Costruzione di Capannoni in Ferro: Approcci Prefabbricati e Risparmio Temporale

Costruzione di Capannoni in Ferro: Approcci Prefabbricati e Risparmio Temporale
Nell’ambito della costruzione di capannoni in ferro, uno dei principali obiettivi dei costruttori è la riduzione dei tempi di realizzazione senza compromettere la qualità finale. A tal fine, l’utilizzo di approcci prefabbricati si è dimostrato estremamente vantaggioso in termini di efficienza e risparmio temporale. Questo articolo si propone di esaminare da un punto di vista tecnico l’impiego di metodologie prefabbricate nella costruzione di capannoni in ferro, analizzando i benefici derivanti da questa pratica e il ruolo fondamentale che svolge nel contesto attuale.
Indice dei contenuti
- Approccio prefabbricato: vantaggi e considerazioni
- Materiali per la costruzione di capannoni in ferro
- Risparmio temporale con l’utilizzo di approcci prefabbricati
- Importanza della progettazione accurata per la costruzione di capannoni in ferro
- Raccomandazioni per la scelta dei fornitori di capannoni prefabbricati in ferro
- Benefici dell’utilizzo di tecnologie innovative nella costruzione di capannoni in ferro
- Considerazioni sulla manutenzione e la durata dei capannoni prefabbricati in ferro
- Domande e risposte
- In Conclusione
Approccio prefabbricato: vantaggi e considerazioni
L’approccio prefabbricato sta guadagnando sempre più popolarità nel settore dell’edilizia grazie ai suoi numerosi vantaggi. Questo metodo costruttivo innovative rappresenta una soluzione efficiente, rapida e sostenibile per la realizzazione di edifici di qualità superiore. In questo articolo esploreremo i vantaggi e le considerazioni chiave associate all’utilizzo dell’approccio prefabbricato.
Vantaggi:
1. Riduzione dei tempi di costruzione: Grazie all’utilizzo di elementi prefabbricati, il processo di costruzione risulta notevolmente accelerato rispetto ai tradizionali metodi di costruzione in loco. Questo si traduce in una riduzione significativa dei tempi di completamento del progetto, consentendo di risparmiare tempo e denaro.
2. Qualità controllata: Gli elementi prefabbricati vengono prodotti in fabbrica sotto rigorosi standard di qualità. Ciò permette di avere un controllo più accurato sulla qualità dei materiali e delle finiture, riducendo così il rischio di difetti e imperfezioni.
3. Sostenibilità: Alcune persone potrebbero considerare l’approccio prefabbricato come una soluzione più sostenibile rispetto ai tradizionali metodi di costruzione. La produzione in fabbrica consente di ridurre lo spreco di materiali ed energia, oltre a ridurre al minimo l’impatto ambientale durante la fase di costruzione.
4. Flessibilità nell’adattamento: Grazie alla modularità degli elementi prefabbricati, è possibile apportare modifiche o ampliamenti a un edificio in modo relativamente semplice. Questa flessibilità consente di rispondere in modo rapido ed efficiente alle future esigenze dell’edificio, riducendo la necessità di demolizioni costose e ridisegni complessi.
Considerazioni:
1. Progettazione accurata: Per ottenere i migliori risultati dall’approccio prefabbricato, è fondamentale un’attenta progettazione in fase iniziale. La collaborazione tra architetti, ingegneri strutturali e produttori di elementi prefabbricati è essenziale per garantire la precisione nelle misure e la conformità alle normative vigenti.
2. Trasporto e logistica: Gli elementi prefabbricati devono essere trasportati in cantiere in modo sicuro ed efficiente. È necessario pianificare accuratamente le operazioni di trasporto e avere le attrezzature adatte per il sollevamento e l’installazione degli elementi prefabbricati.
3. Coordinamento tra i vari specialisti: L’approccio prefabbricato richiede una stretta collaborazione tra i vari specialisti coinvolti nel processo di costruzione. Questo include fabbricanti, ingegneri, architetti e appaltatori. Una comunicazione chiara e costante tra tutte le parti interessate è fondamentale per una costruzione senza intoppi.
4. Costi iniziali: Sebbene l’utilizzo dell’approccio prefabbricato possa portare a un risparmio di tempo e una riduzione dei costi durante la fase di costruzione, gli investimenti iniziali possono essere più elevati rispetto ai metodi tradizionali. È importante valutare attentamente i costi a lungo termine e i vantaggi derivanti dall’approccio prefabbricato prima di prendere una decisione.
In sintesi, l’approccio prefabbricato offre numerosi vantaggi in termini di tempi di costruzione ridotti, qualità controllata, sostenibilità e flessibilità nell’adattamento. Tuttavia, richiede anche una pianificazione accurata, coordinamento tra specialisti, attrezzature adeguate e, inizialmente, un investimento finanziario più elevato. Valutando attentamente i vantaggi e le considerazioni, l’approccio prefabbricato potrebbe essere un’opzione molto interessante per i progetti edilizi futuri.
Materiali per la costruzione di capannoni in ferro
Per la realizzazione di capannoni in ferro, è fondamentale avere a disposizione i giusti materiali di costruzione. Questi componenti sono indispensabili per garantire la solidità, la resistenza e la durata nel tempo delle strutture metalliche.
Di seguito, elencheremo i principali materiali necessari per la costruzione di capannoni in ferro:
- Tondini filettati: questi tondini di acciaio sono fondamentali per fissare le diverse componenti metalliche tra loro. Forniscono una connessione stabile e resistente, garantendo la stabilità strutturale.
- Pannelli grecati: i pannelli in ferro grecato rappresentano il rivestimento esterno dei capannoni. La loro struttura rinforzata permette di resistere alle intemperie, proteggendo l’interno delle strutture.
- Travi e colonne in acciaio: queste componenti fondamentali costituiscono la struttura portante dei capannoni. Le travi e le colonne sono realizzate in acciaio ad alta resistenza, garantendo la stabilità del capannone.
- Tegole metalliche: queste sono usate per il tetto dei capannoni. Le tegole in metallo offrono una protezione superiore rispetto alle tradizionali soluzioni, come le tegole in ceramica, e richiedono minor manutenzione.
- Porte e finestre: le porte e le finestre in ferro rappresentano le aperture del capannone. La scelta di modelli resistenti e sicuri garantisce una buona isolazione termica e acustica, oltre a una maggiore sicurezza.
- Pannelli isolanti: questi pannelli, realizzati in materiale isolante come il poliuretano espanso, vengono utilizzati per isolare termicamente i capannoni. Garantiscono un miglior comfort all’interno delle strutture, riducendo i costi energetici.
