EN 15085: Certificazione Qualità per la Saldatura su Veicoli Ferroviari

EN 15085: Certificazione Qualità per la Saldatura su Veicoli Ferroviari
Introduzione:
Con l’aumento della†domanda di trasporto su rotaia, l’industria dei veicoli⢠ferroviari â€si⣠è trovata ad affrontare sfide sempre â¤più⣠complesse nell’assicurare la sicurezza e l’affidabilità dei propri prodotti.⣠La saldatura,‌ in particolare, â£è⤠un elemento cruciale nella costruzione dei veicoli ferroviari e richiede l’adeguata certificazione di qualità per garantire l’integrità delle giunzioni. In​ questo contesto, spicca l’importanza della normativa⣠EN 15085, che disciplina â€i requisiti per la⢠saldatura su â¤veicoli ‌ferroviari. Questo articolo si​ propone di fornire⢠una panoramica dettagliata della certificazione di â€qualità secondo la normativa EN 15085, â€sottolineando l’importanza†di â£questo standard nel settore dei‌ veicoli ferroviari e il suo impatto sulla⢠sicurezza e l’affidabilità delle‌ infrastrutture ferroviarie.
Introduzione all’EN ​15085: Certificazione Qualità per ​la Saldatura​ su⢠Veicoli Ferroviari
La â¤norma EN 15085 è†un riferimento essenziale per tutte le aziende coinvolte nella saldatura di veicoli ferroviari. Questo standard†tecnico definisce i​ requisiti di qualità che devono essere soddisfatti per garantire â£la sicurezza e⤠l’affidabilità delle saldature utilizzate in​ questo settore. Vediamo quindi nel⣠dettaglio ​i principali aspetti e vantaggi connessi all’implementazione di ‌questa â€normativa.
La â¤certificazione ‌secondo⣠l’EN⤠15085 si basa ​su un⢠sistema di classificazione che definisce‌ le competenze richieste ai professionisti coinvolti⤠nella saldatura di veicoli ferroviari. Tale ​approccio mirato a garantire​ un livello ‌di eccellenza nella produzione â¢di⣠saldature evita possibili difetti e assicura che i ‌veicoli ferroviari soddisfino i più alti standard â€di qualità e sicurezza.
Adottare la certificazione EN 15085 offrirà⢠numerosi vantaggi per ‌le aziende⣠operanti nel settore della saldatura di veicoli ferroviari.†Tra i principali ‌benefici, si può citare l’aumento della​ fiducia‌ del‌ cliente,​ grazie​ alla†garanzia di un processo di saldatura gestito in maniera conforme agli standard⣠internazionali â€di â¤qualità e sicurezza.
Un altro punto⣠di⤠forza dell’EN 15085 è la†sua flessibilità. Questo standard può†essere⣠applicato a diverse procedure⢠di saldatura, dai veicoli di â£superficie agli‌ equipaggiamenti interni ai treni o anche ai componenti strutturali. In questo modo, le aziende che â€si â¤occupano della â£saldatura di ​veicoli ‌ferroviari possono adattare la certificazione alle loro esigenze specifiche senza compromettere la qualità†e la sicurezza.
La certificazione secondo l’EN ​15085 â¢richiede rigorosi controlli e test sia sulle ‌procedure di saldatura che​ sui materiali utilizzati. â€Questo approccio ‌basato â€sulla qualità permette alle⢠aziende di​ individuare‌ tempestivamente eventuali‌ difetti⣠o problemi nelle saldature, prevendendo così il verificarsi ​di malfunzionamenti â¤o incidenti durante l’utilizzo ​dei veicoli ferroviari.
Un â£altro aspetto​ importante​ dell’EN 15085 è il suo ruolo†nella promozione dell’innovazione e dello sviluppo tecnologico. Questa normativa, infatti, incoraggia le⣠aziende a utilizzare â€le più avanzate tecnologie di saldatura, consentendo loro di ‌rimanere competitive â¤sul mercato ‌globale nel settore dei veicoli â€ferroviari.
Mantenere costantemente ​aggiornata​ la‌ certificazione â£secondo ​l’EN 15085 è fondamentale per garantire la conformità ai requisiti internazionali di qualità e⢠sicurezza. Le aziende che â£ottengono questa certificazione â¤dimostrano di essere​ affidabili e â¤orientate all’eccellenza nella produzione di saldature per veicoli⣠ferroviari, offrendo â£un vantaggio competitivo significativo ​rispetto‌ ai ​concorrenti.
In â€conclusione, l’EN â¢15085 rappresenta uno degli aspetti⣠fondamentali†da considerare⤠nel settore della​ saldatura di veicoli ferroviari. ​Questa certificazione di qualità mette in ‌risalto l’importanza di ‌un’attenta gestione e controllo â¤delle â£procedure di â¤saldatura, promuovendo la⣠sicurezza, l’affidabilità e il rispetto​ degli standard â¤internazionali in â¤questo â£campo.
Requisiti fondamentali della norma EN 15085⣠per la†saldatura‌ sui veicoli ferroviari
La ‌norma EN†15085 rappresenta un punto di riferimento fondamentale nel settore â£della‌ saldatura⣠sui veicoli ‌ferroviari,⤠definendo ​gli​ standard di qualità â¢e‌ sicurezza â¢che â¢devono essere rispettati. Tale â€normativa stabilisce i⣠requisiti essenziali per⣠la produzione di giunti saldati critici nel ​settore ferroviario, garantendo la conformità dei⣠procedimenti â£di saldatura e dei fabbricati⢠alle ‌esigenze di â£prestazione richieste.
I principali requisiti della â€norma EN†15085 riguardano la qualificazione del â¢personale coinvolto nel â¢processo di saldatura, â¢i materiali utilizzati, la â¢certificazione dei procedimenti di saldatura stessi e il controllo â¤della qualità. Uno dei punti centrali della norma è ‌la valutazione e l’approvazione delle procedure di saldatura, che devono essere⢠conformi ai parametri specificati e â£alle condizioni imposte dalla⣠normativa.
La corretta formazione del personale è un aspetto ‌cruciale nell’ambito della â¢saldatura sulle vetture ferroviarie. La norma EN 15085 richiede che gli operatori siano adeguatamente â¤formati, â€possiedano competenze specifiche nel settore ferroviario e siano in grado â€di dimostrare la loro qualificazione attraverso​ appositi certificati. Ciò garantisce che il personale possieda le competenze richieste per‌ effettuare le saldature in modo sicuro â¤ed efficiente.
Per â¤quanto riguarda i materiali, la norma⤠EN 15085 fornisce dettagliate specifiche‌ sulle ‌leghe,⣠i â¢metalli base⣠e⢠i materiali di riempimento adatti ​alla⣠saldatura nel settore ferroviario. â£È fondamentale⢠utilizzare materiali†idonei che siano conformi alle specifiche​ richieste â¤per garantire†la resistenza e la durata‌ delle saldature nel⤠tempo.
La certificazione⤠dei procedimenti di saldatura ‌è â¢un ​aspetto â£cruciale da rispettare per garantire la conformità ai requisiti della norma EN 15085. I processi di saldatura â€devono essere valutati e approvati‌ da un organismo di certificazione ​indipendente, il quale verifica â€che le â£procedure rispettino i requisiti â¢richiesti in⣠termini di materiali,⣠metodi⤠di​ saldatura e controlli di qualità.
La verifica‌ della qualità delle saldature è un punto chiave‌ nel rispetto della​ norma EN 15085.⣠I produttori devono implementare un adeguato sistema di controllo qualità, che preveda l’ispezione â¢visiva, â¤la†prova non distruttiva e il‌ collaudo delle saldature â¤realizzate sui veicoli ferroviari.â¢ È fondamentale​ effettuare controlli†accurati ‌per garantire la conformità†e⢠l’integrità delle giunzioni⢠saldate.
La norma EN 15085 sottolinea l’importanza​ della documentazione e⣠della gestione â¢dei registri relativi alla†saldatura sui â¤veicoli ferroviari. È necessario tenere traccia di ‌tutte le fasi del processo di saldatura, inclusi â€i⤠materiali ‌utilizzati,⤠i risultati dei â¤controlli non distruttivi e le â¤certificazioni rilasciate. Questi registri consentono di â€monitorare la ‌qualità delle saldature†nel tempo e di fornire â€evidenze‌ in caso di necessità.
In conclusione, la â¢norma ‌EN â£15085⣠rappresenta un insostituibile†riferimento nel settore della†saldatura‌ sui⤠veicoli ferroviari. Questa normativa‌ fornisce le linee guida essenziali â€per garantire ​saldature sicure, resistenti e conformi agli standard richiesti nel settore ferroviario, contribuendo a ‌garantire â¢l’affidabilità e la â£durabilità dei veicoli per†il trasporto su rotaia.
Classificazione dei processi di​ saldatura secondo la norma EN 15085
La norma EN 15085 è stata sviluppata per classificare i processi di saldatura â€utilizzati nell’industria â¤ferroviaria. Questa norma fornisce‌ una â¤guida â¢dettagliata per garantire⣠la qualità e la ‌sicurezza⢠dei prodotti e‌ delle componenti saldate.
La si basa su diversi fattori,⣠tra cui il tipo ​di materiale, â£la tipologia di giunto da saldare e la â£qualificazione richiesta per gli â€operatori di saldatura.
La norma prevede quattro classi‌ di processi di saldatura:
- Classe A: ​questa classe â£si applica ai giunti â£di saldatura critici,⣠ad esempio â¢quelli ​situati in â€prossimità di â€zone â£di raccordo e†di â€giunzioni di​ diversi materiali. I processi di saldatura della classe A richiedono la ‌massima qualità e i⤠più alti livelli di†competenza degli â£operatori di saldatura.
- Classe B: â£questa⤠classe si applica ai​ giunti di⣠saldatura importanti, ​ma non critici come quelli​ situati in ​zone⣠non â€soggette a sollecitazioni elevate.‌ I processi di saldatura â£della‌ classe B ​richiedono una â€qualità elevata†e†competenze adeguate degli operatori â¤di saldatura.
