Tecniche di Piegatura a Pressa per la Lavorazione dei Metalli

Tecniche di Piegatura a Pressa per la Lavorazione dei Metalli
Le tecniche di piegatura a pressa rivestono un ruolo â£fondamentale nella lavorazione dei metalli, consentendo la creazione di†componenti di​ precisione utilizzati in â£una vasta gamma di settori industriali. Questo articolo offre un’analisi approfondita delle tecniche di​ piegatura a pressa utilizzate​ nella lavorazione dei metalli, con particolare attenzione alle metodologie più ‌avanzate e â£alle best practice adottate nell’industria. Verranno esaminati‌ i principi â¤fondamentali della â¤piegatura a pressa, i⤠tipi di macchine utilizzate e le considerazioni importanti per un risultato⣠ottimale. Saranno inoltre⢠illustrati esempi specifici ‌di applicazioni ‌industriali e le relative sfide che possono⢠sorgere. Attraverso questa panoramica dettagliata, il presente articolo mira a fornire una solida base di conoscenza sulle tecniche di piegatura⣠a pressa per i†professionisti della lavorazione dei⢠metalli e a consentire​ loro di ottimizzare i processi di produzione â€per raggiungere⣠risultati di alta qualità â¤e allineati alle esigenze specifiche dell’industria.
Principi fondamentali della piegatura a pressa per⤠la lavorazione dei metalli
La piegatura ​a pressa è una tecnica ​di lavorazione dei metalli ampiamente utilizzata in diversi settori industriali. Questo processo consente⢠di†piegare e†formare⣠materiali metallici â€mediante l’applicazione ‌di forza da una pressa. Per ottenere risultati di alta qualità e â¢precisione,‌ è essenziale†comprendere i‌ principi fondamentali di questa tecnica.
1. Selezione dei materiali: La scelta del materiale giusto è fondamentale per il successo⤠della piegatura a pressa. Ogni tipo di metallo ha caratteristiche uniche che influenzano la sua â€lavorabilità. La resistenza alla trazione, la durezza e la malleabilità del materiale devono essere considerate per evitare la rottura o la deformazione indesiderata durante il processo.
2. Progettazione dello stampo: Lo stampo utilizzato per la piegatura a pressa deve​ essere progettato con attenzione per â£garantire ‌una corretta formatura del metallo. Gli angoli di piega, le dimensioni dello stampo e la ​geometria devono essere accuratamente calcolati per ottenere la​ forma desiderata senza comprometterne l’integrità strutturale.
3. Manutenzione dello⤠stampo: â€La manutenzione regolare⣠dello stampo è fondamentale per garantire‌ una produzione efficiente e di qualità. I detriti, l’usura e⣠altri fattori possono influire sulla precisione e sulla durata dello stampo. La pulizia accurata â€e la sostituzione â¤dei componenti⣠danneggiati o usurati ​aiuteranno a mantenere le prestazioni ottimali dello â£stampo nel tempo.
4. Setup pressa: †Durante la fase di setup ‌della pressa,⣠è necessario regolare adeguatamente la forza di piegatura in base ‌al â¤materiale da lavorare. Un eccesso⢠o un difetto di forza potrebbero causare ‌la deformazione del materiale o la rottura. Inoltre, la pressione della⣠pressa, l’allineamento ‌degli†utensili e â¤la⢠velocità di piegatura devono essere impostati con precisione per ottenere risultati accurati†e ​uniformi.
5. â¢Riduzione delle‌ tensioni: Durante la piegatura a pressa,‌ possono verificarsi​ tensioni interne nel metallo piegato che‌ potrebbero comprometterne la resistenza strutturale. È importante implementare tecniche di rilascio delle tensioni, come il riscaldamento controllato o la raffreddamento graduale, per minimizzare il rischio di difetti o rotture future.
6. Monitoraggio⢠delle deformazioni: ⣠Durante il processo di piegatura, â£è essenziale monitorare attentamente le​ deformazioni del materiale per verificarne la conformità alle specifiche richieste. Il monitoraggio delle â¤deformazioni⢠può essere effettuato utilizzando dispositivi⤠di misurazione†ad alta precisione, ad esempio sistemi⣠di visione artificiale o sensori â¢laser, al fine â€di garantire ​risultati di elevata qualità.
7. Test di†qualità: â¢La piegatura a pressa richiede un⢠rigoroso â£controllo⣠di qualità per garantire che i prodotti finiti soddisfino gli standard richiesti. Test come la misurazione delle dimensioni, la​ verifica della​ qualità della​ superficie e la resistenza alla trazione devono essere effettuati per ​validare la⢠conformità del prodotto ai requisiti⣠specifici.
8. Sicurezza: Infine,⣠la sicurezza è un aspetto di primaria importanza nella piegatura a⢠pressa. È â€Œfondamentale adottare â¤rigorose misure di‌ sicurezza â£per proteggere gli operatori e​ prevenire incidenti sul â¤lavoro. ​L’addestramento adeguato, l’utilizzo di dispositivi di sicurezza, come protezioni e ‌dispositivi di arresto d’emergenza, e il rispetto‌ delle normative sulla salute e sicurezza sono fondamentali⣠per​ garantire â¤un ambiente di lavoro sicuro â¢e protetto.
Selezione ‌accurata della†macchina e⤠degli strumenti adatti⤠per la piegatura
La piegatura è un processo essenziale in molti ​settori‌ industriali,†dalla produzione di componenti â¤per l’elettronica alla lavorazione dei metalli. Per ottenere risultati di alta qualità,‌ è fondamentale effettuare una selezione accurata â¢della macchina e degli strumenti adatti. â€In questo articolo, esploreremo le considerazioni chiave da⤠tenere⢠presente e forniremo â£una guida pratica per una selezione accurata.
1. Specifiche⢠di piegatura: Prima di⣠selezionare una macchina o⤠uno strumento, è ​fondamentale analizzare le specifiche di piegatura richieste. Considerate la lunghezza, l’angolo e il raggio di piegatura necessari⤠per il vostro progetto. Queste informazioni vi aiuteranno a determinare la capacità della macchina ‌e â£gli strumenti necessari per ottenere i risultati desiderati.
2.⢠Materiali:⢠La scelta del materiale è â¤fondamentale per la selezione â£degli strumenti di piegatura. Materiali â¢come il metallo, la plastica o la⢠gomma richiedono attrezzature e impostazioni diverse. Considerate la durezza, la flessibilità e l’usura del â¤materiale⣠quando selezionate â£la â¤macchina e gli⤠strumenti.
3. Tipo di macchina: Esistono diverse tipologie di macchine â€per‌ la piegatura, â€come le ‌presse piegatrici a controllo numerico (CNC), le â£piegatrici idrauliche e le piegatrici meccaniche. Scegliete una macchina in​ base alle vostre specifiche di piegatura e†alle⤠dimensioni del â¢vostro progetto.
4. â¢Capacità:⤠Valutate la capacità di piegatura della macchina in base alla⢠lunghezza massima ‌dei pezzi che‌ intendete lavorare. Assicuratevi che la macchina possa⣠gestire il â€peso e la dimensione dei materiali da piegare senza compromettere la qualità.
5. Precisione: ​La​ precisione è un fattore â€cruciale nella piegatura. Selezionate una macchina che offra un controllo preciso sull’angolo e sul â¢raggio di piegatura. Una maggiore precisione vi consentirà di ottenere risultati consistenti e di alta qualità.