Bisogna ricordare che la corretta scelta dei materiali di costruzione è fondamentale per garantire la qualità e la durabilità del capannone in ferro. Si consiglia di rivolgersi a esperti nel settore, che saranno in grado di consigliare i materiali più adatti alle esigenze specifiche del progetto di costruzione.
Infine, è importante effettuare controlli di routine sulla struttura del capannone, per verificare la presenza di eventuali danni o usure che potrebbero comprometterne la sicurezza. L’utilizzo di materiali di qualità e la manutenzione regolare garantiranno una lunga vita utile al vostro capannone in ferro.
Risparmio temporale con l’utilizzo di approcci prefabbricati
Gli approcci prefabbricati rappresentano una soluzione innovativa per coloro che desiderano risparmiare tempo nella realizzazione di progetti complessi. Grazie alla loro natura modulare e pre-assemblata, queste soluzioni consentono di velocizzare significativamente il processo di costruzione o montaggio, consentendo di rispettare tempi di consegna più stretti.
One dei principali vantaggi dell’utilizzo di approcci prefabbricati è la riduzione dei tempi di produzione. Con l’utilizzo di componenti pre-assemblati, è possibile eliminare la necessità di creare parti da zero durante la costruzione. Ciò significa che le fasi di taglio, assemblaggio e finitura possono essere notevolmente ridotte, consentendo di risparmiare una quantità considerevole di tempo e risorse.
Altro aspetto importante è la riduzione dei tempi di installazione. Grazie alla loro natura modulare, i componenti prefabbricati possono essere facilmente trasportati e posizionati nel luogo desiderato. Questo permette di accelerare la fase di montaggio e ridurre i tempi di installazione, a differenza dei tradizionali metodi di costruzione che richiedono l’assemblaggio in sito.
Inoltre, gli approcci prefabbricati permettono una migliore pianificazione delle attività di costruzione. Essendo i componenti già completati e pronti per l’installazione, è possibile definire con precisione i tempi di consegna e pianificare le attività di costruzione in modo da ridurre al minimo i ritardi. Questa precisione nella pianificazione permette di ottimizzare i tempi di lavoro e di evitare interruzioni indesiderate.
Infine, l’utilizzo di approcci prefabbricati può ridurre il rischio di errori nella costruzione. Poiché i componenti sono prodotti in fabbrica, dove vengono seguiti rigorosi standard di qualità, è possibile minimizzare gli errori umani o le imperfezioni nella costruzione. Questo può garantire una maggiore sicurezza e un risultato finale di alta qualità.
In conclusione, l’utilizzo di approcci prefabbricati consente un significativo risparmio di tempo nella realizzazione di progetti complessi. Grazie alla riduzione dei tempi di produzione, installazione e pianificazione, è possibile completare i progetti più rapidamente, garantendo al contempo un elevato livello di qualità e sicurezza. Se sei alla ricerca di un modo per ottimizzare la tua produzione o costruzione, gli approcci prefabbricati sono sicuramente una scelta da considerare.
Importanza della progettazione accurata per la costruzione di capannoni in ferro
La progettazione accurata è un elemento fondamentale per la costruzione di capannoni in ferro di qualità. I capannoni in ferro sono strutture complesse che richiedono un approccio tecnico e professionale per garantire la loro solidità, sicurezza e durabilità nel tempo.
La progettazione accurata comprende una serie di fasi e processi che devono essere seguiti con attenzione. Prima di tutto, è necessario analizzare le specifiche del capannone in base alle esigenze del cliente. Questo include valutare la dimensione, l’altezza, la capacità di carico e altri requisiti strutturali. Una volta ottenute queste informazioni, è possibile procedere con la progettazione dettagliata.
Durante la fase di progettazione, vengono utilizzati software avanzati e calcoli strutturali per determinare la disposizione delle travi in ferro, delle colonne e degli altri elementi strutturali. È importante garantire che la struttura sia in grado di sopportare il peso previsto e le sollecitazioni meccaniche a cui sarà sottoposta nel corso della sua vita.
La progettazione accurata tiene conto anche dell’orientamento del capannone rispetto al sole, il quale può influire sulla temperatura interna e sull’efficienza energetica dell’edificio. Inoltre, vengono considerati anche fattori come la resistenza al vento, la neve e altre condizioni atmosferiche che potrebbero influenzare la struttura.
Un altro aspetto importante della progettazione accurata è la scelta dei materiali giusti. I capannoni in ferro richiedono l’utilizzo di acciaio di alta qualità, che sia resistente alla corrosione e agli agenti atmosferici. Inoltre, è necessario selezionare materiali isolanti adeguati per garantire un’adeguata climatizzazione interna.
Infine, la progettazione accurata considera anche gli aspetti estetici dell’edificio. È possibile personalizzare il design dei capannoni in ferro con diverse soluzioni architettoniche, come l’inserimento di finestre, porte, lucernari e altri elementi decorativi.
In conclusione, l’ non può essere sottovalutata. Una progettazione professionale e attenta ai dettagli garantisce la solidità, la sicurezza e la durabilità degli edifici, oltre a consentire una migliore efficienza energetica e una maggiore personalizzazione estetica.
Raccomandazioni per la scelta dei fornitori di capannoni prefabbricati in ferro
La scelta del fornitore giusto per l’acquisto di capannoni prefabbricati in ferro è cruciale per garantire la qualità, la durabilità e la sicurezza della struttura. Con una vasta gamma di opzioni disponibili sul mercato, è importante considerare attentamente alcuni fattori chiave prima di prendere una decisione finale. Ecco alcune raccomandazioni da tenere in considerazione:
- Esperti nella progettazione e produzione: Scegliere un fornitore con una vasta esperienza nella progettazione e produzione dei capannoni prefabbricati in ferro. Una competenza tecnica consolidata garantisce un processo di costruzione accurato e una solida struttura.
- Materiali di alta qualità: Assicurarsi che il fornitore utilizzi materiali di alta qualità per la costruzione dei capannoni. Il ferro utilizzato dovrebbe essere resistente alla corrosione e agli agenti atmosferici, garantendo la durabilità nel tempo.
- Personalizzazione delle soluzioni: Verificare se il fornitore offre la possibilità di personalizzare le soluzioni in base alle esigenze specifiche. Ogni progetto è unico e le strutture prefabbricate devono essere in grado di adattarsi a diverse configurazioni e requisiti.
- Conformità normativa: Assicurarsi che il fornitore rispetti tutte le normative di sicurezza e costruzione vigenti nel settore. Questo include il rispetto delle norme antisismiche, l’utilizzo di materiali certificati e l’adozione di procedure di controllo qualità rigorose.