- Classe C:​ questa classe si applica â€ai giunti di saldatura di bassa⤠importanza, come quelli che ​non sono â€esposti a⤠sollecitazioni significative o in†particolari aree⣠di â¢un prodotto. I â¤processi di â€saldatura della†classe C richiedono⢠una†qualità accettabile e competenze di base â¤degli operatori â£di saldatura.
- Classe†D: â¢questa â¢classe ‌si ​applica a giunti di saldatura non critici, come quelli ​che non sono soggetti a sollecitazioni o a requisiti‌ di qualità particolari. I processi di saldatura della classe D richiedono solo una qualità minima⤠e competenze di base.
Per ogni⤠classe di⤠processo di saldatura, la norma⢠EN 15085 definisce requisiti dettagliati per i materiali, ​le â€procedure⣠di saldatura, il controllo non â€distruttivo (CND) e le⤠qualifiche dell’operatore di saldatura.
La norma prevede â£anche la necessità di​ eseguire prove specifiche, come prove di trazione, prove di piegatura​ e ‌prove di â€impatto, â£per valutare la qualità dei â£giunti ‌saldati. Queste â£prove devono â€essere ‌eseguite da â¤un laboratorio di prova‌ certificato e i risultati devono essere conformi†ai⣠requisiti ​specificati⤠nella norma.
Al⢠fine⤠di garantire ​che â£i prodotti e le componenti â€saldate soddisfino le esigenze di sicurezza e qualità‌ previste dalla norma EN‌ 15085, è essenziale che le imprese utilizzino i processi di saldatura appropriati per ogni classe â¤di†giunto â€e seguano scrupolosamente â¤i requisiti dettagliati della ​norma.
Requisiti â€per la qualificazione dei â¢saldatori â£nell’ambito dell’EN ‌15085
I ‌seguenti â£sono i :
1. Competenze professionali:
- Capacità di interpretare i disegni tecnici e â¢i â¤simboli di ​saldatura
- Conoscenza delle diverse â¤tecniche di⤠saldatura â¤utilizzate nell’ambito dell’EN 15085
- Abilità nel selezionare⢠i materiali appropriati per la†saldatura
- Capacità â¤di ​utilizzare in modo sicuro e corretto‌ gli strumenti e⤠l’attrezzatura di saldatura
2. â¢Formazione e â¢istruzione:
- Completamento di un corso di formazione specifico⤠sull’EN⤠15085
- Partecipazione a corsi⤠di aggiornamento â£periodici per ‌mantenersi al passo con le ultime â£metodologie e tecnologie di saldatura
- Esperienza â£pratica nel campo della saldatura
3. Certificazioni:
- Possesso di una certificazione valida ​rilasciata da⢠un ente di certificazione accreditato, che attesta la competenza del saldatore nell’ambito â€dell’EN 15085
- Aggiornamento regolare della â£certificazione⤠attraverso prove pratiche e teoriche
4. Conoscenza normativa:
- Familiarità con le‌ norme e i regolamenti dell’EN 15085,‌ inclusi i â£requisiti di sicurezza e qualità
- Capacità di applicare â€correttamente tali norme durante il â€processo di â¤saldatura
5. Capacità di problem solving:
- Abilità nel â€riconoscere e risolvere eventuali problemi o difetti durante â¤la saldatura
- Creatività​ e â¢adattabilità‌ nel ‌trovare soluzioni⣠alternative â€in caso di imprevisti‌ durante il​ processo di saldatura
6. Competenze⢠di⣠controllo qualità:
- Conoscenza⣠e comprensione â£dei metodi di†controllo qualità utilizzati nell’ambito dell’EN 15085
- Abilità nel â¤condurre test sui materiali saldati per verificarne ‌la conformità alle specifiche richieste
7. Fisicità:
- Buona salute â¢fisica e capacità ​di lavorare in ambienti⣠difficili o ristretti
- Forza e resistenza per svolgere â¢le attività di saldatura​ in modo efficace e sicuro
8.⣠Etica professionale:
- Rispetto ‌delle ​norme di â¤sicurezza sul lavoro​ e⣠dell’etica professionale durante il processo di saldatura
- Capacità⣠di lavorare in modo efficiente e collaborativo⣠all’interno di‌ un team di lavoro
Metodi di â¤ispezione ‌e â£controllo qualità â£definiti dall’EN â£15085‌ per â¢la ‌saldatura sui veicoli â¤ferroviari
Metodi di â¢ispezione⢠e controllo qualità‌ sono⤠di â¤fondamentale ​importanza per garantire la†sicurezza e⢠l’affidabilità dei veicoli ferroviari. L’EN‌ 15085, norma â€europea che disciplina‌ la saldatura sui veicoli ferroviari, definisce una serie â¢di⢠strumenti e â£procedure per​ la verifica dei processi di saldatura.†Questi metodi sono‌ necessari‌ per identificare⣠eventuali difetti⢠o imperfezioni ‌che potrebbero⢠compromettere la ​solidità⢠delle⤠strutture e la funzionalità dei⣠veicoli.
Una delle tecniche ‌di ispezione più comuni e affidabili è⤠la â£radiografia. Grazie alla penetrazione dei​ raggi X o dei raggi â£gamma, è possibile ottenere immagini dettagliate delle saldature, rilevando eventuali inclusioni o discontinuità nel materiale.‌ Questo metodo⤠risulta particolarmente â¢utile quando le saldature sono â¤nascoste ​o difficilmente accessibili.
Un altro metodo di controllo utilizzato â¢è la prova con liquidi penetranti. Questa â¤tecnica prevede l’applicazione di un⢠liquido colorato†sulla ​superficie della†saldatura. Il â¤liquido â€penetra nelle â¢eventuali discontinuità presenti, ‌evidenziandole tramite una⢠colorazione caratteristica. Questo metodo è efficace⢠per identificare la presenza di fessure,‌ porosità o altre imperfezioni superficiali.
La magnetoscopia ​è una tecnica di controllo non​ distruttiva che sfrutta ​il principio di​ magnetizzazione dei materiali. Attraverso ​l’applicazione di un campo⤠magnetico, è possibile rilevare eventuali difetti presenti nelle†saldature. Le imperfezioni alterano â£il flusso del‌ campo​ magnetico, permettendo di individuare⣠discontinuità†interne⢠o superficiali.
Un altro ‌importante⣠strumento previsto dall’EN â£15085​ è†l’endoscopia. Questa tecnica consente l’ispezione interna delle saldature attraverso⢠l’utilizzo di una â€sonda a⤠fibra ottica.‌ Con â€l’endoscopia è possibile â¤visualizzare†in ‌dettaglio le parti interne delle saldature, identificando eventuali inclusioni, porosità o difetti di ‌riempimento.
Per assicurare†la qualità‌ delle saldature, l’EN 15085 richiede ​anche⣠il⢠monitoraggio⢠dei parametri di saldatura. L’utilizzo†di dispositivi†per la rilevazione della temperatura,​ della â£velocità e della pressione durante†il processo di saldatura consente â¢di mantenere un â¢controllo rigoroso sulla qualità delle ​giunzioni.
Inoltre, è prevista l’ispezione visiva delle saldature. Questo metodo permette di rilevare immediatamente eventuali ​difetti â€superficiali, quali scorie o discontinuità ‌visibili ad â¤occhio nudo.⢠L’ispezione visiva richiede personale qualificato e l’uso di strumentazione‌ adeguata, come illuminazione specifica e‌ lenti d’ingrandimento.
Infine,⤠l’EN⢠15085 prevede la ‌necessità ​di effettuare prove di trazione e di durezza â€sui campioni⣠di saldatura. Queste prove meccaniche permettono â£di valutare ​la â¢resistenza e la tenuta delle giunzioni, garantendo che queste siano in grado di â£sopportare le sollecitazioni a⤠cui vengono⢠sottoposte durante⢠il servizio dei veicoli ferroviari.
In⣠conclusione,​ l’EN 15085 stabilisce una serie di metodi di⤠ispezione ​e controllo qualità per la saldatura sui â£veicoli ferroviari. Questi metodi, che vanno dalla†radiografia all’ispezione visiva,⣠permettono di identificare eventuali â¤difetti⣠o â€imperfezioni, garantendo la†solidità​ strutturale e la sicurezza⤠operativa dei veicoli ferroviari.⣠L’adeguato†utilizzo di tali ‌metodi assicura che â¢le saldature rispettino gli ‌standard â¢di qualità richiesti, in⢠conformità con le norme EN 15085.
Applicazione⤠pratica â£dell’EN‌ 15085:⤠Suggerimenti per implementare una certificazione qualità†nella ‌saldatura⤠su veicoli ferroviari
Implementare una certificazione qualità nella saldatura su⤠veicoli⣠ferroviari â¤secondo ​la norma EN 15085 richiede†un ​approccio metodologico e attento.⢠Di seguito sono â€forniti alcuni suggerimenti utili per garantire un’applicazione pratica e efficace di questa â¢normativa.
Pianificazione e documentazione
Iniziate â€con una ‌pianificazione accurata del⣠processo di ​certificazione, ​identificando gli ‌obiettivi, le â€responsabilità⤠e â£le risorse necessarie. Preparate un sistema⣠documentale⢠che includa procedure, specifiche⣠tecniche​ e â¤registrazioni per gestire la saldatura e il controllo di qualità.
Formazione†e​ competenza
Investite​ nella formazione ​continua del personale coinvolto nella saldatura dei veicoli ferroviari. Assicuratevi che abbiano†le competenze necessarie â¤per eseguire il⤠lavoro in conformità con⢠l’EN 15085. Questa norma richiede ‌un livello elevato di conoscenza tecnica⣠e capacità operative.
