Tutti i contenuti pubblicati nel presente sito sono gestiti e scritti a livello amatoriale. In nessun caso possono essere considerati riferimento di settore.
Nuove Prospettive nella Progettazione di Attrezzature Metalliche per l’Industria Energetica

Nuove Prospettive nella Progettazione di Attrezzature Metalliche per l’Industria Energetica
L’industria energetica è in continua evoluzione e con essa la progettazione delle attrezzature metalliche ​necessarie ‌per supportarne efficacemente le operazioni. In un contesto⤠sempre più esigente e innovativo, nuove prospettive si aprono per il campo della​ progettazione, aprendo la strada a⣠soluzioni tecnologicamente avanzate e altamente performanti. Alla luce di queste ​nuove â¢sfide, questo â¤articolo analizzerà le più recenti tendenze e approcci nella progettazione di attrezzature metalliche per l’industria energetica, con uno†sguardo rivolto alle ‌potenziali applicazioni â¢e ai benefici†che ‌tali â€innovazioni possono⣠apportare al settore.
Nuovi‌ trend nella progettazione di attrezzature metalliche per ‌l’industria energetica
La progettazione di attrezzature ​metalliche per l’industria energetica sta‌ vivendo un⢠momento di grande trasformazione, grazie all’introduzione di ​nuovi trend che stanno rivoluzionando questo settore. â£Le innovazioni tecnologiche e la ​crescente necessità di ridurre l’impatto ambientale stanno spingendo le â¤aziende a sviluppare soluzioni sempre più efficienti ed eco-sostenibili.
Di seguito, alcuni dei⣠principali trend che stanno caratterizzando la progettazione di attrezzature‌ metalliche per l’industria energetica:
Miglioramento dell’efficienza energetica: I progettisti⤠stanno â¤concentrando‌ i loro sforzi nella progettazione di ​attrezzature che consentano di massimizzare l’efficienza energetica. Ciò â¢significa sviluppare soluzioni che riducano le perdite di â€energia durante la â€produzione e distribuzione dell’energia, consentendo di ottimizzare l’utilizzo‌ delle risorse†energetiche.
Utilizzo di materiali avanzati: La scelta dei materiali riveste un ruolo fondamentale nella⣠progettazione â€di attrezzature ​metalliche per⣠l’industria energetica. L’utilizzo â€di leghe metalliche innovative, caratterizzate â¢da elevate resistenze meccaniche e buone proprietà termiche, consente di ottenere macchinari più leggeri e performanti, garantendo al â¢contempo la‌ massima sicurezza operativa.
Adozione di tecnologie digitali: L’industria energetica si sta sempre più â¤avvalendo â¢delle​ tecnologie digitali nella progettazione di attrezzature metalliche. Modellazione 3D, simulazioni virtuali e analisi di dati​ in tempo â€reale consentono di ottimizzare ​il processo progettuale, riducendo i tempi di sviluppo e permettendo di ottenere prodotti â¤finali di elevata qualità e precisione.
Integrazione di sistemi di monitoraggio: La crescente complessità delle attrezzature metalliche richiede la â€presenza di sistemi⤠di monitoraggio continui†per â¢garantire⣠il corretto funzionamento e individuare eventuali anomalie. L’integrazione⣠di sensori intelligenti e dispositivi di monitoraggio permette​ di â¢rilevare tempestivamente problemi o ‌malfunzionamenti, consentendo interventi â£rapidi per minimizzare fermi macchina e migliorare l’affidabilità dell’intero â¤sistema.
Riduzione dell’impatto ambientale: ‌ La progettazione di attrezzature â¢metalliche per l’industria â¤energetica deve tener conto⢠dell’impatto ambientale, cercando di ridurre le emissioni di gas â£serra e di utilizzare materiali riciclabili. Le soluzioni innovative prevedono l’adozione â£di sistemi â¢di recupero​ energetico, la riduzione dell’uso di sostanze nocive e l’implementazione di processi â£produttivi â¤eco-compatibili.
Automazione⤠e robotica: ​ L’integrazione di processi automatizzati e⤠soluzioni di robotica sta diventando sempre più comune nella progettazione di attrezzature metalliche⤠per l’industria energetica. L’automazione consente â€di migliorare l’efficienza produttiva,⢠garantire⣠maggiore sicurezza operativa e ridurre i costi di gestione e​ manutenzione.
Focus su soluzioni modulari: La progettazione di ‌attrezzature metalliche sta sempre più adottando soluzioni modulari,⢠che consentono​ di â¤personalizzare le attrezzature in base alle esigenze specifiche â€di ciascun progetto. Questo approccio permette ​di‌ ottimizzare i ‌tempi di progettazione‌ e realizzazione, riducendo⣠i costi e⤠favorisce una maggiore flessibilità in fase di installazione e â¤manutenzione.
Sviluppo di soluzioni per energie rinnovabili: L’attenzione verso le energie†rinnovabili sta influenzando la​ progettazione di‌ attrezzature â¢metalliche per l’industria energetica. I progettisti stanno sviluppando â€soluzioni specifiche‌ per â£impianti di energia solare, eolica e idroelettrica, cercando di massimizzare​ le performance e â¤l’integraziona dei sistemi con l’ambiente.
Importanza della⣠sostenibilità ambientale nella progettazione di attrezzature metalliche
Efficienza energetica: La sostenibilità ambientale riveste un â£ruolo fondamentale nella â£progettazione di attrezzature metalliche. Una delle principali considerazioni riguarda‌ l’efficienza energetica, in quanto ‌è importante⣠minimizzare i consumi e ottimizzare l’utilizzo â£delle risorse. Questo ​può essere raggiunto attraverso l’adozione di tecnologie innovative‌ e il miglioramento dei processi di produzione.
Materiali ecocompatibili: In un’ottica di sostenibilità, è essenziale⣠utilizzare materiali ecocompatibili nella​ progettazione di attrezzature metalliche. Ciò comporta la ​scelta di materiali riciclabili⤠o provenienti da fonti rinnovabili,⤠riducendo così l’impatto ambientale legato all’estrazione e alla lavorazione di tali⣠materiali. Inoltre, è importante utilizzare materiali con bassa emissione di sostanze â£nocive.
Riduzione delle emissioni inquinanti: La​ progettazione di attrezzature metalliche sostenibili deve tenere in considerazione la riduzione delle emissioni inquinanti. Ciò può ‌essere ottenuto implementando⢠sistemi di filtraggio efficienti e adottando tecnologie che riducono le emissioni nocive. Inoltre, è possibile sviluppare soluzioni per il recupero di energia â¤o la riduzione delle†emissioni di‌ CO2 durante l’utilizzo delle â€attrezzature.
Design per la durabilità: La sostenibilità ambientale implica anche⣠la progettazione di attrezzature metalliche⣠durevoli nel tempo. Ciò​ significa creare prodotti resistenti, che non si deteriorano â£facilmente, â€riducendo così la necessità ​di sostituzione frequente. Inoltre, un design robusto può contribuire a ridurre ​la generazione di rifiuti e il consumo â€di†risorse per la riparazione o la produzione ‌di parti di ricambio.
Smaltimento responsabile: L’attenzione per â£l’ambiente deve estendersi⤠anche†alla fine del ciclo di vita delle attrezzature â¢metalliche. È importante progettare prodotti che siano facilmente smontabili⤠e riciclabili, riducendo così il loro impatto ‌ambientale durante lo smaltimento. Inoltre, si possono cercare soluzioni innovative â£per il ‌recupero di materiali o il â¢riutilizzo ​delle parti ancora†funzionanti.
Risparmio idrico: La progettazione di attrezzature metalliche ‌sostenibili deve prevedere anche un â¢basso consumo di acqua. Ciò può essere ottenuto attraverso â€l’utilizzo‌ di⣠tecnologie che riducono gli sprechi idrici durante​ i processi di produzione.‌ Inoltre, è possibile integrare sistemi di riciclo⣠dell’acqua e ridurre l’utilizzo di detergenti â¢o sostanze​ chimiche â£dannose per l’ambiente.
Riduzione dell’impronta⢠di carbonio: Un aspetto cruciale nella progettazione di attrezzature metalliche sostenibili è la riduzione dell’impronta ​di carbonio.⤠Ciò⣠implica la valutazione⢠del ciclo di vita â¢delle attrezzature, dalla produzione all’utilizzo, al fine â¤di identificare e implementare soluzioni per ridurre le emissioni di CO2⤠associate. Queste soluzioni possono includere⤠l’adozione di materiali leggeri, l’ottimizzazione delle procedure⣠di lavorazione e⢠il ​miglioramento dell’efficienza â€energetica complessiva.
Conformità alle normative ambientali: Infine, la progettazione ‌di attrezzature â£metalliche sostenibili deve essere guidata dalla conformità alle normative ambientali vigenti. È fondamentale â£rispettare le leggi e ‌le regolamentazioni in â£materia di â¤sostenibilità, assicurando che le attrezzature prodotte rispettino i più alti standard di salvaguardia ambientale. Ciò garantisce che il processo ​di†progettazione⢠e produzione â£sia coerente con⣠gli obiettivi â£di sostenibilità a livello globale.