Non dimenticare di fare un’attenta valutazione dei costi e dei tempi di consegna offerti dal fornitore. Considera anche la reputazione del fornitore, leggendo recensioni e richiedendo referenze da clienti precedenti. Un fornitore affidabile e di fiducia sarà in grado di fornirti tutte le informazioni necessarie per prendere una decisione informata. Prenditi il tempo necessario per valutare le opzioni a tua disposizione e scegliere il fornitore che meglio soddisfi le tue esigenze specifiche.
Infine, ricorda che la scelta del fornitore giusto per i capannoni prefabbricati in ferro è un investimento a lungo termine. Porta avanti una ricerca accurata e non esitare a consultare esperti nel settore per ottenere ulteriori consigli e raccomandazioni specifiche per il tuo progetto.
Benefici dell’utilizzo di tecnologie innovative nella costruzione di capannoni in ferro
Le tecnologie innovative stanno rivoluzionando il settore della costruzione di capannoni in ferro, offrendo una serie di benefici significativi sia per i costruttori che per i clienti finali. Questi progressi consentono di ottenere strutture più solide, efficienti e durevoli, garantendo un valore aggiunto a lungo termine. Di seguito sono elencati alcuni dei principali vantaggi derivanti dall’utilizzo di tecnologie innovative in questa area:
- Maggiore precisione: L’uso di tecnologie avanzate come la modellazione tridimensionale (BIM) e il monitoraggio in tempo reale consente di progettare e costruire capannoni in ferro con una precisione senza precedenti. Ciò garantisce una migliore aderenza ai piani e riduce notevolmente gli errori di costruzione.
- Efficacia energetica: Le tecnologie innovative consentono la progettazione di capannoni in ferro con un’alta efficienza energetica. L’utilizzo di materiali a isolamento termico avanzati e sistemi di gestione dell’energia intelligente permette di ridurre i costi operativi e di rispettare gli standard di sostenibilità ambientale.
- Velocità di costruzione: Grazie al progresso tecnologico, è possibile ridurre significativamente i tempi di costruzione dei capannoni in ferro. L’utilizzo di macchine avanzate come le gru e i robot offre una maggiore velocità e precisione nell’assemblaggio delle strutture, permettendo di rispettare stretti cronogrammi senza compromettere la qualità del lavoro.
- Adattabilità: Le tecnologie innovative consentono di progettare capannoni in ferro altamente adattabili, in grado di resistere a diverse condizioni climatiche e di soddisfare le specifiche esigenze dei clienti. L’utilizzo di software di progettazione assistita consente di personalizzare i dettagli e di ottimizzare le prestazioni delle strutture in base alle esigenze specifiche di utilizzo.
- Maggiore sicurezza: L’uso di tecnologie innovative nella costruzione di capannoni in ferro contribuisce a garantire una maggiore sicurezza sia per i lavoratori che per gli utenti finali delle strutture. L’integrazione di sistemi di rilevamento e di monitoraggio permette di identificare potenziali rischi in tempo reale, contribuendo a prevenire incidenti e migliorando gli standard di sicurezza sul cantiere.
In conclusione, l’utilizzo di tecnologie innovative nella costruzione di capannoni in ferro offre una serie di vantaggi sia in termini di qualità che di efficienza. Questi progressi consentono di realizzare strutture più precise, energeticamente efficienti, veloci da costruire, adattabili e sicure. Grazie all’adozione di queste soluzioni innovative, gli operatori del settore possono soddisfare le esigenze dei clienti e restare al passo con le sfide e le aspettative in continua evoluzione del mercato delle costruzioni in ferro.
Considerazioni sulla manutenzione e la durata dei capannoni prefabbricati in ferro
1. Importanza della manutenzione regolare:
La manutenzione regolare dei capannoni prefabbricati in ferro è di fondamentale importanza per garantirne la durata nel tempo e preservarne l’integrità strutturale. Attraverso interventi preventivi e periodici, si possono individuare eventuali segni di usura, danni o corrosione, evitando così problemi maggiori e costosi ripristini. La manutenzione regolare rappresenta dunque un investimento necessario per garantire la longevità dei capannoni.
2. Routine di pulizia e ispezione:
Per mantenere i capannoni prefabbricati in ferro in ottimo stato, è importante adottare una routine di pulizia e ispezione. Rimuovere detriti e sporcizia dalle superfici esterne e interne, inclusi tetti e pareti, può impedire l’accumulo di umidità e ridurre il rischio di corrosione. Inoltre, ispezionare regolarmente le aree critiche come le giunzioni e le viti permette di individuare tempestivamente eventuali segni di deterioramento strutturale
3. Trattamento della corrosione:
La corrosione è uno dei principali nemici dei capannoni in ferro. Per prevenirne l’insorgenza o limitarne l’avanzamento, è essenziale applicare un adeguato trattamento anticorrosione. Ciò può includere la verniciatura delle superfici metalliche con prodotti protettivi, l’applicazione di rivestimenti anti-corrosione o l’utilizzo di materiali zincati.
4. Riparazioni e sostituzioni:
Anche con una manutenzione adeguata, può essere necessario affrontare eventuali riparazioni o sostituzioni di parti dei capannoni in ferro. In presenza di danni strutturali, è importante intervenire prontamente per evitare complicazioni a lungo termine. Ciò può richiedere la sostituzione di singoli elementi, la riparazione delle superfici danneggiate o l’applicazione di rinforzi strutturali. È fondamentale affidarsi a professionisti qualificati e utilizzare materiali di alta qualità per garantire interventi duraturi e sicuri.
5. Consulenza professionale:
Per affrontare al meglio la manutenzione e garantire la durata dei capannoni prefabbricati in ferro, è consigliabile ricorrere a consulenti o specialisti nel settore. Questi professionisti possono fornire valutazioni tecniche, consigliarvi sulle migliori pratiche di manutenzione, offrire soluzioni personalizzate e persino fornire piani di manutenzione programmati. Una guida esperta può fare la differenza per preservare l’efficienza strutturale e l’estetica dei vostri capannoni nel lungo periodo.
Domande e risposte
Q: Quali sono gli approcci prefabbricati nella costruzione di capannoni in ferro?
R: Gli approcci prefabbricati nella costruzione di capannoni in ferro includono l’utilizzo di componenti preassemblati come travi, pilastri e pannelli murali che vengono realizzati in fabbrica e successivamente trasportati sul sito di costruzione per essere assemblati. Questo metodo riduce notevolmente i tempi di costruzione e la necessità di lavori in loco.
