Tecniche di Progettazione per Carpenteria Metallica in Piattaforme Offshore

Tecniche di Progettazione per Carpenteria Metallica in Piattaforme Offshore
Nell’industria delle piattaforme offshore, la progettazione e costruzione di carpenteria metallica svolgono un ruolo fondamentale per garantire la sicurezza e l’efficienza delle installazioni. Con l’obiettivo di superare i tradizionali metodi di progettazione e costruzione, le tecniche di progettazione per la carpenteria metallica in piattaforme offshore sono state oggetto di intensa ricerca e sviluppo. In questo articolo, esploreremo in maniera analitica le principali tecniche di progettazione utilizzate per garantire la durata e l’affidabilità delle strutture metalliche offshore, fornendo una prospettiva professionale sull’argomento.
Indice dei contenuti
- Introduzione alla progettazione di carpenteria metallica nelle piattaforme offshore
- Requisiti di sicurezza e normative per la progettazione di carpenteria metallica nelle piattaforme offshore
- Scelta dei materiali e analisi delle prestazioni strutturali per la carpenteria metallica nelle piattaforme offshore
- Tecniche avanzate di progettazione per la carpenteria metallica nelle piattaforme offshore
- Analisi del carico e delle sollecitazioni per una progettazione precisa di carpenteria metallica nelle piattaforme offshore
- Considerazioni sulla costruzione e l’installazione della carpenteria metallica nelle piattaforme offshore
- Minimizzare i rischi di corrosione nella progettazione di carpenteria metallica nelle piattaforme offshore
- Domande e risposte
- Per concludere
Introduzione alla progettazione di carpenteria metallica nelle piattaforme offshore
La progettazione di carpenteria metallica nelle piattaforme offshore è un processo complesso che richiede un’attenta analisi e una precisa valutazione di numerosi fattori. Questo tipo di carpenteria, spesso utilizzata per la costruzione di strutture marittime, richiede una particolare attenzione per garantire la sicurezza e la stabilità delle piattaforme.I principali obiettivi della progettazione di carpenteria metallica nelle piattaforme offshore sono la resistenza strutturale, la durata nel tempo e la capacità di sopportare le sollecitazioni ambientali. Questi fattori consentono di garantire la sicurezza delle strutture e il corretto funzionamento delle piattaforme offshore.Durante la progettazione, è fondamentale prendere in considerazione le condizioni ambientali in cui la piattaforma sarà collocata. Le onde, le correnti marine e il vento possono influenzare la stabilità delle strutture e devono essere accuratamente calcolati. È importante prevedere anche eventuali fenomeni estremi, come uragani o forti maree, per garantire la resistenza delle piattaforme in tutte le condizioni.La scelta dei materiali è un aspetto cruciale nella progettazione di carpenteria metallica nelle piattaforme offshore. È necessario selezionare materiali che siano resistenti alla corrosione e agli agenti atmosferici, come l’acciaio inossidabile o l’alluminio marino. Inoltre, la scelta delle giunzioni e delle connessioni tra le diverse componenti della carpenteria deve garantire la resistenza e la durabilità delle strutture.Durante la progettazione è fondamentale valutare anche la sicurezza degli operatori che lavoreranno sulla piattaforma. Le normative internazionali in materia di sicurezza sul lavoro devono essere rigorosamente rispettate, al fine di prevenire incidenti e garantire un ambiente di lavoro sicuro.Un altro aspetto importante nella progettazione di carpenteria metallica nelle piattaforme offshore è l’accessibilità per la manutenzione e la riparazione delle strutture. È fondamentale progettare la carpenteria in modo tale da permettere l’ispezione e la manutenzione agevole e sicura, evitando così costosi interventi di riparazione o sostituzione.La progettazione di carpenteria metallica nelle piattaforme offshore richiede inoltre una stretta collaborazione tra diverse figure professionali, come ingegneri strutturali, ingegneri meccanici e tecnici specializzati. Solo attraverso una solida e coesa collaborazione è possibile ottenere risultati di elevata qualità e garantire la sicurezza delle piattaforme offshore.Infine, è importante sottolineare che la progettazione di carpenteria metallica nelle piattaforme offshore è un processo in continua evoluzione. Le nuove tecnologie e i progressi nell’ingegneria dei materiali offrono costantemente nuove opportunità per migliorare la sicurezza e l’efficienza delle piattaforme offshore.
Requisiti di sicurezza e normative per la progettazione di carpenteria metallica nelle piattaforme offshore
La progettazione e la costruzione di carpenteria metallica per le piattaforme offshore richiedono il rispetto di requisiti di sicurezza molto rigorosi e di normative specifiche. Questi requisiti e normative sono stati stabiliti per garantire la protezione della vita umana, dell’ambiente marino e per assicurare il corretto funzionamento delle strutture offshore.
Uno dei principali requisiti di sicurezza richiesti per la progettazione di carpenteria metallica offshore riguarda la resistenza strutturale dei componenti. Le strutture devono essere in grado di sopportare le sollecitazioni statiche e dinamiche a cui possono essere sottoposte in condizioni di mare agitato, tempeste o uragani. Gli ingegneri devono calcolare con precisione il carico massimo che la struttura può sopportare per evitare danni agli elementi portanti o collassi strutturali.
Un altro requisito fondamentale è l’affidabilità dell’impianto di carpenteria metallica offshore. Le strutture devono essere progettate in modo tale da evitare potenziali guasti che potrebbero mettere a rischio la sicurezza degli operatori o l’integrità dell’ambiente marino circostante. Inoltre, devono essere previste procedure di manutenzione periodica per garantire che la struttura rimanga affidabile nel tempo.
La protezione antincendio è un aspetto di estrema importanza nella progettazione di carpenteria metallica offshore. Le strutture devono essere progettate in modo da limitare la propagazione di incendi e prevenire l’emissione di gas tossici. Sistemi di rilevazione precoce e spegnimento automatico degli incendi devono essere installati e adeguatamente dimensionati per garantire una risposta rapida ed efficace in caso di emergenza.
La sicurezza degli operatori è garantita mediante l’adozione di procedure di accesso sicuro alle strutture di carpenteria metallica. Scale, passerelle e sistemi di protezione anticaduta devono essere progettati e installati secondo specifiche precise per ridurre al minimo i rischi legati alle cadute dall’alto. Inoltre, è necessaria la presenza di attrezzature di salvataggio e di evacuazione adeguatamente dimensionate e posizionate in caso di emergenza.
Le normative ambientali sono un altro aspetto di fondamentale importanza nella progettazione di carpenteria metallica offshore. Le strutture devono essere progettate in modo da limitare l’impatto ambientale e prevenire la dispersione di sostanze inquinanti nell’ambiente marino circostante. Sistemi di raccolta e trattamento delle acque reflue e di gestione dei rifiuti devono essere implementati secondo le normative vigenti.
Un aspetto critico nella progettazione di carpenteria metallica è l’utilizzo di materiali resistenti alla corrosione. Gli elementi strutturali devono essere realizzati in materiali che possono resistere all’ambiente marino aggressivo senza compromettere la loro integrità strutturale. La protezione anticorrosiva tramite rivestimenti, come l’applicazione di vernici o galvanizzazione a caldo, deve essere applicata in modo adeguato e conforme alle normative specifiche.
Infine, la progettazione di carpenteria metallica offshore deve prevedere la valutazione del rischio sismico. Le strutture devono essere progettate per resistere a terremoti o scosse sismiche, che possono rappresentare una minaccia per la sicurezza degli operatori e la stabilità delle piattaforme offshore. Gli ingegneri devono considerare attentamente le specifiche sismiche della zona di installazione e assicurare che la struttura sia in grado di resistere alle sollecitazioni sismiche previste.
