Tutti i contenuti pubblicati nel presente sito sono gestiti e scritti a livello amatoriale. In nessun caso possono essere considerati riferimento di settore.
Materiali Innovativi che Facilitano la Produzione Rapida nelle Strutture Metalliche: Tecnologie, Proprietà e Vantaggi
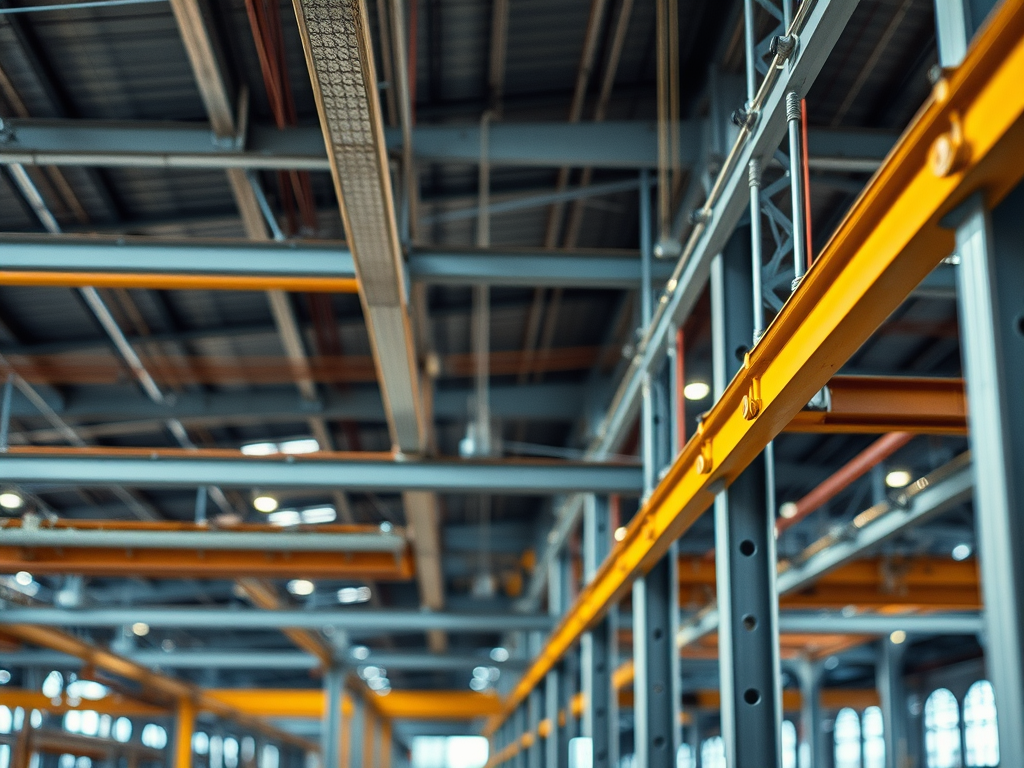
Materiali Innovativi che Facilitano la Produzione Rapida nelle Strutture Metalliche: Tecnologie, Proprietà e Vantaggi
1. Introduzione: L’importanza dei materiali innovativi nelle strutture metalliche
L’evoluzione del settore delle costruzioni metalliche è strettamente legata all’innovazione nei materiali utilizzati. La ricerca di materiali più leggeri, resistenti e facili da lavorare ha portato alla creazione di leghe avanzate che riducono i tempi di produzione e migliorano le prestazioni delle strutture finali. Materiali come gli acciai ad alta resistenza, le leghe di alluminio e i nuovi compositi metallici consentono di realizzare strutture più leggere e resistenti, riducendo al contempo i costi e i tempi di lavorazione. In questo articolo, analizzeremo i principali materiali innovativi che stanno rivoluzionando il settore delle costruzioni metalliche, con un focus sui loro vantaggi produttivi e sulle tecnologie che ne facilitano l’utilizzo.
2. Gli acciai ad alta resistenza e basso legato (HSLA): caratteristiche e benefici
Uno dei materiali più innovativi nel campo delle strutture metalliche è l’acciaio ad alta resistenza e basso legato (HSLA). Questo tipo di acciaio è progettato per offrire una combinazione ottimale di resistenza e duttilità, consentendo la realizzazione di strutture più leggere senza compromettere la sicurezza. Gli acciai HSLA contengono elementi come vanadio, niobio e titanio, che migliorano le proprietà meccaniche senza aumentare significativamente il peso. Grazie alla loro alta resistenza, gli acciai HSLA richiedono meno materiale per realizzare una struttura, riducendo così i tempi di produzione e i costi di fabbricazione.