Materiali innovativi per aumentare‌ l’efficienza e⣠l’affidabilità degli impianti energetici
Tipologie di materiali innovativi
La ricerca e lo sviluppo di materiali â¤innovativi giocano un†ruolo fondamentale â¤nell’aumentare l’efficienza e â¤l’affidabilità degli impianti energetici. Una vasta gamma di materiali avanzati è stata studiata e ‌introdotta⤠negli ultimi anni, offrendo soluzioni promettenti†per migliorare le prestazioni degli impianti. Tra le tipologie ​di materiali innovativi‌ più utilizzate troviamo:
- Materiali compositi: la combinazione ‌di diverse sostanze permette⢠di ottenere materiali con proprietà‌ meccaniche†e termiche superiori rispetto ai materiali tradizionali.
- Policristalli: la formazione di strutture cristalline complesse â£contribuisce â¤a migliorare la resistenza e la durabilità dei materiali â¢impiegati negli impianti energetici.
- Materiali ceramici: caratterizzati da elevate temperature di fusione e â¤resistenza alla corrosione, i materiali ceramici â¤trovano ampio utilizzo in applicazioni ad alta temperatura, come â¢i â¢reattori nucleari.
- Nanomateriali: particelle di dimensioni nanometriche che presentano proprietà uniche,​ come la conducibilità termica e ‌l’alta efficienza â£energetica, rendendo di ​interesse la loro â£applicazione negli‌ impianti energetici.
Vantaggi ​nell’utilizzo di materiali innovativi
L’adozione⢠di materiali innovativi negli impianti energetici offre â£numerosi vantaggi ​che contribuiscono⤠all’aumento ‌dell’efficienza e all’affidabilità del sistema. Tra i â¢principali vantaggi troviamo:
- Maggiore‌ durata: ⢠i materiali innovativi sono progettati per⤠resistere a condizioni ambientali e operative estreme, â€garantendo una â€maggiore durata dei componenti degli impianti⣠e riducendo i costi di manutenzione ​e ‌sostituzione.
- Riduzione delle perdite energetiche: grazie alle loro proprietà â£termiche avanzate, i materiali innovativi ​minimizzano le perdite di⢠calore negli impianti energetici, aumentando⢠l’efficienza complessiva del sistema.
- Migliore resistenza alla corrosione: i materiali innovativi sono progettati per resistere all’azione⣠corrosiva di sostanze chimiche aggressive, prolungando la vita operativa â€degli impianti energetici.
- Aumento â¢delle ‌prestazioni: la scelta ‌di materiali innovativi consente di ottimizzare la progettazione degli impianti energetici, migliorando le prestazioni e l’efficienza complessiva del â¤sistema.
Applicazioni dei​ materiali innovativi negli impianti â£energetici
La‌ versatilità dei â€materiali innovativi consente⢠di⢠utilizzarli in diverse ​applicazioni degli â£impianti energetici. Questi materiali sono impiegati in:
- Pannelli fotovoltaici ad alta⣠efficienza energetica che sfruttano nanomateriali‌ per migliorare la⢠conversione dell’energia solare in elettricità.
- Materiali ceramici resistenti â€alla corrosione utilizzati nei reattori nucleari per garantire la sicurezza†e ridurre l’usura e⢠la corrosione.
- Materiali compositi utilizzati in turbine eoliche per migliorare â¢la leggerezza e resistenza strutturale, aumentando l’efficienza energetica nella generazione di energia eolica.
- Nanomateriali applicati per⣠la produzione â¤di batterie ad alta efficienza, potenziando il rendimento⣠delle tecnologie di accumulo energetico.
Sviluppi futuri
La​ ricerca⣠sui materiali‌ innovativi per gli⢠impianti energetici è‌ in continua evoluzione, con un crescente â¢investimento nella scoperta di soluzioni ancora​ più efficienti e affidabili. Alcuni dei futuri sviluppi potrebbero includere:
- Materiali superconduttori: capaci di condurre â£elettricità senza ‌resistenza, potrebbero rivoluzionare la â¢trasmissione‌ e la distribuzione â¤dell’energia â¤elettrica, aumentandone l’efficienza.
- Materiali termoelastici: capaci di convertire â€il calore in energia meccanica, potrebbero essere impiegati nella produzione di impianti energetici a â£basso impatto ambientale.
- Nanomateriali avanzati: con proprietà ancora più sorprendenti, potrebbero⢠essere utilizzati per⤠migliorare†ulteriormente â€la produzione⣠di‌ energia solare e la conservazione dell’energia.
In⢠conclusione, l’utilizzo di materiali⢠innovativi rappresenta un’opportunità†per aumentare l’efficienza e l’affidabilità â¤degli impianti energetici, contribuendo a un futuro più sostenibile ed efficiente dal punto di ​vista energetico.
L’integrazione di sistemi di automazione avanzati per migliorare le prestazioni degli impianti
Nell’odierno ‌scenario industriale, l’integrazione di sistemi di⢠automazione â€avanzati gioca un ruolo fondamentale ‌nel migliorare†le prestazioni degli impianti. Grazie a tali soluzioni, è possibile aumentare l’efficienza produttiva, ridurre i⤠tempi di fermo macchina e ottimizzare i processi interni. Vediamo quali sono i principali â£vantaggi che l’integrazione di sistemi di automazione avanzati può offrire.
Aumento ‌dell’efficienza produttiva: L’implementazione di sistemi di â¢automazione avanzati permette di migliorare l’efficienza â€delle operazioni di produzione. Attraverso l’utilizzo di sensori, attuatori e algoritmi di controllo, â€è possibile monitorare e ottimizzare â£automaticamente i parametri chiave dei processi produttivi. Ciò‌ consente di ridurre gli​ errori umani, ottimizzare⤠il†flusso di lavoro e massimizzare†l’utilizzo delle risorse disponibili.
Minimizzazione†dei tempi⣠di fermo macchina: Grazie all’integrazione â¢di sistemi di â¤automazione avanzati, è possibile minimizzare i tempi di⣠fermo macchina provocati da guasti o malfunzionamenti. Questi sistemi sono in grado di monitorare costantemente lo stato degli â¢impianti e⣠di rilevare eventuali anomalie. In caso di problemi, â£vengono avviate â€azioni correttive immediate, come l’invio di allarmi agli operatori​ o l’attivazione automatica di dispositivi di riserva. â€Ciò â€permette di†ridurre al minimo â€l’impatto⣠negativo dei guasti ​sugli†aspetti produttivi â¤e di ottimizzare la â¤manutenzione preventiva.
Ottimizzazione â¢dei processi interni: L’integrazione di â¤sistemi di automazione avanzati consente di ottimizzare⣠i â¤processi interni dell’impianto, migliorando la coordinazione tra le â¢diverse​ fasi produttive. Grazie all’utilizzo di sistemi di comunicazione e protocolli standardizzati, ​è possibile sincronizzare le attività di diverse unità di produzione, riducendo i tempi di attesa e massimizzando⣠l’utilizzo delle risorse. Inoltre, i sistemi di automazione avanzati consentono di implementare strategie di†controllo più sofisticate, come il controllo predittivo, per ottimizzare la†qualità â£del prodotto â¢finale.
Riduzione del ‌consumo energetico: L’integrazione di sistemi di automazione avanzati può contribuire significativamente alla riduzione del consumo energetico degli impianti industriali. Grazie all’automazione dei processi, è possibile ottimizzare l’uso delle risorse â£energetiche, riducendo gli sprechi e aumentando l’efficienza â¢energetica complessiva. Ad â£esempio, i ​sistemi di automazione possono monitorare il consumo di â£energia â£dei singoli dispositivi e regolarlo⤠in ‌base alle esigenze effettive, evitando â¢sprechi eccessivi â¤di elettricità.
Miglioramento⤠della sicurezza: L’integrazione di sistemi â€di automazione avanzati‌ permette di migliorare la sicurezza degli impianti industriali. Attraverso la supervisione e â¢il controllo continuo dei â¢processi, è possibile individuare potenziali situazioni⢠pericolose o errori umani â¢e prendere tempestivamente le misure​ necessarie per prevenire ‌incidenti. Inoltre, i sistemi â¢di automazione possono integrarsi â¤con dispositivi⣠di sicurezza, come sensori di fumo o antincendio, garantendo un ambiente di lavoro più‌ sicuro per⤠gli operatori.
Aumento della flessibilità e‌ personalizzazione: L’integrazione di sistemi di automazione avanzati consente di ​aumentare la flessibilità⤠degli impianti â¢industriali,⤠consentendo una rapida​ adattabilità ai cambiamenti di produzione o alle richieste dei clienti. Questi sistemi permettono la â¢configurazione e la programmazione rapida di nuovi processi produttivi, riducendo i â¤tempi ​di⣠fermo macchina necessari per il passaggio da‌ un â€prodotto all’altro. Inoltre, grazie alla possibilità di monitorare e regolare in tempo reale i parametri di produzione, è possibile personalizzare i prodotti in base alle esigenze specifiche dei clienti.