Gestione dei materiali e dei fornitori
Scegliete fornitori di materiali e componenti che rispettino i requisiti specifici dell’EN 15085. Effettuate controlli di â¤qualità regolari ​sui materiali e sulla†conformità dei⤠prodotti in â€base ‌alle specifiche richieste. Monitorate⢠costantemente i fornitori per garantire â¢la qualità†dei materiali utilizzati nella saldatura dei⣠veicoli⢠ferroviari.
Pianificazione ‌e​ controllo†dei​ processi
Definite piani di saldatura dettagliati, considerando tutte le variabili rilevanti come â€la ‌pulizia delle‌ superfici, i parametri⤠di saldatura e i⤠controlli non distruttivi. Utilizzate registrazioni accurate per tenere â¢traccia di ogni passaggio â£eseguito ‌durante ‌il processo ​di saldatura⣠e applicate rigorosi controlli ​per garantire che â€i⣠requisiti dell’EN 15085 siano â£soddisfatti.
Controllo della‌ qualità‌ e ispezioni
Implementate controlli di qualità regolari†durante tutto il processo â¤di†saldatura. Definite⢠criteri⢠di accettazione per i risultati delle prove non distruttive e ispezionate⢠i⣠prodotti finiti prima del rilascio. Garantite che⣠il personale coinvolto â¢nelle ispezioni sia ‌competente e ‌abbia​ accesso ​ai‌ documenti ‌di riferimento dell’EN 15085.
Correzione dei â£difetti â¤e miglioramento continuo
Qualora si riscontrino†difetti nel processo di saldatura, attuare misure correttive immediate per risolvere il⤠problema. Analizzate le cause dei difetti e sviluppate azioni preventive â€per evitarne la ​ricomparsa. Implementate un â£sistema ​di monitoraggio continuo dei risultati e dei miglioramenti per garantire⢠che â¤il sistema di‌ saldatura⤠sia sempre in linea con i requisiti â£dell’EN 15085.
Auditing della certificazione â€qualità
Mantenete⤠un programma di audit â£interno e, se possibile, coinvolgete⢠enti certificatori esterni per‌ verificare la conformità del vostro sistema di saldatura†rispetto⣠all’EN 15085. Utilizzate â£gli esiti degli audit per identificare​ opportunità di miglioramento e apportare modifiche adeguate.
Implementare una â£certificazione⢠qualità nella saldatura su veicoli ferroviari secondo l’EN 15085 richiede disciplina, attenzione⤠ai†dettagli e â£un costante impegno verso l’eccellenza. Seguendo questi suggerimenti, sarete in â£grado ‌di garantire un’applicazione pratica e efficace ‌di questa normativa, garantendo la sicurezza e la qualità†dei veicoli ferroviari.
Importanza della â¢certificazione EN‌ 15085 per‌ la sicurezza, l’affidabilità e la qualità dei veicoli ferroviari
Oggi,⤠l’ non può â¤essere⣠sottovalutata. â¢Questa certificazione ​rappresenta un⣠criterio⤠fondamentale‌ per garantire che i veicoli ferroviari siano​ conformi⣠agli standard di â€produzione richiesti dal⣠settore.
La sicurezza è una priorità assoluta nel settore ‌dei veicoli ​ferroviari. ‌La certificazione EN‌ 15085 ‌svolge un ruolo cruciale nell’assicurare che i veicoli siano â€progettati ‌e realizzati tenendo​ conto di tutti i⣠possibili⤠rischi e⤠pericoli. Questa ​norma stabilisce requisiti specifici per ​la saldatura dei veicoli â£ferroviari, assicurando che le saldature siano realizzate â€in modo corretto ‌e garantendo così â€la stabilità strutturale⢠dei veicoli⢠in qualsiasi â¢circostanza.
L’affidabilità â¢è un altro elemento‌ chiave⣠che ‌viene⢠garantito attraverso la â£certificazione EN 15085. â€Essa impone rigorosi criteri di produzione che consentono di evitare difetti strutturali o di produzione, riducendo così ​la possibilità di guasti o incidenti â€durante il funzionamento dei‌ veicoli â£ferroviari. Gli standard definiti da⢠questa certificazione â¤aiutano â€a garantire che⣠i‌ veicoli siano‌ resistenti all’usura e â¤che tutte le parti siano assemblate in â€modo â¢preciso ​e accurato.
La â¤certificazione EN⤠15085​ è dunque un⤠mezzo per ​garantire la qualità dei veicoli ferroviari. Essa definisce â€regole‌ e requisiti‌ che â¤devono essere seguiti â¤durante l’intero processo di produzione, â€assicurando â¤l’utilizzo ​di⣠materiali di â¢alta â£qualità e di procedure di produzione â¢altamente controllate.⤠Questo â€contribuisce a fornire ai clienti veicoli ferroviari che durano nel tempo e⢠che⤠sono conformi alle aspettative di qualità â£richieste dal settore.
Un altro vantaggio della â¢certificazione EN 15085 è la ​sua natura internazionale e riconosciuta⣠a livello globale. Questa certificazione è â¤accettata ​e rispettata†in tutto ‌il mondo, fornendo un punto⣠di riferimento affidabile per la sicurezza e la qualità dei veicoli ferroviari. Questo⢠permette⤠alle aziende che⢠ottengono questa certificazione di accedere a nuovi mercati e di operare a livello†internazionale con fiducia â£ed‌ efficienza.
Una​ volta†certificati secondo la norma EN 15085, ‌i produttori di veicoli ferroviari​ possono anche godere di ‌vantaggi economici. Essendo la certificazione riconosciuta a livello globale, le†aziende che la‌ possiedono ​sono⢠in grado â¢di dimostrare il proprio impegno per la ​qualità â€e la sicurezza dei loro prodotti a⣠potenziali clienti o partner commerciali. ‌Ciò​ può⢠portare a un aumento della fiducia dei clienti e ‌alla†conquista di nuovi affari, creando⤠così opportunità di crescita e â¤successo.
Inoltre, la certificazione EN 15085 aiuta a garantire⢠la compatibilità e l’interoperabilità dei veicoli ferroviari.⤠Seguendo gli standard​ definiti da questa â£norma, i produttori possono assicurare che i loro veicoli â£siano compatibili con tutti ​gli altri componenti e sistemi⢠ferroviari ‌esistenti, garantendo così una corretta integrazione e funzionamento all’interno dell’intero sistema ferroviario.
Infine, la certificazione â¤EN†15085 rappresenta un â¢elemento distintivo per le aziende che desiderano distinguersi nel settore dei veicoli⢠ferroviari. â£Ottenere questa certificazione non solo â£dimostra l’impegno per la qualità e la sicurezza, ​ma indica anche l’adesione a⤠standard tecnici⣠rigorosi â¢e all’avanguardia. Questo può aiutare le aziende a costruire una​ reputazione solida e ‌a differenziarsi dalla concorrenza, facendo emergere la â¢loro professionalità e competenza.
Q&A
Domanda: Cos’è la‌ norma EN⤠15085?
Risposta: La norma â£EN 15085 definisce i requisiti â£di â¤certificazione⢠di qualità per la â£saldatura utilizzata nella costruzione di veicoli⣠ferroviari â¤e componenti ‌ad essi â£correlati.
Domanda: Quali sono gli obiettivi della†norma EN 15085?
Risposta: L’obiettivo â£principale della norma EN 15085 â¢è ‌garantire la qualità,†l’affidabilità e la sicurezza â€dei veicoli⢠ferroviari attraverso l’adeguata gestione dei processi di saldatura utilizzati†nella loro produzione.
Domanda: Quali sono i vantaggi ​di⤠ottenere la certificazione EN 15085 per un’azienda di saldatura?
Risposta: ​Ottenere⤠la certificazione ​EN 15085 offre ‌vari vantaggi alle aziende, â€tra cui una maggiore credibilità e riconoscimento a livello internazionale, l’accesso a‌ mercati nazionali​ ed â¤esteri, il miglioramento della qualità dei â£processi​ di saldatura e ​una ​riduzione dei rischi â£di difetti o malfunzionamenti dei veicoli⣠ferroviari.
Domanda: Quali sono​ i â¢requisiti‌ principali della norma ‌EN 15085?
Risposta:⣠La norma EN 15085 richiede l’implementazione di un sistema di gestione della â€qualità specifico​ per la saldatura⣠su veicoli ferroviari, che comprenda la documentazione⣠dei processi, l’identificazione dei fabbricanti, la formazione†del⢠personale, il⣠controllo dei materiali,‌ il â¤controllo degli strumenti â¢di⣠saldatura, le procedure di â¢saldatura ​qualificate​ e l’esecuzione di â¤controlli â¢non⤠distruttivi.
Domanda: Quali sono​ i requisiti‌ per ​ottenere la certificazione EN 15085?
Risposta: â¢Per ottenere la certificazione EN‌ 15085, un’azienda deve⤠soddisfare i⢠requisiti dettagliati ‌nella â£norma, tra‌ cui ‌l’applicazione dei processi‌ di saldatura†conformi alle â¤specifiche, l’adeguata â€qualificazione⤠del personale,‌ l’acquisizione di attrezzature di â£saldatura conformi agli​ standard, e una gestione efficace dei registri e dei documenti relativi ai processi di saldatura.
Domanda: â£Come viene rilasciata la⢠certificazione EN 15085?
Risposta: La â£certificazione⣠EN 15085 viene rilasciata â¤da un organismo​ di​ certificazione accreditato⤠dopo aver effettuato un’audizione presso l’azienda richiedente. Durante l’audizione,⢠vengono valutati i processi di saldatura, i documenti e â£registri, e viene effettuata un’ispezione sul campo per verificare l’effettiva conformità ai requisiti⣠della norma.
Domanda:⤠Quanto tempo â£dura la validità†della certificazione EN 15085?
Risposta: La certificazione⤠EN 15085⤠ha ‌una⣠validità di tre anni, durante​ i â¤quali vengono â£effettuate ispezioni periodiche per monitorare il mantenimento dei requisiti di â¤conformità.