Tabella 1: Confronto tra acciaio HSLA e acciaio al carbonio standard
Caratteristica | Acciaio HSLA | Acciaio al Carbonio Standard |
---|---|---|
Resistenza alla trazione | 550-700 MPa | 400-500 MPa |
Densità | 7.85 g/cm³ | 7.85 g/cm³ |
Peso per unità di resistenza | Inferiore del 20% | Standard |
Duttilità | Alta | Media |
3. L’uso dell’alluminio nelle strutture metalliche: leggerezza e lavorabilità
L’alluminio è un materiale che sta guadagnando sempre più spazio nelle costruzioni metalliche grazie alla sua leggerezza e facilità di lavorazione. Rispetto all’acciaio, l’alluminio ha una densità molto inferiore (circa un terzo), il che lo rende ideale per applicazioni in cui il peso è un fattore critico, come nel settore dei trasporti e nelle strutture modulari. Inoltre, l’alluminio è altamente resistente alla corrosione, eliminando la necessità di trattamenti superficiali costosi e riducendo i tempi di manutenzione. Grazie a queste proprietà, l’alluminio permette di accelerare la produzione, riducendo i tempi di saldatura e assemblaggio.
4. Leghe di alluminio ad alte prestazioni: una soluzione versatile
Le leghe di alluminio ad alte prestazioni, come la serie 7000 (contenente zinco come elemento principale), sono state sviluppate per combinare la leggerezza dell’alluminio con una resistenza meccanica elevata. Queste leghe offrono un’eccellente lavorabilità e possono essere facilmente estruse, saldate e formate, rendendole ideali per la produzione di componenti complessi in tempi ridotti. Le leghe della serie 7000 sono ampiamente utilizzate nel settore aerospaziale e nelle strutture leggere ad alta resistenza, dove il tempo di produzione e il peso del materiale sono fattori chiave.
Tabella 2: Confronto tra leghe di alluminio della serie 7000 e leghe tradizionali
Caratteristica | Serie 7000 | Leghe di alluminio tradizionali |
---|---|---|
Resistenza alla trazione | 500-600 MPa | 250-300 MPa |
Peso | Molto leggero | Leggero |
Resistenza alla corrosione | Alta | Media |
Applicazioni | Aerospaziale, strutture leggere | Generiche |
5. Compositi metallici avanzati: una rivoluzione nella produzione
I compositi metallici, che combinano metalli con materiali ceramici o polimerici, rappresentano un’altra innovazione nel settore delle strutture metalliche. Questi materiali offrono proprietà superiori rispetto ai metalli puri, come una maggiore resistenza alla corrosione, una maggiore rigidità e una riduzione del peso. I compositi metallici sono particolarmente utili nelle applicazioni in cui sono richieste proprietà termiche ed elettriche specifiche. Inoltre, possono essere stampati in 3D o formati con tecnologie additive, riducendo significativamente i tempi di produzione e i costi associati alla lavorazione tradizionale.
6. L’uso dell’acciaio inox duplex nelle strutture metalliche
L’acciaio inossidabile duplex è una combinazione di austenite e ferrite che offre una resistenza alla corrosione significativamente superiore rispetto agli acciai inossidabili tradizionali. Questo materiale è particolarmente indicato per applicazioni in ambienti aggressivi, come piattaforme offshore, strutture chimiche e impianti di trattamento delle acque. Oltre alla resistenza alla corrosione, l’acciaio duplex offre anche una resistenza meccanica maggiore, riducendo il peso complessivo della struttura e facilitando la produzione rapida grazie alla riduzione dei tempi di saldatura e assemblaggio.
Tabella 3: Proprietà dell’acciaio inox duplex rispetto all’acciaio inox austenitico
Caratteristica | Acciaio Inox Duplex | Acciaio Inox Austenitico |
---|---|---|
Resistenza alla corrosione | Molto alta | Alta |
Resistenza alla trazione | 600-800 MPa | 400-600 MPa |
Costo | Più alto | Standard |
Tempi di saldatura | Ridotti | Standard |
7. Titanio: alta resistenza e leggerezza per applicazioni speciali
Il titanio è un materiale che offre un’incredibile combinazione di leggerezza, resistenza e resistenza alla corrosione. Anche se è più costoso rispetto all’acciaio e all’alluminio, il titanio è utilizzato in applicazioni speciali dove queste proprietà sono cruciali, come nell’industria aerospaziale, nella costruzione di ponti e in strutture esposte a condizioni ambientali estreme. Il titanio richiede tecnologie di lavorazione avanzate, come la saldatura a fascio di elettroni e la forgiatura a caldo, ma la sua alta resistenza meccanica consente di ridurre il peso complessivo della struttura e, di conseguenza, i tempi di produzione.