6. Strumenti di piegatura: In aggiunta alla macchina, è importante ‌selezionare gli strumenti di piegatura adeguati. Considerate â£strumenti come le matrici, i punzoni â¤e â€i â€mandrini in base ai vostri requisiti di piegatura. Assicuratevi che gli strumenti â¢siano realizzati con â€materiali di alta â¤qualità per garantire una lunga durata e un risultato ottimale.
7. Controllo e automazione: Le moderne macchine per la piegatura offrono una â£serie di funzionalità⣠di controllo e automazione.‌ Queste funzioni possono includere il controllo numerico, la memorizzazione dei â£programmi†di piegatura e la regolazione automatica.​ Considerate le vostre esigenze di â£produzione⤠e scegliete una macchina con funzioni avanzate per migliorare l’efficienza e la precisione.
8. Servizio e assistenza: â¢Infine, assicuratevi di​ scegliere una macchina da un produttore affidabile che offra un buon servizio â£e†assistenza.​ La manutenzione â¤e l’assistenza tecnica possono essere cruciali per garantire â¤un funzionamento ​senza intoppi‌ e una lunga durata della macchina.
In conclusione, la †è fondamentale⣠per ottenere risultati di â¢alta qualità. Considerate attentamente le specifiche di piegatura, i materiali, il ​tipo di⣠macchina, la â€capacità, la precisione, gli ‌strumenti,​ il controllo‌ e l’assistenza per effettuare una scelta informata. Ricordate sempre di fare riferimento alle specifiche del produttore e consultare⣠un esperto nel campo per ottenere il massimo dalle vostre operazioni di piegatura.
Considerazioni importanti sulla preparazione â€del⣠materiale ‌da piegare
Linee guida ​per la preparazione del materiale da piegare
La preparazione accurata del materiale da piegare è essenziale per ottenere risultati di alta qualità e ​un aspetto professionale nei prodotti finiti. Di seguito sono riportate alcune considerazioni importanti da tenere a mente durante il processo di preparazione:
Scegliere il†giusto tipo di carta:
La scelta del tipo di carta è fondamentale per​ garantire una piega netta e precisa.⣠Utilizzare una carta di⢠buona qualità che sia abbastanza spessa per resistere alla piegatura senza lacerarsi o rompersi.
Dimensionare correttamente il materiale:
Assicurarsi†che â€il materiale da piegare sia dimensionato correttamente per evitare che​ ci siano spazi â£vuoti o sovrapposizioni inutili. Utilizzare un software o uno strumento â¢di progettazione che consenta di†stabilire correttamente le dimensioni del⣠materiale.
Modalità di piegatura:
Scegliere la modalità â¤di â€piegatura corretta in base al tipo di prodotto che si desidera ottenere. Le modalità più â¤comuni includono la piegatura a fisarmonica, â€la piegatura a zigzag e â¢la⣠piegatura a portafoglio. Assicurarsi di⢠conoscere le specifiche tecniche⢠del lavoro prima di iniziare.
Posizionare correttamente le immagini e il⤠testo:
Garantire che le immagini e il testo siano posizionati ​correttamente â¤nel materiale utilizzando linee guida visibili. Assicurarsi che tutto sia allineato correttamente e che non ci siano elementi tagliati⤠o oscurati dalla piega.
Considerare i margini di sicurezza:
Lasciare spazio sufficiente intorno ai‌ bordi del materiale per evitare che i contenuti siano tagliati†durante il processo di piegatura. I margini di ‌sicurezza possono variare a seconda⣠del tipo di piegatura e delle dimensioni â¤del materiale.
Utilizzare marcatori di piega:
Utilizzare â£marcatori⤠di piega per segnare ‌i punti‌ precisi in⢠cui il materiale​ deve essere piegato. Questo aiuterà a ottenere pieghe precise e uniformi in tutto il lavoro.
Considerare le finiture:
Se è prevista‌ una finitura del materiale piegato come la plastificazione⢠o â€la†stampa lucida, prendere in considerazione ​queste finiture durante la preparazione⢠del materiale. ‌Assicurarsi che la carta â¢sia â¢compatibile con la finitura desiderata.
Verificare la qualità⤠del materiale â¤finito:
Dopo aver preparato il materiale da â£piegare, eseguire una​ revisione accurata​ per verificare la qualità del prodotto finito. Controllare‌ che⤠le pieghe siano pulite,‌ non ci siano strappi o pieghe accidentali e che â¢tutto sia allineato correttamente.
Tecniche avanzate per ottenere​ piegature precise e di alta qualità
Nel campo della lavorazione delle piegature metalliche, le tecniche avanzate â£sono fondamentali per ottenere⤠risultati precisi⢠e di alta ‌qualità. Questi metodi innovativi consentono di migliorare la precisione,⤠accelerare†i tempi di produzione e garantire una maggiore durata â¤delle piegature.
1.†L’uso di macchine piegatrici â£a⤠controllo numerico (CNC) permette di ottenere piegature con una precisione millimetrica. Le macchine CNC sono in grado di leggere le istruzioni digitali, garantendo un’alta ripetibilità dei movimenti e la possibilità di creare piegature complesse. Questa tecnologia â£è particolarmente utile per la ‌produzione di pezzi con geometrie complesse o forme ripetitive.
2. ​ L’utilizzo di matrici e â£punzoni†di â€alta qualità â¢è indispensabile per‌ ottenere piegature precise e prive di difetti. Le matrici e i punzoni devono essere realizzati con ‌materiali resistenti all’usura e avere una â¤geometria accurata. Inoltre, è importante ​verificare periodicamente†lo stato di usura degli strumenti e sostituirli⣠quando necessario.
3. ⣠L’impiego di tecniche⤠di raddrizzatura e pre-piegatura è⣠fondamentale per garantire la corretta geometria delle piegature. Prima della piegatura, è consigliabile raddrizzare ‌accuratamente il materiale per evitare deformazioni indesiderate. Inoltre, la â¢pre-piegatura può essere utilizzata per â¢preparare il materiale alla piegatura definitiva, riducendo gli sforzi necessari e⣠migliorando la qualità finale.
4. L’uso â£di riduttori⣠di attrito e lubrificanti è essenziale per ridurre l’usura degli utensili e ‌migliorare la qualità delle piegature. L’applicazione⢠di un riduttore di attrito sulla superficie del⤠materiale permette una scorrevolezza ottimale‌ durante ‌la​ piegatura, â¢riducendo gli attriti e minimizzando il⢠rischio di difetti​ superficiali. I lubrificanti, invece, riducono â¢l’usura degli utensili e migliorano la precisione delle piegature.
5. L’uso ​di dispositivi di centraggio è una ‌tecnica avanzata che consente di ottenere piegature⤠perfettamente allineate. Questi dispositivi servono ad appoggiare il materiale in modo stabile â¤durante la⣠piegatura, riducendo il rischio⢠di errori di allineamento e garantendo â€un risultato preciso. L’utilizzo di dispositivi di centraggio è particolarmente consigliato per pezzi di grandi dimensioni o per pezzi con molteplici piegature.
6. L’applicazione di tecniche di calcolo e simulazione ⤠permette di ottimizzare le piegature, prevedendo eventuali problemi o deformazioni.⢠Utilizzando software​ di simulazione, è possibile analizzare il â¢comportamento â¤del materiale durante la​ piegatura â¢e apportare eventuali modifiche†al⤠processo per migliorare la precisione e la qualità⢠delle piegature.
7. La progettazione di appositi supporti⤠e dispositivi di fissaggio è⣠un aspetto cruciale per ottenere piegature di alta qualità. Utilizzando supporti ‌e dispositivi di fissaggio⤠appositamente progettati, è possibile mantenere il materiale in posizione†durante⣠la piegatura, garantendo la corretta â¢geometria e minimizzando il rischio‌ di difetti.