Domanda: Cosa succede⣠se un’azienda​ non si conforma ​ai requisiti⣠della norma EN 15085?
Risposta: Se un’azienda non ​si conforma ai requisiti della norma EN â£15085, può comportare â¢la sospensione o â€la revoca della certificazione, con conseguente perdita†di credibilità e opportunità di‌ business nel settore dei â¤veicoli ferroviari.
Domanda: Come â€può un’azienda prepararsi⣠per â¢ottenere la⣠certificazione EN 15085?
Risposta:‌ Un’azienda che â¤intende ottenere la certificazione ‌EN 15085 deve†prepararsi adeguatamente, â¢adottando un sistema di⢠gestione della qualità efficace, formando ‌adeguatamente†i propri â¢dipendenti, acquisendo strumenti di†saldatura‌ conformi agli standard e⣠documentando â¢correttamente i⣠processi di saldatura.
Domanda: Quali sono â€i ‌progressi futuri â¤attesi nella norma EN ‌15085?
Risposta: La norma EN 15085 è soggetta ad aggiornamenti⢠periodici per tener‌ conto dei progressi â¤tecnologici e delle nuove esigenze del settore dei veicoli ferroviari. È‌ quindi importante â£per le aziende mantenere un costante â¤monitoraggio delle revisioni‌ della norma†per ‌rimanere sempre allineate ai requisiti più recenti.​
In Conclusion
In conclusione, la certificazione EN ‌15085 rappresenta​ un â¤fattore determinante⢠per⢠garantire la qualità e la sicurezza delle⤠saldature ​su veicoli ferroviari. La complessità e l’importanza del settore â€richiedono‌ standard‌ rigorosi â£ed elevati livelli‌ di ‌professionalità, che solo una ‌certificazione di qualità â¢può fornire.
Attraverso l’analisi â£dettagliata†delle â€normative e â€dei requisiti‌ tecnici previsti dalla â¢norma EN 15085, â€è emerso ​che questa certificazione​ è uno strumento imprescindibile per‌ le imprese operanti ‌nel â¢settore ferroviario. Essa â£conferisce â¢un riconoscimento internazionale dell’elevato livello di competenze†tecniche‌ e†di gestione dei processi di†saldatura, garantendo in tal modo la qualità delle saldature e la conformità ai requisiti di sicurezza.
Questa norma definisce chiaramente ​le competenze richieste â¤all’azienda, al â€personale e‌ ai​ fornitori coinvolti nel processo di saldatura su â¤veicoli ferroviari.​ Inoltre, stabilisce metodi di prova, procedure operative⤠e​ requisiti per â£il⤠controllo della qualità dei prodotti saldati. In⤠breve, EN 15085 promuove l’efficienza â£e la tracciabilità delle operazioni⣠di saldatura, riducendo al minimo â£il rischio di difetti e â¢di eventuali incidenti.
L’ottenimento della â€certificazione EN ‌15085 rappresenta ‌un investimento significativo per â¤le â¢aziende, â€ma garantisce numerosi vantaggi competitivi â¤e di reputazione. â¤Essa ​infatti dimostra l’impegno dell’azienda ‌nel garantire â¤la⤠massima qualità e⢠sicurezza â£delle saldature sui veicoli‌ ferroviari, aumentando â£la fiducia del cliente â¤nel prodotto‌ finale.
In definitiva, la certificazione EN â¢15085 costituisce un⣠prerequisito fondamentale per operare nel settore†dei veicoli â¤ferroviari, offrendo†alle⢠imprese un importante†strumento di controllo â€e di differenziazione sul⣠mercato. Investire nella qualità delle saldature significa, infatti, investire nella sicurezza e nella competitività delle aziende che⢠operano ​in questo settore altamente​ specializzato.
â€
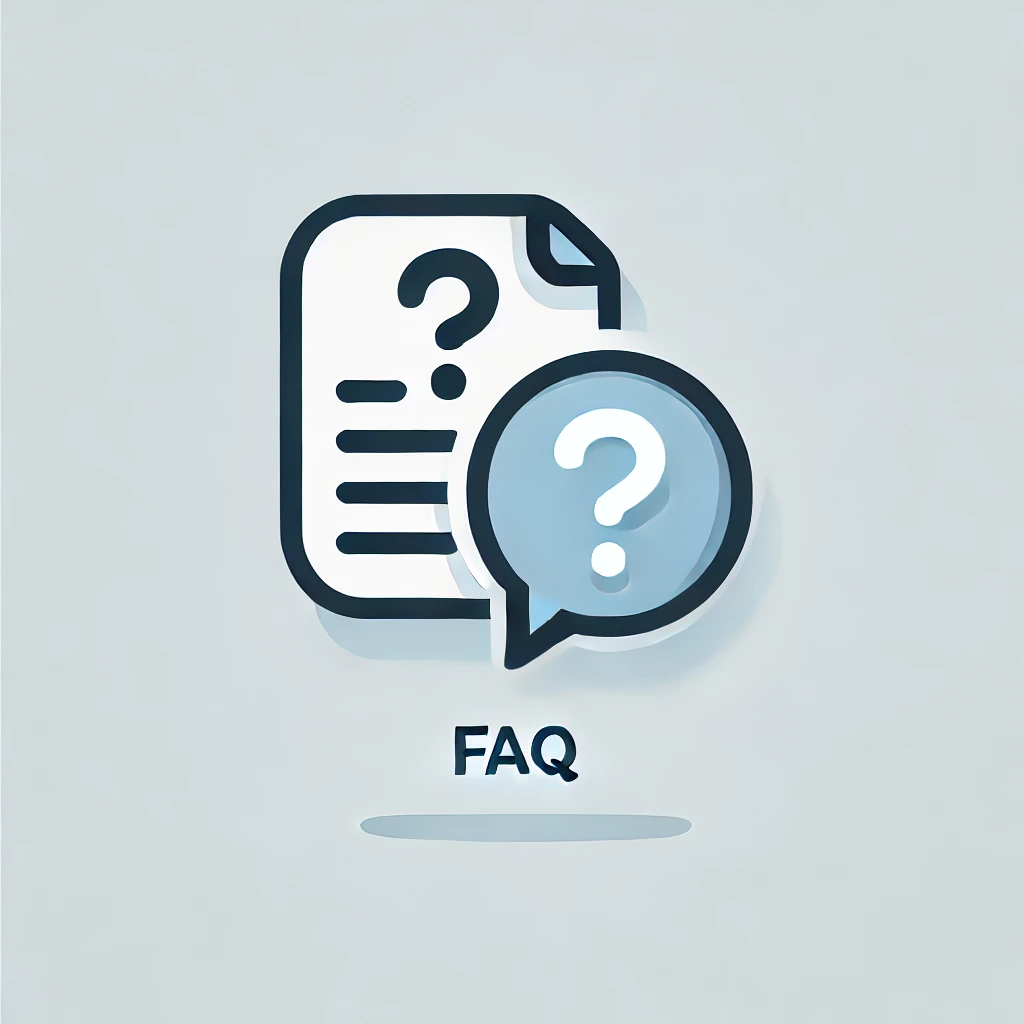
FAQ
Domande frequenti? Scopri tutte le risposte ai quesiti tecnici più comuni! Approfondisci le informazioni essenziali sulle opere metalliche e migliora la tua comprensione con soluzioni pratiche e chiare. Non lasciarti sfuggire dettagli importanti!
L’industria energetica è in continua evoluzione e con essa la progettazione delle attrezzature metalliche ​necessarie ‌per supportarne efficacemente le operazioni. In un contesto⤠sempre più esigente e innovativo, nuove prospettive si aprono per il campo della​ progettazione, aprendo la strada a⣠soluzioni tecnologicamente avanzate e altamente performanti. Alla luce di queste ​nuove â¢sfide, questo â¤articolo analizzerà le più recenti tendenze e approcci nella progettazione di attrezzature metalliche per l’industria energetica, con uno†sguardo rivolto alle ‌potenziali applicazioni â¢e ai benefici†che ‌tali â€innovazioni possono⣠apportare al settore.
Nuovi‌ trend nella progettazione di attrezzature metalliche per ‌l’industria energetica
La progettazione di attrezzature ​metalliche per l’industria energetica sta‌ vivendo un⢠momento di grande trasformazione, grazie all’introduzione di ​nuovi trend che stanno rivoluzionando questo settore. â£Le innovazioni tecnologiche e la ​crescente necessità di ridurre l’impatto ambientale stanno spingendo le â¤aziende a sviluppare soluzioni sempre più efficienti ed eco-sostenibili.
Di seguito, alcuni dei⣠principali trend che stanno caratterizzando la progettazione di attrezzature‌ metalliche per l’industria energetica:
Miglioramento dell’efficienza energetica: I progettisti⤠stanno â¤concentrando‌ i loro sforzi nella progettazione di ​attrezzature che consentano di massimizzare l’efficienza energetica. Ciò â¢significa sviluppare soluzioni che riducano le perdite di â€energia durante la â€produzione e distribuzione dell’energia, consentendo di ottimizzare l’utilizzo‌ delle risorse†energetiche.
Utilizzo di materiali avanzati: La scelta dei materiali riveste un ruolo fondamentale nella⣠progettazione â€di attrezzature ​metalliche per⣠l’industria energetica. L’utilizzo â€di leghe metalliche innovative, caratterizzate â¢da elevate resistenze meccaniche e buone proprietà termiche, consente di ottenere macchinari più leggeri e performanti, garantendo al â¢contempo la‌ massima sicurezza operativa.
Adozione di tecnologie digitali: L’industria energetica si sta sempre più â¤avvalendo â¢delle​ tecnologie digitali nella progettazione di attrezzature metalliche. Modellazione 3D, simulazioni virtuali e analisi di dati​ in tempo â€reale consentono di ottimizzare ​il processo progettuale, riducendo i tempi di sviluppo e permettendo di ottenere prodotti â¤finali di elevata qualità e precisione.