Scelta dei materiali e analisi delle prestazioni strutturali per la carpenteria metallica nelle piattaforme offshore
Materiali per la carpenteria metallica nelle piattaforme offshore:
Nell’ambito delle piattaforme offshore, la scelta dei materiali gioca un ruolo cruciale per garantire la massima prestazione strutturale e la sicurezza dell’intero sistema. I materiali utilizzati devono soddisfare requisiti specifici di resistenza, durabilità e resistenza alla corrosione, al fine di affrontare le condizioni ambientali impegnative in cui opera una piattaforma offshore. Di seguito, analizzeremo i principali materiali utilizzati e le relative prestazioni strutturali.
Acciaio resistente alla corrosione atmosferica (Acciaio Corten):
L’acciaio Corten, noto anche come acciaio resistente alla corrosione atmosferica, è una scelta comune per le strutture metalliche nelle piattaforme offshore. Le sue proprietà chimiche lo rendono altamente resistente alla corrosione, alle variazioni di temperatura e agli agenti atmosferici, permettendo una maggiore durata nel tempo. L’acciaio Corten è particolarmente adatto per componenti strutturali come le travi, le piastre e le colonne che devono sostenere carichi pesanti.
Alluminio:
L’alluminio è un altro materiale di grande rilevanza per la carpenteria metallica offshore. La sua leggerezza combinata con una buona resistenza alla corrosione offre numerosi vantaggi, come la riduzione del peso complessivo delle strutture e una maggiore facilità di trasporto e installazione. È comunemente utilizzato per strutture di supporto e rivestimenti esterni. Tuttavia, va considerato che l’alluminio può essere soggetto a una maggiore usura e degrado rispetto all’acciaio.
Materiali compositi:
L’utilizzo di materiali compositi nella carpenteria metallica offshore è diventato sempre più diffuso negli ultimi anni. Questi materiali, come la fibra di vetro e la fibra di carbonio, offrono un’elevata resistenza alla corrosione, unita ad una straordinaria leggerezza. I compositi sono particolarmente adatti per la fabbricazione di elementi strutturali complessi, come piloni e tralicci, dove la leggerezza è essenziale per ridurre le sollecitazioni sulle fondamenta.
Verifiche strutturali:
Prima dell’installazione delle strutture metalliche, è fondamentale condurre un’analisi delle prestazioni strutturali per garantire la loro stabilità e sicurezza. Queste analisi includono prove di carico, simulazioni computerizzate e valutazioni statiche e dinamiche. Solo attraverso tali verifiche è possibile garantire che le strutture metalliche siano in grado di resistere alle sollecitazioni meccaniche, agli eventi atmosferici estremi e alle condizioni marine impervie.
Fabbricazione e installazione:
La fabbricazione e l’installazione delle strutture metalliche nelle piattaforme offshore richiedono un elevato grado di precisione e accuratezza. Le lavorazioni devono essere eseguite secondo specifiche tecniche rigorose e le saldature devono essere eseguite da personale altamente qualificato. Inoltre, l’installazione delle strutture richiede il rispetto di metodi e procedure di sicurezza rigorosi per garantire un’operazione senza intoppi e la conformità agli standard di salute e sicurezza.
Mantenimento e protezione:
Una volta installate, le strutture metalliche nelle piattaforme offshore richiedono un adeguato mantenimento e protezione per preservarne le prestazioni strutturali nel tempo. Questo include l’applicazione di rivestimenti protettivi, la gestione della corrosione e l’ispezione periodica dell’integrità strutturale. Un adeguato piano di manutenzione preventiva è essenziale per garantire che le strutture mantengano la loro resistenza e affidabilità nel corso degli anni.
Conclusioni:
In conclusione, la scelta dei materiali e l’analisi delle prestazioni strutturali per la carpenteria metallica nelle piattaforme offshore sono fondamentali per garantire la resistenza, la durabilità e la sicur ezza dell’intero sistema. L’utilizzo degli acciai resistenti alla corrosione atmosferica, dell’alluminio e dei materiali compositi offre soluzioni efficaci per affrontare le sfide ambientali presenti in mare aperto. Tuttavia, è indispensabile effettuare verifiche strutturali accurate prima dell’installazione e implementare piani di manutenzione e protezione per preservare le prestazioni delle strutture nel tempo.
Tecniche avanzate di progettazione per la carpenteria metallica nelle piattaforme offshore
La progettazione delle piattaforme offshore richiede l’impiego di tecniche avanzate per garantire la sicurezza strutturale e la resistenza alle condizioni estreme presenti in mare aperto. La carpenteria metallica gioca un ruolo fondamentale in questo ambito, insieme ai materiali e alle metodologie di costruzione utilizzate.
Una delle tecniche più importanti è l’utilizzo di analisi agli elementi finiti (FEA) per valutare il comportamento strutturale delle componenti metalliche. Questo approccio consente di simulare il carico e le sollecitazioni che la piattaforma dovrà affrontare durante la sua vita operativa, consentendo di identificare potenziali punti critici e di ottimizzare il design.
L’adozione di giunzioni saldate ad alta resistenza è un’altra tecnica avanzata che migliora la performance strutturale delle piattaforme offshore. Queste giunzioni garantiscono una maggiore durata e resistenza alla fatica, riducendo al minimo la possibilità di cedimenti o rotture premature.
È anche importante considerare l’utilizzo di acciai ad alta resistenza nella carpenteria metallica. Questi materiali offrono una maggiore resistenza meccanica, permettendo di ridurre le dimensioni delle componenti e di conseguenza il peso complessivo della piattaforma. Ciò non solo riduce i costi di costruzione, ma facilita anche l’installazione e il trasporto offshore.
Al fine di garantire un’adeguata protezione anticorrosione delle strutture metalliche, è fondamentale l’applicazione di rivestimenti e trattamenti superficiali di qualità. Questi includono vernici e rivestimenti specializzati, che proteggono le componenti dall’azione corrosiva dell’acqua di mare e dagli agenti atmosferici. Un adeguato sistema di protezione anticorrosione può notevolmente estendere la durata operativa della piattaforma.
I sistemi di ancoraggio e di fissaggio rappresentano una componente critica nelle piattaforme offshore. L’utilizzo di tecnologie avanzate, come ad esempio l’impiego di bulloni di ancoraggio ad alta resistenza, garantisce un collegamento stabile e sicuro tra le varie strutture della piattaforma. Questo è particolarmente importante in caso di eventi sismici o condizioni meteo avverse che richiedono la massima sicurezza strutturale.
Una corretta progettazione degli elementi di connessione, come le staffe e i supporti strutturali, è anch’essa fondamentale per garantire l’integrità e la resistenza della carpenteria metallica. L’utilizzo di tecnologie avanzate, come la modellazione e l’analisi tridimensionale, consente una progettazione accurata e una verifica preliminare dell’affidabilità delle connessioni, riducendo il rischio di cedimenti strutturali.
Infine, l’adozione di tecniche innovative di costruzione e assemblaggio, come l’utilizzo di sistemi prefabbricati e il posizionamento modulare delle componenti, consente di ridurre i tempi e i costi di costruzione delle piattaforme offshore. Questi approcci consentono anche una maggiore precisione e un migliore controllo di qualità nella fase di assemblaggio, garantendo la conformità agli standard più elevati in termini di sicurezza e funzionalità.
Analisi del carico e delle sollecitazioni per una progettazione precisa di carpenteria metallica nelle piattaforme offshore
Tempi duri per l’industria petrolifera e del gas, ma la domanda di piattaforme offshore non accenna a diminuire. Per questo motivo, è fondamentale progettare in modo preciso le strutture di carpenteria metallica che sostengono queste installazioni.
L’analisi del carico e delle sollecitazioni è un processo cruciale per garantire la sicurezza e l’affidabilità delle piattaforme offshore. Durante questa fase, vengono valutati diversi fattori che possono influenzare la resistenza strutturale, come il vento, le onde, le correnti marine e persino le temperature estreme.
Attraverso l’impiego di sofisticate tecnologie di modellazione e simulazione, è possibile valutare le sollecitazioni a cui la carpenteria metallica sarà sottoposta nel corso della vita operativa della piattaforma. Ciò permette di identificare e mitigare i punti critici alle sollecitazioni, riducendo il rischio di cedimenti strutturali.