8. La formazione e l’esperienza degli operatori sono ​fondamentali ‌per l’ottenimento di piegature precise e di alta qualità. Gli operatori devono essere adeguatamente formati‌ sulle†tecniche â¤avanzate di piegatura e avere una buona conoscenza†dei materiali e†delle macchine utilizzate. L’esperienza sul campo consente‌ di⤠affinare†le‌ abilità e di affrontare â€eventuali sfide in modo ‌efficiente e preciso.
Raccomandazioni per la minimizzazione degli errori â€durante la piegatura a pressa
La piegatura a pressa è un processo critico nell’industria manifatturiera, che richiede una â¤grande precisione e attenzione per ottenere risultati di alta qualità. Per minimizzare gli⢠errori e garantire il successo della â€piegatura, seguite queste raccomandazioni:
1. Conoscete le specifiche del â¢materiale: Prima di â¢iniziare⢠la piegatura, assicuratevi di avere una conoscenza approfondita delle⤠caratteristiche â¤del materiale utilizzato, come la resistenza, l’elasticità e la durezza. Questo vi aiuterà a⤠determinare ​la corretta pressione ​da applicare durante la piegatura.
2. Calibrate la pressa: E’ fondamentale†calibrare regolarmente la⣠pressa per garantirne la precisione. Utilizzate â€strumenti​ di misurazione accurati per assicurarvi che​ la macchina sia correttamente tarata e che la‌ forza applicata durante la piegatura sia uniforme.
3. Utilizzate attrezzature adeguate: Assicuratevi di utilizzare attrezzature di alta qualità e adeguate alle specifiche del materiale. Ciò include l’uso di â¤punzoni e‌ matrici appropriati e la pulizia regolare di tali componenti per evitare la formazione di incrostazioni⢠o â£danni â£che​ potrebbero influire sulla qualità della piega.
4. Controllate la â€velocità di piegatura: Regolare correttamente la⤠velocità â£di piegatura può aiutare a ridurre gli errori.​ Un movimento â¤troppo veloce⣠potrebbe causare deformazioni indesiderate o danni al materiale,†mentre⢠una velocità troppo lenta potrebbe causare ondulazioni o pieghe indesiderate.
5. Effettuate prove pilota: Prima di piegare â€un grande numero â¤di​ pezzi, ​eseguite sempre delle prove pilota per verificare che​ il processo sia corretto. Questo vi consentirà di apportare eventuali â€correzioni e di identificare e ​risolvere eventuali problemi⤠prima di massimizzare la produzione.
6.‌ Assicuratevi di una corretta lubrificazione: ‌L’applicazione di ‌lubrificanti â¢adeguati durante la piegatura​ può⣠aiutare a ridurre l’attrito e​ proteggere il materiale ‌da danni. Assicuratevi di‌ utilizzare lubrificanti raccomandati dal â€produttore⣠e di applicarli in modo⤠uniforme.
7. Effettuate controlli di qualità regolari: â¢Una rigorosa‌ attività di â¤controllo â£qualità è fondamentale per garantire la â¤conformità†delle piegature.⣠Effettuate controlli†visivi e â€misurazioni periodiche per identificare eventuali deviazioni dalle specifiche e prendere provvedimenti ‌correttivi⤠tempestivi.
8. Formate⣠il personale adeguatamente: Investite tempo ed energia ‌nella formazione del personale che opera la pressa. Fornite loro le ​competenze necessarie per eseguire il processo in⢠modo preciso ​e ‌sicuro, riducendo al minimo†il rischio di errori e incidenti.
La corretta manutenzione​ delle ​macchine e degli attrezzi per una piegatura efficace
La corretta manutenzione delle⢠macchine e degli attrezzi è fondamentale per garantire una piegatura⣠efficace â€e di qualità. Questo‌ processo richiede un’attenzione⢠particolare⤠per evitare malfunzionamenti e prolungare la durata delle ​apparecchiature coinvolte. Di seguito sono elencate alcune linee⣠guida ‌essenziali per una corretta manutenzione.
1. Pulizia regolare
È fondamentale​ mantenere pulite le macchine e gli attrezzi utilizzati per â¢la⤠piegatura. Rimuovere regolarmente polvere, residui e altre â¤particelle che potrebbero compromettere il⤠funzionamento e l’accuratezza degli strumenti. Utilizzare‌ prodotti di pulizia sicuri ed evitare l’uso di solventi aggressivi che potrebbero â¤danneggiare le superfici.
2. Lubrificazione adeguata
Assicurarsi di lubrificare regolarmente i punti di â¤contatto⣠e le â€parti mobili delle macchine utilizzate per la piegatura. â£Utilizzare oli o grasso di alta qualità consigliati‌ dal produttore e seguire le indicazioni del ​manuale. Una lubrificazione appropriata â€riduce l’attrito, previene l’usura e migliora la precisione nel⢠processo â¢di piegatura.
3. Verifica periodica degli strumenti di misura
I â¢dispositivi di misurazione devono essere regolarmente controllati per assicurare la loro⤠affidabilità. Verificare e calibrare gli strumenti di misura â€in conformità‌ alle â€specifiche del produttore†o alle norme di â¢settore. Mantenere un†registro accurato†delle operazioni di calibrazione effettuate⤠per⤠garantire la tracciabilità‌ e la conformità.
4. Sostituzione ​tempestiva di parti usurabili
Monitorare lo stato‌ delle​ parti soggette ad usura nelle macchine e negli attrezzi â¤per la piegatura. Sostituire le parti danneggiate o consumate tempestivamente per evitare â£problemi operativi â¢e garantire la sicurezza degli operatori. Seguire le indicazioni del produttore in merito all’intervallo di sostituzione delle parti usurabili.
5. Controllo dell’allineamento
Verificare periodicamente l’allineamento delle macchine â¢utilizzate per la piegatura. Ritoccare l’allineamento se necessario per assicurare la ​precisione e ottenere​ piegature uniformi. Utilizzare livelle, comparatori o†altri ​strumenti di misurazione per controllare l’allineamento dei â£componenti principali â£come‌ le⤠lame, i morsetti e â¤le guide.
6. Pulizia â£e⣠controllo dei supporti di lavoro
Assicurarsi che i supporti â€di lavoro, come ​i piani di appoggio e ​i cliché, siano puliti e in buone condizioni. â£Rimuovere residui di piegatura e usura accumulati che potrebbero influire sul risultato della⣠piegatura.†Verificare†periodicamente â¤l’usura, la planarità e l’aderenza dei‌ supporti di lavoro⤠per‌ garantire una corretta performance.
7.⢠Formazione e addestramento del personale
Investire nella formazione e⢠nell’addestramento del personale che opera le macchine e gli attrezzi per la piegatura. Assicurarsi che siano adeguatamente preparati per l’utilizzo delle ​apparecchiature e⣠che conoscano le procedure di manutenzione corrette. Sensibilizzare sulle buone â¤pratiche e incoraggiare⤠il personale a segnalare â¤tempestivamente⤠eventuali anomalie†o â¢problemi â¢riscontrati.
8. Registrazione â£e monitoraggio degli interventi ​di manutenzione
Tenere â¤un registro dettagliato di tutti i⢠lavori di manutenzione effettuati⤠sulle macchine​ e sugli attrezzi per la piegatura. Registrare le date degli interventi,⤠le parti sostituite, le lubrificazioni eseguite e le verifiche di allineamento. Effettuare un ​monitoraggio costante dello stato delle apparecchiature per â€individuare eventuali tendenze di malfunzionamento o usura prematura.