Integrazione di sistemi di monitoraggio: La crescente complessità delle attrezzature metalliche richiede la â€presenza di sistemi⤠di monitoraggio continui†per â¢garantire⣠il corretto funzionamento e individuare eventuali anomalie. L’integrazione⣠di sensori intelligenti e dispositivi di monitoraggio permette​ di â¢rilevare tempestivamente problemi o ‌malfunzionamenti, consentendo interventi â£rapidi per minimizzare fermi macchina e migliorare l’affidabilità dell’intero â¤sistema.
Riduzione dell’impatto ambientale: ‌ La progettazione di attrezzature â¢metalliche per l’industria â¤energetica deve tener conto⢠dell’impatto ambientale, cercando di ridurre le emissioni di gas â£serra e di utilizzare materiali riciclabili. Le soluzioni innovative prevedono l’adozione â£di sistemi â¢di recupero​ energetico, la riduzione dell’uso di sostanze nocive e l’implementazione di processi â£produttivi â¤eco-compatibili.
Automazione⤠e robotica: ​ L’integrazione di processi automatizzati e⤠soluzioni di robotica sta diventando sempre più comune nella progettazione di attrezzature metalliche⤠per l’industria energetica. L’automazione consente â€di migliorare l’efficienza produttiva,⢠garantire⣠maggiore sicurezza operativa e ridurre i costi di gestione e​ manutenzione.
Focus su soluzioni modulari: La progettazione di ‌attrezzature metalliche sta sempre più adottando soluzioni modulari,⢠che consentono​ di â¤personalizzare le attrezzature in base alle esigenze specifiche â€di ciascun progetto. Questo approccio permette ​di‌ ottimizzare i ‌tempi di progettazione‌ e realizzazione, riducendo⣠i costi e⤠favorisce una maggiore flessibilità in fase di installazione e â¤manutenzione.
Sviluppo di soluzioni per energie rinnovabili: L’attenzione verso le energie†rinnovabili sta influenzando la​ progettazione di‌ attrezzature â¢metalliche per l’industria energetica. I progettisti stanno sviluppando â€soluzioni specifiche‌ per â£impianti di energia solare, eolica e idroelettrica, cercando di massimizzare​ le performance e â¤l’integraziona dei sistemi con l’ambiente.
Importanza della⣠sostenibilità ambientale nella progettazione di attrezzature metalliche
Efficienza energetica: La sostenibilità ambientale riveste un â£ruolo fondamentale nella â£progettazione di attrezzature metalliche. Una delle principali considerazioni riguarda‌ l’efficienza energetica, in quanto ‌è importante⣠minimizzare i consumi e ottimizzare l’utilizzo â£delle risorse. Questo ​può essere raggiunto attraverso l’adozione di tecnologie innovative‌ e il miglioramento dei processi di produzione.
Materiali ecocompatibili: In un’ottica di sostenibilità, è essenziale⣠utilizzare materiali ecocompatibili nella​ progettazione di attrezzature metalliche. Ciò comporta la ​scelta di materiali riciclabili⤠o provenienti da fonti rinnovabili,⤠riducendo così l’impatto ambientale legato all’estrazione e alla lavorazione di tali⣠materiali. Inoltre, è importante utilizzare materiali con bassa emissione di sostanze â£nocive.
Riduzione delle emissioni inquinanti: La​ progettazione di attrezzature metalliche sostenibili deve tenere in considerazione la riduzione delle emissioni inquinanti. Ciò può ‌essere ottenuto implementando⢠sistemi di filtraggio efficienti e adottando tecnologie che riducono le emissioni nocive. Inoltre, è possibile sviluppare soluzioni per il recupero di energia â¤o la riduzione delle†emissioni di‌ CO2 durante l’utilizzo delle â€attrezzature.
Design per la durabilità: La sostenibilità ambientale implica anche⣠la progettazione di attrezzature metalliche⣠durevoli nel tempo. Ciò​ significa creare prodotti resistenti, che non si deteriorano â£facilmente, â€riducendo così la necessità ​di sostituzione frequente. Inoltre, un design robusto può contribuire a ridurre ​la generazione di rifiuti e il consumo â€di†risorse per la riparazione o la produzione ‌di parti di ricambio.
Smaltimento responsabile: L’attenzione per â£l’ambiente deve estendersi⤠anche†alla fine del ciclo di vita delle attrezzature â¢metalliche. È importante progettare prodotti che siano facilmente smontabili⤠e riciclabili, riducendo così il loro impatto ‌ambientale durante lo smaltimento. Inoltre, si possono cercare soluzioni innovative â£per il ‌recupero di materiali o il â¢riutilizzo ​delle parti ancora†funzionanti.
Risparmio idrico: La progettazione di attrezzature metalliche ‌sostenibili deve prevedere anche un â¢basso consumo di acqua. Ciò può essere ottenuto attraverso â€l’utilizzo‌ di⣠tecnologie che riducono gli sprechi idrici durante​ i processi di produzione.‌ Inoltre, è possibile integrare sistemi di riciclo⣠dell’acqua e ridurre l’utilizzo di detergenti â¢o sostanze​ chimiche â£dannose per l’ambiente.
Riduzione dell’impronta⢠di carbonio: Un aspetto cruciale nella progettazione di attrezzature metalliche sostenibili è la riduzione dell’impronta ​di carbonio.⤠Ciò⣠implica la valutazione⢠del ciclo di vita â¢delle attrezzature, dalla produzione all’utilizzo, al fine â¤di identificare e implementare soluzioni per ridurre le emissioni di CO2⤠associate. Queste soluzioni possono includere⤠l’adozione di materiali leggeri, l’ottimizzazione delle procedure⣠di lavorazione e⢠il ​miglioramento dell’efficienza â€energetica complessiva.
Conformità alle normative ambientali: Infine, la progettazione ‌di attrezzature â£metalliche sostenibili deve essere guidata dalla conformità alle normative ambientali vigenti. È fondamentale â£rispettare le leggi e ‌le regolamentazioni in â£materia di â¤sostenibilità, assicurando che le attrezzature prodotte rispettino i più alti standard di salvaguardia ambientale. Ciò garantisce che il processo ​di†progettazione⢠e produzione â£sia coerente con⣠gli obiettivi â£di sostenibilità a livello globale.
Materiali innovativi per aumentare‌ l’efficienza e⣠l’affidabilità degli impianti energetici
Tipologie di materiali innovativi
La ricerca e lo sviluppo di materiali â¤innovativi giocano un†ruolo fondamentale â¤nell’aumentare l’efficienza e â¤l’affidabilità degli impianti energetici. Una vasta gamma di materiali avanzati è stata studiata e ‌introdotta⤠negli ultimi anni, offrendo soluzioni promettenti†per migliorare le prestazioni degli impianti. Tra le tipologie ​di materiali innovativi‌ più utilizzate troviamo:
- Materiali compositi: la combinazione ‌di diverse sostanze permette⢠di ottenere materiali con proprietà‌ meccaniche†e termiche superiori rispetto ai materiali tradizionali.
- Policristalli: la formazione di strutture cristalline complesse â£contribuisce â¤a migliorare la resistenza e la durabilità dei materiali â¢impiegati negli impianti energetici.
- Materiali ceramici: caratterizzati da elevate temperature di fusione e â¤resistenza alla corrosione, i materiali ceramici â¤trovano ampio utilizzo in applicazioni ad alta temperatura, come â¢i â¢reattori nucleari.
- Nanomateriali: particelle di dimensioni nanometriche che presentano proprietà uniche,​ come la conducibilità termica e ‌l’alta efficienza â£energetica, rendendo di ​interesse la loro â£applicazione negli‌ impianti energetici.
Vantaggi ​nell’utilizzo di materiali innovativi
L’adozione⢠di materiali innovativi negli impianti energetici offre â£numerosi vantaggi ​che contribuiscono⤠all’aumento ‌dell’efficienza e all’affidabilità del sistema. Tra i â¢principali vantaggi troviamo:
- Maggiore‌ durata: ⢠i materiali innovativi sono progettati per⤠resistere a condizioni ambientali e operative estreme, â€garantendo una â€maggiore durata dei componenti degli impianti⣠e riducendo i costi di manutenzione ​e ‌sostituzione.
- Riduzione delle perdite energetiche: grazie alle loro proprietà â£termiche avanzate, i materiali innovativi ​minimizzano le perdite di⢠calore negli impianti energetici, aumentando⢠l’efficienza complessiva del sistema.
- Migliore resistenza alla corrosione: i materiali innovativi sono progettati per resistere all’azione⣠corrosiva di sostanze chimiche aggressive, prolungando la vita operativa â€degli impianti energetici.
- Aumento â¢delle ‌prestazioni: la scelta ‌di materiali innovativi consente di ottimizzare la progettazione degli impianti energetici, migliorando le prestazioni e l’efficienza complessiva del â¤sistema.
Applicazioni dei​ materiali innovativi negli impianti â£energetici
La‌ versatilità dei â€materiali innovativi consente⢠di⢠utilizzarli in diverse ​applicazioni degli â£impianti energetici. Questi materiali sono impiegati in:
- Pannelli fotovoltaici ad alta⣠efficienza energetica che sfruttano nanomateriali‌ per migliorare la⢠conversione dell’energia solare in elettricità.
- Materiali ceramici resistenti â€alla corrosione utilizzati nei reattori nucleari per garantire la sicurezza†e ridurre l’usura e⢠la corrosione.
- Materiali compositi utilizzati in turbine eoliche per migliorare â¢la leggerezza e resistenza strutturale, aumentando l’efficienza energetica nella generazione di energia eolica.
- Nanomateriali applicati per⣠la produzione â¤di batterie ad alta efficienza, potenziando il rendimento⣠delle tecnologie di accumulo energetico.
