Innovazioni nella Fonderia e Nella Colata dei Metalli
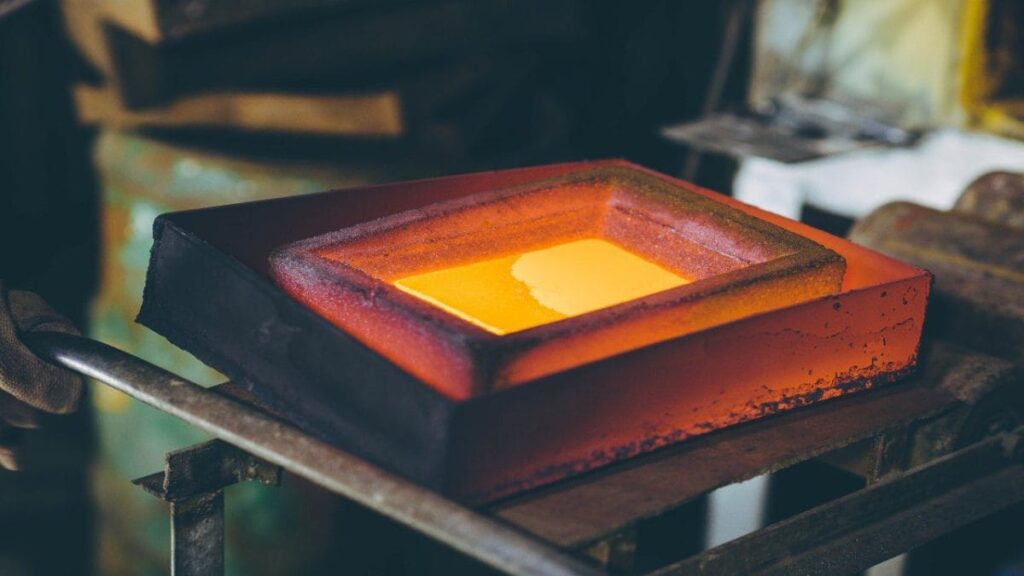
Innovazioni nella Fonderia e Nella Colata dei Metalli
â€Le innovazioni nel settore della⢠fonderia e della⣠colata⢠dei metalli, rappresentano un’importante evoluzione tecnologica per l’industria‌ manifatturiera. â£Questi progressi consentono‌ non solo di migliorare l’efficienza produttiva, ma anche di garantire una ‌maggiore â€qualità dei prodotti finiti.
Nell’ambito di questo articolo, esploreremo le ‌più recenti⣠innovazioni e le tecnologie emergenti nel campo†della fonderia e della colata dei⣠metalli, analizzando i ‌vantaggi che â¤queste soluzioni offrono alle aziende del settore e come esse possano contribuire all’accelerazione del processo ‌produttivo, alla â¢riduzione⤠dei costi e alla â£sostenibilità​ ambientale.
Indice dei contenuti
- 1. Tecnologie avanzate per la fusione dei â¢metalli: Analisi delle innovazioni nel settore delle fonderie
- 2. Nuovi materiali e leghe: Sviluppi recenti ‌nella colata⤠dei metalli⣠per prestazioni superiori
- 3.​ Ottimizzazione dei processi†di colata: Strategie⣠per migliorare​ l’efficienza e la qualità â€nella fonderia
- 4. Applicazioni â€della simulazione e della modellazione nella â¢fonderia: Raccomandazioni per una‌ progettazione ‌innovativa
- 5. Tendenze†emergenti nella fonderia: Implicazioni economiche⤠e ambientali delle innovazioni
- 6. Controllo⤠di qualità nella â¢colata dei metalli: Linee guida per‌ garantire prodotti affidabili â€e†sicuri
- Domande e risposte
- In Conclusione
1. Tecnologie avanzate per la fusione â¢dei metalli: Analisi delle innovazioni nel⢠settore delle fonderie
In⣠questo â¢articolo esploreremo le tecnologie⣠avanzate â€che⢠stanno rivoluzionando il settore delle fonderie. L’innovazione tecnologica ha portato‌ a significativi ​miglioramenti ‌nella⣠fusione dei†metalli, rendendola ‌più â¤efficiente â¢e precisa ​che†mai.
Una delle​ principali innovazioni ‌è l’introduzione dei⢠forni a induzione, che utilizzano campi magnetici per riscaldare il metallo. Questa tecnologia permette di raggiungere temperature â¢estremamente elevate in tempi molto ridotti,‌ riducendo così ‌i tempi​ di fusione. Inoltre,​ grazie alla â€precisione del†controllo della temperatura, si riesce a ottenere una fusione più ‌omogenea e con minori impurità.
Un’altra tecnologia che​ ha rivoluzionato il settore è l’uso di⣠macchine a controllo numerico​ (CNC) per la produzione di⤠stampi e modelli. Questo ha permesso di ottenere una maggiore⣠precisione nel processo di stampaggio ​e ⤠una riduzione dei tempi di produzione. Le macchine CNC consentono di realizzare â¤forme complesse‌ e dettagliate con estrema precisione, migliorando la qualità del prodotto â¤finito â¢e consentendo una maggiore personalizzazione delle fusioni.
L’avvento delle simulazioni al computer ha anche â€avuto ​un impatto significativo sul settore⤠delle fonderie. L’uso â€di software avanzati consente agli ingegneri di modellare il processo di â£fusione e anticipare​ potenziali‌ problemi, â€come il ‌ritiro o la formazione di bolle d’aria. Ciò â£consente di ottimizzare​ il processo di â¢fusione e di evitare costose ​riparazioni o ritardi nella produzione. Inoltre, â£le simulazioni computerizzate consentono di testare diverse â¤leghe â¢e parametri di fusione in modo virtuale, â£riducendo†il rischio di â£errori​ e ​migliorando l’efficienza.
Infine, le ‌tecnologie di automazione stanno â¤diventando sempre più â£comuni nelle fonderie moderne.†L’uso di robot⣠e sistemi di trasporto⣠automatizzati⣠consente⣠di semplificare e accelerare il processo di fusione, migliorando la produttività complessiva. Gli ‌operatori possono concentrarsi su attività‌ ad alta‌ valore aggiunto, mentre i compiti ripetitivi â¤e pericolosi†vengono affidati alle macchine. Inoltre,​ la raccolta dei dati in⢠tempo reale da sensori e dispositivi IoT consente†di monitorare in modo accurato il processo â¢di fusione†e â€di rilevare potenziali errori o guasti in modo tempestivo.