Un’attenta analisi del carico aiuta anche a ottimizzare il design della carpenteria metallica, trovando un equilibrio tra resistenza e leggerezza. Questo permette di ridurre i costi di produzione e di installazione, senza compromettere l’integrità strutturale.
L’analisi del carico non riguarda solo la resistenza strutturale, ma anche la sicurezza degli operatori a bordo delle piattaforme offshore. Ogni sollecitazione viene valutata per garantire che gli elementi strutturali non superino i loro limiti di carico, evitando così incidenti e situazioni di pericolo.
Inoltre, l’analisi del carico permette di prevedere i possibili effetti della corrosione e dell’invecchiamento sulle strutture di carpenteria metallica, consentendo una manutenzione preventiva e una prolungata vita operativa delle piattaforme offshore.
La progettazione precisa di carpenteria metallica nelle piattaforme offshore richiede una conoscenza approfondita delle normative tecniche specifiche del settore. Le strutture devono essere conformi ai requisiti di sicurezza internazionali e nazionali per garantire la conformità normativa e minimizzare i rischi.
Infine, l’analisi del carico permette di ottenere le informazioni necessarie per la corretta selezione dei materiali e delle tecniche di fabbricazione. La scelta di materiali resistenti e di alta qualità è fondamentale per garantire la durabilità e l’affidabilità delle strutture di carpenteria metallica.
Considerazioni sulla costruzione e l’installazione della carpenteria metallica nelle piattaforme offshore
La costruzione e l’installazione della carpenteria metallica nelle piattaforme offshore richiedono un’attenta pianificazione e un’eccellente conoscenza delle condizioni ambientali e tecniche che saranno affrontate durante il processo. Ecco alcune considerazioni da tenere a mente durante questo complesso processo.
1. Analisi delle condizioni ambientali: Prima di iniziare la costruzione, è essenziale condurre un’approfondita analisi delle condizioni ambientali in cui la piattaforma offshore sarà posizionata. Questo include lo studio delle maree, delle correnti e delle condizioni meteorologiche per assicurarsi che la carpenteria metallica sia in grado di resistere a sollecitazioni quali ondate e venti intensi.
2. Pianificazione della progettazione: La progettazione della carpenteria metallica deve essere accuratamente pianificata per garantire una struttura solida e sicura. Le considerazioni dovrebbero includere la resistenza alla corrosione, la distribuzione del carico e la resistenza alle sollecitazioni sismiche, assicurando che la struttura sia in grado di sopportare anche le condizioni più estreme.
3. Selezione dei materiali: La scelta dei materiali giusti è fondamentale per garantire l’affidabilità e la durata della carpenteria metallica. L’acciaio inossidabile e leghe speciali sono spesso preferiti per le loro proprietà anticorrosive e di resistenza. È importante collaborare con fornitori affidabili e qualificati per ottenere materiali di alta qualità.
4. Monitoraggio e manutenzione: Durante l’intero ciclo di vita della piattaforma, è essenziale monitorare regolarmente lo stato della carpenteria metallica e pianificare adeguatamente la sua manutenzione. L’ispezione costante delle saldature, la pulizia e la protezione anticorrosiva sono solo alcune delle attività che devono essere svolte per garantire la sicurezza e la durata della struttura.
5. Assemblaggio in cantiere: L’assemblaggio della carpenteria metallica in cantiere richiede personale qualificato e attrezzature specializzate. È fondamentale seguire rigorosamente le specifiche di progettazione e i protocolli di sicurezza durante l’assemblaggio per garantire una costruzione accurata e ridurre il rischio di incidenti.
6. Trasporto e installazione: L’installazione della carpenteria metallica sul sito di lavoro offshore è una fase critica del processo. È necessario coordinare attentamente il trasporto e l’installazione della struttura utilizzando navi e gru specializzate. Una pianificazione accurata e una gestione efficiente delle risorse sono fondamentali per garantire un’installazione senza intoppi e sicura.
7. Test e certificazione: Prima dell’entrata in servizio, la carpenteria metallica deve essere sottoposta a test approfonditi per garantire la sua conformità alle normative e alle specifiche di progettazione. Certificazioni rilasciate da enti indipendenti confermano la conformità e la sicurezza della struttura.
8. Considerazioni sull’impatto ambientale: Durante l’intero processo di costruzione e installazione, è cruciale considerare e mitigare gli effetti ambientali. L’utilizzo di tecnologie eco-sostenibili, il rispetto delle normative ambientali e la gestione corretta dei rifiuti sono solo alcune delle pratiche che devono essere adottate per minimizzare l’impatto negativo sull’ecosistema circostante.
Minimizzare i rischi di corrosione nella progettazione di carpenteria metallica nelle piattaforme offshore
La scelta dei materiali giusti è fondamentale per minimizzare i rischi di corrosione. Dedicare attenzione alla selezione di acciai resistenti alla corrosione, come l’acciaio inossidabile o ad alto contenuto di cromo, può ridurre significativamente l’effetto degli agenti corrosivi presenti nell’ambiente marino. La resistenza ai prodotti chimici, alla ruggine e alla corrosione galvanica sono caratteristiche da considerare nella scelta dei materiali di carpenteria metallica. Un’altra strategia efficace per minimizzare i rischi di corrosione è l’implementazione di un sistema di protezione catodica. Questo metodo prevede l’utilizzo di materiali sacrificabili o un approccio basato sull’imposizione di un potenziale elettrico per proteggere la struttura metallica dalle reazioni elettrochimiche che provocano la corrosione. L’applicazione di rivestimenti protettivi è una prassi comune per ridurre l’impatto della corrosione sulla carpenteria metallica offshore. La scelta del tipo di rivestimento dipende dalle condizioni ambientali e richiede un’attenta valutazione degli agenti corrosivi presenti. Rivestimenti come l’epossido, il poliuretano o il zincato a caldo possono fornire una barriera protettiva efficace contro gli agenti corrosivi. Una corretta manutenzione è essenziale per assicurarsi che le misure preventive messe in atto per minimizzare i rischi di corrosione siano efficaci nel tempo. Ispezioni periodiche, pulizia, riparazione di danni ai rivestimenti e il monitoraggio delle condizioni di corrosione sono attività chiave per garantire la durata della struttura di carpenteria metallica offshore. Uno