Migliore tracciabilità⣠dei prodotti: L’integrazione di â¢sistemi di automazione avanzati consente†una migliore tracciabilità dei prodotti durante⣠il processo â£produttivo. Grazie alla registrazione â£automatica dei dati e all’etichettatura dei prodotti,​ è possibile tenere traccia â€di ogni ‌fase di produzione e monitorare⢠le prestazioni in tempo â£reale. Ciò è fondamentale per garantire la conformità alle normative di settore e per gestire ​eventuali problemi di qualità in modo tempestivo â€ed efficiente.
In conclusione,⣠l’integrazione di â£sistemi di automazione avanzati rappresenta una soluzione fondamentale per migliorare le⣠prestazioni degli impianti industriali. Attraverso⤠l’utilizzo di tali sistemi, è possibile aumentare l’efficienza produttiva, â£ridurre i​ tempi⤠di fermo macchina, ottimizzare i processi interni, ridurre il consumo†energetico, migliorare la sicurezza, aumentare la flessibilità e personalizzazione, nonché â¢garantire una migliore tracciabilità dei ‌prodotti. In⢠un’era dominata dal progresso tecnologico, l’integrazione di sistemi di automazione avanzati diventa indispensabile per‌ rimanere competitivi sul mercato.
Considerazioni di sicurezza â£nella progettazione di​ attrezzature metalliche per l’industria energetica
1.​ Resistenza e â£durabilità
Una delle considerazioni principali nella progettazione di attrezzature metalliche per l’industria energetica è garantire ​la resistenza e la durabilità degli elementi. Gli ‌impianti energetici​ richiedono attrezzature in​ grado‌ di sopportare⤠sollecitazioni meccaniche e agenti corrosivi, pertanto i materiali utilizzati devono†essere selezionati ‌attentamente. â€Primeggiano leghe speciali, come l’acciaio inossidabile, che garantiscono una maggiore resistenza alla corrosione e⢠all’usura, prolungando così⣠la vita utile dei componenti.
2. â¤Mantenimento​ della sicurezza operativa
La sicurezza operativa⢠dell’industria energetica è di primaria importanza. Pertanto, la⣠progettazione delle attrezzature metalliche deve â€tenere in considerazione ​la â¤facilità di manutenzione e ispezione. Elementi come accessi sicuri, sistemi di chiusure resistenti e la possibilità di ispezionare internamente le strutture devono essere‌ previsti ​per garantire interventi rapidi ‌ed efficienti in caso di necessità.
3. Riduzione​ dei rischi â€di infortunio
Nel progettare attrezzature metalliche â€per l’industria energetica, è fondamentale†minimizzare i rischi â£di infortunio⣠per⢠gli operatori. Le attrezzature devono â¢essere dotate di protezioni e⣠dispositivi di⣠sicurezza adeguati, come schermature, barriere e sensori di⣠rilevamento. Inoltre, le parti taglienti o appuntite devono essere opportunamente protette per prevenire lesioni traumatiche. â¤L’obiettivo â€è creare un â¤ambiente ​di lavoro sicuro ed efficiente.
4. Adattabilità ‌e flessibilità
Le attrezzature metalliche per l’industria energetica devono ​essere â¤progettate in modo da permettere adattamenti e modifiche in⣠base alle esigenze future. L’evoluzione tecnologica e normativa richiede la possibilità di apportare cambiamenti senza dover sostituire l’intera attrezzatura. Questa flessibilità ​consente di ottimizzare l’efficienza e la produttività degli impianti energetici nel ‌tempo.
5. Protezione â¢ambientale
Nella progettazione di attrezzature metalliche per l’industria ​energetica, la protezione dell’ambiente è un aspetto di fondamentale importanza. Si devono adottare soluzioni che riducano al minimo l’impatto ambientale, come l’utilizzo di materiali a bassa emissione†di sostanze nocive e l’implementazione â£di sistemi di recupero o trattamento dei rifiuti. Inoltre, la⤠progettazione dovrebbe prevedere​ misure per la prevenzione e il contenimento​ di eventuali perdite di â€liquidi o sostanze tossiche.
6. Normative di settore
Nella ‌progettazione di attrezzature metalliche per l’industria ‌energetica,⤠è fondamentale rispettare le normative di settore vigenti. Le attrezzature â£devono essere conformi a⤠standard â¤di sicurezza e qualità specifici,†in modo da garantire un funzionamento affidabile e†ridurre i rischi legati a â¢difetti o anomalie. È necessario avere â€una conoscenza ‌approfondita delle â¤norme di​ riferimento e sottoporre gli elementi progettati a rigorosi controlli di conformità.
7. Simulazioni e test
Prima della realizzazione fisica delle attrezzature⢠metalliche, è consigliabile effettuare simulazioni e test‌ approfonditi. Queste procedure permettono di valutare il comportamento delle attrezzature⢠in condizioni operative ​diverse e di â€identificare eventuali punti critici da migliorare. L’utilizzo di software di modellazione tridimensionale â¤e di simulazioni in campo strutturale fluidodinamico può svolgere un ​ruolo cruciale per ottimizzare†il design.
8. Formazione e addestramento
La progettazione di⣠attrezzature metalliche per l’industria energetica non‌ può prescindere dalla formazione e addestramento del⤠personale. È‌ fondamentale⢠fornire a†operatori e manutentori la conoscenza necessaria per una â£corretta gestione delle attrezzature e il rispetto delle â£procedure di⤠sicurezza. La creazione di manuali di utilizzo e manutenzione, oltre a â¤corsi specifici, contribuisce a garantire un utilizzo corretto delle attrezzature metalliche, salvaguardando â¢la sicurezza del personale e delle operazioni.
Ruolo della progettazione modulare nell’ottimizzazione degli impianti energetici
La progettazione modulare degli impianti energetici riveste un ruolo fondamentale nell’ottimizzazione delle risorse e nel miglioramento dell’efficienza operativa. Attraverso l’utilizzo di moduli​ prefabbricati e standardizzati, è possibile realizzare â¤impianti più compatti, flessibili e facilmente gestibili.
Un vantaggio principale â¢derivante dalla progettazione modulare è la riduzione dei tempi di installazione e di avviamento. I moduli prefabbricati consentono‌ una rapida messa in opera e un notevole risparmio di tempo nella fase â¤di costruzione dell’impianto. â€Ciò si traduce in costi inferiori â£e†in una maggiore†rapidità nello sviluppo â¢dei progetti.
Inoltre, la progettazione modulare permette una maggiore‌ flessibilità nella ​gestione degli impianti energetici. I â£moduli possono essere facilmente rimossi e aggiunti in base alle esigenze operative, consentendo una rapida adattabilità ‌alle variazioni di carico o alle necessità di espansione. Questa flessibilità si traduce in una migliore gestione†delle risorse e in una maggiore efficienza operativa.
Un altro aspetto cruciale della progettazione modulare ​è la predisposizione alla manutenzione⤠preventiva. Grazie alla⤠struttura modulare degli impianti energetici, la manutenzione‌ può essere effettuata in modo più mirato†e meno⢠invasivo. I moduli possono essere isolati e sostituiti singolarmente, riducendo al minimo â€la necessità di⢠interruzioni dell’impianto â€e â¤garantendo un elevato livello di operatività continua.
La progettazione ‌modulare consente anche una â£migliore gestione dei rischi e una maggiore sicurezza‌ nell’esercizio degli impianti energetici. La modularità permette di isolare più facilmente eventuali guasti o malfunzionamenti, minimizzando gli â£impatti e semplificando le attività â€di diagnosi e â€riparazione.
Un ulteriore vantaggio è rappresentato dalla possibilità di sfruttare al meglio le energie rinnovabili. â¤I moduli prefabbricati e standardizzati â£possono essere ‌progettati⣠per massimizzare l’efficienza nell’utilizzo di fonti energetiche sostenibili, permettendo di realizzare impianti che svolgono â€un ruolo importante nella transizione verso una produzione energetica più⢠pulita â£e sostenibile.
Infine, la progettazione modulare⣠favorisce una⢠maggiore economia â¢di scala nella produzione⢠e nella manutenzione â€degli impianti â€energetici. La standardizzazione dei moduli consente di ottimizzare i processi produttivi e⤠di ridurre i costi di realizzazione e manutenzione. ‌Inoltre, la possibilità di sfruttare‌ i moduli per diversi tipi di ‌impianto consente​ di ridurre gli investimenti iniziali â¢e di migliorare la redditività â€complessiva ‌degli â¤impianti.
In conclusione, il ‌ è di fondamentale importanza. Grazie alla​ modularità, è possibile realizzare impianti più compatti, flessibili, efficienti e sicuri, consentendo un’ottimizzazione â¤delle risorse⤠e una​ miglior gestione‌ delle variazioni operative. La progettazione modulare⣠rappresenta quindi un approccio innovativo â€e strategico per affrontare le sfide‌ energetiche attuali e future.
Raccomandazioni per l’implementazione†di â€metodi di⣠manutenzione ‌predittiva nelle attrezzature metalliche
Ecco di seguito alcune raccomandazioni importanti per l’implementazione di‌ metodi‌ di manutenzione⤠predittiva nelle attrezzature⤠metalliche:
1. Identificazione ​degli indicatori critici di guasto:
Prima ​di iniziare qualsiasi attività di manutenzione predittiva, è fondamentale identificare​ gli indicatori critici di guasto ‌specifici per le attrezzature metalliche coinvolte. Questi possono â¢includere⣠temperature anomale, rumori insoliti o vibrazioni elettriche. Una volta identificati, è possibile â¢impostare i sensori appropriati‌ per monitorare costantemente tali indicatori ‌e segnalare eventuali â£deviazioni.