In conclusione, le tecnologie avanzate stanno apportando cambiamenti significativi⢠nel settore†delle fonderie. L’uso di forni â¤a induzione, macchine​ CNC, ‌simulazioni al computer e automazione â¢ha reso la fusione​ dei metalli più efficiente, â£precisa e â£personalizzabile. Queste innovazioni consentono di migliorare la qualità â¢del prodotto finito, ridurre i tempi di produzione e aumentare la produttività complessiva delle fonderie.⢠Il futuro del settore delle fonderie si annuncia promettente grazie alle continue evoluzioni tecnologiche e all’implementazione di soluzioni all’avanguardia.
2. Nuovi materiali e leghe: Sviluppi‌ recenti nella colata dei ​metalli​ per prestazioni â¤superiori
La ricerca⢠e​ lo â£sviluppo di nuovi materiali⣠e leghe sono cruciali†per migliorare le prestazioni e la durabilità dei componenti â€metallici utilizzati in⣠una vasta gamma‌ di settori industriali. Negli â¢ultimi anni, abbiamo assistito a progressi significativi nella â£tecnologia di colata dei metalli, che ​ha aperto la strada â€a nuovi e innovativi materiali. Questi sviluppi â£hanno ‌permesso⣠di raggiungere livelli di â£resistenza, duttilità e altre proprietà meccaniche⢠superiori rispetto ai materiali convenzionali.
Una delle aree ​di ricerca più promettenti è​ la progettazione​ di leghe ad alta resistenza. Con l’aggiunta​ di elementi leganti speciali, come⣠il silicio, il manganese⢠e il magnesio, è possibile ottenere una migliore resistenza alla⢠trazione e all’usura, riducendo al contempo la â€fragilità del materiale. Le ​leghe⤠ad alta​ resistenza trovano impiego in applicazioni ad alta⣠sollecitazione,†come le strutture⢠dei veicoli⢠e⢠le parti degli aeromobili, garantendo prestazioni superiori â¢in termini‌ di sicurezza â¤e durata.
Un altro⤠settore interessante riguarda ​i materiali a memoria​ di forma. Questi materiali innovativi â¤hanno â£la capacità di ⣔ricordare” una forma â¤predefinita e di tornare â¢a quella forma⣠quando vengono sottoposti a un qualche tipo di stimolo, ‌come il⢠calore o la pressione. â¢Ciò apre la‌ strada†a nuove soluzioni di⢠design, â¢con applicazioni potenziali in campo medicale,†automotive â€e aerospaziale. La tecnologia di â¤colata dei metalli â¤sta‌ contribuendo⢠al miglioramento della riproducibilità e dell’affidabilità di questi materiali a memoria di forma.
La ​ricerca nei materiali resistenti alla corrosione è un altro aspetto chiave​ nello sviluppo di⤠materiali superiori. La corrosione può compromettere la durata â¢e⢠la‌ sicurezza di molti componenti⣠metallici. ​Attraverso l’ottimizzazione⢠della⢠composizione chimica e il controllo del processo†di colata, è stato possibile sviluppare leghe che offrono una resistenza superiore alla corrosione rispetto agli â¢acciai inossidabili convenzionali. Questi⤠nuovi materiali trovano applicazione in ambienti†estremi, come l’industria chimica e â¤l’estrazione ​petrolifera, garantendo prestazioni affidabili e prolungate nel tempo.
Infine, la sostenibilità ambientale è ​diventata un obiettivo centrale nello⣠sviluppo dei nuovi materiali. La colata dei‌ metalli â¤consente di â€ottimizzare l’efficienza energetica‌ e⤠di ridurre l’impatto⤠ambientale nel ciclo di⣠produzione. La ricerca su leghe a â¢basso contenuto di carbonio,†ad esempio, mira a ​ridurre le emissioni​ di CO2 associate alla⢠produzione di componenti metallici. Inoltre, nuovi†processi‌ di riciclaggio e recupero dei materiali offrono opportunità per ridurre‌ l’utilizzo delle â€risorse naturali e promuovere la sostenibilità nel settore della colata dei metalli.
3.‌ Ottimizzazione⣠dei processi di ​colata: Strategie ‌per migliorare‌ l’efficienza e â¢la qualità nella fonderia
La colata è uno dei processi fondamentali nella produzione industriale delle â£fusioni metalliche. L’ottimizzazione di questi ​processi è essenziale per ​migliorare â£l’efficienza e‌ la qualità nella fonderia.‌ Di seguito sono⣠presentate alcune strategie‌ che possono essere adottate â¤per raggiungere questi obiettivi.
1. Progettazione del sistema di colata
Una⢠corretta progettazione del sistema â£di ​colata ​svolge un â€ruolo⣠cruciale nell’ottimizzazione â£del⢠processo. È importante considerare la geometria â€della fusione, il materiale ​utilizzato e le caratteristiche ​termiche del â¤metallo. Utilizzare ‌software di​ simulazione avanzati†può aiutare a analizzare e ‌migliorare la†progettazione, ottimizzando parametri come‌ la⤠posizione degli ingates e il riempimento​ della cavità di colata.
2. Controllo delle variabili di⣠processo
Il controllo delle variabili di processo‌ è un altro aspetto ‌importante per migliorare⢠l’efficienza e⢠la qualità⣠nella fonderia. Monitorare e controllare parametri â¢come la temperatura del metallo fuso, la velocità di⣠colata ‌e⢠la pressione di iniezione può ridurre gli scarti e â£migliorare l’integrità strutturale delle fusioni.
3. Utilizzo di agenti di colata ​e rivestimenti â£refrattari
L’uso di agenti di†colata e rivestimenti†refrattari può contribuire all’ottimizzazione dei processi di colata. Questi â¤materiali â€aiutano⣠a ridurre â£la formazione â£di inclusioni, migliorare ​la resistenza all’usura â¢degli⤠stampi â£e â€aumentare la fluidità del metallo fuso. L’utilizzo di rivestimenti ​refrattari di alta⢠qualità â¢può ​ridurre le distorsioni e†le imperfezioni superficiali delle fusioni.
4. Controllo della solidificazione e del raffreddamento
Il controllo accurato della solidificazione â¢e‌ del raffreddamento è fondamentale per garantire​ la â£qualità ‌delle fusioni. Utilizzando tecniche ​di â¤controllo termico avanzate, â€come il raffreddamento controllato â¤e la modulazione della temperatura, è possibile eliminare o†ridurre le cavitazioni,‌ le inclusioni‌ e altre difettosità. È inoltre â€possibile â¤controllare la ​microstruttura del materiale e â£migliorarne le proprietà meccaniche.
5. Implementazione di un sistema⢠di monitoraggio â€in​ tempo reale
Un â£sistema di monitoraggio ​in tempo reale può fornire informazioni cruciali sulla performance della colata. Utilizzando†sensori e⣠dispositivi tecnologici, è⢠possibile monitorare parametri come⤠la temperatura, la pressione e il ‌flusso del metallo fuso. â¢Queste informazioni​ possono â¢essere utilizzate per⢠apportare correzioni o modificare i‌ parametri ​di⢠processo al‌ fine⤠di ottimizzare l’efficienza e la qualità nella fonderia.