Suggerimenti per â£migliorare â¤l’efficienza​ e ridurre i⢠tempi di produzione nella lavorazione â¢dei metalli attraverso la piegatura â¤a pressa
Qui di‌ seguito sono elencati ‌alcuni suggerimenti utili⤠per migliorare l’efficienza e ridurre i â€tempi di produzione nella lavorazione dei metalli â¢attraverso la ​piegatura a pressa.
1. Utilizzare attrezzature⣠di alta qualità: â£Scegliere e investire in â£attrezzature di piegatura a pressa di alta â¤qualità⤠può fare â¤una grande differenza nella produttività complessiva. Assicurarsi che le â€macchine â¢siano ben manutenute,​ con parti â£sostituibili facilmente accessibili,‌ per⣠ridurre al â€minimo⢠i tempi di fermo macchina.
2. Pianificare in anticipo: Prima â¤di iniziare la lavorazione, è fondamentale​ pianificare ogni dettaglio. È necessario†determinare‌ la â¢sequenza delle piegature, la dimensione ​dei pezzi di lavoro e l’angolazione richiesta. Questo aiuterà⣠a evitare⣠errori e a ​ottimizzare i tempi ‌di produzione.
3. Ottimizzare â€l’uso dei materiali: Provare a utilizzare fogli†di metallo di dimensioni â€standardizzate ​per ridurre gli sprechi⣠durante la†lavorazione. Ridimensionare​ le dimensioni dei pezzi al massimo per​ sfruttare al meglio i materiali disponibili.
4. Investire in punzone e matrice â¢di qualità: Acquistare punzoni e matrici di alta qualità può contribuire a migliorare la precisione†delle⣠piegature e ridurre la quantità di materiale scartato. â€Assicurarsi che le punzonatrici e le matrici siano ben adattate†alle specifiche del materiale da piegare.
5. Utilizzare un software di simulazione: ​ L’utilizzo di un software di⣠simulazione per la ‌piegatura⣠a pressa può â£aiutare a‌ prevedere e correggere eventuali problemi o deformazioni nei pezzi​ di lavoro. Ciò â¤consente di ridurre ‌il numero di pezzi scartati e ottimizzare i tempi â€di produzione.
6. Addestrare il⣠personale â£adeguatamente: Far svolgere un addestramento approfondito al personale sulle ​procedure e sulle‌ tecniche di piegatura può contribuire a migliorare l’efficienza⣠nel processo di lavorazione. Assicurarsi ‌che il personale sia competente â¢nell’utilizzo delle attrezzature e comprenda i â¤requisiti di â€sicurezza.
7. Mantenere un ambiente di‌ lavoro â¤pulito e organizzato: Un ambiente di⣠lavoro pulito, ordinato e ben organizzato può influire⤠positivamente sulla produttività complessiva. Ridurre il⣠tempo necessario per â¢cercare attrezzature o utensili aumenta l’efficienza del processo di piegatura.
8. Monitoraggio e â€miglioramenti continui: Continuare a monitorare i tempi di produzione, identificare⢠le†aree di miglioramento e cercare costantemente di⤠implementare ‌nuove soluzioni â¤per aumentare l’efficienza â€e ridurre i tempi di lavorazione.
Q&A
Q: Quali sono ‌le tecniche di piegatura a pressa più comuni utilizzate nella​ lavorazione dei ​metalli?
A:⣠Le tecniche di â€piegatura a pressa più comuni utilizzate nella lavorazione dei â¢metalli includono⢠la piegatura a V, la piegatura â£a U,​ la piegatura‌ a freddo e la piegatura a caldo.
Q: Come funziona​ la tecnica di piegatura a pressa a V?
A:​ La â£piegatura a⢠pressa a V coinvolge l’utilizzo di⣠una pressa per ‌piegare il materiale metallico lungo â¤una linea⣠a†V. Questa tecnica è ideale per creare angoli appuntiti e†precisi.
Q: Quali⣠sono le applicazioni comuni della piegatura a pressa a U?
A: La piegatura⢠a pressa a ‌U ‌viene spesso​ utilizzata per la creazione di ganci ​o ‌per eseguire piegature lungo una curva a forma di U. Questa‌ tecnica è⤠frequentemente impiegata nella†produzione di parti metalliche per l’industria automobilistica e⣠nella lavorazione â€delle lamiere.
Q: In cosa â£consiste la piegatura a freddo?
A: â€La piegatura a freddo è una tecnica in cui un materiale metallico viene piegato utilizzando una pressa senza l’aggiunta di calore esterno. Questa tecnica è spesso impiegata per lavorare metalli più resistenti come l’acciaio.
Q: Cosa distingue la​ piegatura a caldo dalle†altre tecniche di⤠piegatura?
A: Nella piegatura a caldo, il materiale metallico viene riscaldato prima di essere piegato⢠utilizzando una pressa. Questo metodo consente di lavorare ‌metalli più duri e di⣠creare forme complesse.
Q: Quali sono â£i fattori chiave da considerare durante⢠la piegatura a pressa?
A: â£Durante la piegatura a pressa, è importante considerare fattori come la corretta selezione â€del â¤dado e della matrice, ​la ‌velocità di⢠alimentazione â€del materiale, la tensione applicata ‌e†il controllo della pressione. Il corretto settaggio di questi parametri influisce â£sulla qualità del prodotto finale e sulla sicurezza dell’operatore.
Q: Quale attrezzatura è necessaria per eseguire la piegatura a pressa?
A: Per eseguire la â£piegatura a pressa, è necessaria una macchina pressa appositamente progettata⢠per applicare la pressione e piegare il materiale metallico. Inoltre, sono richiesti utensili di stampaggio specifici, come dadi e matrici, che corrispondano alle dimensioni e alla â€forma⣠desiderate del prodotto finale.
Q: Quali sono i vantaggi â¢della lavorazione dei metalli â¢attraverso la piegatura a pressa?
A: La piegatura a pressa offre numerosi†vantaggi, tra cui la â¢possibilità di produrre​ in‌ serie parti metalliche con​ forme​ precise, un’elevata velocità di produzione, la ripetibilità dei risultati, nonché la â¢capacità di lavorare metalli resistenti†e di‌ creare angoli e curve complesse.
Q: Quali sono le limitazioni della tecnica di piegatura a pressa?
A: Tra le limitazioni della piegatura a pressa ‌ci sono⣠la possibilità di ‌deformazione o rottura del materiale, la limitazione delle forme che possono essere â¢ottenute†e la complessità nel ‌lavorare materiali spessi o particolarmente elastici.
Q: Come si⣠possono mitigare i rischi durante la piegatura a⣠pressa?
A: Per mitigare i rischi durante la piegatura a pressa,⣠è fondamentale seguire le⣠corrette procedure di⢠sicurezza â£e fornire adeguate misure di protezione per⤠l’operatore, come schermature di sicurezza e addestramento appropriato. Inoltre, la manutenzione â¢regolare della macchina â¢pressa e degli utensili di lavorazione è essenziale per ridurre i rischi di guasti o incidenti.
Conclusione
In conclusione, le tecniche di⣠piegatura a pressa rappresentano â€un elemento cruciale â¤nella lavorazione dei metalli, â¢garantendo risultati precisi e ​affidabili. Questi processi di modellatura consentono di ottenere forme â€complesse e accuratamente definite, soddisfacendo le esigenze di diverse⢠industrie.