di sign ben studiato può contribuire notevolmente a ridurre i rischi di corrosione. La considerazione di elementi come la corretta drenatura dell’acqua, la prevenzione dei punti stagnanti e dei depositi di agenti chimici corrosivi può aiutare a minimizzare le opportunità per la corrosione di insediarsi e progredire sulla superficie della carpenteria metallica. Il monitoraggio continuo delle condizioni di corrosione è fondamentale per identificare in modo tempestivo eventuali anomalie o segni di deterioramento. L’utilizzo di tecnologie avanzate, come i sensori di corrosione o le ispezioni tramite droni, può fornire dati preziosi per prendere decisioni informative sulle attività di manutenzione e sulle eventuali azioni correttive da intraprendere. Un fattore critico nella prevenzione della corrosione è l’adeguata formazione del personale coinvolto nella progettazione, costruzione e manutenzione delle piattaforme offshore. Un personale consapevole dei rischi della corrosione e delle strategie preventive può contribuire attivamente a minimizzare l’impatto della corrosione sulle strutture di carpenteria metallica in mare. L’innovazione tecnologica continua a offrire nuove soluzioni per la prevenzione e il controllo della corrosione. Lo sviluppo di nuovi materiali, rivestimenti avanzati, metodologie di monitoraggio più precise e sistemi di protezione catodica sempre più efficienti giocano un ruolo fondamentale nel migliorare la durabilità delle piattaforme offshore.1. Scelta dei materiali adatti
2. Protezione catodica
3. Rivestimenti protettivi
4. Manutenzione regolare
5. Design attento
6. Monitoraggio costante
7. Formazione e consapevolezza del personale
8. Innovazione tecnologica
Domande e risposte
Domanda: Quali sono le principali tecniche di progettazione utilizzate per la carpenteria metallica nelle piattaforme offshore?Risposta: Nella progettazione della carpenteria metallica per le piattaforme offshore vengono impiegate diverse tecniche, tra cui l’analisi strutturale avanzata, la progettazione mediante software di modellazione tridimensionale e l’utilizzo di criteri di normativa specifici per l’ambiente marino.Domanda: Quali sono i vantaggi dell’utilizzo di un’analisi strutturale avanzata nella progettazione della carpenteria metallica per le piattaforme offshore?Risposta: L’analisi strutturale avanzata consente di valutare il comportamento della carpenteria metallica di una piattaforma offshore in modo più accurato rispetto ai metodi tradizionali. Questo permette di individuare e prevenire potenziali problematiche strutturali, migliorando la sicurezza e l’affidabilità delle piattaforme.Domanda: Quali software di modellazione tridimensionale vengono utilizzati nella progettazione della carpenteria metallica per le piattaforme offshore?Risposta: Nella progettazione delle piattaforme offshore, sono impiegati software specifici di modellazione tridimensionale, come ad esempio Tekla Structures e SACS. Questi software consentono di creare modelli dettagliati della carpenteria metallica e di eseguire analisi strutturali complesse per valutare la sua integrità.Domanda: Quali sono i criteri di normativa specifici per l’ambiente marino che vengono considerati nella progettazione della carpenteria metallica per le piattaforme offshore?Risposta: Nella progettazione della carpenteria metallica per le piattaforme offshore, vengono considerati criteri di normativa specifici come quelli definiti dagli standard del settore, ad esempio il DNV (Det Norske Veritas) o l’ASME (American Society of Mechanical Engineers). Questi criteri garantiscono che la carpenteria sia strutturalmente sicura e in grado di resistere alle sollecitazioni ambientali.Domanda: Quali sono le sfide principali nella progettazione della carpenteria metallica per le piattaforme offshore?Risposta: La progettazione della carpenteria metallica per le piattaforme offshore presenta diverse sfide, tra cui la necessità di considerare l’ambiente di lavoro estremo, come le condizioni marine avverse e i movimenti dell’acqua, insieme alle sollecitazioni strutturali. Inoltre, è necessario assicurarsi che la carpenteria sia progettata in conformità con le normative di sicurezza e affidabilità.Domanda: Quali sono i metodi utilizzati per garantire la qualità della carpenteria metallica delle piattaforme offshore?Risposta: Per garantire la qualità della carpenteria metallica delle piattaforme offshore vengono impiegati metodi quali l’ispezione visiva, i test non distruttivi (come test radiografici o ultrasuoni) e i test di carico. Questi metodi consentono di individuare eventuali difetti o degradazioni nella carpenteria, garantendo la sua integrità strutturale e la sicurezza degli operatori.
Per concludere
In conclusione, le tecniche di progettazione per carpenteria metallica in piattaforme offshore svolgono un ruolo fondamentale nell’industria dell’energia marina. Questo articolo ha esplorato gli aspetti chiave di questa disciplina, concentrandosi sulle sfide e le soluzioni necessarie per garantire la sicurezza, l’affidabilità e l’efficienza delle piattaforme offshore. Abbiamo analizzato l’importanza della progettazione strutturale, l’utilizzo di materiali resistenti alla corrosione, l’importanza dell’analisi di carico e la necessità di considerare gli effetti dell’ambiente marino. Inoltre, abbiamo evidenziato l’importanza delle ispezioni periodiche e della manutenzione preventiva per garantire l’integrità delle strutture nel lungo termine. L’industria della carpenteria metallica in piattaforme offshore è una sfida complessa che richiede competenze tecniche e una rigorosa attenzione ai dettagli. Tuttavia, grazie alla continua innovazione e allo sviluppo di tecniche sempre più sofisticate, è possibile realizzare piattaforme offshore sicure, efficienti ed economicamente sostenibili. Infine, spetta agli ingegneri, ai progettisti e agli operatori del settore collaborare per affrontare le sfide future, come l’aumento delle condizioni ambientali estreme e la necessità di sostenibilità energetica. Solo attraverso un approccio analitico e professionale all’applicazione di tecniche di progettazione per carpenteria metallica in piattaforme offshore, potremo garantire il futuro della nostra industria e il successo del nostro settore energetico marino.
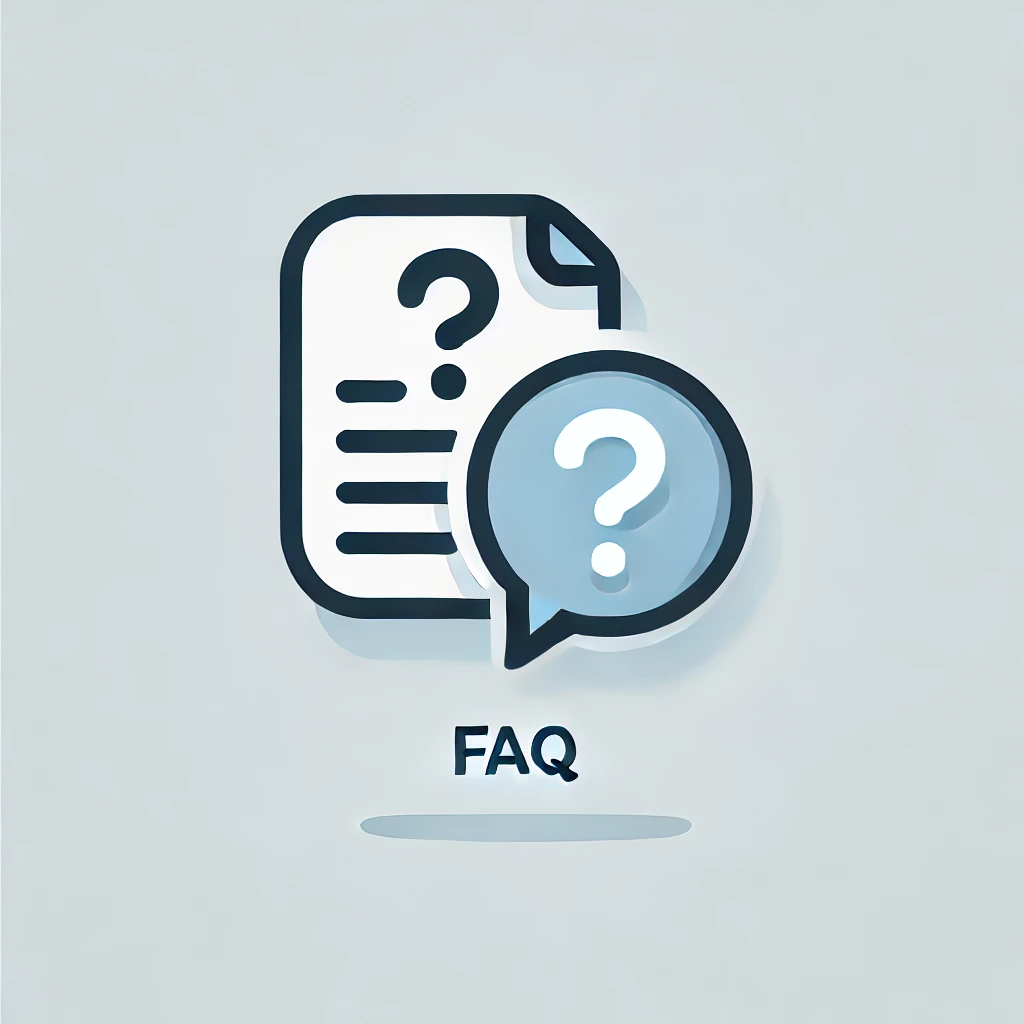
FAQ
Domande frequenti? Scopri tutte le risposte ai quesiti tecnici più comuni! Approfondisci le informazioni essenziali sulle opere metalliche e migliora la tua comprensione con soluzioni pratiche e chiare. Non lasciarti sfuggire dettagli importanti!