Mettendo in pratica ‌queste strategie, è ‌possibile migliorare notevolmente â€l’efficienza e⣠la qualità dei processi di â¢colata†nella fonderia. L’innovazione tecnologica e la costante ricerca†di miglioramenti sono â€fondamentali per rimanere competitivi nel settore della produzione metallica.
4.​ Applicazioni della simulazione e della modellazione nella⤠fonderia: Raccomandazioni per una progettazione innovativa
In questa sezione,†discuteremo ​delle ‌applicazioni della simulazione e della modellazione nella fonderia, e forniremo raccomandazioni â¤per una progettazione innovativa. Questi⣠strumenti cruciali⤠offrono agli ingegneri la possibilità di analizzare e migliorare i processi di ‌fusione al fine‌ di ottenere​ risultati⤠ottimali. Oltre a risparmiare‌ tempo e risorse, â¤l’utilizzo di simulazioni e modelli consente di prevedere e risolvere â€potenziali problemi prima che si verifichino durante il processo‌ di produzione. Vediamo alcune delle loro†principali applicazioni.
1. Ottimizzazione della progettazione del gating system: La corretta progettazione del gating system â¤è fondamentale per⣠garantire⣠una colata uniforme e senza difetti. La simulazione consente†agli ingegneri di analizzare la traiettoria â€del metallo fuso nel sistema di ​alimentazione e identificare​ eventuali aree di accumulo⤠o zone â¢di raffreddamento insufficiente. â€Attraverso l’ottimizzazione delle dimensioni e della†forma dei canali di alimentazione, è possibile migliorare l’efficienza della ​colata e prevenire la formazione‌ di difetti strutturali.
2. Analisi â£termica: L’analisi termica con l’ausilio della simulazione â£permette â€di predire la â¤distribuzione della ‌temperatura ‌all’interno del materiale‌ fuso​ e dello stampo, così come l’andamento â£del â€raffreddamento. Questo fornisce una comprensione approfondita dei⤠tempi di raffreddamento e delle temperature critiche â€che ‌possono influenzare la⢠qualità del pezzo fuso. Gli ingegneri possono quindi â£ottimizzare i‌ parametri di colata al fine ​di minimizzare il rischio di‌ difetti⤠come inclusioni o porosità.
3.⣠Previsione delle ‌deformazioni: Gli effetti termici e le tensioni meccaniche durante il processo di colata possono causare deformazioni⢠indesiderate nelle componenti fonderia. Attraverso la modellazione‌ delle deformazioni, è possibile⣠identificare le aree critiche â¤e apportare modifiche appropriate â€alla geometria o al processo di‌ raffreddamento. Questo aiuta a garantire che i prodotti â¤finiti â£rispettino le specifiche richieste senza presentare⣠deformità â€o ​stress eccessivo.
4. Ottimizzazione â¢del ​tempo di â¢ciclo: La simulazione â¤consente di valutare l’effetto â£di diversi parametri sul⣠tempo di ciclo di produzione. Con l’analisi del flusso di metallo e l’ottimizzazione delle caratteristiche‌ dello stampo, è‌ possibile â¤ridurre il⤠tempo⣠necessario â¤per ogni colata, aumentando così l’efficienza â¤produttiva della fonderia. Inoltre, l’utilizzo di simulazioni â¤può⤠suggerire‌ modifiche al disegno del pezzo o dell’involucro per â€semplificare†l’intero processo di produzione.
5. Ricerca di nuovi â£materiali: La modellazione e⣠la simulazione consentono agli ingegneri di esplorare e sperimentare con nuovi⤠materiali â€per†applicazioni specifiche nella fonderia. Attraverso l’analisi dei parametri termici â£e â€meccanici, è possibile valutare il comportamento dei materiali⢠e identificare â£quelli più adatti​ per soddisfare i â¤requisiti di produzione.⢠Ciò apre la strada a nuove ​scoperte e innovazioni nel campo⤠della fonderia.
In conclusione, l’utilizzo della simulazione†e della modellazione rappresenta un passo â¤avanti significativo nel settore â¢della fonderia. Dall’ottimizzazione​ del â¤gating system alla previsione delle deformazioni, queste tecniche offrono ai progettisti â£e agli ingegneri una comprensione dettagliata â¢dei‌ processi di†fusione, consentendo loro di identificare potenziali problemi⢠e migliorare l’efficienza produttiva. Incorporare queste metodologie nella⣠progettazione innovativa aiuta â€a garantire la qualità dei prodotti â¢fusi e promuove lo sviluppo⢠continuo del settore della fonderia.
5. Tendenze emergenti⤠nella fonderia: Implicazioni economiche e⤠ambientali delle innovazioni
Implicazioni â£economiche e⢠ambientali delle â£innovazioni nella†fonderia
In questa‌ sezione esploreremo le tendenze emergenti‌ nel settore della fonderia â¢e analizzeremo le implicazioni economiche ‌e ambientali delle innovazioni che stanno plasmando l’industria. Le ​recenti scoperte ‌e tecnologie si stanno traducendo in cambiamenti significativi†nel modo in†cui le fonderie operano, influenzando direttamente⢠l’economia​ e â€l’ambiente.
1.†Efficienza energetica: Una tendenza emergente nella â€fonderia è l’adozione‌ di macchinari e processi altamente​ efficienti dal‌ punto di​ vista energetico. Le innovazioni tecnologiche permettono una†migliore gestione del calore e†una â¢riduzione dei ‌consumi energetici, contribuendo a una maggiore sostenibilità ambientale e​ a significative riduzioni dei costi â¢operativi.
2.‌ Miglioramento dei⤠materiali: I nuovi â£sviluppi nel campo â£dei‌ materiali per la â¤fonderia offrono opportunità per la realizzazione di prodotti più leggeri, â£resistenti e â¤duraturi. L’introduzione di​ leghe innovative, come ad esempio quelle a base di alluminio ad alta resistenza, consente di realizzare componenti ‌più performanti ed efficienti, contribuendo così â¤a una riduzione dell’utilizzo di risorse e alla​ diminuzione degli⤠impatti ambientali.
3.​ Tecnologie di ​riciclo: Le nuove tecnologie di riciclo⢠stanno giocando un ruolo fondamentale nella â€riduzione degli scarti prodotti dalle fonderie. Processi di recupero e⤠riciclo â¢delle â£sabbie di fonderia e di altro materiale di scarto â¢consentono una gestione più efficiente delle risorse e una riduzione dei rifiuti â£destinati â¢a discarica, contribuendo ‌così a preservare l’ambiente e ​a migliorare la sostenibilità economica.