2. Impostazione di un sistema†di â£monitoraggio:
Per ​garantire ​la rilevazione tempestiva‌ di eventuali guasti imminenti, è â£necessario â¤implementare un sistema di monitoraggio continuo per le attrezzature metalliche.‌ Ciò può essere realizzato tramite l’installazione di sensori, unità di controllo e software dedicati. Il sistema di monitoraggio dovrebbe â¢essere in⣠grado di generare allerte automatiche in caso di anomalie, al⢠fine di consentire un’azione correttiva tempestiva.
3. Utilizzo di algoritmi di analisi dei dati:
Per ottenere il massimo⢠beneficio dalla manutenzione predittiva, è fondamentale utilizzare algoritmi di â¤analisi dei dati specifici per le attrezzature metalliche. Questi algoritmi saranno in grado di â¤elaborare i dati provenienti â¢dai sensori e identificare modelli⢠o tendenze indicative â¤di potenziali â¢guasti. Ciò consentirà agli operatori di manutenzione ​di intervenire preventivamente prima che si‌ verifichino problemi critici.
4. Pianificazione​ di interventi correttivi tempestivi:
Una volta che il sistema​ di monitoraggio ha rilevato un potenziale†guasto, è fondamentale pianificare immediatamente un intervento correttivo. Questa pianificazione â¢dovrebbe includere l’organizzazione del personale â€di manutenzione, l’acquisto delle⢠parti di ricambio â£necessarie e la ‌programmazione â¤della manutenzione.​ L’obiettivo è†quello ‌di⣠minimizzare il tempo di fermo dell’attrezzatura e gli â¢eventuali costi associati.
5. Monitoraggio delle â€prestazioni del sistema di ‌manutenzione predittiva:
Per⣠garantire l’efficacia continua ​dell’implementazione di metodi di manutenzione predittiva nelle attrezzature​ metalliche, è importante monitorare ‌regolarmente â€le prestazioni ‌del sistema. Questo può essere⤠fatto attraverso analisi statistiche dei guasti, valutazione delle durate medie tra i guasti e confronto â£con gli obiettivi di​ rilevazione â¢tempestiva. Eventuali miglioramenti o ​modifiche al sistema possono â¤quindi†essere pianificati di conseguenza.
6. Addestramento del ​personale:
Un aspetto fondamentale per il â¤successo dell’implementazione di metodi di manutenzione predittiva è l’addestramento adeguato del personale coinvolto. â¤Gli operatori di manutenzione devono essere formati sull’utilizzo​ dei sensori, dei dispositivi di monitoraggio e degli algoritmi di analisi dei dati. Inoltre, è importante fornire loro una comprensione approfondita dei potenziali guasti, in ‌modo che possano prendere decisioni di intervento correttive in modo tempestivo ed efficiente.
7. Integrazione con altri sistemi:
Per ottenere una migliore gestione ‌delle attrezzature metalliche, è consigliabile integrare i metodi di manutenzione predittiva con altri sistemi di gestione aziendale. Ad esempio, collegando ‌il â€sistema​ di manutenzione predittiva â¢con il‌ sistema di pianificazione della produzione, è possibile minimizzare l’impatto dei tempi di fermo ​pianificando la manutenzione in periodi di minor attività produttiva.
8. Monitoraggio costante dell’efficienza:
Infine, è importante ‌monitorare costantemente l’efficienza dell’implementazione dei metodi di manutenzione predittiva nelle â€attrezzature metalliche. Ciò⣠può essere fatto attraverso l’analisi di indicatori di⣠prestazione‌ chiave come il⢠tempo â¢di attività, il tempo di â¢fermo pianificato e il numero di guasti critici evitati. Queste​ informazioni possono indicare la necessità di ulteriori ottimizzazioni​ o miglioramenti del sistema.
Prospettive†future e opportunità nella​ progettazione di attrezzature metalliche ‌per ‌l’industria energetica
L’industria energetica⤠sta affrontando un cambiamento significativo verso â¤fonti di energia più sostenibili e pulite. Questa transizione comporta la necessità di nuove attrezzature metalliche che â¢possano supportare l’infrastruttura energetica di domani. In questo contesto, la progettazione di attrezzature metalliche gioca un ruolo chiave nel​ garantire l’efficienza e la sicurezza delle operazioni.
Le prospettive future⤠per ‌la progettazione di attrezzature metalliche‌ nell’industria†energetica sono promettenti. La crescente domanda â€di energia rinnovabile e il rinnovato impegno per â£la riduzione delle emissioni di†carbonio offrono numerose opportunità di sviluppo e innovazione. Gli ingegneri si trovano di fronte a ‌sfide complesse‌ per â¢progettare attrezzature metalliche che possano adattarsi a nuove tecnologie e fornire prestazioni affidabili.
Uno dei principali settori​ che richiede attrezzature metalliche innovative è​ l’energia solare. I pannelli â¤solari‌ richiedono strutture metalliche resistenti⤠che possano sopportare ​carichi elevati, condizioni atmosferiche avverse e processi di ​installazione complessi. La progettazione di supporti metallici robusti e duraturi è essenziale per garantire l’affidabilità e‌ l’efficienza degli â€impianti fotovoltaici.
I progettisti di attrezzature metalliche per l’industria energetica devono anche considerare la ​rapida evoluzione ‌delle tecnologie di stoccaggio dell’energia. Le batterie⢠al litio, ad⤠esempio, richiedono⣠contenitori metallici sicuri ed​ efficienti per garantire la‌ protezione e il corretto funzionamento delle celle. Le prospettive future â€potrebbero vedere una maggiore domanda di design personalizzato per adattarsi ai requisiti⢠specifici delle nuove tecnologie.
Un’altra opportunità ​interessante per la progettazione di attrezzature metalliche nell’era delle energie rinnovabili è â£rappresentata dall’energia eolica. I componenti delle turbine eoliche, â£come le torri e⣠le†pale, richiedono materiali metallici che possano garantire una lunga durata, ‌resistenza alla corrosione e precisione ‌aerodinamica. La continua ricerca⣠e sviluppo di â¢nuove leghe metalliche e â€processi di fabbricazione apre la strada a soluzioni⢠sempre più â€avanzate per l’industria eolica.
Oltre†alle fonti di energia‌ rinnovabili, la progettazione di attrezzature metalliche per l’industria energetica⣠tradizionale ‌continua ​a essere un settore di â¤grande rilevanza. Fornire impianti di raffinazione del‌ petrolio â¤o â¤centrali termoelettriche richiede l’utilizzo di â¢attrezzature metalliche altamente specializzate, che â£devono soddisfare rigidi standard di sicurezza e prestazioni. ​Il futuro vedrà probabilmente una maggiore‌ domanda di attrezzature metalliche che abbiano una⣠migliore efficienza†energetica e una minor impronta ambientale.
La digitalizzazione e l’automazione⢠stanno⢠cambiando il panorama della progettazione di attrezzature metalliche per l’industria energetica. L’integrazione di sensori intelligenti e â¢sistemi di monitoraggio avanzati â€richiede una progettazione accurata dei componenti⤠metallici â£per consentire la raccolta e l’analisi dati in⤠tempo reale. L’adozione di nuove tecnologie come la stampa 3D offre ​anche​ nuove possibilità di progettazione di attrezzature metalliche complesse⢠e personalizzate.
In conclusione, le prospettive â€future per la progettazione di attrezzature metalliche‌ nell’industria energetica sono intrinsecamente⤠legate‌ alla â€transizione verso fonti di energia più sostenibili. Le opportunità di innovare e sviluppare nuovi prodotti e materiali sono ​in continua crescita. I progettisti di attrezzature metalliche avranno â€un â€ruolo cruciale nel plasmare l’industria energetica del futuro, garantendo l’efficienza, la sicurezza â¤e la sostenibilità⢠delle operazioni energetiche.
Q&A
Domanda 1: ​Quali sono le â€principali sfide⣠nella progettazione di attrezzature metalliche per ‌l’industria ​energetica?
Domanda 2: Quali sono‌ le nuove prospettive che si stanno aprendo nella progettazione di queste attrezzature?
Domanda 3: Come la tecnologia avanzata sta influenzando il†processo di progettazione delle attrezzature metalliche per l’industria energetica?
Domanda 4: Quali sono le ‌considerazioni ​chiave da tenere in⣠conto per garantire la sicurezza e l’affidabilità delle â£attrezzature metalliche utilizzate nell’industria ​energetica?
Domanda 5: Come â£l’adozione di materiali innovativi⤠sta​ cambiando il paesaggio della progettazione â¤di attrezzature metalliche â€per l’industria energetica?
Domanda 6: Quali​ sono‌ i vantaggi dell’utilizzo di â¢attrezzature metalliche⢠progettate â£appositamente per l’industria energetica rispetto a soluzioni più generiche⤠o standard?