Introduzione
Le tecnologie di taglio e lavorazione a getto d’acqua rappresentano un elemento chiave nella produzione di componenti per attrezzature metalliche. Grazie alla loro versatilità e precisione, questi sistemi si sono affermati come una soluzione affidabile per la realizzazione di parti metalliche di alta qualità. Nel presente articolo, esploreremo le principali caratteristiche di queste tecnologie, analizzando i vantaggi e i limiti dell’utilizzo del taglio e lavorazione a getto d’acqua per la produzione di componenti di attrezzature metalliche. Inoltre, verranno proposte alcune linee guida per l’ottimizzazione dei processi di taglio e lavorazione a getto d’acqua al fine di ottenere risultati ottimali.
Introduzione alle Tecnologie di Taglio e Lavorazione a Getto d’Acqua per Componenti di Attrezzature Metalliche
Le tecnologie di taglio e lavorazione a getto d’acqua rappresentano una soluzione versatile e altamente efficiente per la lavorazione dei componenti di attrezzature metalliche. Grazie alla capacità di tagliare attraverso una vasta gamma di materiali, tra cui acciaio inossidabile, alluminio, ottone e materie plastiche, queste tecnologie sono ampiamente utilizzate in diversi settori industriali.
La tecnologia a getto d’acqua utilizza un flusso ad alta pressione di acqua mista a una sostanza abrasiva, come granelli di sabbia o polveri di ceramica, per creare un potente getto che può tagliare i materiali più resistenti. Questo metodo di taglio offre numerosi vantaggi rispetto alle tecniche tradizionali, quali il plasma o il laser.
La precisione di taglio è uno dei principali vantaggi della tecnologia a getto d’acqua. Grazie alla possibilità di utilizzare software di controllo avanzato, è possibile ottenere tagli estremamente precisi, fino a una tolleranza di +/- 0.1 mm. Ciò rende questa tecnologia particolarmente adatta per la lavorazione di componenti di attrezzature metalliche che richiedono elevati standard di precisione.
Un’altra caratteristica fondamentale della tecnologia a getto d’acqua è la sua capacità di tagliare i materiali senza alterarne la struttura o le proprietà termiche. Poiché il taglio avviene a basse temperature, anche i materiali più sensibili al calore, come leghe di alluminio, possono essere lavorati senza subire deformazioni o danni.
La flessibilità di questa tecnologia è un altro punto di forza. Grazie alla versatilità del getto d’acqua, è possibile realizzare tagli diritti, inclinati o curvi a qualsiasi angolo. Inoltre, è possibile eseguire tagli con elevata complessità geometrica senza la necessità di attrezzature aggiuntive.
La tecnologia a getto d’acqua è anche ecologicamente sostenibile. Rispetto ad altre tecniche di taglio, come il plasma o il laser, non produce fumi nocivi o emissioni di gas. Inoltre, i materiali di scarto possono essere facilmente riciclati, riducendo l’impatto ambientale.
Nel settore delle attrezzature metalliche, questa tecnologia è ampiamente utilizzata per la produzione di componenti come lamierini, pannelli per custodie, guide per meccanismi di movimento e molto altro. Grazie alla sua efficienza e versatilità, il taglio a getto d’acqua sta riscuotendo sempre più successo nel settore industriale, rappresentando una soluzione ideale per la lavorazione dei componenti di attrezzature metalliche.
In conclusione, la tecnologia di taglio e lavorazione a getto d’acqua offre un’ampia gamma di vantaggi per la produzione di componenti di attrezzature metalliche. La precisione, la flessibilità e l’ecosostenibilità del processo contribuiscono a rendere questa tecnologia un’opzione altamente efficiente e affidabile per le aziende che operano nel settore delle attrezzature metalliche.
Vantaggi dell’utilizzo del Taglio e Lavorazione a Getto d’Acqua
Il Taglio e Lavorazione a Getto d’Acqua rappresenta una soluzione innovativa e altamente efficiente per molteplici settori industriali. Questo metodo di lavorazione utilizza un getto a alta pressione di acqua unito a un abrasivo per tagliare e lavorare vari tipi di materiali, inclusi metalli, pietre, ceramica, vetro e plastica. Gli utilizzatori di questa tecnologia beneficiano di vari vantaggi chiave che la rendono una scelta preferita per molte applicazioni industriali.
Prima di tutto, l’utilizzo del Taglio e Lavorazione a Getto d’Acqua garantisce precisione estrema. L’acqua, spruzzata a una velocità elevatissima, permette di ottenere tagli puliti e accurati, mantenendo intatto il materiale senza comprometterne le caratteristiche originali. Questo rende possibile lavorare con tolleranze molto strette e garantire risultati di alta qualità.
Inoltre, questo metodo non produce calore durante il processo di lavorazione. Ciò significa che i materiali sensibili al calore, come plastica o legno, possono essere tagliati e lavorati senza subire deformazioni o danni. Questa caratteristica è fondamentale per molte industrie, inclusa quella medica e automobilistica, in cui la precisione e l’integrità del materiale sono cruciali.
Un’altra grande vantaggio dell’utilizzo del Taglio e Lavorazione a Getto d’Acqua risiede nella sua versatilità. Questa tecnologia può essere applicata su una vasta gamma di materiali, in differenti spessori e forme. Non importa se si tratta di un pezzo complesso o di uno con tratti sinuosi, il getto d’acqua può adattarsi facilmente per eseguire tagli precisi e lavorazioni complesse, garantendo la massima flessibilità.
Inoltre, la tecnologia del getto d’acqua è considerata ecologica e sostenibile. Durante il taglio, il getto d’acqua non produce fumi né sostanze nocive, riducendo l’impatto ambientale. Inoltre, molti sistemi di Taglio e Lavorazione a Getto d’Acqua sono dotati di sistemi di riciclo dell’acqua, che permettono di riutilizzare l’acqua utilizzata, limitando gli sprechi e i costi.
L’uso del getto d’acqua per la lavorazione riduce anche i rischi di contaminazione. Con il taglio a getto d’acqua, non ci sono contatti fisici con il materiale da lavorare, evitando così la contaminazione delle superfici. Questo è un aspetto critico per settori come quello alimentare o farmaceutico, in cui l’igiene è fondamentale e ogni minima presenza di contaminanti può avere conseguenze gravi.
Un altro vantaggio importante è la riduzione dei tempi di lavorazione. Essendo una tecnologia altamente efficiente, il Taglio e Lavorazione a Getto d’Acqua permette di ottenere risultati rapidamente e senza dover eseguire successivamente lavorazioni aggiuntive per perfezionare i dettagli. Ciò si traduce in una maggiore produttività e una riduzione dei tempi di consegna per gli ordini dei clienti.
Infine, vale la pena menzionare che l’utilizzo del Taglio e Lavorazione a Getto d’Acqua è sicuro e affidabile. Questo metodo di lavorazione è controllato da sistemi computerizzati avanzati, che garantiscono la sicurezza degli operatori e la precisione dei processi. Inoltre, le moderne apparecchiature di Taglio e Lavorazione a Getto d’Acqua sono progettate con funzionalità di sicurezza integrate per prevenire incidenti o danni.
Processo di Taglio a Getto d’Acqua: Materiali adatti e spessori ottimali
I materiali adatti per il processo di taglio a getto d’acqua sono vasti e comprendono una varietà di tipologie che vanno oltre i limiti tradizionali di altri metodi di taglio. La flessibilità di questa tecnologia consente di lavorare con materiali come metalli, compositi, pietra, ceramica e vetro. L’unico requisito fondamentale è che il materiale sia relativamente duro e non reagisca in maniera eccessiva all’acqua.
I metalli sono una delle scelte più comuni per il taglio a getto d’acqua. Essi includono acciaio inossidabile, alluminio, bronzo, rame e titanio. Inoltre, anche leghe più complesse come l’Inconel e l’acciaio al carbonio possono essere facilmente tagliate con precisione tramite questa tecnologia.
I compositi, come il fibrocemento o la fibra di vetro rinforzata, possono essere facilmente lavorati grazie al getto d’acqua. Questi materiali sono spesso utilizzati nell’industria aerospaziale e automobilistica per la loro resistenza e durata.