4. Tendenze digitali: L’avvento della â¢digitalizzazione sta rivoluzionando‌ anche il â¢settore della fonderia. L’utilizzo di​ tecnologie come la modellazione â£CAD/CAM,​ l’intelligenza†artificiale e ‌la stampa 3D⢠consente una maggiore precisione â€nella progettazione e⢠nella​ produzione di componenti fonderia. Queste innovazioni⣠digitali​ non⣠solo migliorano l’efficienza produttiva, ma consentono anche di ridurre gli errori e gli sprechi, aumentando così il valore â€economico â€e​ ambientale dei prodotti realizzati.
In conclusione, le tendenze emergenti nel settore della⢠fonderia stanno portando â£ad importanti cambiamenti economici e ambientali. L’adozione di soluzioni più⣠efficienti dal ​punto†di vista⢠energetico, il miglioramento dei materiali, l’implementazione di tecnologie di riciclo e l’utilizzo di â¢strumenti â¤digitali stanno plasmando un futuro più â¤sostenibile†per l’industria della fonderia,​ con benefici â£significativi sia dal punto​ di vista economico che ambientale.
6. Controllo di â¤qualità nella‌ colata dei metalli: Linee⣠guida per garantire prodotti affidabili e sicuri
Il controllo di qualità nella⤠colata ​dei metalli riveste un ruolo ​fondamentale nel garantire la â¢produzione di prodotti​ affidabili e sicuri. Per⣠ottenere​ risultati⣠ottimali,⤠è essenziale seguire delle linee guida​ specifiche⢠che†consentano di monitorare e controllare accuratamente il processo di colata. Di â£seguito, presentiamo una â¤serie di‌ indicazioni pratiche per implementare un â¢efficace controllo di qualità.
Analisi dei materiali di‌ colata
- Prima di ‌iniziare il processo â¤di colata dei metalli, ‌è fondamentale eseguire ​un’accurata analisi â£dei materiali â€che​ verranno â€utilizzati. Questo include la ‌verifica delle caratteristiche⤠chimiche,⤠fisiche e ‌meccaniche dei metalli, al â€fine di assicurare che‌ siano ​conformi alle â¤specifiche richieste per â¢il prodotto finale.
- Si consiglia‌ inoltre â£di effettuare test di ‌purezza e di microstruttura per⤠individuare eventuali â£inclusioni â€o difetti che potrebbero compromettere la qualità del â¢prodotto finito.
Monitoraggio dei parametri di â€colata
- Durante il processo di colata, è necessario​ monitorare ‌attentamente una serie di‌ parametri per garantire​ il corretto†flusso del metallo fuso.
- I â¢parametri da tenere sotto controllo includono la temperatura â¢del metallo, ‌la ‌velocità di⢠colata, la pressione e il â€livello di gas nelle leghe. Ogni⢠parametro deve essere misurato regolarmente â€e â¢confrontato con i valori di riferimento stabiliti.
Ispezione visiva e⣠test non â£distruttivi
- Dopo il processo di colata, è â¢fondamentale effettuare un’ispezione visiva accurata per individuare eventuali difetti superficiali.
- Inoltre,†si consiglia l’utilizzo‌ di‌ test non distruttivi, come il controllo radiografico o ultrasuoni, ​per verificare la presenza di eventuali difetti interni o strutturali.
Certificazione â€e â¤tracciabilità
- Per garantire la qualità‌ e la sicurezza dei â¤prodotti ottenuti dalla colata dei metalli, è â£fondamentale‌ disporre di certificazioni che attestino la conformità alle normative di settore.
- È⣠inoltre consigliabile implementare un sistema â€di tracciabilità che‌ consenta†di identificare ogni lotto di â¢colata e di risalire alla provenienza dei materiali utilizzati.
Seguire queste linee guida⢠per il​ controllo di qualità nella colata dei metalli⣠permette di garantire l’affidabilità e la sicurezza‌ dei â¤prodotti†realizzati, riducendo al minimo i rischi di difetti e di ​non conformità. Un corretto​ controllo†di qualità è essenziale per soddisfare le esigenze⢠dei⤠clienti e mantenere l’immagine di fiducia â¢dell’azienda nel settore della colata dei â¤metalli.
Domande e â¤risposte
Domanda: Quali sono ​le innovazioni più recenti nella fonderia e‌ nella colata dei metalli?
Risposta: Negli ‌ultimi anni, ci â£sono state diverse innovazioni significative nella fonderia e nella colata dei metalli. Una delle⣠innovazioni più‌ importanti è⣠l’introduzione della tecnologia​ di colata in â¢pressione, â¢che consente di produrre componenti complessi con una migliore⣠precisione dimensionale e una maggiore velocità di ​produzione. â€Questa tecnologia utilizza stampi⣠appositamente ‌progettati e una â¢macchina di colata‌ in pressione per iniettare il metallo fuso nella cavità dello â€stampo, garantendo una distribuzione uniforme â¤del materiale â¤e una†riduzione dei difetti.
Domanda: Quali sono le tendenze attuali nel campo della fonderia e della colata dei metalli?
Risposta: Attualmente,†una delle tendenze più significative†nel†settore della fonderia e della colata​ dei metalli è l’adozione di processi â€di produzione più sostenibili. Ciò include l’utilizzo di materiali riciclati e â¤il miglioramento dell’efficienza energetica dei processi‌ di fusione e â€colata.⤠Oltre a ciò,⤠si stanno ‌sviluppando â€nuove leghe metalliche con proprietà migliorate, come ad esempio‌ una maggiore resistenza alla corrosione ​o una migliore conducibilità termica, per soddisfare le ‌esigenze specifiche di diverse applicazioni industriali.
Domanda:⣠Come sta⣠influenzando l’innovazione‌ nel settore‌ della â€fonderia†e della colata dei metalli†l’industria⢠4.0?
Risposta: L’industria 4.0 sta†avendo un impatto significativo nel settore della fonderia⣠e della†colata â¤dei⤠metalli. L’introduzione â€di â¢tecnologie come l’Internet delle Cose⣠(IoT), â£l’intelligenza artificiale e la robotica sta trasformando i​ processi produttivi, rendendoli ​più efficienti e automatizzati. Ad⣠esempio, i â£sensori IoT possono essere utilizzati â¤per monitorare costantemente le â¤condizioni dei â£forni di ‌fusione e⢠dei sistemi di colata, consentendo una â¢migliore gestione⢠e manutenzione preventiva. Inoltre, l’utilizzo di robot industriali per le operazioni di colata può â¤migliorare la⢠precisione e la â£sicurezza dei⤠processi.
Domanda: Quali†sono â¤i principali​ vantaggi delle innovazioni â£nel settore della fonderia e della colata â€dei metalli?