Q: Quali sono i vantaggi dell’utilizzo di approcci prefabbricati?
R: Gli approcci prefabbricati offrono diversi vantaggi. Innanzitutto, riducono il tempo necessario per completare la costruzione di un capannone in ferro, consentendo un risparmio di tempo significativo rispetto ai tradizionali metodi di costruzione. Inoltre, la prefabbricazione consente una maggiore precisione e qualità dei componenti, riducendo il rischio di errori e migliorando l’affidabilità della struttura. Infine, l’utilizzo di componenti preassemblati riduce la quantità di lavoro svolto in loco, riducendo così i costi di manodopera e la possibilità di errori durante l’assemblaggio.
Q: Quali sono i materiali utilizzati nella costruzione di capannoni in ferro prefabbricati?
R: I capannoni in ferro prefabbricati sono generalmente realizzati utilizzando travi, pilastri e pannelli murali in acciaio. L’acciaio è un materiale molto resistente che offre la robustezza necessaria per supportare le sollecitazioni e i carichi sostenuti dalla struttura. Inoltre, è anche un materiale flessibile che consente la realizzazione di design personalizzati e adattabili alle esigenze specifiche.
Q: Quali sono i passaggi principali nella costruzione di capannoni in ferro prefabbricati?
R: La costruzione di capannoni in ferro prefabbricati comprende diversi passaggi chiave. Inizialmente, vengono progettati e realizzati i componenti prefabbricati in fabbrica. Questi componenti vengono successivamente trasportati sul sito di costruzione e assemblati in base al progetto specifico. Durante l’assemblaggio, le travi e i pilastri vengono collegati utilizzando giunzioni e bulloni, mentre i pannelli murali vengono montati sulla struttura. Infine, vengono effettuati i collegamenti e l’ancoraggio alla fondazione per garantire la stabilità e la robustezza della struttura.
Q: Quali sono i possibili risparmi temporali nel processo di costruzione di capannoni in ferro prefabbricati?
R: L’utilizzo di approcci prefabbricati nella costruzione di capannoni in ferro può portare a risparmi temporali significativi. Questi includono la riduzione del tempo necessario per fabbricare i componenti in fabbrica, il trasporto efficiente dei componenti preassemblati sul sito di costruzione e l’assemblaggio rapido e accurato grazie alla compatibilità dei componenti. Questi fattori combinati riducono notevolmente il tempo di costruzione complessivo rispetto ai tradizionali metodi di costruzione in loco.
Q: Quali sono le considerazioni da tenere in mente quando si opta per l’approccio prefabbricato nella costruzione di capannoni in ferro?
R: Quando si sceglie l’approccio prefabbricato nella costruzione di capannoni in ferro, è importante considerare diversi aspetti. Ad esempio, è necessario valutare la qualità e l’affidabilità del fornitore dei componenti prefabbricati, assicurandosi che rispetti gli standard di qualità richiesti. Inoltre, è fondamentale pianificare adeguatamente i tempi di consegna dei componenti prefabbricati in modo da evitare ritardi nella costruzione. Infine, è essenziale includere nelle fasi progettuali tutti gli elementi prefabbricati necessari, garantendo una corretta integrazione con il resto della struttura.
In Conclusione
In definitiva, la costruzione di capannoni in ferro mediante approcci prefabbricati si rivela una soluzione efficace ed efficiente per ottenere un rapido edificio industriale. Attraverso l’utilizzo di strutture in acciaio prefabbricate, viene garantito un notevole risparmio di tempo, risorse economiche e operazioni on-site, consentendo così di accelerare i tempi di consegna e di massimizzare i profitti.
L’approccio prefabbricato offre numerosi vantaggi, tra cui la possibilità di personalizzare la struttura in base alle specifiche esigenze del cliente, ottenendo così una soluzione su misura che soddisfa pienamente le sue necessità. Inoltre, grazie alla capacità di anticipare la realizzazione di alcune fasi di produzione in officina, si riducono al minimo i tempi di assemblaggio in cantiere, evitando così interruzioni alla produzione e riducendo i costi complessivi.
Una delle caratteristiche più interessanti dell’utilizzo di capannoni in ferro prefabbricati è la loro resistenza e durabilità nel tempo. Lo scheletro in acciaio conferisce all’edificio una struttura robusta e affidabile, in grado di sopportare carichi pesanti e di resistere alle intemperie e agli agenti atmosferici.
È importante sottolineare come l’impiego di questa tecnologia prefabbricata rispetti le norme di sicurezza vigenti, garantendo un ambiente di lavoro sicuro e conforme alle disposizioni normative in materia.
In conclusione, la costruzione di capannoni in ferro mediante approcci prefabbricati rappresenta una soluzione vantaggiosa sotto molteplici aspetti. Il risparmio di tempo, risorse economiche e operazioni on-site permette di ottimizzare il processo costruttivo e incrementare la produttività. Grazie alla personalizzazione delle strutture, è possibile adattare l’edificio alle esigenze specifiche del cliente, garantendo un alto standard di qualità nella realizzazione.
In un contesto in cui i tempi sono preziosi e il risparmio è fondamentale, le soluzioni prefabbricate in ferro si rivelano una scelta vincente per la costruzione di capannoni industriali, garantendo efficienza, solidità e durabilità nel tempo.