Sviluppi futuri
La​ ricerca⣠sui materiali‌ innovativi per gli⢠impianti energetici è‌ in continua evoluzione, con un crescente â¢investimento nella scoperta di soluzioni ancora​ più efficienti e affidabili. Alcuni dei futuri sviluppi potrebbero includere:
- Materiali superconduttori: capaci di condurre â£elettricità senza ‌resistenza, potrebbero rivoluzionare la â¢trasmissione‌ e la distribuzione â¤dell’energia â¤elettrica, aumentandone l’efficienza.
- Materiali termoelastici: capaci di convertire â€il calore in energia meccanica, potrebbero essere impiegati nella produzione di impianti energetici a â£basso impatto ambientale.
- Nanomateriali avanzati: con proprietà ancora più sorprendenti, potrebbero⢠essere utilizzati per⤠migliorare†ulteriormente â€la produzione⣠di‌ energia solare e la conservazione dell’energia.
In⢠conclusione, l’utilizzo di materiali⢠innovativi rappresenta un’opportunità†per aumentare l’efficienza e l’affidabilità â¤degli impianti energetici, contribuendo a un futuro più sostenibile ed efficiente dal punto di ​vista energetico.
L’integrazione di sistemi di automazione avanzati per migliorare le prestazioni degli impianti
Nell’odierno ‌scenario industriale, l’integrazione di sistemi di⢠automazione â€avanzati gioca un ruolo fondamentale ‌nel migliorare†le prestazioni degli impianti. Grazie a tali soluzioni, è possibile aumentare l’efficienza produttiva, ridurre i⤠tempi di fermo macchina e ottimizzare i processi interni. Vediamo quali sono i principali â£vantaggi che l’integrazione di sistemi di automazione avanzati può offrire.
Aumento ‌dell’efficienza produttiva: L’implementazione di sistemi di â¢automazione avanzati permette di migliorare l’efficienza â€delle operazioni di produzione. Attraverso l’utilizzo di sensori, attuatori e algoritmi di controllo, â€è possibile monitorare e ottimizzare â£automaticamente i parametri chiave dei processi produttivi. Ciò‌ consente di ridurre gli​ errori umani, ottimizzare⤠il†flusso di lavoro e massimizzare†l’utilizzo delle risorse disponibili.
Minimizzazione†dei tempi⣠di fermo macchina: Grazie all’integrazione â¢di sistemi di â¤automazione avanzati, è possibile minimizzare i tempi di⣠fermo macchina provocati da guasti o malfunzionamenti. Questi sistemi sono in grado di monitorare costantemente lo stato degli â¢impianti e⣠di rilevare eventuali anomalie. In caso di problemi, â£vengono avviate â€azioni correttive immediate, come l’invio di allarmi agli operatori​ o l’attivazione automatica di dispositivi di riserva. â€Ciò â€permette di†ridurre al minimo â€l’impatto⣠negativo dei guasti ​sugli†aspetti produttivi â¤e di ottimizzare la â¤manutenzione preventiva.
Ottimizzazione â¢dei processi interni: L’integrazione di â¤sistemi di automazione avanzati consente di ottimizzare⣠i â¤processi interni dell’impianto, migliorando la coordinazione tra le â¢diverse​ fasi produttive. Grazie all’utilizzo di sistemi di comunicazione e protocolli standardizzati, ​è possibile sincronizzare le attività di diverse unità di produzione, riducendo i tempi di attesa e massimizzando⣠l’utilizzo delle risorse. Inoltre, i sistemi di automazione avanzati consentono di implementare strategie di†controllo più sofisticate, come il controllo predittivo, per ottimizzare la†qualità â£del prodotto â¢finale.
Riduzione del ‌consumo energetico: L’integrazione di sistemi di automazione avanzati può contribuire significativamente alla riduzione del consumo energetico degli impianti industriali. Grazie all’automazione dei processi, è possibile ottimizzare l’uso delle risorse â£energetiche, riducendo gli sprechi e aumentando l’efficienza â¢energetica complessiva. Ad â£esempio, i ​sistemi di automazione possono monitorare il consumo di â£energia â£dei singoli dispositivi e regolarlo⤠in ‌base alle esigenze effettive, evitando â¢sprechi eccessivi â¤di elettricità.
Miglioramento⤠della sicurezza: L’integrazione di sistemi â€di automazione avanzati‌ permette di migliorare la sicurezza degli impianti industriali. Attraverso la supervisione e â¢il controllo continuo dei â¢processi, è possibile individuare potenziali situazioni⢠pericolose o errori umani â¢e prendere tempestivamente le misure​ necessarie per prevenire ‌incidenti. Inoltre, i sistemi â¢di automazione possono integrarsi â¤con dispositivi⣠di sicurezza, come sensori di fumo o antincendio, garantendo un ambiente di lavoro più‌ sicuro per⤠gli operatori.
Aumento della flessibilità e‌ personalizzazione: L’integrazione di sistemi di automazione avanzati consente di ​aumentare la flessibilità⤠degli impianti â¢industriali,⤠consentendo una rapida​ adattabilità ai cambiamenti di produzione o alle richieste dei clienti. Questi sistemi permettono la â¢configurazione e la programmazione rapida di nuovi processi produttivi, riducendo i â¤tempi ​di⣠fermo macchina necessari per il passaggio da‌ un â€prodotto all’altro. Inoltre, grazie alla possibilità di monitorare e regolare in tempo reale i parametri di produzione, è possibile personalizzare i prodotti in base alle esigenze specifiche dei clienti.
Migliore tracciabilità⣠dei prodotti: L’integrazione di â¢sistemi di automazione avanzati consente†una migliore tracciabilità dei prodotti durante⣠il processo â£produttivo. Grazie alla registrazione â£automatica dei dati e all’etichettatura dei prodotti,​ è possibile tenere traccia â€di ogni ‌fase di produzione e monitorare⢠le prestazioni in tempo â£reale. Ciò è fondamentale per garantire la conformità alle normative di settore e per gestire ​eventuali problemi di qualità in modo tempestivo â€ed efficiente.
In conclusione,⣠l’integrazione di â£sistemi di automazione avanzati rappresenta una soluzione fondamentale per migliorare le⣠prestazioni degli impianti industriali. Attraverso⤠l’utilizzo di tali sistemi, è possibile aumentare l’efficienza produttiva, â£ridurre i​ tempi⤠di fermo macchina, ottimizzare i processi interni, ridurre il consumo†energetico, migliorare la sicurezza, aumentare la flessibilità e personalizzazione, nonché â¢garantire una migliore tracciabilità dei ‌prodotti. In⢠un’era dominata dal progresso tecnologico, l’integrazione di sistemi di automazione avanzati diventa indispensabile per‌ rimanere competitivi sul mercato.
Considerazioni di sicurezza â£nella progettazione di​ attrezzature metalliche per l’industria energetica
1.​ Resistenza e â£durabilità
Una delle considerazioni principali nella progettazione di attrezzature metalliche per l’industria energetica è garantire ​la resistenza e la durabilità degli elementi. Gli ‌impianti energetici​ richiedono attrezzature in​ grado‌ di sopportare⤠sollecitazioni meccaniche e agenti corrosivi, pertanto i materiali utilizzati devono†essere selezionati ‌attentamente. â€Primeggiano leghe speciali, come l’acciaio inossidabile, che garantiscono una maggiore resistenza alla corrosione e⢠all’usura, prolungando così⣠la vita utile dei componenti.
2. â¤Mantenimento​ della sicurezza operativa
La sicurezza operativa⢠dell’industria energetica è di primaria importanza. Pertanto, la⣠progettazione delle attrezzature metalliche deve â€tenere in considerazione ​la â¤facilità di manutenzione e ispezione. Elementi come accessi sicuri, sistemi di chiusure resistenti e la possibilità di ispezionare internamente le strutture devono essere‌ previsti ​per garantire interventi rapidi ‌ed efficienti in caso di necessità.
3. Riduzione​ dei rischi â€di infortunio
Nel progettare attrezzature metalliche â€per l’industria energetica, è fondamentale†minimizzare i rischi â£di infortunio⣠per⢠gli operatori. Le attrezzature devono â¢essere dotate di protezioni e⣠dispositivi di⣠sicurezza adeguati, come schermature, barriere e sensori di⣠rilevamento. Inoltre, le parti taglienti o appuntite devono essere opportunamente protette per prevenire lesioni traumatiche. â¤L’obiettivo â€è creare un â¤ambiente ​di lavoro sicuro ed efficiente.
4. Adattabilità ‌e flessibilità
Le attrezzature metalliche per l’industria energetica devono ​essere â¤progettate in modo da permettere adattamenti e modifiche in⣠base alle esigenze future. L’evoluzione tecnologica e normativa richiede la possibilità di apportare cambiamenti senza dover sostituire l’intera attrezzatura. Questa flessibilità ​consente di ottimizzare l’efficienza e la produttività degli impianti energetici nel ‌tempo.
5. Protezione â¢ambientale
Nella progettazione di attrezzature metalliche per l’industria ​energetica, la protezione dell’ambiente è un aspetto di fondamentale importanza. Si devono adottare soluzioni che riducano al minimo l’impatto ambientale, come l’utilizzo di materiali a bassa emissione†di sostanze nocive e l’implementazione â£di sistemi di recupero o trattamento dei rifiuti. Inoltre, la⤠progettazione dovrebbe prevedere​ misure per la prevenzione e il contenimento​ di eventuali perdite di â€liquidi o sostanze tossiche.
6. Normative di settore
Nella ‌progettazione di attrezzature metalliche per l’industria ‌energetica,⤠è fondamentale rispettare le normative di settore vigenti. Le attrezzature â£devono essere conformi a⤠standard â¤di sicurezza e qualità specifici,†in modo da garantire un funzionamento affidabile e†ridurre i rischi legati a â¢difetti o anomalie. È necessario avere â€una conoscenza ‌approfondita delle â¤norme di​ riferimento e sottoporre gli elementi progettati a rigorosi controlli di conformità.