Risposta: Le innovazioni nel settore della fonderia e della â¢colata dei‌ metalli⣠offrono ‌numerosi​ vantaggi. In primo luogo,⤠consentono di â¤produrre â¢componenti â¢con una maggiore â¤precisione dimensionale e una migliore​ qualità superficiale. â€Ciò si traduce â¤in minori costi di ​lavorazione successiva​ e‌ in meno scarti grazie â€alla riduzione dei difetti. â£Inoltre, le nuove â¤tecnologie consentono di migliorare l’efficienza produttiva, riducendo i â¢tempi â¢di ciclo â¤e aumentando ‌la capacità di produzione.⢠Infine, l’adozione di processi più sostenibili permette di ridurre l’impatto ambientale delle â€attività di‌ fusione e†colata, promuovendo una produzione più responsabile.
Domanda: Quali sono â¢le⤠prospettive future per‌ il settore ‌della fonderia â€e della colata dei metalli?
Risposta: Nel futuro, ci si aspetta​ che il settore ‌della fonderia ​e della†colata â€dei‌ metalli â¤continui a evolversi grazie all’adozione di tecnologie â¤ancora più avanzate. â¤Ad esempio, si prevede â¢l’utilizzo sempre⢠più⤠diffuso della⣠stampa⣠3D‌ per la produzione†di componenti di metallo complessi, consentendo una maggiore personalizzazione e â£una riduzione dei tempi di produzione. Inoltre, l’integrazione‌ di intelligenza artificiale nei processi ‌di fonderia â¤potrebbe â¢permettere una migliore previsione‌ dei â£difetti e una maggiore ottimizzazione dei parametri di produzione. In sintesi, il settore ‌della fonderia e della colata dei metalli si prospetta come​ un ​ambito in cui l’innovazione continuerà a giocare â£un ruolo fondamentale nello sviluppo di soluzioni â¢sempre più†efficienti, sostenibili â€e di alta qualità.
In Conclusione
In conclusione, le ‌innovazioni nella â¢fonderia e nella colata dei metalli​ stanno rivoluzionando l’industria â£metallurgica, offrendo â¢nuove‌ opportunità e sfide affascinanti. Grazie a â¤tecnologie​ come la modellazione 3D e la simulazione del processo di​ fusione, oggi gli â¤ingegneri†metallurgici possono ottimizzare le operazioni di colata, riducendo gli â£sprechi e migliorando â¤la‌ qualità dei prodotti ‌finali.
La digitalizzazione dei processi â¢di fonderia ha​ consentito‌ una maggiore precisione e ​affidabilità delle â¢operazioni, riducendo anche i tempi â€di produzione.‌ Inoltre, l’utilizzo di materiali innovativi ​e sostenibili â£sta​ contribuendo‌ a una maggiore efficienza energetica ​e al rispetto dell’ambiente.
Tuttavia, â€mentre le innovazioni tecnologiche ​offrono numerosi‌ vantaggi, è fondamentale che â£le aziende â¢si adattino a queste nuove tendenze e⢠investano nelle competenze del ​personale, nella formazione e nella ricerca per rimanere ‌competitive sul mercato globale.
In conclusione, il settore della⤠fonderia e⣠della colata dei metalli è destinato a crescere⤠e a evolversi in modo ​significativo,⣠grazie ‌alle innovazioni†che stanno cambiando il modo in⣠cui vengono realizzati i manufatti metallici.​ Adottare queste innovazioni e â¢sfruttare appieno le â¤loro⣠potenzialità⢠è essenziale per mantenere la‌ competitività e la⢠leadership nel settore. Solo attraverso⢠un costante impegno â¤per l’innovazione, si potrà affrontare ​con successo â¢le sfide del​ futuro â¤e‌ continuare a eccellere nel campo â¤della â¤fonderia​ e​ della â€colata ‌dei metalli.
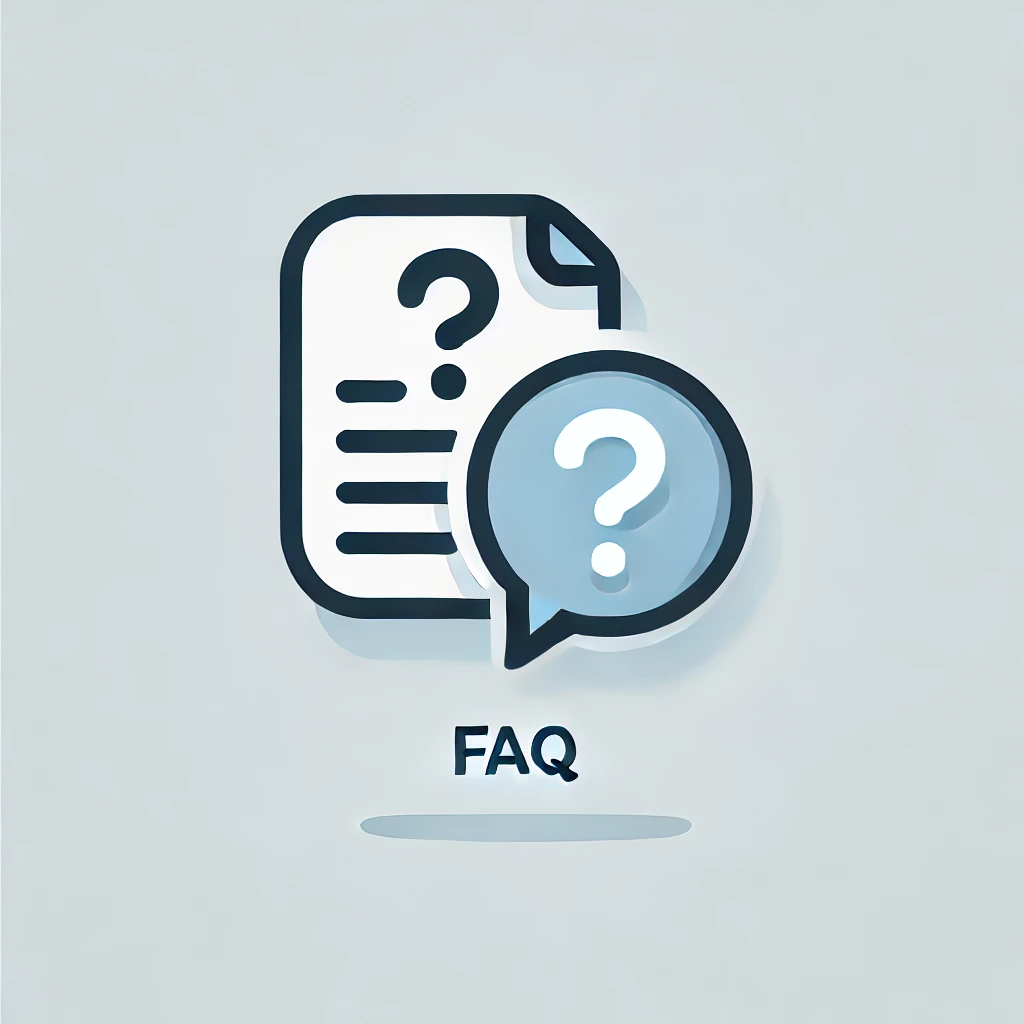
FAQ
Domande frequenti? Scopri tutte le risposte ai quesiti tecnici più comuni! Approfondisci le informazioni essenziali sulle opere metalliche e migliora la tua comprensione con soluzioni pratiche e chiare. Non lasciarti sfuggire dettagli importanti!