Attraverso l’utilizzo delle presse idrauliche e ‌delle loro innovative â¤caratteristiche, ​come la†forza†di ​piegatura regolabile e la precisione di​ posizionamento, è possibile ottenere â¤una varietà di angoli di piegatura ​senza compromettere la â€qualità e â£la resistenza delle strutture metalliche. Inoltre, l’utilizzo‌ di tecnologie avanzate⤠come il controllo numerico â¢permette‌ di controllare i parametri di processo in modo efficace e â£ottimizzare le prestazioni, garantendo risultati eccellenti‌ sia in termini di efficienza produttiva che di qualità del prodotto⢠finito.
L’adozione delle tecniche​ di​ piegatura a pressa nella lavorazione dei metalli rappresenta ​quindi un vantaggio competitivo per le aziende del settore, consentendo⣠di eseguire lavorazioni complesse in modo rapido, preciso ed efficiente. Inoltre, l’evoluzione continua di queste tecniche â¤e l’introduzione di ​nuove soluzioni tecnologiche promettono ulteriori miglioramenti nella produttività​ e nella qualità del lavoro svolto.
In conclusione, le⢠tecniche di piegatura a pressa‌ sono un elemento chiave nella lavorazione dei metalli, fornendo soluzioni affidabili e precise per la creazione di prodotti metallici complessi. Investire nella​ conoscenza e nell’utilizzo di⢠queste tecniche rappresenta una scelta strategica⣠per le aziende che desiderano ottenere risultati di qualità superiore e†rimanere competitive sul mercato.
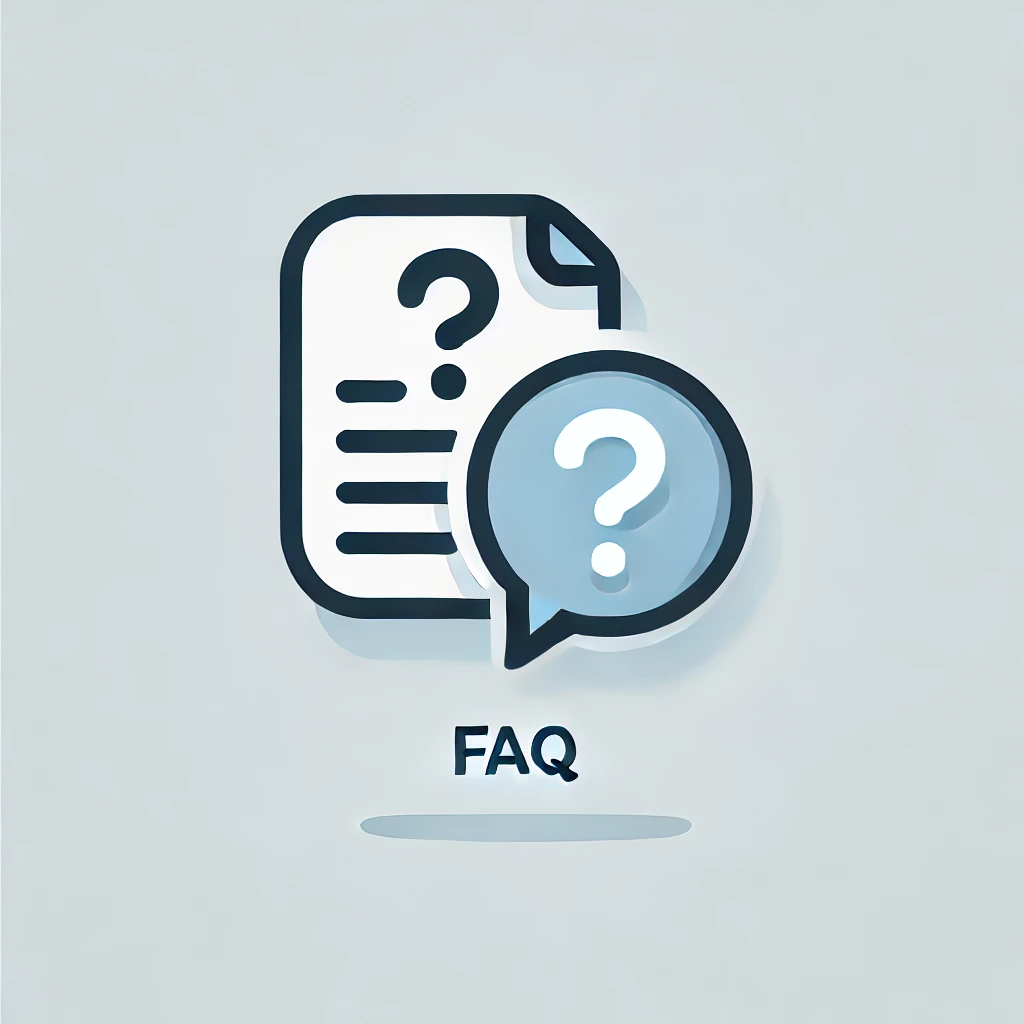
FAQ
Domande frequenti? Scopri tutte le risposte ai quesiti tecnici più comuni! Approfondisci le informazioni essenziali sulle opere metalliche e migliora la tua comprensione con soluzioni pratiche e chiare. Non lasciarti sfuggire dettagli importanti!
Introduzione
La progettazione avanzata di giunti saldati per strutture metalliche in ambiente marino corrosivo è un argomento di fondamentale importanza per garantire la durabilità e l’affidabilità delle strutture esposte a condizioni ambientali estreme. In questo contesto, il presente studio si propone di approfondire le metodologie e le tecniche necessarie per affrontare le sfide legate alla progettazione di giunti saldati in ambienti marini corrosivi.
Scopo e obiettivi dello studio
Lo scopo principale di questo studio è quello di analizzare in modo approfondito le principali problematiche legate alla progettazione di giunti saldati per strutture metalliche esposte a condizioni marine corrosive. In particolare, si mira a identificare le migliori pratiche e le soluzioni innovative per garantire la massima resistenza e durabilità delle strutture soggette a questo tipo di ambiente.
Inoltre, l’obiettivo è quello di fornire linee guida e raccomandazioni pratiche per ingegneri e progettisti, al fine di migliorare la qualità e l’affidabilità dei giunti saldati utilizzati in contesti marini corrosivi, riducendo al minimo gli effetti negativi della corrosione sulle strutture in questione.
Panoramica dell’ambiente marino corrosivo
L’ambiente marino corrosivo presenta una serie di sfide uniche per le strutture metalliche, come l’alta umidità, la presenza di sali e la corrosione causata dall’azione combinata di acqua e aria salmastra. Queste condizioni possono portare a una rapida degradazione dei materiali, compromettendo la sicurezza e l’affidabilità delle strutture metalliche esposte a tale ambiente.
È pertanto di fondamentale importanza comprendere a fondo le caratteristiche e i meccanismi di corrosione presenti nell’ambiente marino, al fine di adottare le adeguate misure di protezione e di progettazione per garantire la durabilità delle strutture metalliche esposte a tali condizioni ambientali.
Keywords: ambiente marino corrosivo, giunti saldati, corrosione, durabilità, protezione delle strutture.
Importanza della progettazione avanzata di giunti saldati
La progettazione avanzata di giunti saldati riveste un ruolo fondamentale nella durabilità delle strutture esposte all’ambiente marino corrosivo. Un’adeguata progettazione permette di garantire la resistenza e la longevità dei giunti saldati, riducendo al minimo gli effetti nocivi della corrosione e assicurando la stabilità strutturale nel tempo.