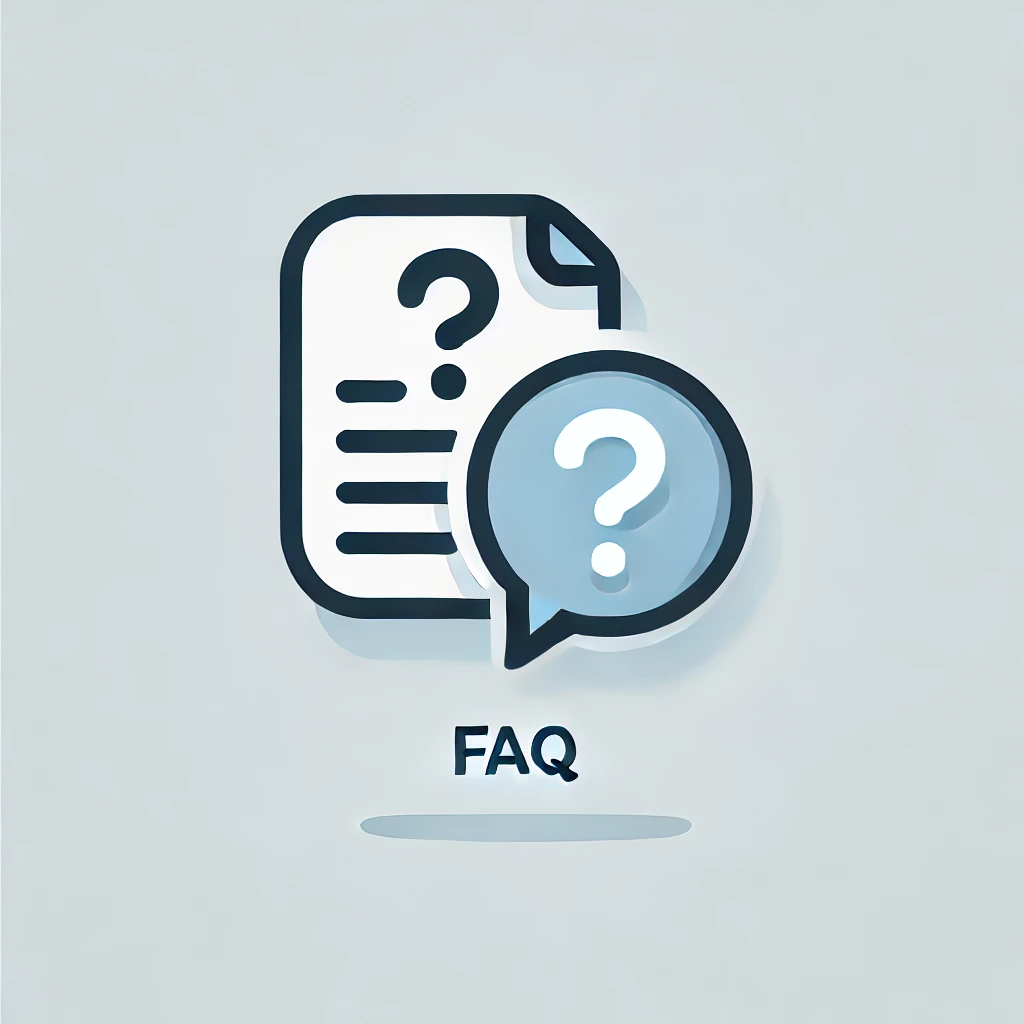
FAQ
Domande frequenti? Scopri tutte le risposte ai quesiti tecnici più comuni! Approfondisci le informazioni essenziali sulle opere metalliche e migliora la tua comprensione con soluzioni pratiche e chiare. Non lasciarti sfuggire dettagli importanti!
Il 30 maggio 2024 è entrata in vigore la nuova norma UNI EN 1090-2:2024, che porta importanti aggiornamenti e modifiche riguardanti la progettazione e la costruzione di strutture in acciaio e alluminio. Questo articolo esplorerà i contenuti principali della norma e le sue implicazioni per progettisti e costruttori.
Contenuti della Norma UNI EN 1090-2:2024
La norma UNI EN 1090-2:2024 si concentra su specifiche tecniche per la costruzione di strutture in acciaio e alluminio, coprendo vari aspetti quali:
Materiali e Componenti: Specifiche sui materiali utilizzati, compresi i requisiti di qualità e le proprietà meccaniche. Include anche dettagli sui componenti standard e sulle tolleranze accettabili.
Progettazione e Calcolo: Linee guida aggiornate per la progettazione strutturale, compresi i metodi di calcolo e le verifiche necessarie per garantire la sicurezza e la conformità alle norme europee.
Produzione e Fabbricazione: Requisiti per il processo di fabbricazione, inclusi i metodi di saldatura, taglio, foratura e assemblaggio. Vengono introdotte nuove tecniche di controllo qualità per garantire la conformità delle strutture prodotte.
Controlli e Ispezioni: Procedure dettagliate per i controlli e le ispezioni durante le varie fasi di costruzione. Questo include test non distruttivi, controlli visivi e verifiche dimensionali.
Documentazione e Tracciabilità: Norme per la gestione della documentazione tecnica e la tracciabilità dei materiali e dei componenti utilizzati. Viene enfatizzata l’importanza della corretta registrazione delle informazioni per la manutenzione futura.
Materiali e Componenti nella Norma UNI EN 1090-2:2024
Specifiche sui materiali utilizzati, compresi i requisiti di qualità e le proprietà meccaniche. Include anche dettagli sui componenti standard e sulle tolleranze accettabili.
Requisiti di Qualità dei Materiali
La norma UNI EN 1090-2:2024 stabilisce specifiche dettagliate riguardo ai materiali utilizzati nella costruzione di strutture in acciaio e alluminio. I requisiti di qualità dei materiali comprendono:
- Classificazione dei Materiali:
- Acciaio: La norma identifica diverse classi di acciaio che possono essere utilizzate, ognuna con specifiche caratteristiche meccaniche e chimiche. Le classi comuni includono acciaio al carbonio, acciaio legato e acciaio inossidabile.
- Alluminio: Analogamente, l’alluminio è classificato in diverse leghe, ognuna con proprietà uniche in termini di resistenza, durezza e resistenza alla corrosione.
- Certificazione dei Materiali:
- Certificati di Conformità: Tutti i materiali devono essere accompagnati da certificati di conformità che attestino che i materiali soddisfano i requisiti specificati. Questi certificati devono essere emessi dai fornitori dei materiali.
- Tracciabilità: È richiesta una tracciabilità completa dei materiali dalla produzione alla costruzione finale, assicurando che ogni componente possa essere rintracciato fino alla sua origine.
Proprietà Meccaniche
Le proprietà meccaniche dei materiali sono cruciali per garantire la sicurezza e la durabilità delle strutture. La norma UNI EN 1090-2:2024 specifica i seguenti requisiti:
- Resistenza alla Trazione:
- Acciaio: Devono essere rispettati i valori minimi di resistenza alla trazione, che variano a seconda della classe dell’acciaio.
- Alluminio: Analogamente, le leghe di alluminio devono soddisfare specifici requisiti di resistenza alla trazione.
- Durezza e Ductilità:
- Acciaio: La durezza e la ductilità dell’acciaio devono essere tali da garantire che i componenti possano sopportare deformazioni senza rompersi.
- Alluminio: Le leghe di alluminio devono avere una durezza adeguata per resistere all’usura e alla deformazione.
- Resistenza alla Corrosione:
- Acciaio Inossidabile: Per applicazioni in ambienti corrosivi, devono essere utilizzati tipi di acciaio inossidabile che garantiscono una resistenza adeguata alla corrosione.
- Alluminio: Le leghe di alluminio devono essere selezionate in base alla loro resistenza alla corrosione, soprattutto in applicazioni esterne o in ambienti aggressivi.