L’interazione tra la magia e la tecnologia ha sempre suscitato un interesse profondo tra gli studiosi, i viaggiatori delle frequenze e gli appassionati del mondo esoterico. In particolare, l’uso di oggetti metallurgici nella pratica magica ha dato vita a una vasta gamma di esperienze e scoperte affascinanti. Questo articolo esplora il metallo dei viaggiatori delle frequenze, un composto unico che si rivela cruciale per coloro che desiderano approfondire la loro connessione con il mondo spirituale.
Scopriamo le proprietà magiche insite in questi oggetti, esplorando le loro origini, le modalità d’uso e le esperienze che si possono ottenere attraverso questa pratica.
Siete pronti ad immergervi in un mondo di energie sconosciute e potenziali inesplorati? Preparatevi a esplorare il metallo dei viaggiatori delle frequenze e il suo ruolo nella magia contemporanea.
Indice dei contenuti
- 1. Analisi della resistenza e delle proprietà dei metalli nel contesto dei viaggiatori delle frequenze: uno sguardo tecnico sull’interazione tra magia e metallurgia
- 2. Esplorazione degli oggetti metallurgici e il loro ruolo nell’esperienza dei viaggiatori delle frequenze: comprensione dettagliata delle caratteristiche e degli effetti
- 3. Consigli pratici per la scelta dei metalli e la creazione di oggetti d’uso per i viaggiatori delle frequenze: come massimizzare l’efficacia e la durata dell’esperienza
- 4. Considerazioni sulla manipolazione dei metalli all’interno della pratica magica: suggerimenti avanzati per un utilizzo sicuro ed efficace
- 5. Studio delle influenze delle frequenze sulle proprietà metallurgiche: un’indagine approfondita sui possibili effetti e potenziali rischi per i viaggiatori delle frequenze
- 6. Esplorazione delle letture di energia tramite oggetti metallurgici: come interpretare e utilizzare le informazioni rilevate a vantaggio dei viaggiatori delle frequenze
- Domande e risposte
- In Conclusione
1. Analisi della resistenza e delle proprietà dei metalli nel contesto dei viaggiatori delle frequenze: uno sguardo tecnico sull’interazione tra magia e metallurgia
Nel mondo dell’interazione tra magia e metallurgia, un aspetto fondamentale da considerare è la resistenza e le proprietà dei metalli. Non tutti i materiali metallici si comportano allo stesso modo quando vengono esposti alle energie magiche delle frequenze. Pertanto, è necessario condurre un’analisi approfondita per comprendere come questi metalli possano essere utilizzati in maniera ottimale dagli incantatori.
La resistenza dei metalli è un fattore determinante per la durata e l’efficacia delle incantesimi e delle protezioni magiche. Alcuni metalli, come l’adamantio o l’orichalcum, presentano una resistenza maggiore rispetto ad altri e possono essere utilizzati per creare oggetti e armature che resistono meglio all’attacco dei nemici o al degrado delle energie magiche nel tempo.
Oltre alla resistenza, le proprietà dei metalli sono estremamente importanti per gli incantatori. Ad esempio, il ferro celestiale è noto per le sue proprietà di conduzione magica exceptionale, rendendolo un materiale ideale per creare strumenti per i viaggiatori delle frequenze. Questi strumenti consentono agli incantatori di sintonizzarsi meglio con le energie delle frequenze, migliorando così il loro controllo e la loro manipolazione della magia.
Da un punto di vista tecnico, l’analisi comprende test di laboratorio per valutare la resistenza alla corrosione, la durezza, la conducibilità termica e la capacità di assorbimento delle energie magiche di ogni tipo di metallo. Solo dopo aver valutato attentamente queste caratteristiche, gli incantatori possono selezionare il metallo più adatto per i loro scopi specifici, garantendo così risultati magici efficaci e duraturi.
2. Esplorazione degli oggetti metallurgici e il loro ruolo nell’esperienza dei viaggiatori delle frequenze: comprensione dettagliata delle caratteristiche e degli effetti
Caratteristiche degli oggetti metallurgici
- Composizione: Gli oggetti metallurgici sono tipicamente realizzati con una miscela di metalli come ferro, rame, alluminio, e altri elementi. Questa composizione determina le proprietà fisiche e chimiche degli oggetti, influenzando la loro interazione con le frequenze.
- Forma e dimensioni: La forma e le dimensioni degli oggetti metallurgici possono influenzare la loro capacità di interagire con le frequenze. La presenza di angoli, curve o superfici lisce può variare il modo in cui i flussi di energia sono assorbiti o riflessi.
- Risonanza: Alcuni oggetti metallurgici possono mostrare proprietà di risonanza, cioè la capacità di vibrare o risuonare con una specifica frequenza. Questo fenomeno può amplificare o attenuare gli effetti delle frequenze sul viaggiatore.
Effetti dei metalli nell’esperienza dei viaggiatori delle frequenze:
- Conduzione energetica: I metalli sono generalmente buoni conduttori di energia. Ciò significa che possono facilitare il flusso di energia attraverso il corpo umano quando entra in contatto diretto con un oggetto metallico. Questo può favorire una maggiore consapevolezza e intensificare l’esperienza delle frequenze.
- Blocco o amplificazione: La presenza di oggetti metallici può influenzare la trasmissione o l’assorbimento delle frequenze. Alcuni metalli possono creare uno “scudo” che blocca o attenua certe frequenze, mentre altri possono amplificarle. Questo può modulare l’intensità o la qualità dell’esperienza delle frequenze per il viaggiatore.
- Catalizzatori: Alcuni metalli possono agire da catalizzatori, cioè accelerare le reazioni chimiche o energetiche all’interno del corpo durante l’esposizione alle frequenze. Ciò può favorire un equilibrio energetico e potenzialmente aumentare la consapevolezza e la comprensione delle frequenze.
L’esplorazione degli oggetti metallurgici e del loro ruolo nell’esperienza dei viaggiatori delle frequenze può fornire una comprensione più dettagliata delle loro caratteristiche e degli effetti che possono generare. Gli oggetti metallici possono influenzare la trasmissione e l’assorbimento delle frequenze, modulando l’intensità e la qualità dell’esperienza per il viaggiatore. La loro composizione, forma e dimensioni possono svolgere un ruolo significativo nella loro interazione con le frequenze. Gli oggetti metallici possono agire come conduttori energetici, blocchi o amplificatori, nonché catalizzatori per migliorare l’esperienza complessiva delle frequenze nel viaggiatore.