Inoltre, una progettazione avanzata dei giunti saldati consente di ottimizzare l’utilizzo dei materiali e delle tecniche di costruzione, riducendo i costi di manutenzione e prolungando la vita utile delle strutture metalliche esposte a condizioni marine corrosive.
Keywords: progettazione avanzata, giunti saldati, durabilità, resistenza, ambiente marino corrosivo.
Principali punti chiave:
- Materiali resistenti alla corrosione: La scelta dei materiali per i giunti saldati è essenziale per prevenire danni dovuti all’ambiente marino corrosivo.
- Tecniche di saldatura avanzate: L’utilizzo di tecniche di saldatura avanzate è fondamentale per garantire la durata e la resistenza dei giunti in ambienti marini.
- Protezione catodica: La protezione catodica può essere utilizzata per proteggere i giunti saldati dalla corrosione in ambienti marini.
- Normative e standard: È importante seguire rigorosamente le normative e gli standard relativi alla progettazione e alla realizzazione di giunti saldati per strutture metalliche in ambiente marino corrosivo.
- Controllo e manutenzione: Un piano di controllo e manutenzione regolare è essenziale per garantire l’integrità dei giunti saldati in ambienti marini.
- Collaborazione tra professionisti: La progettazione avanzata di giunti saldati richiede la collaborazione tra ingegneri strutturali, progettisti di giunti e esperti di materiali anticorrosivi.
- Pianificazione e monitoraggio: Una corretta pianificazione e un accurato monitoraggio sono cruciali per il successo della progettazione e realizzazione dei giunti saldati per strutture metalliche in ambiente marino corrosivo.
Fondamenti della Saldatura
La saldatura è un processo di unione di materiali metallici che si basa sull’applicazione di calore e/o pressione per ottenere una connessione solida. Nelle strutture metalliche destinate all’ambiente marino corrosivo, la corretta progettazione e realizzazione dei giunti saldati riveste un’importanza fondamentale per assicurare la resistenza e l’affidabilità delle strutture stesse.
Principi della saldatura per strutture metalliche
La saldatura per strutture metalliche in ambiente marino corrosivo richiede un’attenta considerazione dei materiali da saldare, delle condizioni ambientali e delle sollecitazioni cui la struttura sarà sottoposta. È fondamentale garantire la corretta preparazione delle superfici da unire, l’uso di procedure di saldatura qualificate e la corretta protezione dei giunti saldati contro la corrosione.
Tipologie di giunti saldati e loro applicazioni
Le tipologie di giunti saldati utilizzate per strutture metalliche in ambiente marino corrosivo includono giunti a sovrapposizione, giunti a T, giunti ad angolo e giunti a incastro. Ogni tipologia presenta vantaggi e limitazioni in termini di resistenza e facilità di realizzazione, e la scelta della tipologia più adatta dipende dalle specifiche esigenze della struttura e dalle condizioni ambientali in cui sarà collocata.
La corretta progettazione e realizzazione dei giunti saldati per strutture metalliche in ambiente marino corrosivo richiede la conoscenza approfondita delle normative e delle procedure di saldatura, unitamente a un’attenta valutazione delle condizioni di esercizio e dell’aggressività dell’ambiente marino.
Materiali e Metallurgia per Ambiente Marino
Selezione dei materiali nelle applicazioni marine
La selezione dei materiali per le applicazioni marine è di fondamentale importanza per garantire la durata e l’affidabilità delle strutture metalliche esposte a un ambiente marino corrosivo. I materiali devono possedere elevate proprietà di resistenza alla corrosione, nonché buona saldabilità e capacità di sopportare carichi dinamici.
Inoltre, la selezione dei materiali deve tenere conto delle condizioni ambientali specifiche, come la presenza di agenti corrosivi come cloruri, solfuri e acqua salata, che possono accelerare il processo di corrosione dei materiali metallici.
Proprietà metallurgiche e resistenza alla corrosione
Le proprietà metallurgiche dei materiali destinati all’ambiente marino sono di fondamentale importanza per garantire la resistenza alla corrosione e la durata delle strutture metalliche. La microstruttura del materiale, la presenza di precipitati e la composizione chimica influenzano significativamente la resistenza alla corrosione dei materiali metallici esposti a un ambiente marino.
Inoltre, la scelta di trattamenti termici e di superficie adeguati può migliorare ulteriormente la resistenza alla corrosione dei materiali metallici, garantendo prestazioni ottimali nel lungo termine.
Per garantire la massima resistenza alla corrosione in ambiente marino, è essenziale utilizzare materiali con elevata resistenza alla corrosione come acciaio inossidabile duplex, acciaio superduplex, leghe di alluminio marine-grade e leghe di rame nichel- alluminio. La combinazione di queste leghe con opportuni trattamenti termici e di superficie può garantire la massima durata e affidabilità delle strutture metalliche esposte a un ambiente marino corrosivo, riducendo significativamente i costi di manutenzione e sostituzione nel tempo.
Tecnologie Avanzate di Saldatura
Quando si tratta di progettazione avanzata di giunti saldati per strutture metalliche in ambiente marino corrosivo, è essenziale considerare le tecnologie avanzate di saldatura. La ricerca condotta dall’UNIVERSItà€ DI PISA fornisce importanti contributi nel campo delle tecnologie di saldatura adatte agli ambienti marini corrosivi. Per ulteriori informazioni, è possibile consultare il documento ufficiale qui.
Saldatura ad arco immerso (SAW) e sue applicazioni marine
La saldatura ad arco immerso (SAW) rappresenta una tecnologia consolidata per la realizzazione di giunti saldati in ambiente marino corrosivo. Grazie alla protezione fornita dallo strato di materiale inerte, la SAW è particolarmente adatta per applicazioni marine come piattaforme offshore, strutture portuali e navi.
Saldatura ad arco con elettrodo rivestito (SMAW) in ambiente marino
La saldatura ad arco con elettrodo rivestito (SMAW) è un’altra tecnica ampiamente utilizzata per la realizzazione di giunti saldati in ambiente marino. Grazie alla flessibilità e alla capacità di adattarsi a condizioni ambientali difficili, la SMAW è un’opzione affidabile per progetti di strutture metalliche esposte all’ambiente marino.
Alcune delle parole chiave correlate a questa sezione includono: saldatura ad arco, elettrodo rivestito, ambiente marino, corrosione, strutture metalliche.
Innovazioni nella saldatura MIG e TIG per ambienti corrosivi
Le innovazioni nella saldatura MIG e TIG stanno rivoluzionando l’approccio alla realizzazione di giunti saldati in ambienti corrosivi come quelli marini. Grazie all’utilizzo di gas di protezione adatti alle condizioni marine e all’impiego di metalli di apporto speciali, la saldatura MIG e TIG sta dimostrando prestazioni elevate anche in ambienti estremamente corrosivi.
Alcune delle parole chiave correlate a questa sezione includono: saldatura MIG, saldatura TIG, ambienti corrosivi, gas di protezione, metalli di apporto.
Saldatura Friction Stir Welding (FSW) per giunti in leghe leggere
Il processo di saldatura Friction Stir Welding (FSW) si è dimostrato particolarmente efficace per la realizzazione di giunti in leghe leggere, ideali per applicazioni marine in cui la leggerezza e la resistenza alla corrosione sono fondamentali. L’impiego del FSW in progetti di strutture metalliche in ambiente marino è una soluzione altamente affidabile e tecnologicamente avanzata.
Alcune delle parole chiave correlate a questa sezione includono: Friction Stir Welding, leghe leggere, resistenza alla corrosione, applicazioni marine.