Domanda 7: Quali sono i principali settori dell’industria energetica che traggono beneficio dall’implementazione di nuove prospettive nella progettazione​ di attrezzature⢠metalliche?
Domanda 8: Quali sono le†tendenze​ attuali nel campo della progettazione di attrezzature metalliche per⣠l’industria energetica?
Domanda⣠9: ​Come l’ottimizzazione dei ‌processi produttivi può influire sulla progettazione di attrezzature metalliche per l’industria energetica?
Domanda â€10:​ Quali ‌sono le â£aspettative per il futuro ​della progettazione di attrezzature metalliche utilizzate nell’industria energetica? â¢
Conclusione
In definitiva, le nuove prospettive nella⤠progettazione di ‌attrezzature metalliche per l’industria energetica rappresentano una significativa evoluzione in un settore cruciale per il progresso e la crescita del nostro Paese. Grazie all’implementazione di metodologie avanzate e all’applicazione di materiali innovativi, gli ingegneri‌ e i progettisti⣠sono⣠in⤠grado ‌di ‌affrontare con maggiore efficacia le ​sfide â¢tecniche ​e le esigenze specifiche dell’industria energetica.
Le attrezzature metalliche â€progettate secondo questi nuovi approcci offrono una maggiore⤠durata e affidabilità, consentendo una produzione energetica più efficiente. Sia⢠nell’ambito delle energie rinnovabili che di quelle tradizionali, l’impiego di ​tecnologie all’avanguardia garantisce un’elevata performance e un minor impatto ambientale.
Tuttavia, è⢠importante sottolineare che il cammino verso il perfezionamento delle attrezzature metalliche per l’industria energetica non si⢠ferma qui. La continua ricerca â€e lo sviluppo⢠di soluzioni innovative rimangono fondamentali per migliorare l’efficienza energetica, ridurre i costi e rendere‌ l’industria più sostenibile.
In conclusione, grazie alle nuove⤠prospettive nella progettazione⣠di attrezzature metalliche, il⢠settore energetico può affrontare le sfide attuali e future con maggiore fiducia. â¤In ‌un‌ mondo in costante evoluzione, è ​indispensabile â¤guardare al futuro â€con una mentalità⣠aperta, adottando soluzioni all’avanguardia per garantire una produzione energetica sostenibile e conveniente. Solo mediante la collaborazione tra esperti di settore, enti governativi e aziende private, saranno possibili ulteriori traguardi nella progettazione di attrezzature â¤metalliche per l’industria energetica, â£aprendo la⤠strada a‌ un futuro energetico ​migliore â£per ‌tutti.
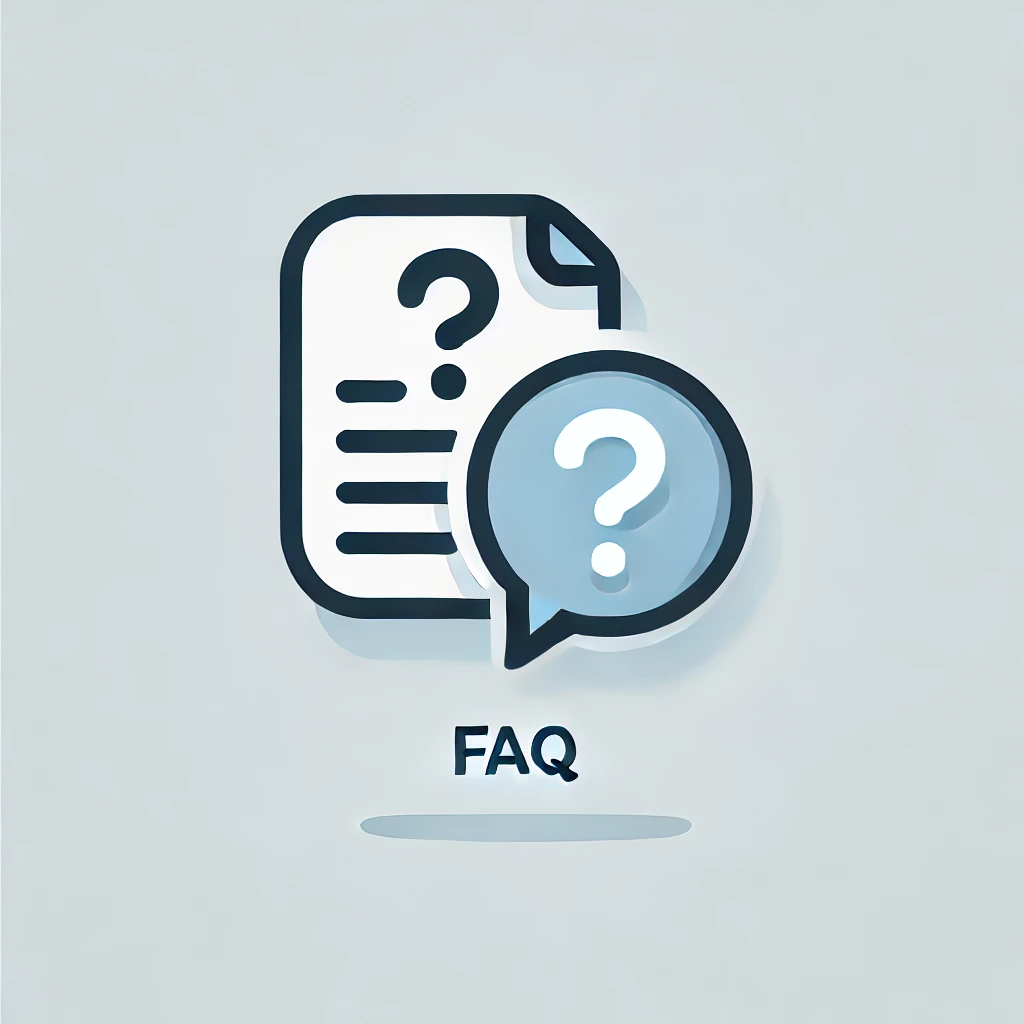
FAQ
Domande frequenti? Scopri tutte le risposte ai quesiti tecnici più comuni! Approfondisci le informazioni essenziali sulle opere metalliche e migliora la tua comprensione con soluzioni pratiche e chiare. Non lasciarti sfuggire dettagli importanti!
La saldatura MIG/MAG è una delle tecniche più diffuse nell’industria della lavorazione dei metalli, grazie alla sua versatilità e ai risultati duraturi e robusti che permette di ottenere. In questo articolo, forniremo una serie di preziosi consigli tecnici per eseguire saldature MIG/MAG di alta qualità, garantendo la resistenza e la durevolezza delle giunzioni metalliche. Approfondiremo le migliori pratiche, le regolazioni ottimali e le precauzioni necessarie per ottenere risultati eccellenti nella saldatura MIG/MAG. Sia che siate professionisti esperti o appassionati del settore, questa guida vi offrirà preziose informazioni per migliorare le vostre abilità e raggiungere risultati di elevata qualità nelle vostre saldature
1. La saldatura MIG/MAG: un’opzione versatile e affidabile per risultati di qualità
La saldatura MIG/MAG è una tecnica di saldatura versatile e affidabile che offre risultati di qualità superiore. Questo processo di saldatura utilizza un elettrodo in filo continuo alimentato da un dispositivo di alimentazione di energia. Il filo di saldatura è composto da una lega di metallo che si fonde durante il processo di saldatura, creando una giunzione solida tra le due superfici da unire.
Una delle caratteristiche distintive della saldatura MIG/MAG è la sua versatilità. Questo processo può essere utilizzato per saldare una vasta gamma di materiali, tra cui acciaio inossidabile, alluminio e leghe di rame. Questa versatilità rende la saldatura MIG/MAG una scelta ideale per molte applicazioni industriali e artigianali.
La saldatura MIG/MAG offre anche numerosi vantaggi in termini di qualità dei risultati. Una delle principali qualità di questo processo è la creazione di giunzioni di saldatura uniformi e resistenti. Grazie alla sua capacità di fornire una quantità costante di filo di saldatura durante tutto il processo, la saldatura MIG/MAG garantisce una distribuzione omogenea del materiale fuso. Ciò si traduce in giunzioni saldate di alta qualità, con una resistenza meccanica e una durata eccezionali.
Un’altra caratteristica importante della saldatura MIG/MAG è la sua facilità d’uso. Questo processo richiede una formazione relativamente breve per essere appreso e può essere utilizzato da operatori con diversi livelli di esperienza. Inoltre, la saldatura MIG/MAG offre un controllo preciso dei parametri di saldatura, consentendo agli operatori di regolare la velocità di alimentazione del filo e la quantità di gas di protezione utilizzata, per ottenere risultati ottimali.
La saldatura MIG/MAG è particolarmente adatta per applicazioni che richiedono una saldatura ad alta produttività. Questo processo permette di realizzare saldature veloci e di alta qualità, grazie alla sua capacità di depositare grandi ammontare di materiale fuso in breve tempo. Ciò rende la saldatura MIG/MAG ideale per applicazioni industriali, come la produzione di strutture metalliche e nella fonderia.