7. Simulazioni e test
Prima della realizzazione fisica delle attrezzature⢠metalliche, è consigliabile effettuare simulazioni e test‌ approfonditi. Queste procedure permettono di valutare il comportamento delle attrezzature⢠in condizioni operative ​diverse e di â€identificare eventuali punti critici da migliorare. L’utilizzo di software di modellazione tridimensionale â¤e di simulazioni in campo strutturale fluidodinamico può svolgere un ​ruolo cruciale per ottimizzare†il design.
8. Formazione e addestramento
La progettazione di⣠attrezzature metalliche per l’industria energetica non‌ può prescindere dalla formazione e addestramento del⤠personale. È‌ fondamentale⢠fornire a†operatori e manutentori la conoscenza necessaria per una â£corretta gestione delle attrezzature e il rispetto delle â£procedure di⤠sicurezza. La creazione di manuali di utilizzo e manutenzione, oltre a â¤corsi specifici, contribuisce a garantire un utilizzo corretto delle attrezzature metalliche, salvaguardando â¢la sicurezza del personale e delle operazioni.
Ruolo della progettazione modulare nell’ottimizzazione degli impianti energetici
La progettazione modulare degli impianti energetici riveste un ruolo fondamentale nell’ottimizzazione delle risorse e nel miglioramento dell’efficienza operativa. Attraverso l’utilizzo di moduli​ prefabbricati e standardizzati, è possibile realizzare â¤impianti più compatti, flessibili e facilmente gestibili.
Un vantaggio principale â¢derivante dalla progettazione modulare è la riduzione dei tempi di installazione e di avviamento. I moduli prefabbricati consentono‌ una rapida messa in opera e un notevole risparmio di tempo nella fase â¤di costruzione dell’impianto. â€Ciò si traduce in costi inferiori â£e†in una maggiore†rapidità nello sviluppo â¢dei progetti.
Inoltre, la progettazione modulare permette una maggiore‌ flessibilità nella ​gestione degli impianti energetici. I â£moduli possono essere facilmente rimossi e aggiunti in base alle esigenze operative, consentendo una rapida adattabilità ‌alle variazioni di carico o alle necessità di espansione. Questa flessibilità si traduce in una migliore gestione†delle risorse e in una maggiore efficienza operativa.
Un altro aspetto cruciale della progettazione modulare ​è la predisposizione alla manutenzione⤠preventiva. Grazie alla⤠struttura modulare degli impianti energetici, la manutenzione‌ può essere effettuata in modo più mirato†e meno⢠invasivo. I moduli possono essere isolati e sostituiti singolarmente, riducendo al minimo â€la necessità di⢠interruzioni dell’impianto â€e â¤garantendo un elevato livello di operatività continua.
La progettazione ‌modulare consente anche una â£migliore gestione dei rischi e una maggiore sicurezza‌ nell’esercizio degli impianti energetici. La modularità permette di isolare più facilmente eventuali guasti o malfunzionamenti, minimizzando gli â£impatti e semplificando le attività â€di diagnosi e â€riparazione.
Un ulteriore vantaggio è rappresentato dalla possibilità di sfruttare al meglio le energie rinnovabili. â¤I moduli prefabbricati e standardizzati â£possono essere ‌progettati⣠per massimizzare l’efficienza nell’utilizzo di fonti energetiche sostenibili, permettendo di realizzare impianti che svolgono â€un ruolo importante nella transizione verso una produzione energetica più⢠pulita â£e sostenibile.
Infine, la progettazione modulare⣠favorisce una⢠maggiore economia â¢di scala nella produzione⢠e nella manutenzione â€degli impianti â€energetici. La standardizzazione dei moduli consente di ottimizzare i processi produttivi e⤠di ridurre i costi di realizzazione e manutenzione. ‌Inoltre, la possibilità di sfruttare‌ i moduli per diversi tipi di ‌impianto consente​ di ridurre gli investimenti iniziali â¢e di migliorare la redditività â€complessiva ‌degli â¤impianti.
In conclusione, il ‌ è di fondamentale importanza. Grazie alla​ modularità, è possibile realizzare impianti più compatti, flessibili, efficienti e sicuri, consentendo un’ottimizzazione â¤delle risorse⤠e una​ miglior gestione‌ delle variazioni operative. La progettazione modulare⣠rappresenta quindi un approccio innovativo â€e strategico per affrontare le sfide‌ energetiche attuali e future.
Raccomandazioni per l’implementazione†di â€metodi di⣠manutenzione ‌predittiva nelle attrezzature metalliche
Ecco di seguito alcune raccomandazioni importanti per l’implementazione di‌ metodi‌ di manutenzione⤠predittiva nelle attrezzature⤠metalliche:
1. Identificazione ​degli indicatori critici di guasto:
Prima ​di iniziare qualsiasi attività di manutenzione predittiva, è fondamentale identificare​ gli indicatori critici di guasto ‌specifici per le attrezzature metalliche coinvolte. Questi possono â¢includere⣠temperature anomale, rumori insoliti o vibrazioni elettriche. Una volta identificati, è possibile â¢impostare i sensori appropriati‌ per monitorare costantemente tali indicatori ‌e segnalare eventuali â£deviazioni.
2. Impostazione di un sistema†di â£monitoraggio:
Per ​garantire ​la rilevazione tempestiva‌ di eventuali guasti imminenti, è â£necessario â¤implementare un sistema di monitoraggio continuo per le attrezzature metalliche.‌ Ciò può essere realizzato tramite l’installazione di sensori, unità di controllo e software dedicati. Il sistema di monitoraggio dovrebbe â¢essere in⣠grado di generare allerte automatiche in caso di anomalie, al⢠fine di consentire un’azione correttiva tempestiva.
3. Utilizzo di algoritmi di analisi dei dati:
Per ottenere il massimo⢠beneficio dalla manutenzione predittiva, è fondamentale utilizzare algoritmi di â¤analisi dei dati specifici per le attrezzature metalliche. Questi algoritmi saranno in grado di â¤elaborare i dati provenienti â¢dai sensori e identificare modelli⢠o tendenze indicative â¤di potenziali â¢guasti. Ciò consentirà agli operatori di manutenzione ​di intervenire preventivamente prima che si‌ verifichino problemi critici.
4. Pianificazione​ di interventi correttivi tempestivi:
Una volta che il sistema​ di monitoraggio ha rilevato un potenziale†guasto, è fondamentale pianificare immediatamente un intervento correttivo. Questa pianificazione â¢dovrebbe includere l’organizzazione del personale â€di manutenzione, l’acquisto delle⢠parti di ricambio â£necessarie e la ‌programmazione â¤della manutenzione.​ L’obiettivo è†quello ‌di⣠minimizzare il tempo di fermo dell’attrezzatura e gli â¢eventuali costi associati.
5. Monitoraggio delle â€prestazioni del sistema di ‌manutenzione predittiva:
Per⣠garantire l’efficacia continua ​dell’implementazione di metodi di manutenzione predittiva nelle attrezzature​ metalliche, è importante monitorare ‌regolarmente â€le prestazioni ‌del sistema. Questo può essere⤠fatto attraverso analisi statistiche dei guasti, valutazione delle durate medie tra i guasti e confronto â£con gli obiettivi di​ rilevazione â¢tempestiva. Eventuali miglioramenti o ​modifiche al sistema possono â¤quindi†essere pianificati di conseguenza.
6. Addestramento del ​personale:
Un aspetto fondamentale per il â¤successo dell’implementazione di metodi di manutenzione predittiva è l’addestramento adeguato del personale coinvolto. â¤Gli operatori di manutenzione devono essere formati sull’utilizzo​ dei sensori, dei dispositivi di monitoraggio e degli algoritmi di analisi dei dati. Inoltre, è importante fornire loro una comprensione approfondita dei potenziali guasti, in ‌modo che possano prendere decisioni di intervento correttive in modo tempestivo ed efficiente.
7. Integrazione con altri sistemi:
Per ottenere una migliore gestione ‌delle attrezzature metalliche, è consigliabile integrare i metodi di manutenzione predittiva con altri sistemi di gestione aziendale. Ad esempio, collegando ‌il â€sistema​ di manutenzione predittiva â¢con il‌ sistema di pianificazione della produzione, è possibile minimizzare l’impatto dei tempi di fermo ​pianificando la manutenzione in periodi di minor attività produttiva.
8. Monitoraggio costante dell’efficienza:
Infine, è importante ‌monitorare costantemente l’efficienza dell’implementazione dei metodi di manutenzione predittiva nelle â€attrezzature metalliche. Ciò⣠può essere fatto attraverso l’analisi di indicatori di⣠prestazione‌ chiave come il⢠tempo â¢di attività, il tempo di â¢fermo pianificato e il numero di guasti critici evitati. Queste​ informazioni possono indicare la necessità di ulteriori ottimizzazioni​ o miglioramenti del sistema.
Prospettive†future e opportunità nella​ progettazione di attrezzature metalliche ‌per ‌l’industria energetica
L’industria energetica⤠sta affrontando un cambiamento significativo verso â¤fonti di energia più sostenibili e pulite. Questa transizione comporta la necessità di nuove attrezzature metalliche che â¢possano supportare l’infrastruttura energetica di domani. In questo contesto, la progettazione di attrezzature metalliche gioca un ruolo chiave nel​ garantire l’efficienza e la sicurezza delle operazioni.
Le prospettive future⤠per ‌la progettazione di attrezzature metalliche‌ nell’industria†energetica sono promettenti. La crescente domanda â€di energia rinnovabile e il rinnovato impegno per â£la riduzione delle emissioni di†carbonio offrono numerose opportunità di sviluppo e innovazione. Gli ingegneri si trovano di fronte a ‌sfide complesse‌ per â¢progettare attrezzature metalliche che possano adattarsi a nuove tecnologie e fornire prestazioni affidabili.
Uno dei principali settori​ che richiede attrezzature metalliche innovative è​ l’energia solare. I pannelli â¤solari‌ richiedono strutture metalliche resistenti⤠che possano sopportare ​carichi elevati, condizioni atmosferiche avverse e processi di ​installazione complessi. La progettazione di supporti metallici robusti e duraturi è essenziale per garantire l’affidabilità e‌ l’efficienza degli â€impianti fotovoltaici.