8. L’alluminio-litio: il futuro delle leghe leggere
Una delle innovazioni più recenti nel campo delle leghe leggere è l’alluminio-litio. Questa lega combina le proprietà dell’alluminio con quelle del litio, rendendola ancora più leggera e resistente. L’alluminio-litio è particolarmente adatto per applicazioni aerospaziali e automobilistiche, dove la riduzione del peso è fondamentale. Rispetto alle leghe di alluminio tradizionali, l’alluminio-litio offre una maggiore resistenza meccanica, migliorando al contempo la lavorabilità. Inoltre, il litio riduce la densità della lega, permettendo di realizzare componenti più leggeri e con una migliore resistenza alla fatica.
9. L’adozione dei materiali ibridi: combinazione di metalli e polimeri
I materiali ibridi, che combinano metalli con polimeri o fibre di vetro, sono una delle soluzioni più avanzate per accelerare la produzione nelle strutture metalliche. Questi materiali offrono una combinazione unica di leggerezza, resistenza meccanica e flessibilità, rendendoli ideali per applicazioni che richiedono strutture leggere ma resistenti. I materiali ibridi vengono utilizzati soprattutto nel settore automobilistico e nelle costruzioni modulari, dove è essenziale ridurre il peso senza compromettere le prestazioni strutturali. La produzione di materiali ibridi può essere automatizzata attraverso tecnologie di stampaggio e laminazione avanzate, riducendo notevolmente i tempi di produzione.
10. L’uso dei rivestimenti metallici avanzati per migliorare la durabilità
Un’altra innovazione importante per la produzione rapida nelle strutture metalliche è rappresentata dai rivestimenti avanzati, che migliorano la durabilità e la resistenza alla corrosione dei materiali metallici. I rivestimenti ceramici e a base di nanotecnologie possono essere applicati su superfici metalliche per proteggerle dall’usura e dalla corrosione, prolungando la durata della struttura e riducendo la necessità di manutenzione. Questi rivestimenti possono essere applicati rapidamente mediante tecnologie di spruzzatura termica o deposizione fisica in fase di vapore (PVD), riducendo i tempi di lavorazione e migliorando le prestazioni del materiale.
Tabella 4: Confronto tra rivestimenti metallici tradizionali e avanzati
Tipo di rivestimento | Tradizionale | Avanzato (nanotecnologico) |
---|---|---|
Resistenza alla corrosione | Media | Molto alta |
Durabilità | 5-10 anni | 15-20 anni |
Tempi di applicazione | Lenti | Veloci |
Costo | Basso | Moderato |
11. Riduzione dei tempi di lavorazione con tecnologie additive
Le tecnologie additive, come la stampa 3D di metalli, stanno rivoluzionando il modo in cui le strutture metalliche vengono progettate e prodotte. Grazie alla capacità di creare forme complesse direttamente da file digitali, la stampa 3D riduce notevolmente i tempi di produzione, eliminando la necessità di stampi e utensili. I materiali utilizzati nella stampa 3D includono leghe di acciaio, alluminio, titanio e compositi metallici, che offrono proprietà meccaniche superiori rispetto ai materiali convenzionali. Le tecnologie additive consentono inoltre di ridurre gli sprechi di materiale, poiché solo il materiale necessario viene utilizzato nel processo di costruzione.
12. L’evoluzione dei materiali autoriparanti nelle strutture metalliche
Un’innovazione emergente nel settore dei materiali metallici è rappresentata dai materiali autoriparanti, che sono in grado di riparare autonomamente le microfratture e i danni superficiali. Questi materiali, spesso realizzati con l’aggiunta di capsule di polimeri autoriparanti o con rivestimenti avanzati, offrono un notevole vantaggio in termini di riduzione della manutenzione e della durata operativa. L’utilizzo di materiali autoriparanti nelle strutture metalliche può migliorare significativamente la durabilità delle infrastrutture, riducendo i costi operativi e accelerando la produzione grazie alla minore necessità di interventi di riparazione.