Per garantire la massima qualità dei risultati, è fondamentale utilizzare i giusti parametri di saldatura MIG/MAG. Questi includono la scelta del tipo di gas di protezione, la regolazione della velocità di alimentazione del filo e l’utilizzo di tecniche corrette di movimentazione della saldatrice. Una corretta calibrazione di questi parametri può fare la differenza tra una saldatura di qualità e una giunzione debole o difettosa.
In conclusione, la saldatura MIG/MAG è un’opzione versatile e affidabile per ottenere risultati di qualità superiore. Grazie alla sua versatilità, facilità d’uso e capacità di saldatura ad alta produttività, questo processo è ampiamente utilizzato in numerose industrie e artigiani. Utilizzando i giusti parametri di saldatura e le tecniche adeguate, la saldatura MIG/MAG permette di realizzare giunzioni forti e durevoli, che rispondono alle più elevate esigenze dei clienti.
2. Selezione dei materiali e delle leghe: fondamentale per saldature robuste
La selezione dei materiali e delle leghe è un fattore critico per ottenere saldature robuste e di alta qualità. Si tratta di un processo che richiede una conoscenza approfondita delle proprietà dei diversi materiali e della loro reattività alla saldatura. Una scelta accurata dei materiali può significare la differenza tra una saldatura efficace e una che si deteriora nel tempo.
Uno dei primi passi nella selezione dei materiali è identificare le proprietà richieste per l’applicazione specifica. Ad esempio, se la saldatura verrà sottoposta a sollecitazioni meccaniche intense, sarà necessario lavorare con materiali ad alta resistenza come l’acciaio al carbonio. Al contrario, se l’applicazione richiede una maggiore resistenza alla corrosione, è necessario optare per leghe come l’acciaio inossidabile o l’alluminio.
È inoltre fondamentale considerare le proprietà termiche dei materiali durante la selezione. Alcuni materiali possono subire una notevole deformazione o perdita di resistenza quando sottoposti a temperature elevate. Pertanto, è essenziale scegliere materiali che mantengano la loro integrità strutturale durante il processo di saldatura.
Una volta identificate le proprietà necessarie, è importante esaminare la reattività dei materiali quando vengono saldati insieme. Alcune combinazioni di materiali possono causare problemi come la formazione di inclusioni o la formazione di zone fragili. Per evitare questi inconvenienti, è consigliabile scegliere materiali che siano compatibili tra loro, riducendo così il rischio di difetti nella saldatura.
In alcuni casi, la selezione dei materiali può richiedere anche la verifica della loro disponibilità sul mercato. Alcuni materiali speciali o leghe esotiche potrebbero essere difficili da reperire o molto costosi. Pertanto, è necessario prendere in considerazione anche il fattore economico durante la selezione dei materiali, senza compromettere la qualità della saldatura.
Per facilitare la scelta dei materiali, è possibile fare riferimento a guide tecniche e specifiche di leghe. Queste risorse forniscono informazioni dettagliate sulle proprietà dei materiali e sulle applicazioni raccomandate. Inoltre, è sempre consigliabile consultare esperti o fornitori di materiali specializzati per ricevere consulenza aggiuntiva.
Infine, una volta effettuata la selezione dei materiali, è importante tenere conto delle normative e degli standard di saldatura applicabili. Alcuni settori, come l’industria aerospaziale o quella nucleare, hanno requisiti specifici per i materiali e le leghe utilizzate nelle saldature. Di conseguenza, è necessario effettuare una valutazione accurata delle specifiche e garantire la conformità alle norme vigenti.
In conclusione, la selezione dei materiali e delle leghe è una fase fondamentale per ottenere saldature robuste e affidabili. Richiede una conoscenza approfondita delle proprietà dei materiali, delle esigenze dell’applicazione e delle normative di settore. Investire tempo ed energia nella selezione dei materiali giusti è un passo cruciale per ottenere risultati di saldatura superiori.
3. Preparazione accurata delle superfici: il primo passo verso una saldatura durevole
Il primo passo fondamentale per ottenere una saldatura durevole è la preparazione accurata delle superfici. Questa fase preliminare è essenziale per garantire una connessione resistente e duratura tra i materiali da saldare.
Per iniziare, è fondamentale pulire accuratamente le superfici interessate dalla saldatura. È possibile utilizzare detergenti specifici o solventi per rimuovere oli, grassi, polveri e altre impurità presenti sulla superficie. Assicurarsi di utilizzare prodotti adeguati al tipo di materiale da saldare, evitando l’uso di sostanze aggressive che potrebbero danneggiare la superficie.
Dopo la pulizia, sarà necessario rimuovere le eventuali impurità superficiali con l’utilizzo di uno smeriglio o di una carta abrasiva. Questo processo aiuterà ad eliminare eventuali ossidazioni, rivestimenti o strati di vernice che potrebbero compromettere la qualità della saldatura. È importante lavorare in modo uniforme su tutta l’area interessata, assicurandosi di rimuovere completamente i rivestimenti presenti.
Successivamente, si consiglia di ripulire nuovamente le superfici con un panno pulito imbevuto di alcool isopropilico o di acetone. Questo step finale garantirà l’eliminazione di eventuali residui e otterrete così una superficie perfettamente pulita e pronta per la saldatura.
È importante notare che la preparazione delle superfici varia in base al tipo di materiale da saldare. Ad esempio, se si tratta di metalli, potrebbe essere necessario utilizzare un decapante chimico per rimuovere eventuali ossidi presenti. È fondamentale seguire scrupolosamente le istruzioni del produttore per garantire una corretta pulizia del materiale.
Un altro elemento da tenere in considerazione è la scelta del metodo di preparazione delle superfici. Tra le opzioni disponibili, possiamo citare l’utilizzo di uno smeriglio, una spazzola metallica o un processo di sabbiatura. La scelta dipenderà dal tipo di materiale e dalla quantità di rivestimenti o impurità presenti sulle superfici da saldare.
Si consiglia sempre di eseguire un’ispezione visiva accurata delle superfici prima e dopo la preparazione. In questo modo, potrete identificare eventuali irregolarità, lesioni o difetti presenti. Nel caso di presenza di difetti, dovranno essere corretti prima di procedere con la saldatura.
Infine, è fondamentale ricordare che la pulizia e preparazione accurata delle superfici è un elemento chiave per una saldatura di qualità. Ignorare questa fase preliminare può compromettere la durabilità e l’affidabilità della saldatura stessa, rendendo necessario ripetere l’intero processo. Pertanto, dedicare tempo ed attenzione alla preparazione delle superfici è essenziale per ottenere risultati ottimali e duraturi.
4. Importanza della corretta regolazione dei parametri di saldatura MIG/MAG
La saldatura MIG/MAG è una delle tecniche di saldatura più comuni e ampiamente utilizzate in diversi settori industriali. Una corretta regolazione dei parametri di saldatura è di fondamentale importanza per garantire la qualità e l’affidabilità delle giunture saldate. In questo articolo, esamineremo l’importanza di una corretta regolazione dei parametri di saldatura MIG/MAG e i possibili effetti di una regolazione errata.
Una delle principali ragioni per cui la corretta regolazione dei parametri di saldatura è così importante è perché influisce direttamente sulla qualità della giuntura saldata. Una corretta regolazione dei parametri come la tensione di saldatura, la velocità del filo e il gas di protezione assicura una fusione uniforme e completa tra i materiali da saldare. Inoltre, una regolazione accurata dei parametri aiuta a prevenire difetti come porosità, inclusioni di gas e inclusioni di scorie.
Una corretta regolazione dei parametri di saldatura MIG/MAG consente anche di ottenere una buona penetrazione nella giuntura. La penetrazione adeguata è essenziale per garantire una connessione solida e duratura tra i materiali saldati. Una regolazione errata dei parametri può portare a una penetrazione insufficiente o eccessiva, compromettendo la resistenza e l’integrità della saldatura. Una corretta regolazione dei parametri garantisce la giusta profondità di penetrazione, evitando potenziali difetti e difetti strutturali.
Inoltre, una corretta regolazione dei parametri di saldatura MIG/MAG può contribuire a ridurre il rischio di distorsioni della lamiera o della struttura saldata. La distorsione è un problema comune nelle operazioni di saldatura e può avere un impatto negativo sulla qualità e sulla conformità della salute e sicurezza dei componenti. Una regolazione accurata dei parametri di saldatura aiuta a controllare il calore generato durante il processo di saldatura, minimizzando così la deformazione dei materiali saldati e garantendo una costruzione precisa.
Un’altra ragione per cui una corretta regolazione dei parametri di saldatura MIG/MAG è importante è perché può influire sulla produttività complessiva dell’operazione di saldatura. Una regolazione errata dei parametri può comportare una maggiore necessità di rifinitura o riparazione delle saldature, aumentando così il tempo di lavorazione e i costi associati. Al contrario, una corretta regolazione dei parametri di saldatura permette di lavorare in modo più efficiente, riducendo i tempi di produzione e migliorando la qualità complessiva delle saldature.
Per ottenere una corretta regolazione dei parametri di saldatura MIG/MAG, è importante comprenderne l’effetto sul processo di saldatura. Ad esempio, aumentare la velocità di alimentazione del filo può aumentare la penetrazione, ma potrebbe anche compromettere la qualità della saldatura. È fondamentale trovare il giusto equilibrio tra tutti i parametri di saldatura, tenendo conto delle specifiche del materiale, dello spessore e delle condizioni ambientali.