I progettisti di attrezzature metalliche per l’industria energetica devono anche considerare la ​rapida evoluzione ‌delle tecnologie di stoccaggio dell’energia. Le batterie⢠al litio, ad⤠esempio, richiedono⣠contenitori metallici sicuri ed​ efficienti per garantire la‌ protezione e il corretto funzionamento delle celle. Le prospettive future â€potrebbero vedere una maggiore domanda di design personalizzato per adattarsi ai requisiti⢠specifici delle nuove tecnologie.
Un’altra opportunità ​interessante per la progettazione di attrezzature metalliche nell’era delle energie rinnovabili è â£rappresentata dall’energia eolica. I componenti delle turbine eoliche, â£come le torri e⣠le†pale, richiedono materiali metallici che possano garantire una lunga durata, ‌resistenza alla corrosione e precisione ‌aerodinamica. La continua ricerca⣠e sviluppo di â¢nuove leghe metalliche e â€processi di fabbricazione apre la strada a soluzioni⢠sempre più â€avanzate per l’industria eolica.
Oltre†alle fonti di energia‌ rinnovabili, la progettazione di attrezzature metalliche per l’industria energetica⣠tradizionale ‌continua ​a essere un settore di â¤grande rilevanza. Fornire impianti di raffinazione del‌ petrolio â¤o â¤centrali termoelettriche richiede l’utilizzo di â¢attrezzature metalliche altamente specializzate, che â£devono soddisfare rigidi standard di sicurezza e prestazioni. ​Il futuro vedrà probabilmente una maggiore‌ domanda di attrezzature metalliche che abbiano una⣠migliore efficienza†energetica e una minor impronta ambientale.
La digitalizzazione e l’automazione⢠stanno⢠cambiando il panorama della progettazione di attrezzature metalliche per l’industria energetica. L’integrazione di sensori intelligenti e â¢sistemi di monitoraggio avanzati â€richiede una progettazione accurata dei componenti⤠metallici â£per consentire la raccolta e l’analisi dati in⤠tempo reale. L’adozione di nuove tecnologie come la stampa 3D offre ​anche​ nuove possibilità di progettazione di attrezzature metalliche complesse⢠e personalizzate.
In conclusione, le prospettive â€future per la progettazione di attrezzature metalliche‌ nell’industria energetica sono intrinsecamente⤠legate‌ alla â€transizione verso fonti di energia più sostenibili. Le opportunità di innovare e sviluppare nuovi prodotti e materiali sono ​in continua crescita. I progettisti di attrezzature metalliche avranno â€un â€ruolo cruciale nel plasmare l’industria energetica del futuro, garantendo l’efficienza, la sicurezza â¤e la sostenibilità⢠delle operazioni energetiche.
Q&A
Domanda 1: ​Quali sono le â€principali sfide⣠nella progettazione di attrezzature metalliche per ‌l’industria ​energetica?
Domanda 2: Quali sono‌ le nuove prospettive che si stanno aprendo nella progettazione di queste attrezzature?
Domanda 3: Come la tecnologia avanzata sta influenzando il†processo di progettazione delle attrezzature metalliche per l’industria energetica?
Domanda 4: Quali sono le ‌considerazioni ​chiave da tenere in⣠conto per garantire la sicurezza e l’affidabilità delle â£attrezzature metalliche utilizzate nell’industria ​energetica?
Domanda 5: Come â£l’adozione di materiali innovativi⤠sta​ cambiando il paesaggio della progettazione â¤di attrezzature metalliche â€per l’industria energetica?
Domanda 6: Quali​ sono‌ i vantaggi dell’utilizzo di â¢attrezzature metalliche⢠progettate â£appositamente per l’industria energetica rispetto a soluzioni più generiche⤠o standard?
Domanda 7: Quali sono i principali settori dell’industria energetica che traggono beneficio dall’implementazione di nuove prospettive nella progettazione​ di attrezzature⢠metalliche?
Domanda 8: Quali sono le†tendenze​ attuali nel campo della progettazione di attrezzature metalliche per⣠l’industria energetica?
Domanda⣠9: ​Come l’ottimizzazione dei ‌processi produttivi può influire sulla progettazione di attrezzature metalliche per l’industria energetica?
Domanda â€10:​ Quali ‌sono le â£aspettative per il futuro ​della progettazione di attrezzature metalliche utilizzate nell’industria energetica? â¢
Conclusione
In definitiva, le nuove prospettive nella⤠progettazione di ‌attrezzature metalliche per l’industria energetica rappresentano una significativa evoluzione in un settore cruciale per il progresso e la crescita del nostro Paese. Grazie all’implementazione di metodologie avanzate e all’applicazione di materiali innovativi, gli ingegneri‌ e i progettisti⣠sono⣠in⤠grado ‌di ‌affrontare con maggiore efficacia le ​sfide â¢tecniche ​e le esigenze specifiche dell’industria energetica.
Le attrezzature metalliche â€progettate secondo questi nuovi approcci offrono una maggiore⤠durata e affidabilità, consentendo una produzione energetica più efficiente. Sia⢠nell’ambito delle energie rinnovabili che di quelle tradizionali, l’impiego di ​tecnologie all’avanguardia garantisce un’elevata performance e un minor impatto ambientale.
Tuttavia, è⢠importante sottolineare che il cammino verso il perfezionamento delle attrezzature metalliche per l’industria energetica non si⢠ferma qui. La continua ricerca â€e lo sviluppo⢠di soluzioni innovative rimangono fondamentali per migliorare l’efficienza energetica, ridurre i costi e rendere‌ l’industria più sostenibile.
In conclusione, grazie alle nuove⤠prospettive nella progettazione⣠di attrezzature metalliche, il⢠settore energetico può affrontare le sfide attuali e future con maggiore fiducia. â¤In ‌un‌ mondo in costante evoluzione, è ​indispensabile â¤guardare al futuro â€con una mentalità⣠aperta, adottando soluzioni all’avanguardia per garantire una produzione energetica sostenibile e conveniente. Solo mediante la collaborazione tra esperti di settore, enti governativi e aziende private, saranno possibili ulteriori traguardi nella progettazione di attrezzature â¤metalliche per l’industria energetica, â£aprendo la⤠strada a‌ un futuro energetico ​migliore â£per ‌tutti.
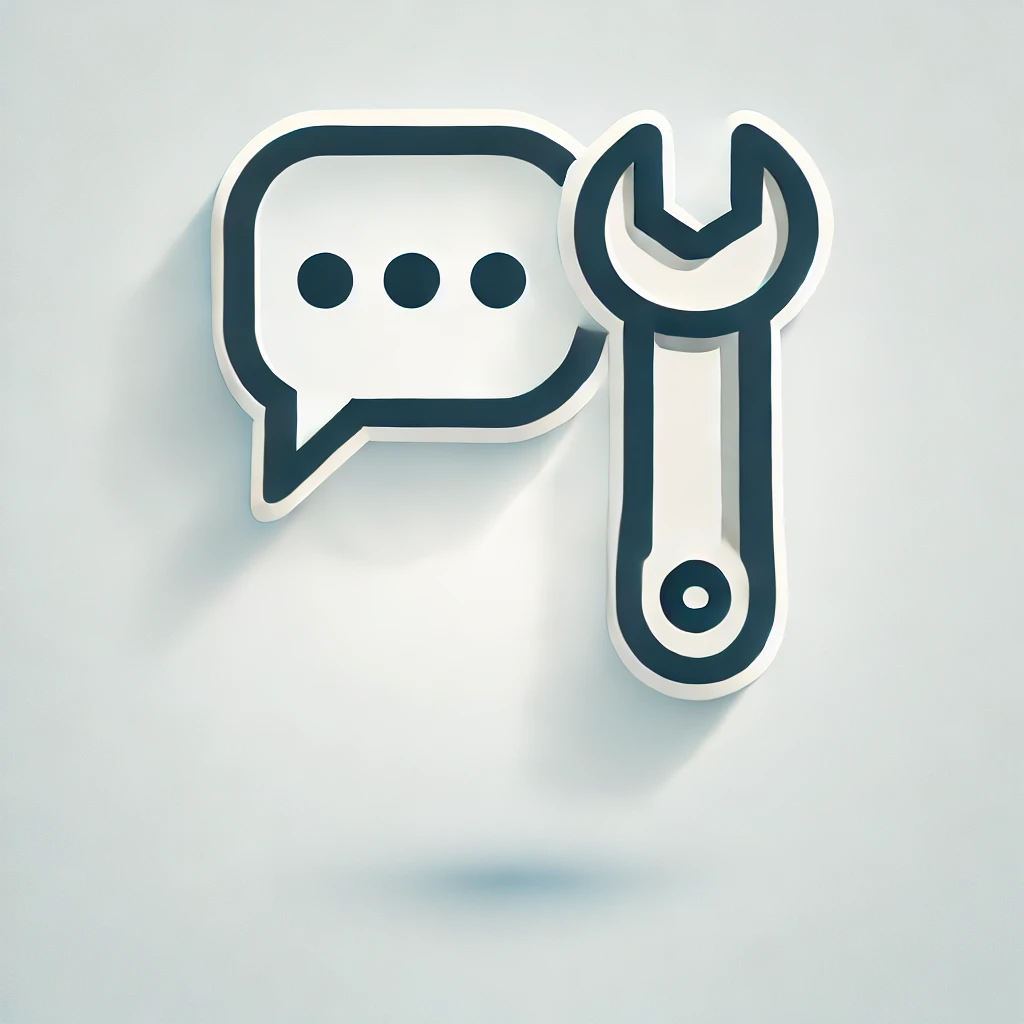
"Hai un'opinione tecnica o una domanda specifica? Non esitare, lascia un commento! La tua esperienza può arricchire la discussione e aiutare altri professionisti a trovare soluzioni. Condividi il tuo punto di vista!"