13. L’ottimizzazione della produzione grazie all’uso di leghe leggere e resistenti
L’uso di leghe leggere e resistenti, come il magnesio e le sue leghe, è un altro passo verso l’accelerazione della produzione nelle strutture metalliche. Il magnesio è uno dei metalli strutturali più leggeri, con una densità significativamente inferiore rispetto all’alluminio e all’acciaio. Le sue leghe, rinforzate con elementi come il litio, l’alluminio e il silicio, offrono un’eccellente resistenza meccanica e un’elevata capacità di assorbire urti. Questi materiali sono ideali per le strutture leggere e modulari, dove la velocità di produzione e l’efficienza sono fondamentali. Le leghe di magnesio possono essere lavorate rapidamente mediante fusione e stampaggio, accelerando ulteriormente i tempi di produzione.
14. L’impiego di nanotecnologie nei materiali metallici
L’integrazione delle nanotecnologie nei materiali metallici sta aprendo nuove opportunità per la produzione rapida e la realizzazione di strutture ad alte prestazioni. I nanomateriali metallici, come le nanoparticelle di rame o le nanofibre di acciaio, possono migliorare significativamente le proprietà meccaniche e termiche dei metalli tradizionali. Questi materiali sono in grado di aumentare la resistenza alla trazione, la durezza e la resistenza alla corrosione, rendendoli ideali per applicazioni industriali e strutturali. Le nanotecnologie permettono inoltre di sviluppare materiali con proprietà autoriparanti, migliorando la durabilità e riducendo i costi di manutenzione.
15. Il ruolo della digitalizzazione nella gestione dei materiali innovativi
La digitalizzazione sta svolgendo un ruolo fondamentale nell’ottimizzazione della produzione rapida di strutture metalliche. I software di gestione avanzata della produzione, come i sistemi MES (Manufacturing Execution System) e ERP (Enterprise Resource Planning), permettono di monitorare in tempo reale il flusso di materiali innovativi lungo la catena produttiva. Questo garantisce una gestione ottimale delle risorse, riducendo i tempi di fermo macchina e ottimizzando i cicli di produzione. Grazie alla digitalizzazione, è possibile tracciare ogni fase del processo produttivo, dal monitoraggio delle scorte di materiali innovativi alla gestione delle fasi di lavorazione e assemblaggio.
16. Materiali a memoria di forma: applicazioni e vantaggi
I materiali a memoria di forma (SMA – Shape Memory Alloys) sono un’altra innovazione significativa che sta migliorando la velocità di produzione nelle strutture metalliche. Questi materiali, principalmente leghe di nichel-titanio (NiTi), hanno la capacità di recuperare la loro forma originale dopo essere stati deformati, rendendoli utili in applicazioni che richiedono componenti autoregolanti o mobili. Gli SMA vengono utilizzati in dispositivi attivi per il controllo delle strutture, come attuatori e ammortizzatori, e consentono di semplificare il design e ridurre i tempi di produzione grazie alla loro versatilità e alla riduzione delle parti mobili.
17. Produzione sostenibile con materiali metallici riciclati
La sostenibilità è diventata una priorità nel settore delle strutture metalliche, e l’uso di materiali metallici riciclati sta diventando una pratica comune per accelerare la produzione e ridurre l’impatto ambientale. L’acciaio, ad esempio, è uno dei materiali più riciclati al mondo, e il suo riutilizzo non solo riduce la domanda di nuove materie prime, ma contribuisce anche a ridurre i costi energetici legati alla produzione. I processi di riciclo avanzati permettono di mantenere la qualità del materiale riciclato, rendendolo adatto per la realizzazione di strutture complesse e durature.
18. Conclusioni: l’importanza dei materiali innovativi nella produzione rapida
I materiali innovativi stanno trasformando il modo in cui le strutture metalliche vengono progettate e prodotte. L’uso di acciai ad alta resistenza, leghe di alluminio, compositi e nanotecnologie consente di ridurre i tempi di produzione e migliorare le prestazioni strutturali. Questi materiali non solo accelerano la fabbricazione, ma offrono anche vantaggi significativi in termini di durabilità, sostenibilità e resistenza alle condizioni ambientali estreme. Le aziende che adottano questi materiali innovativi possono migliorare la loro competitività, riducendo i costi e i tempi di realizzazione dei progetti.