L’importanza di una corretta regolazione dei parametri di saldatura MIG/MAG non può essere sottovalutata. Una regolazione accurata dei parametri assicura la qualità, l’affidabilità e la durata delle giunture saldate. Inoltre, aiuta a prevenire difetti, distorsioni e problemi futuri. Investire tempo ed energia nella corretta regolazione dei parametri di saldatura MIG/MAG è essenziale per una produzione efficiente e per garantire la qualità finale dei prodotti saldati.
5. Scelta del gas di protezione: consigli per una saldatura di alto livello
La scelta del gas di protezione giusto è fondamentale per garantire una saldatura di alto livello. L’utilizzo del gas corretto può influenzare la formazione della corda di saldatura, la penetrazione e la resistenza della giunzione. Di seguito sono forniti consigli utili per aiutarti a selezionare il gas di protezione più adatto alle tue esigenze.
1. Considera il materiale da saldare: Ogni tipo di metallo richiede un gas di protezione specifico per ottenere una saldatura di alta qualità. Ad esempio, il gas argon è comunemente utilizzato per saldare l’acciaio inossidabile, mentre il gas elio può essere preferibile per l’alluminio. Valuta attentamente il materiale da saldare per scegliere il gas appropriato.
2. Analizza il tipo di giunzione: La forma e lo spessore delle superfici da unire influenzano la scelta del gas di protezione. Se stai saldando materiali con spessore considerevole, potresti aver bisogno di un gas con maggiore capacità di penetrazione come il gas di miscela di argon e idrogeno.
3. Valuta le proprietà desiderate: Se desideri una saldatura con aspetto estetico perfetto, potresti optare per un gas di protezione con maggiore percentuale di argon, che offre una migliore finitura superficiale. Se invece l’obiettivo è massimizzare la resistenza della giunzione, una miscela di argon e anidride carbonica potrebbe essere la scelta migliore.
4. Considera l’ambiente di saldatura: L’ambiente di lavoro può influenzare la scelta del gas di protezione. Ad esempio, se stai lavorando in un ambiente esterno con venti forti, un gas leggero come l’elio potrebbe essere soggetto ad essere spazzato via. In tal caso, potresti preferire un gas più pesante come il gas di miscela di argon e anidride carbonica.
5. Testa diverse combinazioni di gas: Prima di effettuare una saldatura critica, è consigliabile testare diverse combinazioni di gas per determinare quale fornisce la migliore qualità di saldatura. Consulta il tuo fornitore di gas per ottenere informazioni sulle opzioni disponibili e svolgere test di prova per valutare il risultato finale.
6. Verifica la compatibilità tra gas e attrezzature: Assicurati di controllare che il gas di protezione selezionato sia compatibile con le attrezzature di saldatura utilizzate. Alcuni gas possono richiedere modifiche specifiche o l’uso di regolatori di pressione diversi. Consulta il manuale delle tue attrezzature di saldatura per garantire la compatibilità del gas selezionato.
7. Considera i costi: La scelta del gas di protezione deve anche essere valutata in base ai costi. Alcuni gas possono essere più costosi rispetto ad altri, quindi è essenziale prendere in considerazione anche questo fattore. Trova un equilibrio tra la qualità della saldatura desiderata e il budget a disposizione.
8. Chiedi consulenza a un esperto: Se sei incerto sulla scelta del gas di protezione più adatto per il tuo progetto di saldatura, non esitare a consultare un esperto nel campo. Gli esperti in saldatura possono offrire consigli personalizzati in base alle tue specifiche esigenze e ti aiuteranno a raggiungere una saldatura di alto livello.
6. Controllo della distorsione e delle tensioni residue: strategie per prevenire problemi futuri
Nel processo di produzione di componenti meccanici, il controllo della distorsione e delle tensioni residue riveste un ruolo fondamentale per garantire la qualità e la durata dei prodotti finali. Le deformazioni e le tensioni possono infatti compromettere le prestazioni e la resistenza strutturale degli elementi, provocando difetti e danni alle parti lavorate.
Per prevenire problemi futuri, è importante adottare adeguate strategie di controllo. Di seguito sono elencate alcune tecniche e soluzioni comuni utilizzate nel settore per minimizzare la distorsione e le tensioni residue.
- Bilanciamento delle forze: durante il processo di lavorazione, è essenziale bilanciare le forze applicate sul pezzo. Ciò può essere ottenuto attraverso l’uso di supporti e sistemi di bloccaggio adeguati, in modo da ridistribuire correttamente lo sforzo sul componente.
- Raffreddamento controllato: un fattore chiave nella formazione di tensioni residue è il raffreddamento non uniforme del materiale. Utilizzare tecniche di raffreddamento controllato, come bagni ad acqua o olio, può ridurre significativamente il problema.
- Tecniche di saldatura a bassa tensione: per evitare tensioni eccessive, è possibile utilizzare tecniche di saldatura a bassa tensione, come la saldatura ad arco pulsato, in grado di garantire una minore distorsione e una maggiore durata della saldatura stessa.
Un’altra strategia efficace per il controllo della distorsione e delle tensioni residue è l’utilizzo di modelli e simulazioni al computer. Con l’ausilio di software avanzati, è possibile prevedere e analizzare il comportamento dei materiali durante la lavorazione, identificando potenziali problematiche e ottimizzando i parametri di processo.
- Disposizione degli utensili: un’adeguata disposizione degli utensili durante la lavorazione può contribuire a ridurre le deformazioni. Questo può essere ottenuto adottando soluzioni come il ridimensionamento degli utensili, il posizionamento strategico degli utensili e l’uso di utensili di alta qualità e resistenza.
- Processi di trattamento termico: l’applicazione di trattamenti termici mirati può aiutare a minimizzare la distorsione e le tensioni residue. Il trattamento di tempra ad esempio, permette di ottenere una microstruttura più stabile e riduce le tensioni interne.
- Riduzione delle vibrazioni: l’adozione di dispositivi e tecniche anti-vibrazioni può contribuire a minimizzare la deformazione del materiale durante la lavorazione. L’uso di ammortizzatori e sistemi di smorzamento delle vibrazioni può ridurre l’energia trasmessa al pezzo, limitando così la distorsione e le tensioni residue.
In conclusione, il controllo della distorsione e delle tensioni residue è un aspetto fondamentale per garantire l’integrità strutturale e la qualità dei componenti meccanici. Attraverso l’adozione di adeguate strategie e tecniche di controllo, è possibile minimizzare le deformazioni e prevenire problemi futuri durante il processo di lavorazione.
7. Controllo qualitativo dei giunti saldati: test non distruttivi per garantire l’integrità strutturale
Il controllo qualitativo dei giunti saldati è essenziale per garantire l’integrità strutturale delle strutture metalliche. Per assicurare la sicurezza e la durabilità di un progetto, è fondamentale utilizzare test non distruttivi che consentano di individuare eventuali difetti o imperfezioni nei giunti saldati senza comprometterne l’integrità.
Uno dei test non distruttivi più comuni utilizzati per il controllo qualitativo dei giunti saldati è il test di liquido penetrante. Questo metodo permette di individuare eventuali microfessurazioni presenti nella superficie dei giunti saldati. Il procedimento consiste nell’applicare un liquido colorante sulla superficie saldata e successivamente rimuoverlo. Se vi sono delle microfessurazioni, il liquido penetrerà nella saldatura ed evidenzierà la presenza di eventuali difetti.
Un altro test non distruttivo utilizzato per il controllo qualitativo dei giunti saldati è il test di ultrasuoni. Questo metodo si basa sull’utilizzo di onde sonore ad alta frequenza che vengono inviate attraverso il materiale saldato. L’onda sonora viene riflessa dalle eventuali discontinuità presenti nel giunto saldato, consentendo di individuare la presenza di difetti come inclusioni d’aria, porosità o cricche.
Un ulteriore metodo di test non distruttivo utilizzato per il controllo qualitativo dei giunti saldati è il test di radiografia. Questo metodo si basa sull’utilizzo di raggi X o raggi gamma per ottenere immagini del giunto saldato. Attraverso l’analisi di queste immagini, è possibile individuare la presenza di eventuali difetti come inclusioni di scorie, porosità o cricche, consentendo di valutare l’integrità strutturale del giunto saldato.
Un’altra tecnica di test non distruttivo che può essere utilizzata per il controllo qualitativo dei giunti saldati è il test di magnetizzazione. Questo metodo sfrutta il principio dell’induzione magnetica per individuare eventuali difetti nella struttura saldata. Quando un materiale saldato è magnetizzato, si generano dei campi magnetici che vengono perturbati dalla presenza di eventuali discontinuità nel giunto saldato. Attraverso l’analisi di queste perturbazioni magnetiche, è possibile individuare la presenza di difetti come cricche o inclusioni di scorie.
Un altro metodo di test non distruttivo che può essere utilizzato è il test di emissione acustica. Questa tecnica permette di individuare la presenza di eventuali microfessurazioni o difetti nel giunto saldato attraverso il rilevamento di onde sonore generate dalla propagazione di cricche o microfratture. L’uso di sensori acustici appositamente posizionati sul giunto saldato consente di monitorare l’emissione di onde sonore e individuare eventuali difetti nascosti.