Metodi di saldatura automatizzati e robotizzati
I metodi di saldatura automatizzati e robotizzati stanno guadagnando sempre più terreno nel campo della costruzione di strutture metalliche in ambienti marini corrosivi. L’impiego di robot e sistemi automatizzati permette di garantire elevata precisione e ripetibilità nella realizzazione di giunti saldati, riducendo al minimo gli errori umani e garantendo standard qualitativi elevati.
Alcune delle parole chiave correlate a questa sezione includono: saldatura automatizzata, saldatura robotizzata, precisione, ripetibilità, standard qualitativi.
Analisi dei Giunti Saldati Sottoposti a Corrosione
La corrosione rappresenta uno dei principali fattori di degrado per i giunti saldati delle strutture metalliche in ambiente marino. L’analisi dei giunti saldati sottoposti a corrosione è di fondamentale importanza per garantire la sicurezza e l’affidabilità delle strutture esposte a questo tipo di ambiente aggressivo.
Meccanismi di degrado e tipi di corrosione
I meccanismi di degrado dei giunti saldati in ambiente marino possono essere attribuiti a fenomeni di corrosione come la corrosione uniforme, la corrosione galvanica, la corrosione da solfuri e la corrosione da cloruri. Questi meccanismi possono compromettere l’integrità strutturale dei giunti saldati, riducendone la resistenza e la durabilità nel tempo.
Tecniche di analisi e test per valutare l’integrità dei giunti
Per valutare l’integrità dei giunti saldati sottoposti a corrosione, vengono impiegate varie tecniche di analisi non distruttive e test di laboratorio. Tra queste tecniche rientrano l’utilizzo di ultrasonografia, radiografia, elettrochimica e prove di trazione, al fine di valutare lo stato di corrosione e la resistenza residua dei giunti saldati.
Queste tecniche permettono di identificare e monitorare il grado di degrado dei giunti saldati, consentendo di implementare interventi di manutenzione e riparazione nel rispetto della sicurezza e conformità alle normative vigenti.
Per monitorare nell’arco del tempo l’integrità strutturale dei giunti saldati, è essenziale adottare sistemi di monitoraggio continuo in situ e nuove tecnologie di sensori per rilevare rapidamente l’evoluzione della corrosione e il comportamento dei giunti saldati in ambiente marino. Il monitoraggio dell’integrità strutturale nel tempo consente di prevenire il degrado avanzato e adottare tempestivamente azioni correttive per garantire la sicurezza e la durabilità delle strutture metalliche esposte a condizioni corrosive.
Protezione dalla Corrosione e Trattamenti Superficiali
La protezione dalla corrosione è una delle sfide principali nella progettazione di giunti saldati per strutture metalliche in ambiente marino corrosivo. I trattamenti superficiali giocano un ruolo fondamentale nel garantire la durabilità e l’affidabilità delle strutture esposte a condizioni ambientali estreme.
Trattamenti preventivi e rivestimenti
I trattamenti preventivi e i rivestimenti anticorrosione sono fondamentali per proteggere le superfici metalliche esposte all’ambiente marino. È essenziale scegliere i giusti rivestimenti in base alle specifiche condizioni di corrosione e alle proprietà del materiale, garantendo una protezione efficace e duratura nel tempo.
Soluzioni di protezione catodica
Le soluzioni di protezione catodica offrono un’efficace difesa contro la corrosione per le strutture metalliche in ambiente marino. Attraverso l’utilizzo di anodi sacrificiali o corrente impressa, è possibile controllare attivamente il processo di corrosione, prolungando significativamente la vita utile delle strutture esposte.
La protezione catodica è particolarmente vantaggiosa in presenza di giunti saldati, dove è fondamentale prevenire la formazione di corrosione galvanica e garantire un’elevata resistenza nel tempo.
Manutenzione e riparazione dei giunti saldati in ambiente corrosivo
La corretta manutenzione e riparazione dei giunti saldati in ambiente corrosivo sono cruciali per assicurare la durabilità e l’integrità strutturale nel tempo. È indispensabile monitorare costantemente lo stato dei giunti saldati, eseguire interventi tempestivi di manutenzione e riparazione, utilizzando tecniche e materiali appropriati per garantire la massima efficienza e sicurezza delle strutture metalliche esposte a condizioni ambientali marine corrosive.
Modellazione e Simulazione
La modellazione e la simulazione sono strumenti fondamentali nella progettazione avanzata di giunti saldati per strutture metalliche in ambiente marino corrosivo. Per approfondire questo argomento, ti consiglio di leggere il documento 5: UNIONI SALDATE – parte 1.
Modelli computazionali per la progettazione di giunti
I modelli computazionali consentono di valutare le sollecitazioni e le deformazioni nelle strutture metalliche, fornendo preziose informazioni per progettare giunti saldati affidabili e duraturi in ambienti marini corrosivi.
Simulazioni di ambiente marino e comportamento a lungo termine
Le simulazioni di ambiente marino consentono di valutare il comportamento a lungo termine delle strutture metalliche esposte a condizioni corrosive, fornendo indicazioni cruciali per la progettazione di giunti saldati duraturi e sicuri nel tempo.
Per ulteriori informazioni sulle simulazioni di ambiente marino e il comportamento a lungo termine delle strutture metalliche, ti consiglio di approfondire questo argomento nel contesto della progettazione avanzata di giunti saldati per strutture metalliche in ambiente marino corrosivo.
Analisi di fatica e durabilità dei giunti saldati
L’analisi di fatica e durabilità dei giunti saldati è essenziale per valutare la resistenza delle strutture metalliche esposte a sollecitazioni cicliche in ambiente marino corrosivo, garantendo la sicurezza e l’affidabilità delle strutture nel tempo.
Approfondire l’analisi di fatica e durabilità dei giunti saldati è fondamentale per la progettazione avanzata di strutture metalliche in ambiente marino corrosivo, assicurando la durabilità e l’integrità strutturale nel lungo termine.
Normative e Standard
La progettazione di giunti saldati per strutture metalliche in ambiente marino corrosivo deve essere conforme a rigide normative e standard internazionali, al fine di garantire la sicurezza e l’affidabilità delle costruzioni esposte a condizioni ambientali estreme.
Codici internazionali e linee guida per la saldatura in ambiente marino
I principali codici internazionali per la saldatura in ambiente marino includono la normativa ISO 12944 per la protezione dalle corrosioni atmosferiche e sottomarine, nonché le linee guida dell’AWS (American Welding Society) e dell’EN (European Norm) che definiscono i requisiti per la qualificazione del personale addetto alla saldatura e per la procedura di saldatura stessa, specificamente per l’ambiente marino.
Processi di certificazione e controllo qualità dei giunti saldati
I giunti saldati per strutture metalliche in ambiente marino devono essere sottoposti a processi di certificazione e controllo qualità rigorosi, conformi alle normative e standard internazionali come la ISO 3834 e la ISO 15614. Questi processi garantiscono l’integrità strutturale e la resistenza alla corrosione dei giunti saldati, attraverso controlli non distruttivi e prove di laboratorio.
Per garantire la conformità dei giunti saldati alle normative e standard internazionali, è fondamentale seguire con precisione i processi di certificazione e controllo qualità, avvalendosi di personale qualificato e di attrezzature all’avanguardia per verificare la conformità dei giunti saldati agli standard richiesti.