Fonti:
- HSLA Steel Properties and Applications: HSLA Steel Overview
- Aluminum-Lithium Alloys for Aerospace: Aluminum-Lithium Innovation
- Nanomaterials in Metal Structures: Nanotechnology in Metals
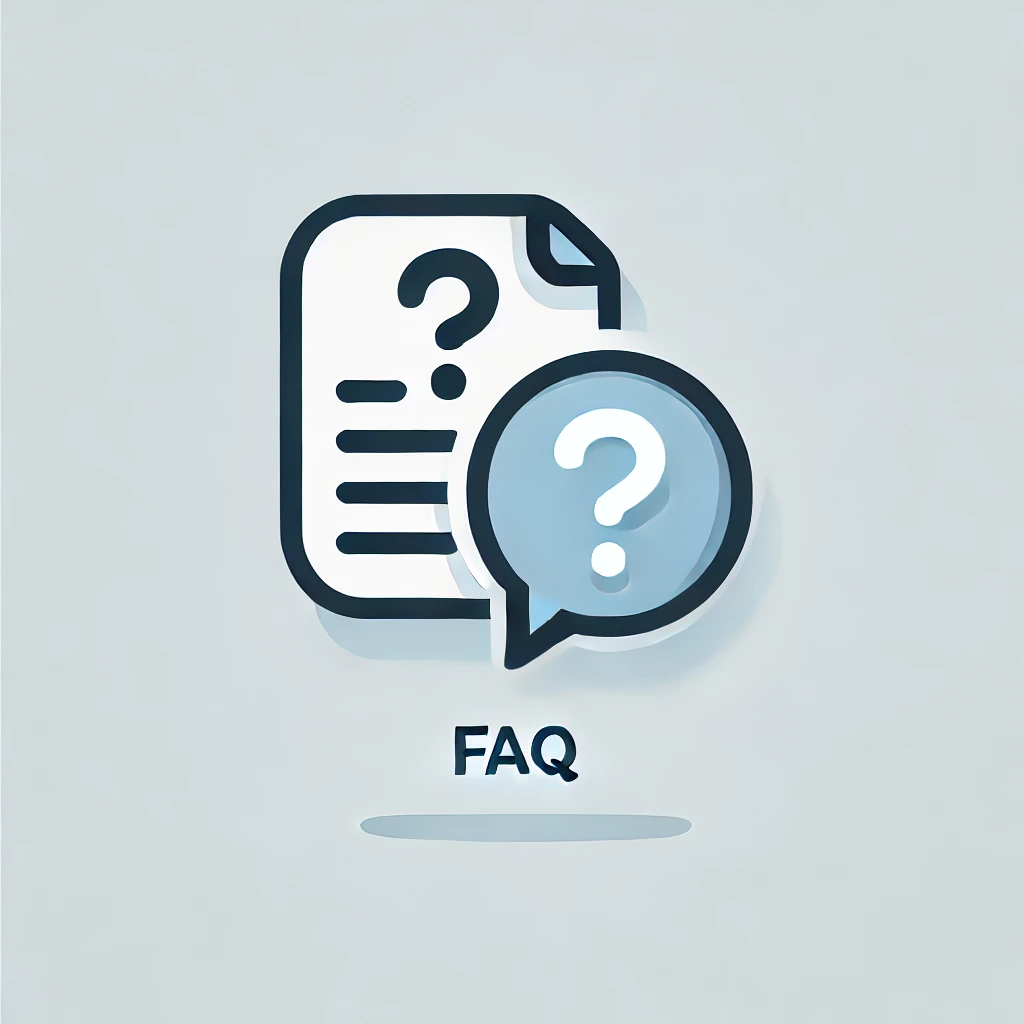
FAQ
Domande frequenti? Scopri tutte le risposte ai quesiti tecnici più comuni! Approfondisci le informazioni essenziali sulle opere metalliche e migliora la tua comprensione con soluzioni pratiche e chiare. Non lasciarti sfuggire dettagli importanti!
La Nimonic è una superlega a base di nichel e cromo sviluppata per resistere alle alte temperature e alle sollecitazioni termiche più estreme. Grazie alla sua combinazione unica di resistenza meccanica e stabilità termica, la Nimonic è utilizzata principalmente nei motori a reazione e in altre applicazioni che richiedono prestazioni elevate a temperature elevate. Questa lega si distingue per la sua eccellente capacità di mantenere la resistenza anche in condizioni di stress termico ripetuto, rendendola una scelta essenziale per numerosi settori industriali.