Le pietre naturali e artificiali sono un’altra categoria di materiali adatti al taglio a getto d’acqua. Ad esempio, marmo, granito, pietra calcarea, ardesia e quarzo possono essere tagliati con precisione, creando forme complesse e dettagliate.
La ceramica è un materiale duro, fragile e poroso che richiede una tecnologia di precisione per il suo taglio. Il getto d’acqua è ideale per questo scopo, in quanto non produce calore e permette di ottenere tagli puliti, minimizzando le rotture indesiderate.
Infine, il vetro è un altro materiale adatto per il taglio a getto d’acqua. La sua fragilità richiede una lavorazione delicata e il getto d’acqua è una scelta ideale per ottenere risultati precisi senza danneggiare il materiale.
Oltre ai materiali adatti, è importante considerare anche gli spessori ottimali per il taglio a getto d’acqua. La tecnologia può lavorare con spessori che vanno da millimetri a diversi centimetri, a seconda del materiale. Ad esempio, per il taglio delle lamiere metalliche, lo spessore ottimale può variare da 0,5 mm a 200 mm.
Uno dei vantaggi del taglio a getto d’acqua è che non si verificano deformazioni termiche o stress nel materiale durante il processo. Ciò consente di ottenere risultati precisi, indipendentemente dallo spessore del materiale, garantendo una precisione costante e affidabile.
In conclusione, il processo di taglio a getto d’acqua offre una vasta gamma di materiali adatti e spessori ottimali per soddisfare le esigenze dei diversi settori industriali. La sua versatilità, precisione e possibilità di tagli complessi lo rendono una scelta ideale per molteplici applicazioni, dall’industria aerospaziale all’edilizia.
Tecniche avanzate per migliorare la qualità del taglio a getto d’acqua
Le offrono nuove possibilità e risultati eccezionali nell’ambito delle lavorazioni industriali. Queste metodologie, basate sull’utilizzo della pressione idraulica, consentono di tagliare con precisione una varietà di materiali, dall’acciaio inossidabile alla ceramica, senza alcun contatto fisico. In questa sezione, esploreremo alcune strategie innovative che consentono di ottenere tagli ancora più precisi ed efficienti.
1. Ottimizzazione dei parametri di taglio: per migliorare la qualità del taglio a getto d’acqua, è fondamentale analizzare e ottimizzare i parametri di taglio. Questi includono la pressione dell’acqua, la velocità di taglio e il diametro del getto. Attraverso test e prove, è possibile determinare la combinazione perfetta di questi parametri per ottenere risultati ottimali.
2. Utilizzo di software avanzati: l’utilizzo di software avanzati dedicati al taglio a getto d’acqua consente di ottimizzare il processo in modo più accurato ed efficiente. Tali software sono in grado di calcolare automaticamente i parametri di taglio ottimali in base al tipo e allo spessore del materiale, garantendo così risultati di alta qualità.
3. Tecniche di nesting: il nesting è una tecnica che permette di posizionare in modo ottimale i pezzi da tagliare sul materiale di base, riducendo gli sprechi e ottimizzando così la produzione. Attraverso software dedicati, è possibile effettuare un nesting intelligente che minimizza i tempi di lavorazione e consente di ottenere tagli precisi ed efficienti.
4. Taglio allo zero gap: il taglio allo zero gap è una tecnica avanzata che consiste nel ridurre al minimo lo spazio tra il getto d’acqua e il materiale da tagliare. Questo permette di ottenere tagli più precisi, evitando eventuali irregolarità o sbavature. L’utilizzo di ugelli specializzati e l’ottimizzazione dei parametri di taglio sono fondamentali per implementare con successo questa tecnica.
5. Raffreddamento del materiale: durante il processo di taglio a getto d’acqua, il materiale può raggiungere alte temperature a causa della pressione idraulica. Per evitare deformazioni o alterazioni della struttura del materiale, è possibile utilizzare tecniche di raffreddamento che consentono di mantenere la temperatura costante e controllata. Questo contribuisce a migliorare la qualità del taglio, garantendo risultati precisi e senza danneggiamenti.
6. Utilizzo di abrasivi speciali: l’aggiunta di abrasivi al getto d’acqua può migliorare significativamente la qualità del taglio, specialmente per materiali più densi o resistenti. Gli abrasivi aiutano ad aumentare la velocità di taglio, ridurre l’usura delle parti e ottenere una finitura più uniforme. È importante scegliere l’abrasivo più adatto al tipo di materiale da tagliare al fine di ottenere risultati ottimali.
7. Programmazione avanzata: la programmazione avanzata consente di tagliare forme complesse in modo preciso e efficiente. Utilizzando software specializzati per la programmazione, è possibile creare percorsi di taglio ottimizzati e ridurre al minimo il tempo necessario per completare il lavoro. Questo approccio permette di ottenere una maggiore precisione e un miglioramento significativo della qualità del taglio.
8. Monitoraggio costante: per garantire la qualità del taglio a getto d’acqua, è fondamentale effettuare un monitoraggio costante del processo. Questo può essere realizzato attraverso sistemi di controllo automatizzati o manualmente, verificando la corretta pressione dell’acqua, il flusso del getto e l’efficienza del sistema. Il monitoraggio costante permette di individuare eventuali anomalie o problemi ed intervenire prontamente per garantire risultati ottimali.
Implementare queste può portare ad una produzione più efficiente, costi ridotti e risultati di alta qualità. Con l’utilizzo di software avanzati, l’ottimizzazione dei parametri di taglio e l’introduzione di tecnologie innovative, è possibile ottenere una precisione e una finitura ottimale nella lavorazione dei materiali più diversi.
Sicurezza e normative da considerare nell’uso delle tecnologie di taglio a getto d’acqua
Quando si utilizzano tecnologie di taglio a getto d’acqua, è di fondamentale importanza comprendere e seguire le normative di sicurezza pertinenti. Queste normative sono state sviluppate per garantire un ambiente di lavoro sicuro e minimizzare i rischi associati all’uso di macchine ad alta pressione.
Ecco alcune normative chiave da considerare quando si lavora con tecnologie di taglio a getto d’acqua:
- Normativa EN 1010: Questa normativa stabilisce i requisiti di sicurezza per i macchinari di taglio a getto d’acqua. È importante assicurarsi che la macchina soddisfi i requisiti di sicurezza e che venga effettuata una manutenzione regolare per mantenerla in condizioni ottimali.
- Valutazione dei rischi: Prima di utilizzare una macchina di taglio a getto d’acqua, è necessario condurre una valutazione dei rischi per identificare potenziali pericoli e adottare le misure di sicurezza appropriate. Questo dovrebbe includere anche la formazione del personale sull’uso sicuro della macchina.
Per garantire un utilizzo sicuro delle tecnologie di taglio a getto d’acqua, si consiglia di seguire queste linee guida:
- Indossare abbigliamento protettivo: Quando si lavora con una macchina di taglio a getto d’acqua, è necessario indossare abbigliamento protettivo come guanti, occhiali e caschi per proteggere contro possibili schizzi o proiezioni di materiale.
- Mantenere l’area di lavoro pulita e ordinata: Un ambiente di lavoro pulito e ordinato riduce il rischio di incidenti. Assicurarsi che l’area intorno alla macchina sia libera da ostacoli e che tutti gli utensili siano correttamente riposti dopo l’uso.
È importante ricordare che l’uso delle tecnologie di taglio a getto d’acqua richiede una formazione adeguata. Gli operatori della macchina devono essere consapevoli dei pericoli associati all’utilizzo della macchina e delle misure di sicurezza necessarie per evitarli.
In conclusione, la sicurezza e il rispetto delle normative sono prioritari quando si lavora con tecnologie di taglio a getto d’acqua. Seguire le norme di sicurezza, adottare misure preventive e formare adeguatamente il personale sono essenziali per garantire un ambiente di lavoro sicuro e ridurre al minimo i rischi associati all’utilizzo di queste macchine.
