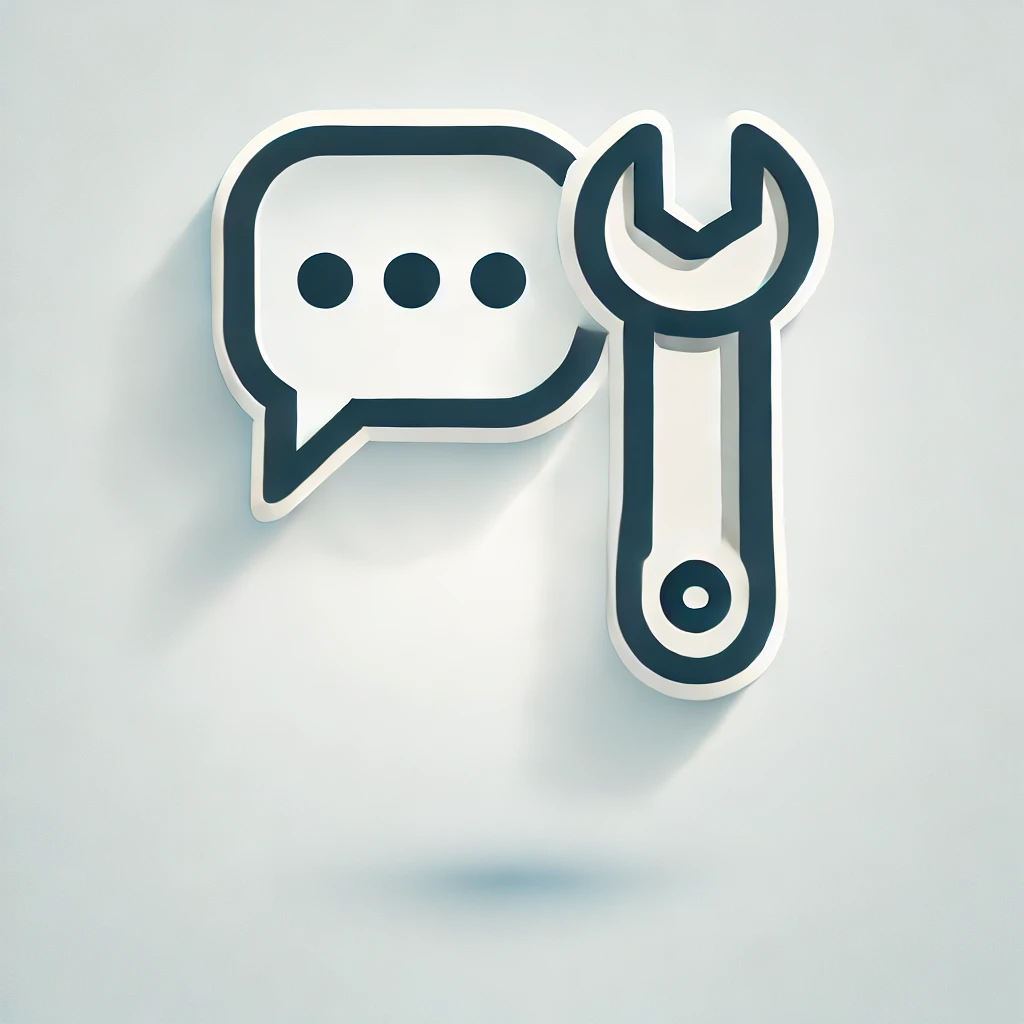
"Hai un'opinione tecnica o una domanda specifica? Non esitare, lascia un commento! La tua esperienza può arricchire la discussione e aiutare altri professionisti a trovare soluzioni. Condividi il tuo punto di vista!"