Componenti Standard e Tolleranze Accettabili
La norma UNI EN 1090-2:2024 fornisce anche linee guida per i componenti standard e le tolleranze accettabili, garantendo l’uniformità e la qualità delle strutture costruite.
- Componenti Standard:
- Bulloneria: Specifiche per bulloni, dadi e rondelle utilizzati nelle connessioni strutturali, inclusi i requisiti di resistenza e le classi di qualità.
- Profili e Sezioni: Dimensioni e forme standard per profili in acciaio e alluminio, come travi a I, H, C, e angolari.
- Piastre e Lamiere: Spessori standard per piastre e lamiere utilizzate nelle costruzioni, con requisiti di planarità e qualità della superficie.
- Tolleranze di Fabbricazione:
- Dimensioni e Forme: Tolleranze precise per le dimensioni e le forme dei componenti, assicurando che ogni pezzo si adatti correttamente durante l’assemblaggio.
- Allineamento e Posizionamento: Tolleranze per l’allineamento e il posizionamento dei componenti durante la costruzione, prevenendo problemi strutturali dovuti a errori di montaggio.
- Finiture Superficiali: Requisiti per le finiture superficiali, incluse le tolleranze per la rugosità della superficie, che influenzano la resistenza alla corrosione e l’estetica finale della struttura.
isfare i rigorosi requisiti delle normative europee.
Tabelle e Dati Numerici: UNI EN 1090-2:2024
Per fornire una comprensione chiara e dettagliata dei requisiti specifici menzionati nella norma UNI EN 1090-2:2024, di seguito sono riportate tabelle esplicative per i vari punti trattati.
1. Requisiti di Qualità dei Materiali
Acciaio
Classe di Acciaio | Resistenza alla Trazione (MPa) | Durezza (HB) | Resistenza alla Corrosione |
---|---|---|---|
S235 | 360-510 | 100-140 | Bassa |
S275 | 410-560 | 120-160 | Moderata |
S355 | 470-630 | 140-190 | Elevata |
S460 | 530-720 | 160-210 | Molto Elevata |
Alluminio
Lega di Alluminio | Resistenza alla Trazione (MPa) | Durezza (HB) | Resistenza alla Corrosione |
---|---|---|---|
6061-T6 | 310-350 | 95 | Elevata |
7075-T6 | 510-570 | 150 | Moderata |
2024-T3 | 470-510 | 120 | Bassa |
5083-H321 | 275-350 | 80 | Molto Elevata |
2. Proprietà Meccaniche
Acciaio
Proprietà Meccanica | S235 | S275 | S355 | S460 |
---|---|---|---|---|
Limite di Snervamento (MPa) | ≥235 | ≥275 | ≥355 | ≥460 |
Allungamento (%) | ≥24 | ≥22 | ≥21 | ≥18 |
Resilienza (J) | ≥27 a 20°C | ≥27 a 20°C | ≥27 a 20°C | ≥27 a 20°C |
Alluminio
Proprietà Meccanica | 6061-T6 | 7075-T6 | 2024-T3 | 5083-H321 |
---|---|---|---|---|
Limite di Snervamento (MPa) | ≥240 | ≥430 | ≥345 | ≥215 |
Allungamento (%) | ≥10 | ≥11 | ≥12 | ≥14 |
Resilienza (J) | ≥15 a 20°C | ≥15 a 20°C | ≥15 a 20°C | ≥15 a 20°C |
3. Componenti Standard e Tolleranze Accettabili
Componenti Standard
Componente | Standard | Specifiche di Qualità |
---|---|---|
Bulloneria | EN 14399 | Classe 8.8, 10.9 |
Profili | EN 10025 | S235, S275, S355 |
Piastre | EN 10029 | Classe A, B |
Lamiere | EN 10149 | Spessori 2-50 mm |
Tolleranze di Fabbricazione
Tipo di Tolleranza | Acciaio | Alluminio |
---|---|---|
Dimensioni Lineari | ±1 mm/m | ±0.5 mm/m |
Planarità | ±2 mm/m | ±1 mm/m |
Allineamento | ±1° | ±0.5° |
Rugosità Superficiale (µm) | ≤25 | ≤20 |
4. Resistenza alla Corrosione
Tipo di Ambiente | Acciaio Inossidabile | Acciaio al Carbonio con Rivestimento | Alluminio |
---|---|---|---|
Atmosferico (rurale) | 20+ anni | 15-20 anni | 20+ anni |
Atmosferico (industriale) | 15-20 anni | 10-15 anni | 15-20 anni |
Immersione in Acqua | 10-15 anni | 5-10 anni | 10-15 anni |
Queste tabelle offrono una panoramica dei requisiti e delle tolleranze specifiche per materiali e componenti secondo la norma UNI EN 1090-2:2024. Progettisti e costruttori devono assicurarsi di conformarsi a questi standard per garantire la qualità e la sicurezza delle strutture costruite.
Progettazione e Calcolo
Linee guida aggiornate per la progettazione strutturale, compresi i metodi di calcolo e le verifiche necessarie per garantire la sicurezza e la conformità alle norme europee.
Dettagli sulla Progettazione e Calcolo nella Norma UNI EN 1090-2:2024
La norma UNI EN 1090-2:2024 fornisce linee guida dettagliate per la progettazione strutturale, garantendo che le costruzioni in acciaio e alluminio rispettino i più elevati standard di sicurezza e conformità alle normative europee. Di seguito vengono spiegati i principali aspetti relativi alla progettazione e calcolo strutturale.
1. Principi Generali di Progettazione
Obiettivi della Progettazione
- Sicurezza: Garantire la resistenza e la stabilità della struttura per prevenire crolli o deformazioni eccessive.
- Durabilità: Progettare strutture che mantengano le loro prestazioni nel tempo, resistendo agli agenti atmosferici e ai carichi operativi.
- Economicità: Ottimizzare l’uso dei materiali e delle risorse per ridurre i costi di costruzione e manutenzione.
Norme di Riferimento
La norma UNI EN 1090-2:2024 si integra con altre normative europee, come:
- Eurocodici (EN 1990 – EN 1999): Serie di norme che forniscono basi comuni per la progettazione strutturale in Europa.
- EN 1090-1: Specifica i requisiti per la marcatura CE delle strutture in acciaio e alluminio.
- EN 10025: Norme per i prodotti in acciaio.
2. Metodi di Calcolo Strutturale
Analisi dei Carichi
- Carichi Permanenti (G): Peso proprio della struttura, inclusi i materiali e gli elementi permanenti.