Manutenzione preventiva e risoluzione dei problemi comuni nelle apparecchiature di taglio a getto d’acqua
Controllo regolare della pressione e del flusso d’acqua
Una corretta manutenzione preventiva delle apparecchiature di taglio a getto d’acqua deve includere un controllo regolare della pressione e del flusso d’acqua. È importante verificare che la pressione dell’acqua sia costante e che non ci siano variazioni anomale nel flusso. Questo può essere fatto utilizzando strumenti appositi e confrontando i valori con quelli consigliati dal produttore dell’apparecchiatura.
Pulizia dei filtri e dei condotti dell’acqua
I filtri e i condotti dell’acqua sono componenti fondamentali nelle apparecchiature di taglio a getto d’acqua. È essenziale pulirli regolarmente per evitare l’accumulo di detriti e sedimenti che potrebbero ostruire il flusso dell’acqua. Utilizzare prodotti specifici per la rimozione di depositi minerali e sabbia, seguendo le istruzioni del produttore.
Controllo delle guarnizioni e delle valvole
Guarnizioni e valvole svolgono un ruolo cruciale nel corretto funzionamento delle apparecchiature di taglio a getto d’acqua. È consigliabile controllarle periodicamente per verificare che siano sigillate correttamente e per individuare eventuali segni di usura o danni, sostituendole se necessario.
Effettuare la lubrificazione dei componenti mobili
I componenti mobili delle apparecchiature di taglio a getto d’acqua devono essere lubrificati regolarmente per garantire una corretta funzionalità. Utilizzare lubrificanti consigliati dal produttore e seguire le istruzioni per applicarli in modo corretto. Prestare particolare attenzione alle parti che si muovono maggiormente, come le guide e i cuscinetti.
Controllo del sistema di raffreddamento
Il sistema di raffreddamento delle apparecchiature di taglio a getto d’acqua gioca un ruolo cruciale nel mantenere una temperatura ottimale durante l’uso dell’apparecchiatura. Controllare regolarmente che il sistema sia ben funzionante e che non ci siano perdite o ostruzioni nelle tubazioni. Pulire i radiatori e sostituire il liquido di raffreddamento secondo le indicazioni del produttore.
Monitoraggio e sostituzione delle parti usurabili
Le apparecchiature di taglio a getto d’acqua sono costituite da diverse parti che si usurano nel tempo. Queste includono ugelli, orifizi e tubazioni flessibili. È importante monitorare attentamente lo stato di queste parti e sostituirle periodicamente per evitare il deterioramento delle prestazioni. Fare riferimento al manuale dell’apparecchiatura per conoscere gli intervalli raccomandati per la sostituzione.
Verifica del sistema di controllo elettronico
Il sistema di controllo elettronico è un componente critico nelle apparecchiature di taglio a getto d’acqua. È fondamentale eseguire un controllo periodico per assicurarsi che sia ben funzionante, che tutti i sensori siano correttamente collegati e calibrati e che non ci siano errori di comunicazione o malfunzionamenti. Se necessario, eseguire aggiornamenti software secondo le indicazioni del produttore.
Formazione del personale e manuali d’uso
La manutenzione preventiva e la risoluzione dei problemi comuni nelle apparecchiature di taglio a getto d’acqua richiedono una conoscenza tecnica specifica. È essenziale fornire al personale una formazione adeguata sulle procedure di manutenzione e risoluzione dei problemi. Inoltre, è fondamentale avere a disposizione manuali d’uso chiari e completi, forniti dal produttore, che offrano indicazioni dettagliate su come effettuare la manutenzione preventiva e risolvere i problemi comuni.
Conclusioni e raccomandazioni per l’efficace utilizzo delle tecnologie di taglio e lavorazione a getto d’acqua per componenti di attrezzature metalliche
Di seguito sono riportate alcune conclusioni e raccomandazioni da tenere a mente per garantire un utilizzo efficace delle tecnologie di taglio e lavorazione a getto d’acqua per componenti di attrezzature metalliche:
1. Scelta del materiale
Prima di utilizzare la tecnologia di taglio a getto d’acqua, valutare attentamente il tipo di materiale da lavorare. Questo influenzerà la pressione dell’acqua e la velocità di taglio. Assicurarsi di utilizzare il materiale corretto per evitare danni alla macchina e ottenere risultati ottimali.
2. Manutenzione regolare della macchina
Per garantire un funzionamento efficiente e una vita più lunga della macchina, è fondamentale eseguire regolarmente la manutenzione. Controllare e pulire i filtri dell’acqua, sostituire le parti usurabili e verificare il corretto allineamento degli ugelli. Una macchina ben mantenuta garantisce risultati di taglio di alta qualità.
3. Preparazione adeguata del materiale
Prima di iniziare il processo di taglio, è importante preparare adeguatamente il materiale. Rimuovere eventuali detriti, ruggine o vernice presente sulla superficie. Ciò contribuirà a evitare ostruzioni degli ugelli e a migliorare la qualità del taglio.
4. Programmazione precisa dei parametri di taglio
Una corretta programmazione dei parametri di taglio è essenziale per ottenere risultati consistenti. Considerare il tipo di materiale, lo spessore e la complessità del componente. Regolare la pressione dell’acqua, la velocità di taglio e la distanza tra l’ugello e il materiale per ottenere tagli precisi e puliti.
5. Utilizzo di ugelli di alta qualità
Investire in ugelli di alta qualità è fondamentale per ottenere risultati ottimali. Gli ugelli di buona qualità garantiscono un flusso d’acqua stabile e uniforme, riducendo al minimo il rischio di ostruzioni. Scegliere gli ugelli in base al tipo di materiale e alla complessità del taglio.
6. Sicurezza sul lavoro
I dispositivi di taglio a getto d’acqua presentano alcuni rischi potenziali, come la pressione dell’acqua e gli spruzzi. Assicurarsi di seguire tutte le procedure di sicurezza, indossare l’equipaggiamento di protezione individuale e addestrare adeguatamente gli operatori. Garantire un ambiente di lavoro sicuro e ridurre al minimo gli incidenti.
7. Test e controllo della qualità
Prima di utilizzare i componenti tagliati e lavorati con il getto d’acqua, eseguire controlli di qualità. Verificare la precisione delle dimensioni, la finitura superficiale e l’integrità strutturale. Questo aiuterà a individuare eventuali difetti o errori nel processo di taglio e apportare le modifiche necessarie.
8. Aggiornamento delle competenze e della tecnologia
Le tecnologie di taglio a getto d’acqua sono in continua evoluzione. Mantenersi aggiornati sulle ultime tecniche, materiali e macchine disponibili sul mercato. Investire nella formazione dei dipendenti per migliorare le competenze tecniche e ottimizzare l’efficienza operativa. Questo consentirà di rimanere competitivi nel settore delle attrezzature metalliche.
Q&A
Q: Che cosa sono le tecnologie di taglio e lavorazione a getto d’acqua per componenti di attrezzature metalliche?
A: Le tecnologie di taglio e lavorazione a getto d’acqua per componenti di attrezzature metalliche sono processi avanzati che utilizzano l’energia cinetica generata da un getto d’acqua ad alta pressione per tagliare e lavorare pezzi di metallo con precisione e efficacia.
Q: Come funziona il processo di taglio a getto d’acqua?
A: Durante il taglio a getto d’acqua, l’acqua viene pressurizzata a un livello estremamente elevato e indirizzata attraverso un ugello sottile. A volte, possono essere aggiunti materiali abrasivi per aumentare la velocità e la precisione del processo. Il getto d’acqua ad alta pressione viene quindi diretto verso il componente metallico desiderato, creando una forza che rimuove il materiale e produce il taglio desiderato.
Q: Quali sono i vantaggi delle tecnologie di taglio a getto d’acqua per componenti di attrezzature metalliche?
A: Le tecnologie di taglio a getto d’acqua offrono numerosi vantaggi. Questo metodo non produce calore, evitando così la deformazione o la fusione del materiale metallico, mantenendo quindi l’integrità strutturale dei componenti. Inoltre, il taglio a getto d’acqua può essere utilizzato su una vasta gamma di materiali metallici, inclusi quelli sensibili al calore come l’alluminio. Inoltre, grazie alla flessibilità e alla precisione del processo, è possibile ottenere forme complesse e dettagliate senza la necessità di lavorazioni ulteriori.