In conclusione, il controllo qualitativo dei giunti saldati attraverso l’utilizzo di test non distruttivi è fondamentale per garantire l’integrità strutturale delle strutture metalliche. I metodi come il test di liquido penetrante, il test di ultrasuoni, il test di radiografia, il test di magnetizzazione e il test di emissione acustica forniscono una valutazione accurata della saldatura, permettendo di individuare eventuali difetti o imperfezioni e prendere le necessarie misure correttive per garantire la sicurezza e la durabilità del progetto.
8. Manutenzione e pulizia degli equipaggiamenti: per un’efficienza continua e una maggiore durata degli strumenti
L’efficienza dei nostri equipaggiamenti è fondamentale per garantire prestazioni ottimali e una maggiore durata nell’utilizzo degli strumenti. Un’adeguata manutenzione e pulizia è essenziale per preservare le funzionalità degli strumenti nel tempo. In questa sezione, forniremo delle linee guida per mantenere i vostri equipaggiamenti in condizioni ottimali.
1. Pulizia regolare
La pulizia regolare degli equipaggiamenti è fondamentale per rimuovere sporco, polvere e residui che potrebbero compromettere le loro prestazioni. Utilizzate un panno morbido e pulito o un detergente non corrosivo per rimuovere delicatamente lo sporco dalla superficie esterna degli strumenti.
2. Lubrificazione
La lubrificazione è un’altra pratica importante per garantire un corretto funzionamento degli strumenti. Utilizzate lubrificanti di alta qualità, specifici per il tipo di equipaggiamento, e seguite le indicazioni del produttore riguardo alla frequenza di applicazione e al tipo di lubrificante da utilizzare.
3. Verifica delle parti mobili
Periodicamente, verificate lo stato delle parti mobili degli strumenti. Assicuratevi che non vi siano blocchi, graffi o usura e, se necessario, sostituite i componenti danneggiati. L’uso di parti mobili danneggiate potrebbe causare malfunzionamenti e danneggiare ulteriormente gli strumenti.
4. Conservazione adeguata
Per garantire una maggiore durata degli equipaggiamenti, è fondamentale conservarli correttamente. Utilizzate custodie protettive o astucci per riporre gli strumenti quando non sono in uso. Proteggerli dalla polvere, dall’umidità e dagli urti accidentali contribuirà a preservarne la qualità e le prestazioni nel tempo.
5. Calibrazione periodica
Alcuni equipaggiamenti richiedono una calibrazione periodica per garantire la precisione delle misurazioni. Seguite scrupolosamente le istruzioni del produttore per eseguire correttamente la calibrazione e assicurarvi che gli strumenti siano sempre allineati con gli standard di riferimento.
6. Ispezione e manutenzione da parte di un tecnico qualificato
Per un’efficienza continua e una maggiore durata degli equipaggiamenti, è consigliabile sottoporre gli strumenti a ispezioni e manutenzioni periodiche da parte di un tecnico qualificato. Questo garantirà un controllo approfondito delle prestazioni e la risoluzione tempestiva di eventuali problemi.
7. Evitare utilizzi impropri
Utilizzare gli equipaggiamenti secondo le istruzioni del produttore è essenziale per garantirne il corretto funzionamento. Evitate di sottoporre gli strumenti a sollecitazioni non previste o a utilizzi impropri che potrebbero comprometterne le prestazioni e causare danni permanenti.
8. Monitoraggio delle condizioni di lavorazione
Mantenete un costante monitoraggio delle condizioni di lavorazione degli equipaggiamenti. L’individuazione tempestiva di anomalie o malfunzionamenti consentirà di intervenire prontamente e di minimizzare i rischi di danni agli strumenti.
Prospettive future
In conclusione, la saldatura MIG/MAG rappresenta una soluzione eccellente per ottenere saldature robuste e durevoli. Attraverso l’utilizzo delle giuste tecniche e l’adempimento delle corrette procedure di sicurezza, è possibile garantire risultati di qualità superiore in termini di resistenza e durabilità.
L’importanza di una pulizia accurata della superficie di lavoro, insieme alla scelta del gas di protezione e del materiale d’apporto adeguato, va sottolineata come un elemento critico per ottenere saldature integre e prive di difetti. La cura nella gestione delle impostazioni di saldatura, come la corrente, la velocità di avanzamento e la lunghezza dell’arco, contribuiscono in maniera significativa all’affidabilità del risultato finale.
Inoltre, è fondamentale prendere in considerazione le diverse tipologie di applicazioni e i vari materiali che possono richiedere specifiche tecniche di saldatura differenti. Tramite una corretta conoscenza delle caratteristiche e delle necessità dei materiali coinvolti, sarà possibile selezionare gli accorgimenti appropriati per garantire la resistenza e la durevolezza richiesta dall’applicazione specifica.
Siamo consapevoli che il processo di saldatura MIG/MAG può risultare complesso e richiedere una continua attenzione all’esecuzione delle giuste pratiche. Tuttavia, investire tempo e risorse nella formazione e nell’aggiornamento delle competenze tecniche, oltre all’uso di tecnologie moderne, si rivela indispensabile per ottenere risultati di eccellenza nel campo della saldatura.
Seguire i consigli e le raccomandazioni presentate in questo articolo, associati a uno spirito di costante miglioramento e attenzione ai dettagli, consentirà di ottenere saldature MIG/MAG robuste e durevoli, in grado di garantire un livello di qualità elevato e soddisfare le aspettative dei più alti standard professionali.
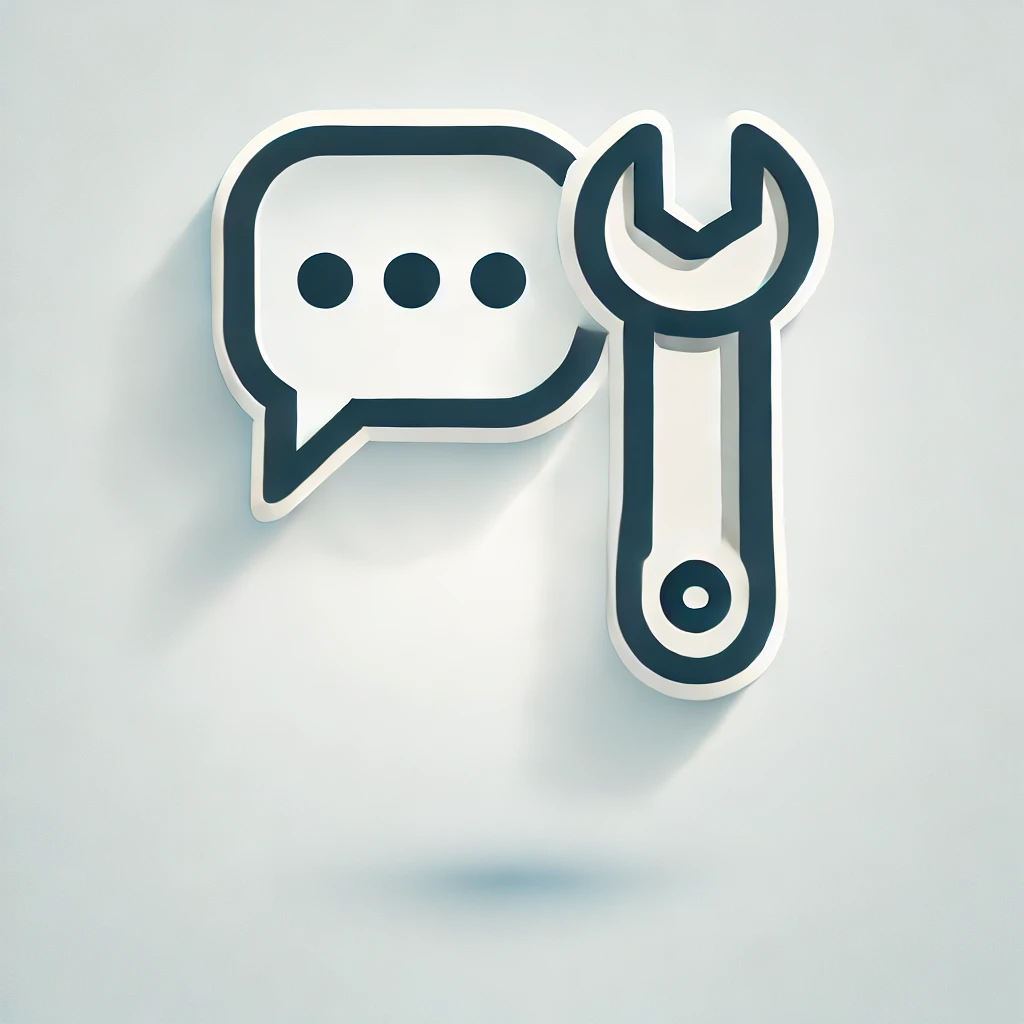
"Hai un'opinione tecnica o una domanda specifica? Non esitare, lascia un commento! La tua esperienza può arricchire la discussione e aiutare altri professionisti a trovare soluzioni. Condividi il tuo punto di vista!"