- Carichi Variabili (Q): Carichi dovuti all’uso e occupazione, come il traffico pedonale, i veicoli, il vento, la neve, ecc.
- Carichi Eccezionali (A): Carichi dovuti a situazioni estreme, come terremoti o esplosioni.
Combinazione dei Carichi
La norma stabilisce le combinazioni di carichi che devono essere considerate nella progettazione, seguendo i principi degli Eurocodici: γG⋅G+γQ⋅Q\gamma_G \cdot G + \gamma_Q \cdot QγG⋅G+γQ⋅Q Dove γG\gamma_GγG e γQ\gamma_QγQ sono i coefficienti parziali di sicurezza.
Metodi di Analisi
- Analisi Lineare: Utilizzata per strutture dove si presume che i materiali e i componenti si comportino in modo elastico. Viene applicata principalmente per strutture con carichi moderati.
- Analisi Non Lineare: Necessaria quando i componenti strutturali si comportano in modo non lineare, come in caso di grandi deformazioni o comportamento plastico. Questo metodo è più complesso ma fornisce risultati più accurati per strutture sotto carichi estremi.
3. Verifiche Strutturali
Verifica degli Elementi Strutturali
- Resistenza alla Trazione e Compressione: Gli elementi devono essere verificati per resistere ai carichi di trazione e compressione, evitando rotture o instabilità.
- Resistenza a Flessione: Gli elementi sottoposti a momenti flettenti devono essere verificati per evitare deformazioni eccessive o collasso.
- Taglio e Torsione: Gli elementi devono essere verificati per resistere ai carichi di taglio e torsione.
Verifica della Stabilità
- Instabilità Locale: Verifica delle piastre e dei profili per prevenire l’instabilità locale, come l’inflessione delle ali delle travi.
- Instabilità Globale: Verifica della stabilità globale della struttura, assicurando che non si verifichi un collasso complessivo.
Dettagli Costruttivi
- Giunzioni: Le giunzioni devono essere progettate per garantire la trasmissione sicura dei carichi tra gli elementi. Questo include giunzioni saldate, bullonate e rivettate.
- Saldature: Le saldature devono essere eseguite secondo le specifiche della norma, con controlli di qualità per assicurare l’integrità delle giunzioni.
- Ancoraggi: Gli ancoraggi alla fondazione e ad altri elementi strutturali devono essere progettati per resistere ai carichi trasmessi.
4. Esempi di Calcolo e Tabelle
Esempio di Calcolo per una Trave in Acciaio
Supponiamo di dover calcolare una trave in acciaio S355 sottoposta a un carico uniformemente distribuito (q) e una lunghezza (L).
- Dati:
- Carico uniformemente distribuito (q): 5 kN/m
- Lunghezza della trave (L): 6 m
- Sezione della trave: IPE 300
- Calcolo del Momento Flettenete (M_max): Mmax=qâ‹…L28=5â‹…628=22.5‰kNmM_{\text{max}} = \frac{q \cdot L^2}{8} = \frac{5 \cdot 6^2}{8} = 22.5 \, \text{kNm}Mmax=8qâ‹…L2=85â‹…62=22.5kNm
- Verifica della Resistenza a Flessione: MRd=Wplâ‹…fy/γM0M_{\text{Rd}} = W_{\text{pl}} \cdot f_y / \gamma_M0MRd=Wplâ‹…fy/γM0 Dove WplW_{\text{pl}}Wpl è il modulo plastico della sezione (in questo caso per IPE 300, Wpl=1054â‹…103‰mm3W_{\text{pl}} = 1054 \cdot 10^3 \, \text{mm}^3Wpl=1054â‹…103mm3), fyf_yfy è il limite di snervamento dell’acciaio (355 MPa), e γM0\gamma_M0γM0 è il coefficiente parziale di sicurezza (1.0). MRd=1054â‹…103â‹…355/106=373.67‰kNmM_{\text{Rd}} = 1054 \cdot 10^3 \cdot 355 / 10^6 = 373.67 \, \text{kNm}MRd=1054â‹…103â‹…355/106=373.67kNm
- Conclusione: Poiché Mmax<MRdM_{\text{max}} < M_{\text{Rd}}Mmax<MRd, la trave soddisfa i requisiti di resistenza a flessione.
5. Tabelle di Consultazione
Moduli Plastici per Sezioni Standard in Acciaio (IPE)
Sezione | Modulo Plastico (W_pl, mm^3) | Peso per Metro (kg/m) |
---|---|---|
IPE 100 | 157.1 x 10^3 | 8.1 |
IPE 200 | 694.4 x 10^3 | 20.4 |
IPE 300 | 1054 x 10^3 | 36.1 |
IPE 400 | 2741 x 10^3 | 52.6 |
Coefficienti Parziali di Sicurezza (γ\gammaγ)
Carico | Coefficiente (γ\gammaγ) |
---|---|
Carico Permanente (GGG) | 1.35 |
Carico Variabile (QQQ) | 1.50 |
Carico Eccezionale (AAA) | 1.00 |
Questi dettagli e tabelle forniscono una guida pratica per la progettazione e il calcolo strutturale secondo la norma UNI EN 1090-2:2024, assicurando che tutte le strutture in acciaio e alluminio siano progettate e costruite secondo i più alti standard di sicurezza e conformità.
Produzione e Fabbricazione
Requisiti per il processo di fabbricazione, inclusi i metodi di saldatura, taglio, foratura e assemblaggio. Vengono introdotte nuove tecniche di controllo qualità per garantire la conformità delle strutture prodotte.
Dettagli sulla Produzione e Fabbricazione nella Norma UNI EN 1090-2:2024
La norma UNI EN 1090-2:2024 specifica requisiti dettagliati per il processo di fabbricazione di strutture in acciaio e alluminio, coprendo metodi di saldatura, taglio, foratura e assemblaggio. Inoltre, introduce nuove tecniche di controllo qualità per garantire la conformità delle strutture prodotte. Di seguito vengono spiegati i principali aspetti relativi alla produzione e fabbricazione.
1. Metodi di Saldatura
Processi di Saldatura
- Saldatura ad Arco (MMA, MIG/MAG, TIG): Utilizzati comunemente per saldature di precisione e di alta qualità.
- MMA (Manual Metal Arc): Adatta per saldature su acciai al carbonio e acciai legati.
- MIG/MAG (Metal Inert Gas/Metal Active Gas): Adatta per saldature di acciai, alluminio e altre leghe.
- TIG (Tungsten Inert Gas): Utilizzata per saldature di alta qualità su materiali sottili e leghe speciali.