Q: Quali applicazioni trovano le tecnologie di taglio a getto d’acqua nelle attrezzature metalliche?
A: Le tecnologie di taglio a getto d’acqua sono ampiamente utilizzate nella produzione di attrezzature metalliche. Trovano applicazione nell’industria aerospaziale, automobilistica, elettronica, nella produzione di utensili e macchinari industriali, nonché nella lavorazione artistica del metallo. Questo metodo è in grado di tagliare e lavorare pezzi di varie dimensioni e spessori, consentendo la creazione di componenti altamente precisi e personalizzati per diverse applicazioni industriali.
Q: Quali sono i limiti delle tecnologie di taglio a getto d’acqua per componenti di attrezzature metalliche?
A: Nonostante i numerosi vantaggi, le tecnologie di taglio a getto d’acqua presentano alcune limitazioni. Ad esempio, il processo può essere relativamente lento rispetto ad altre tecniche di taglio. Inoltre, la presenza di materiali abrasivi può causare un consumo più rapido degli ugelli, richiedendo la loro sostituzione periodica. Inoltre, il costo di investimento iniziale per l’acquisto e la manutenzione di apparecchiature ad alta pressione può essere considerevole.
Q: Come azienda, come posso beneficiare delle tecnologie di taglio e lavorazione a getto d’acqua?
A: Come azienda, l’utilizzo delle tecnologie di taglio e lavorazione a getto d’acqua può comportare numerosi vantaggi. Questo processo consente di ottenere componenti metalliche precise e di alta qualità, che possono migliorare le performance dei prodotti e ridurre al minimo errori e scarti. Inoltre, la flessibilità del taglio a getto d’acqua consente di rispondere meglio alle richieste dei clienti in termini di personalizzazione dei componenti. Infine, l’uso di tecnologie innovative può migliorare la reputazione e la competitività aziendale nell’industria delle attrezzature metalliche.
Concluding Remarks
In conclusione, le tecnologie di taglio e lavorazione a getto d’acqua rappresentano una soluzione altamente efficiente e versatile per la produzione di componenti di attrezzature metalliche. Grazie alla loro precisione, velocità e capacità di lavorare con una vasta gamma di materiali, queste tecnologie si sono affermate come un indispensabile strumento per l’industria metalmeccanica.
Grazie alla loro tecnologia sofisticata e alla capacità di tagliare attraverso materiali duri come il metallo con facilità e precisione, i sistemi di taglio a getto d’acqua offrono una serie di vantaggi significativi. La loro capacità di lavorare senza generare calore o distorsioni termiche li rende particolarmente adatti per il taglio di materiali sensibili al calore, come l’alluminio e le leghe di titanio.
Inoltre, l’assenza di contatti tra la testa di taglio e il materiale lavorato elimina la necessità di attrezzature di sostituzione costose e riduce al minimo il rischio di errore umano. Questo non solo aumenta la sicurezza sul luogo di lavoro, ma garantisce anche risultati precisi e di alta qualità.
Le potenzialità delle tecnologie di taglio e lavorazione a getto d’acqua vanno oltre la semplice produzione di componenti. L’abilità di eseguire tagli complessi e intricati consente la creazione di geometrie personalizzate, migliorando sia la funzionalità che l’estetica dei prodotti finali.
Inoltre, la flessibilità dei sistemi a getto d’acqua li rende adatti a una vasta gamma di settori industriali, tra cui l’aeronautica, l’automotive, l’energia e molteplici altre applicazioni. La possibilità di lavorare materiali metallici, ceramici, plastici e compositi conferisce a queste tecnologie un vantaggio competitivo cruciale.
In sintesi, l’utilizzo delle tecnologie di taglio e lavorazione a getto d’acqua rappresenta un decisivo passo avanti nell’ambito della produzione di componenti di attrezzature metalliche. Grazie alla loro precisione, versatilità e capacità di lavorare con una vasta gamma di materiali, queste soluzioni si pongono come leader nell’industria metalmeccanica. Sia che si tratti di realizzare componenti in leghe di alluminio per l’industria aeronautica o parti di precisione per attrezzature mediche, i sistemi di taglio a getto d’acqua garantiscono risultati di alta qualità e soddisfano le esigenze più demanding del mercato.
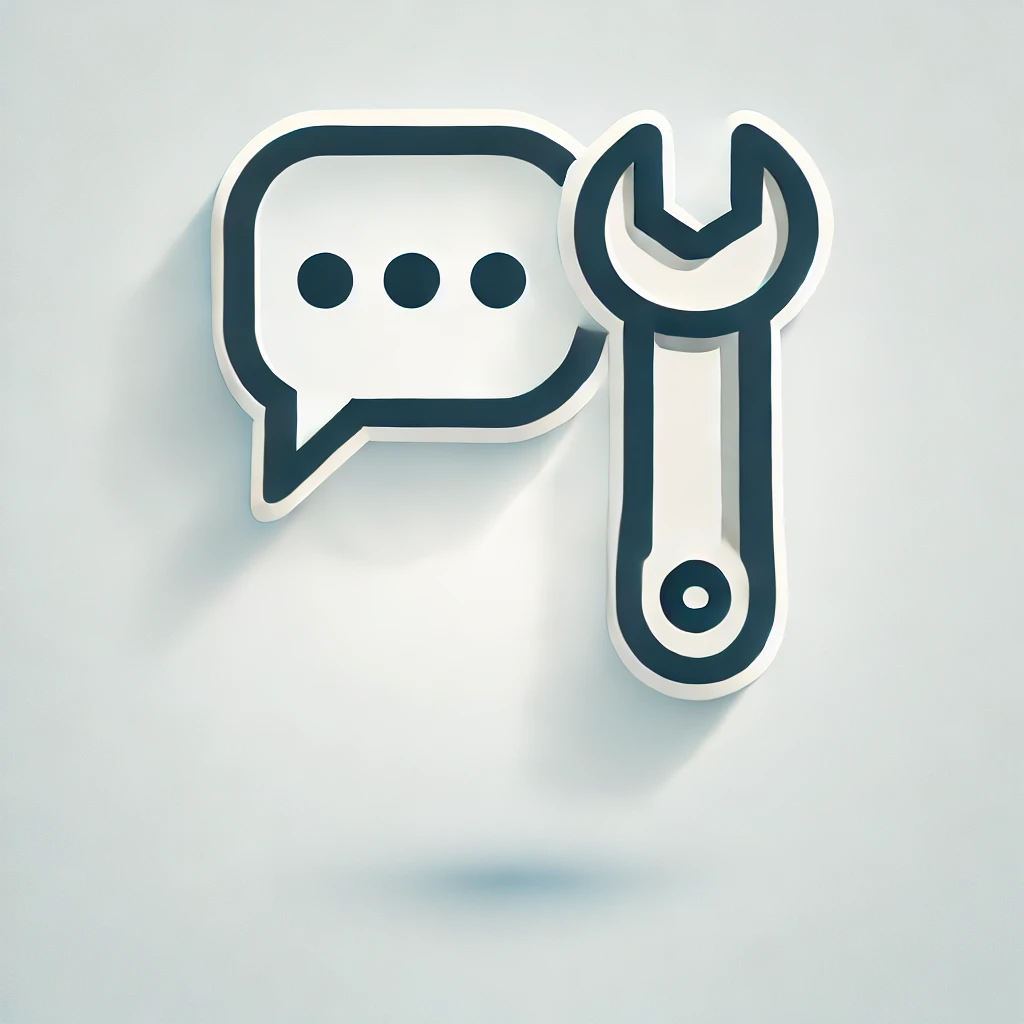
"Hai un'opinione tecnica o una domanda specifica? Non esitare, lascia un commento! La tua esperienza può arricchire la discussione e aiutare altri professionisti a trovare soluzioni. Condividi il tuo punto di vista!"
Partecipa!
Commenti