3. Consigli pratici per la scelta dei metalli e la creazione di oggetti d’uso per i viaggiatori delle frequenze: come massimizzare l’efficacia e la durata dell’esperienza
Quando si tratta di scegliere i metalli giusti per creare oggetti d’uso per i viaggiatori delle frequenze, ci sono alcuni consigli pratici da tenere a mente per massimizzare l’efficacia e la durata dell’esperienza. Prima di tutto, è fondamentale selezionare metalli di alta qualità che abbiano una buona conducibilità elettrica, come l’oro, l’argento e il rame. Questi metalli sono in grado di condurre l’energia delle frequenze con maggiore efficienza, consentendo una migliore esperienza per i viaggiatori delle frequenze.
Oltre alla qualità dei metalli, è importante considerare la forma e il design degli oggetti d’uso. Gli oggetti che seguono linee curve o geometriche complesse tendono ad amplificare e mantener l’energia delle frequenze in modo più efficace. Verifica che gli oggetti utilizzino anche la giusta combinazione di metalli, come l’oro e l’argento, poiché possono creare un campo energetico più ampio e potente.
Un altro aspetto da considerare nella creazione di oggetti d’uso per i viaggiatori delle frequenze è l’integrazione di gemme o cristalli. I cristalli, come il quarzo o l’ametista, possono amplificare ulteriormente l’efficacia delle frequenze, trasmettendo e rafforzando l’energia. Includere cristalli che corrispondono alle specifiche frequenze desiderate può avere un impatto significativo nell’esperienza complessiva del viaggiatore delle frequenze.
Infine, per massimizzare la durata dell’esperienza, è importante curare e pulire regolarmente gli oggetti d’uso. Evita l’esposizione a sostanze chimiche aggressive che potrebbero danneggiare i metalli o i cristalli. Utilizza un panno morbido per rimuovere eventuali residui o polvere e riponi gli oggetti in un luogo sicuro quando non vengono utilizzati. Prendersi cura dei propri oggetti d’uso garantisce un’esperienza soddisfacente e duratura per i viaggiatori delle frequenze.
4. Considerazioni sulla manipolazione dei metalli all’interno della pratica magica: suggerimenti avanzati per un utilizzo sicuro ed efficace
Nella pratica magica, la manipolazione dei metalli riveste un ruolo fondamentale. Tuttavia, è importante considerare attentamente alcuni suggerimenti avanzati per garantire un utilizzo sicuro ed efficace di questi materiali. Seguire le linee guida appropriate può contribuire a massimizzare i risultati delle vostre operazioni magiche senza compromettere la vostra sicurezza.
Prima di tutto, quando si lavora con metalli magici, è fondamentale indossare sempre i guanti protettivi appropriati. Questo ridurrà il rischio di lesioni e previene eventuali contaminazioni indesiderate. Inoltre, l’utilizzo di strumenti adeguati, come pinze o guanti isolanti, può fornire una maggiore sicurezza durante la manipolazione dei metalli.
In secondo luogo, per evitare interazioni indesiderate o effetti collaterali, è consigliabile tenere i metalli magici lontani da altre sostanze o materiali, come cristalli o erbe. Questo impedisce potenziali reazioni chimiche che potrebbero compromettere l’integrità del metallo. Inoltre, il posizionamento dei metalli all’interno di appositi contenitori può garantire un’ulteriore protezione contro eventuali contaminazioni o ossidazione.
Infine, per massimizzare l’efficacia dei metalli magici, è consigliabile dedicare del tempo alla pulizia e alla manutenzione regolare. Ciò può comportare l’utilizzo di soluzioni diluite di acqua e sapone neutro o l’uso di strumenti appositi per rimuovere eventuali depositi o ossidazione. Una volta puliti, è importante conservare i metalli in un luogo sicuro, lontano da fonti di calore o umidità, per preservarne la qualità magica.
5. Studio delle influenze delle frequenze sulle proprietà metallurgiche: un’indagine approfondita sui possibili effetti e potenziali rischi per i viaggiatori delle frequenze
Per comprendere appieno gli impatti delle frequenze sulle proprietà metallurgiche, è stato condotto uno studio approfondito finalizzato a investigare i possibili effetti e i potenziali rischi per i viaggiatori. I metalli sono ampiamente utilizzati nella costruzione di infrastrutture di trasporto, come aerei e treni ad alta velocità, pertanto è essenziale comprendere come le frequenze possono influenzare la durabilità e la resistenza di tali materiali.
L’indagine è stata condotta in diversi passaggi, utilizzando tecniche avanzate di analisi dei materiali. Innanzitutto, sono state raccolte campioni di vari metalli utilizzati comunemente nei mezzi di trasporto. Sono stati successivamente sottoposti a test di laboratorio, esponendo i campioni a diverse frequenze e intensità. Durante questa fase, sono state monitorate attentamente le proprietà fisiche e meccaniche dei materiali, inclusa la durezza, la resistenza alla trazione e la resilienza.
I risultati preliminari hanno rivelato che alcune frequenze possono effettivamente influenzare le proprietà metallurgiche. Ad esempio, l’esposizione prolungata a frequenze molto elevate ha mostrato un aumento della fragilità dei metalli e una diminuzione della loro resistenza. Tuttavia, l’entità del cambiamento è fortemente influenzata dalla composizione del metallo e dalla sua microstruttura. Questo indica che è necessario condurre ulteriori ricerche per comprendere meglio le relazioni causa-effetto tra le frequenze e le proprietà metallurgiche.
Inoltre, è stato identificato il potenziale rischio di fallimento strutturale nei mezzi di trasporto in seguito all’esposizione a determinate frequenze. Ciò sottolinea l’importanza di regolamentazioni specifiche per garantire che le infrastrutture di trasporto siano progettate e costruite tenendo conto dei possibili effetti delle frequenze sulle proprietà metallurgiche. Gli enti normativi e le industrie coinvolte nel settore dei trasporti dovranno collaborare per sviluppare linee guida e standard adeguati per la protezione dei viaggiatori.
6. Esplorazione delle letture di energia tramite oggetti metallurgici: come interpretare e utilizzare le informazioni rilevate a vantaggio dei viaggiatori delle frequenze
Questa sezione fornisce una guida approfondita per comprendere le letture di energia attraverso l’uso di oggetti metallurgici e come tradurre tali informazioni per aiutare i viaggiatori delle frequenze a sfruttare al meglio le loro esperienze energetiche. L’energia che circonda tutti gli oggetti metallurgici è un aspetto fondamentale da considerare per coloro che sono impegnati in pratiche di esplorazione delle frequenze.