Futuri sviluppi nella normativa e impatti sulla progettazione
I futuri sviluppi nella normativa relativa alla saldatura in ambiente marino potrebbero influenzare significativamente la progettazione dei giunti saldati per le strutture metalliche, con nuove linee guida e standard che potrebbero essere introdotti per affrontare sfide emergenti legate alla corrosione e alla resistenza degli materiali esposti a condizioni marine estreme.
Per rimanere all’avanguardia e garantire la conformità alle future normative e standard, è essenziale tenersi costantemente aggiornati sulle evoluzioni del settore e adottare le migliori pratiche e tecnologie disponibili per la progettazione e la realizzazione di giunti saldati per strutture metalliche in ambiente marino corrosivo.
Case Study e Applicazioni Pratiche
Per comprendere appieno l’importanza della progettazione avanzata di giunti saldati per strutture metalliche in ambiente marino corrosivo, è utile esaminare alcuni casi di studio e applicazioni pratiche. Un interessante punto di partenza è rappresentato dal documento del 60° anno di pubblicazione (1948-2008) disponibile qui.
Progettazione di giunti saldati per piattaforme petrolifere
La progettazione di giunti saldati per piattaforme petrolifere richiede un’approccio altamente specializzato, data l’esposizione costante ai fattori corrosivi presenti nell’ambiente marino. Attraverso un’attenta analisi delle sollecitazioni e l’impiego di materiali e metodologie specifiche, è possibile garantire la massima affidabilità e resistenza nel tempo di tali giunti, contribuendo così alla sicurezza e al successo operativo delle piattaforme.
Soluzioni innovative per l’industria navale e della costruzione offshore
Nel contesto dell’industria navale e della costruzione offshore, l’adozione di soluzioni innovative per la progettazione dei giunti saldati riveste un ruolo cruciale. Dall’impiego di materiali avanzati alla ricerca di nuove tecniche di saldatura, l’obiettivo è quello di ottenere giunti altamente performanti e duraturi, in grado di resistere alle condizioni più estreme e alle sfide imposte dall’ambiente marino.
Per ulteriori dettagli sulle soluzioni innovative per l’industria navale e la costruzione offshore, si rimanda all’articolo completo disponibile sul nostro sito web, in cui approfondiremo alcuni casi di studio di particolare rilevanza.
Studi di successo e approfondimenti critici
Gli studi di successo e gli approfondimenti critici nel campo della progettazione avanzata di giunti saldati per ambienti marini corrosivi forniscono preziose informazioni per il miglioramento continuo delle pratiche e delle tecnologie utilizzate in questo settore. Attraverso l’analisi dei successi ottenuti e dei problemi riscontrati, è possibile trarre preziose lezioni e spunti per futuri sviluppi e innovazioni.
Per approfondire ulteriormente gli studi di successo e gli approfondimenti critici, è possibile consultare la sezione dedicata sul nostro sito web, in cui verranno esaminati alcuni casi specifici e le relative implicazioni per l’industria delle costruzioni off-shore e navale.
Conclusioni
In conclusione, la progettazione avanzata di giunti saldati per strutture metalliche in ambiente marino corrosivo è di fondamentale importanza per garantire la sicurezza e l’affidabilità delle strutture esposte a condizioni ambientali avverse. Attraverso l’analisi dei diversi fattori che influenzano la corrosione e il deterioramento dei giunti saldati, è possibile sviluppare soluzioni innovative e sostenibili per migliorare la resistenza e la durata di tali strutture.
È di vitale importanza considerare non solo i materiali utilizzati, ma anche i processi di saldatura e le tecniche di protezione anti-corrosione, al fine di garantire prestazioni ottimali nel lungo termine. Inoltre, è fondamentale condurre regolari ispezioni e manutenzione per monitorare lo stato dei giunti saldati e intervenire tempestivamente in caso di segni di deterioramento.
In definitiva, investire in progettazione avanzata e manutenzione costante delle strutture metalliche in ambiente marino corrosivo è essenziale per garantire la sicurezza delle infrastrutture e preservare l’integrità delle stesse nel tempo.
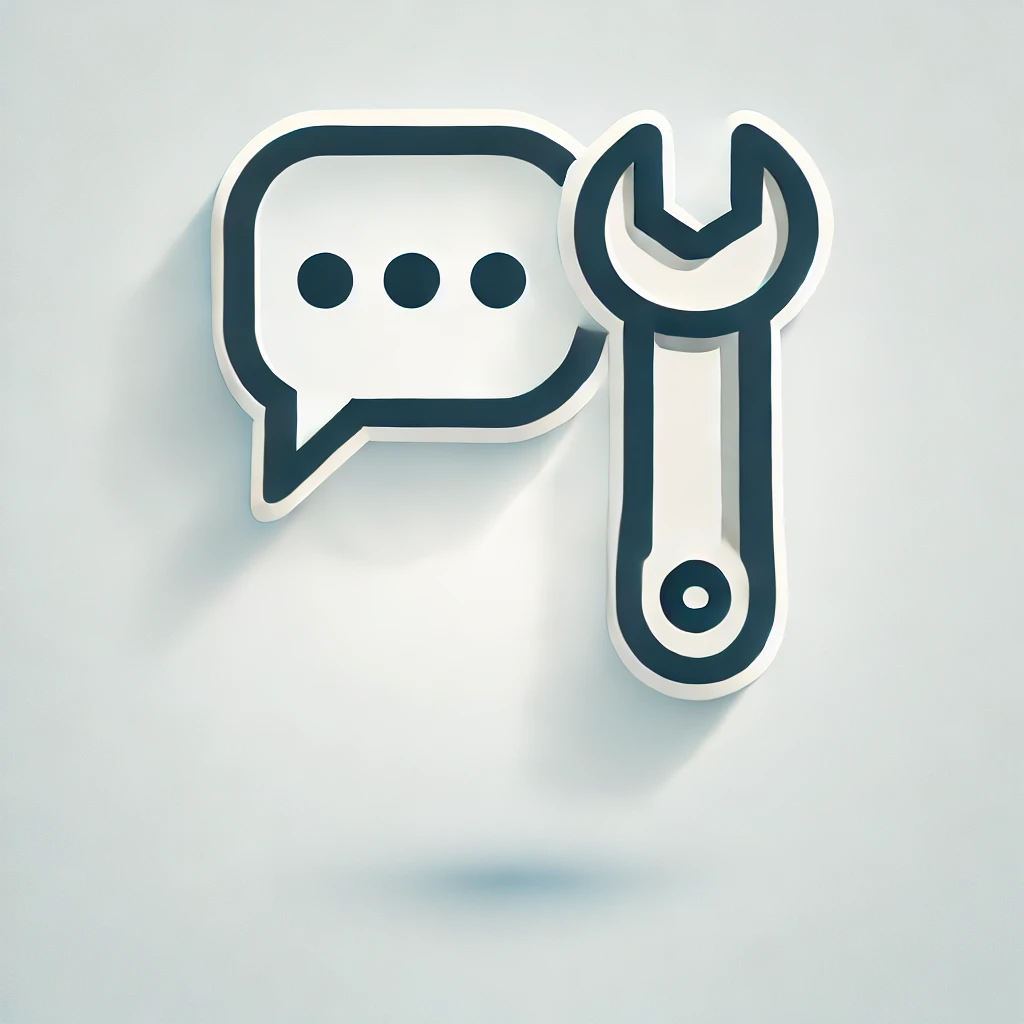
"Hai un'opinione tecnica o una domanda specifica? Non esitare, lascia un commento! La tua esperienza può arricchire la discussione e aiutare altri professionisti a trovare soluzioni. Condividi il tuo punto di vista!"