Proprietà della Nimonic
Le superleghe Nimonic offrono una serie di proprietà uniche che le rendono ideali per applicazioni critiche, soprattutto in ambienti che richiedono resistenza alle alte temperature e alle sollecitazioni meccaniche elevate:
- Resistenza alle alte temperature: Le leghe Nimonic sono progettate per mantenere la loro resistenza meccanica anche a temperature superiori ai 700°C, rendendole ideali per i motori a reazione e altre applicazioni ad alta temperatura.
- Resistenza alla fatica termica: Grazie alla loro composizione chimica, le leghe Nimonic resistono alle sollecitazioni cicliche dovute ai continui cambiamenti di temperatura. Questa proprietà le rende fondamentali per componenti che subiscono costanti riscaldamenti e raffreddamenti.
- Stabilità strutturale: Le leghe Nimonic mantengono la loro struttura cristallina anche sotto carichi elevati e a temperature elevate, prevenendo deformazioni e garantendo la durata dei componenti.
- Resistenza all’ossidazione e alla corrosione: La presenza di cromo nella lega garantisce una buona resistenza all’ossidazione, riducendo la formazione di strati di ossido che potrebbero compromettere le prestazioni dei componenti.
Applicazioni della Nimonic
Le leghe Nimonic sono utilizzate in settori industriali avanzati, dove la resistenza a condizioni estreme è un requisito essenziale. Di seguito alcune delle principali applicazioni:
2.1 Settore aerospaziale
Nel settore aerospaziale, la Nimonic è una delle leghe più utilizzate per la costruzione di componenti dei motori a reazione, come le palette delle turbine, le camere di combustione e i dischi delle turbine. Questi componenti devono operare a temperature estremamente elevate, e la Nimonic, grazie alla sua elevata resistenza alla fatica termica, garantisce prestazioni affidabili e sicure anche dopo migliaia di cicli operativi.
2.2 Produzione di energia
Nel settore della produzione di energia, le leghe Nimonic vengono impiegate nella costruzione di turbine a gas per centrali elettriche. Le turbine a gas devono funzionare a temperature elevate per massimizzare l’efficienza del ciclo termodinamico, e la Nimonic offre la resistenza necessaria per garantire una lunga durata dei componenti e un’elevata efficienza operativa.
2.3 Industria automobilistica
Le leghe Nimonic sono utilizzate anche nel settore automobilistico, in particolare per la realizzazione di valvole dei motori ad alte prestazioni. I motori ad alte prestazioni, come quelli utilizzati nelle auto da corsa, richiedono materiali in grado di resistere a temperature elevate e a sollecitazioni meccaniche intense, e la Nimonic è una delle scelte principali per garantire queste caratteristiche.
Tecniche di lavorazione della Nimonic
La lavorazione delle leghe Nimonic richiede competenze specifiche e l’uso di tecnologie avanzate a causa della loro durezza e resistenza. Ecco alcune delle principali tecniche utilizzate:
- Lavorazione meccanica: La fresatura, la tornitura e la foratura delle leghe Nimonic richiedono utensili in carburo di tungsteno e macchine con elevata potenza, poiché queste leghe tendono a indurirsi durante la lavorazione e sono difficili da tagliare.
- Saldatura: La saldatura delle leghe Nimonic è complessa e richiede il controllo preciso della temperatura per evitare cricche e garantire la resistenza meccanica delle giunzioni. Le tecniche di saldatura più utilizzate includono il TIG (Tungsten Inert Gas) e il laser.
Innovazioni nelle leghe Nimonic
Negli ultimi anni, la ricerca e lo sviluppo nel campo delle superleghe hanno portato a miglioramenti significativi nelle prestazioni delle leghe Nimonic. L’integrazione della stampa 3D additiva per la produzione di componenti complessi in Nimonic ha permesso di ridurre il peso dei componenti, aumentare la precisione e migliorare la flessibilità nella progettazione.
Inoltre, sono state sviluppate nuove varianti di Nimonic che offrono una maggiore resistenza alla fatica e una migliore lavorabilità, rendendo queste leghe ancora più adatte per le applicazioni critiche nei settori aerospaziale e della produzione di energia.