Per interpretare correttamente le letture di energia dei metalli, è essenziale prendere in considerazione la loro composizione chimica e la sua interazione con le frequenze. Attraverso un accurato studio dei diversi metalli e delle loro proprietà energetiche, i viaggiatori delle frequenze possono ottenere una profonda comprensione dell’ambiente che li circonda, nonché un livello più elevato di consapevolezza e consapevolezza energetica.
Un metodo efficace per utilizzare queste informazioni è stabilire connessioni energetiche con gli oggetti metallici che ci circondano. Questo può essere fatto attraverso la meditazione e la concentrazione focalizzata sui metalli stessi. I metalli, con le loro proprietà uniche, consentono ai viaggiatori delle frequenze di amplificare e potenziare le loro esperienze energetiche, facilitando la connessione con le diverse frequenze e rendendo più facile l’esplorazione delle letture energetiche.
In Conclusione
L’articolo ha fornito un’approfondita analisi sul metallo dei viaggiatori delle frequenze, dedicandosi alla sua magia e alle molteplici esperienze che gli oggetti metallurgici possono offrire. Attraverso un approccio tecnico, abbiamo esplorato le proprietà uniche di questo metallo e le sue connessioni con il mondo delle frequenze vibranti.
Iniziamo con la comprensione di come i viaggiatori delle frequenze manipolino la magia attraverso l’uso di oggetti metallurgici. La loro abilità di sintonizzare le frequenze e amplificarne l’energia ci ha permesso di scoprire il potenziale illimitato che questi oggetti possono offrire. Sia per gli incantesimi difensivi che per quelli offensivi, il metallo dei viaggiatori delle frequenze si rivela essere un compagno fidato per gli incantatori esperti.
Inoltre, abbiamo esaminato le esperienze uniche che gli utenti possono vivere con gli oggetti metallici alchemici. Grazie alla loro specifica composizione, questi oggetti possono connettere il loro possessore a mondi invisibili, consentendo esperienze trascendentali che vanno ben oltre la comprensione umana ordinaria. I viaggiatori delle frequenze diventano così ponti verso dimensioni sconosciute, aprendo porte a nuovi orizzonti di conoscenza e saggezza.
È importante sottolineare che, nonostante la loro capacità di arricchire le esperienze magiche, l’utilizzo di oggetti metallurgici richiede un’attenta formazione e un approccio rispettoso nei confronti delle frequenze e del loro potere. Solo una conoscenza approfondita e una preparazione adeguata possono garantire un uso sicuro ed efficace di questi oggetti, evitando rischi e conseguenze indesiderate.
In conclusione, il metallo dei viaggiatori delle frequenze è un elemento prezioso nella pratica della magia. Grazie alle sue proprietà uniche e alla sua connessione con il mondo delle frequenze vibranti, gli oggetti metallici alchemici offrono nuove possibilità e profonde esperienze per gli incantatori esperti. Tuttavia, è fondamentale approcciare questi oggetti con rispetto e consapevolezza, al fine di utilizzarli in modo sicuro ed evitare effetti indesiderati.
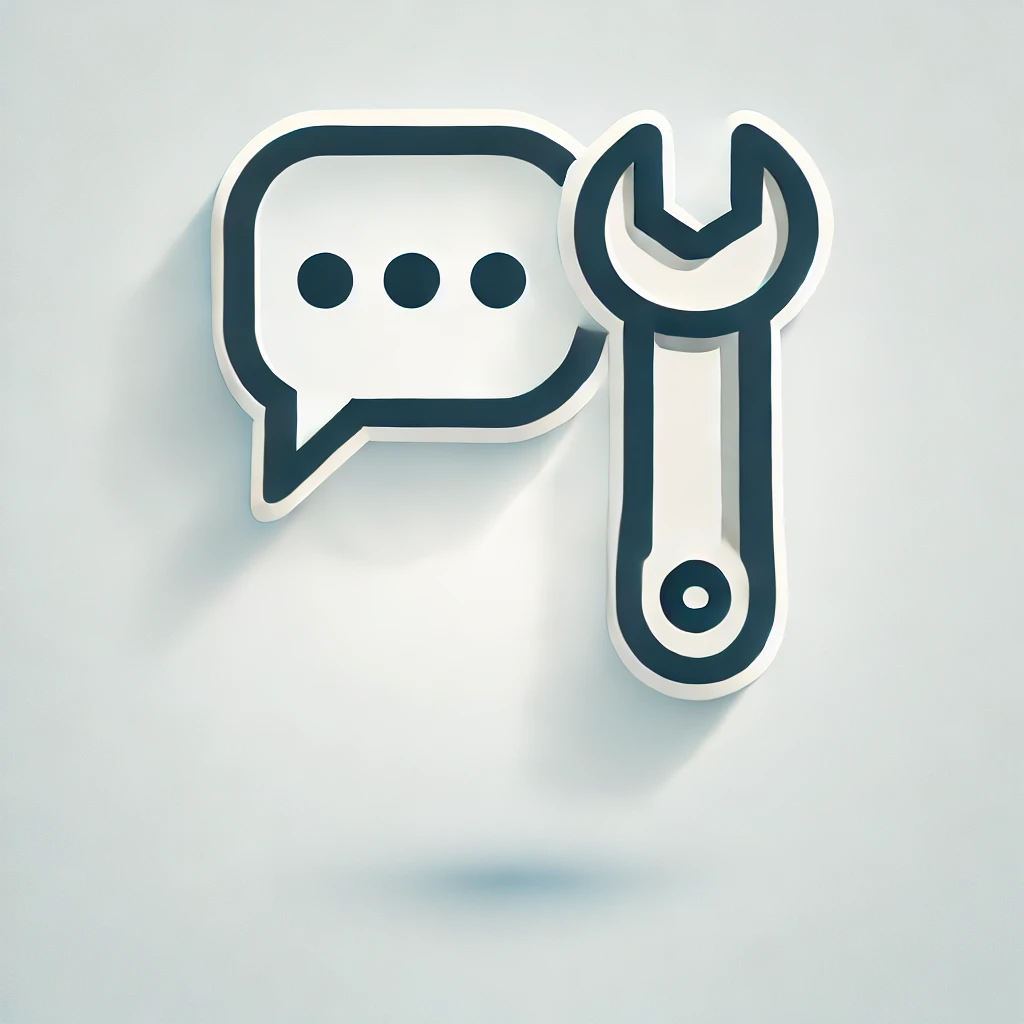
"Hai un'opinione tecnica o una domanda specifica? Non esitare, lascia un commento! La tua esperienza può arricchire la discussione e aiutare altri professionisti a trovare soluzioni. Condividi il tuo punto di vista!"