Conclusioni
La Nimonic è una delle superleghe più importanti per le applicazioni che richiedono elevata resistenza alle alte temperature e affidabilità meccanica. Grazie alle sue proprietà di resistenza alla fatica termica e all’ossidazione, la Nimonic è ampiamente utilizzata nei motori a reazione, nelle turbine a gas e nei motori ad alte prestazioni. La capacità di mantenere la stabilità strutturale e la resistenza meccanica anche in condizioni di temperatura estreme rende la Nimonic una scelta indispensabile per molte applicazioni industriali avanzate.
Le innovazioni tecnologiche, come l’uso della stampa 3D e lo sviluppo di nuove varianti della lega, continueranno a migliorare le prestazioni della Nimonic, contribuendo a garantirne il ruolo fondamentale nelle sfide ingegneristiche del futuro.
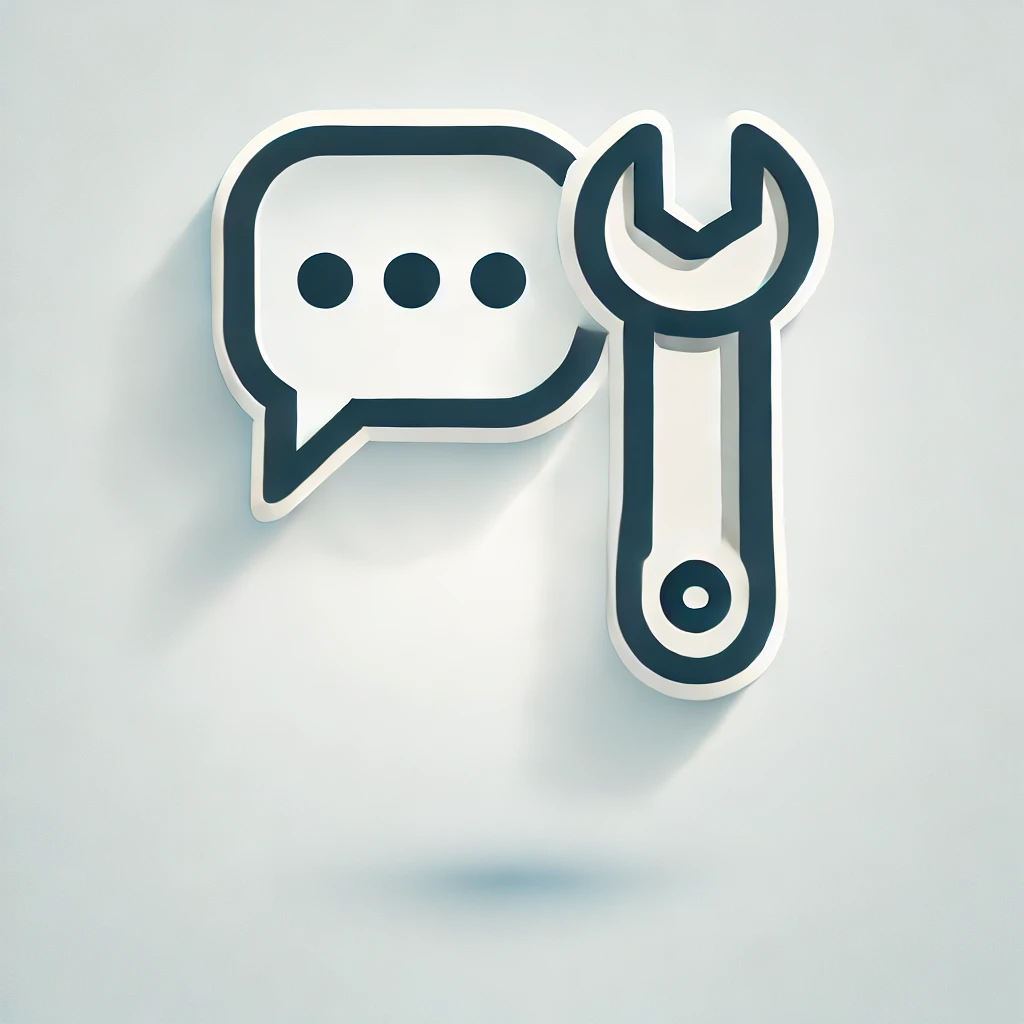
"Hai un'opinione tecnica o una domanda specifica? Non esitare, lascia un commento! La tua esperienza può arricchire la discussione e aiutare altri professionisti a trovare soluzioni. Condividi il tuo punto di vista!"