Qualifica dei Saldatori
- Certificazioni: I saldatori devono essere certificati secondo EN ISO 9606, che definisce i requisiti per la qualifica dei saldatori.
- Procedure di Saldatura: Le procedure di saldatura devono essere qualificate secondo EN ISO 15614, che specifica i requisiti per la qualificazione delle procedure di saldatura.
Controlli e Ispezioni delle Saldature
- Controllo Visivo (VT): Ispezione visiva per rilevare difetti superficiali.
- Controllo con Liquidi Penetranti (PT): Utilizzato per rilevare difetti superficiali non visibili ad occhio nudo.
- Controllo con Ultrasuoni (UT): Utilizzato per rilevare difetti interni.
- Radiografia (RT): Utilizzata per controllare la qualità interna delle saldature.
2. Metodi di Taglio
Tecniche di Taglio
- Taglio al Plasma: Adatto per acciai al carbonio e acciai legati, offre precisione e velocità.
- Taglio Oxy-Fuel: Utilizzato per tagliare acciai al carbonio di spessori elevati.
- Taglio Laser: Adatto per acciai e alluminio, offre alta precisione e finitura di qualità.
- Taglio a Getto d’Acqua: Utilizzato per materiali che possono essere danneggiati dal calore, come alcune leghe di alluminio.
Requisiti di Qualità del Taglio
- Precisione delle Dimensioni: Le dimensioni tagliate devono rispettare le tolleranze specificate.
- Finitura dei Bordi: I bordi tagliati devono essere lisci e privi di bave o irregolarità.
- Assenza di Difetti: I tagli devono essere privi di crepe, bruciature o deformazioni.
3. Metodi di Foratura
Tecniche di Foratura
- Foratura a Trapano: Utilizzata per fori di diametro piccolo e medio.
- Punzonatura: Adatta per fori di diametro piccolo su lamiere sottili.
- Foratura CNC: Utilizzata per fori di alta precisione e per geometrie complesse.
- Perforazione con Utensili a Taglio Rotante: Utilizzata per acciai duri e leghe speciali.
Requisiti di Qualità della Foratura
- Precisione del Diametro: I fori devono rispettare le tolleranze di diametro specificate.
- Assenza di Bave: I fori devono essere privi di bave e devono avere una finitura interna liscia.
- Allineamento e Posizionamento: I fori devono essere allineati correttamente e posizionati con precisione.
4. Metodi di Assemblaggio
Tecniche di Assemblaggio
- Assemblaggio Bullonato: Utilizzato per connessioni smontabili.
- Requisiti dei Bulloni: I bulloni devono essere conformi agli standard EN 14399 (bulloni strutturali ad alta resistenza).
- Coppie di Serraggio: Le coppie di serraggio devono essere controllate e verificate per garantire una connessione sicura.
- Assemblaggio Saldato: Utilizzato per connessioni permanenti.
- Preparazione delle Superfici: Le superfici devono essere pulite e preparate secondo le specifiche per garantire una buona saldatura.
- Allineamento e Posizionamento: I componenti devono essere allineati e posizionati correttamente prima della saldatura.
5. Tecniche di Controllo Qualità
Controlli Durante la Produzione
- Ispezione delle Materie Prime: Controlli per verificare la qualità dei materiali in entrata, inclusi certificati di conformità e analisi chimiche.
- Controlli In-Process: Controlli eseguiti durante le varie fasi di produzione, come taglio, foratura, saldatura e assemblaggio.
- Controlli Finali: Ispezioni finali per verificare che il prodotto finito rispetti tutte le specifiche tecniche e i requisiti di qualità.
Documentazione e Tracciabilità
- Registrazione dei Controlli: Tutti i controlli devono essere documentati e registrati in modo accurato.
- Tracciabilità dei Materiali: Ogni componente deve essere tracciabile fino al lotto di produzione del materiale di base.
- Certificati di Conformità: I certificati di conformità devono essere rilasciati per tutte le fasi della produzione e fabbricazione, garantendo la trasparenza e la conformità alle norme.
Tabelle di Riferimento
Tipi di Saldature e Metodi di Controllo
Tipo di Saldatura | Metodo di Controllo Primario | Metodo di Controllo Secondario |
---|---|---|
MMA | VT | UT, RT |
MIG/MAG | VT | PT, UT |
TIG | VT | PT, RT |
Tolleranze di Taglio
Metodo di Taglio | Tolleranza Dimensionale (mm) | Qualità della Finitura |
---|---|---|
Plasma | ±1 | Media |
Oxy-Fuel | ±2 | Bassa |
Laser | ±0.5 | Alta |
Getto d’Acqua | ±0.3 | Molto Alta |
Tolleranze di Foratura
Metodo di Foratura | Tolleranza Diametrale (mm) | Finitura Interna |
---|---|---|
Foratura a Trapano | ±0.1 | Media |
Punzonatura | ±0.2 | Bassa |
Foratura CNC | ±0.05 | Alta |
Utensili a Taglio Rotante | ±0.1 | Alta |
Requisiti dei Bulloni per Assemblaggio
Classe di Bullone | Coppia di Serraggio (Nm) | Requisiti di Qualità |
---|---|---|
8.8 | 400-600 | Alta |
10.9 | 600-800 | Molto Alta |
Questi dettagli e tabelle offrono una guida pratica e specifica per la produzione e fabbricazione di strutture in acciaio e alluminio secondo la norma UNI EN 1090-2:2024, assicurando che tutte le fasi del processo siano conformi ai più alti standard di qualità e sicurezza.
Controlli e Ispezioni
Procedure dettagliate per i controlli e le ispezioni durante le varie fasi di costruzione. Questo include test non distruttivi, controlli visivi e verifiche dimensionali.
Dettagli sui Controlli e Ispezioni nella Norma UNI EN 1090-2:2024
La norma UNI EN 1090-2:2024 fornisce linee guida dettagliate per i controlli e le ispezioni durante le varie fasi di costruzione delle strutture in acciaio e alluminio. Questi controlli sono fondamentali per garantire la qualità e la conformità delle strutture alle specifiche tecniche. Di seguito vengono spiegati i principali aspetti relativi ai controlli e alle ispezioni.
1. Tipi di Controlli e Ispezioni
Controllo Visivo (VT)
Il controllo visivo è il metodo più semplice e diretto per verificare la qualità delle saldature e delle superfici dei componenti strutturali. Viene eseguito da personale qualificato e si concentra sulla rilevazione di difetti superficiali come crepe, porosità, inclusioni di scorie e imperfezioni della superficie.
Procedure per il Controllo Visivo:
- Preparazione delle Superfici: Le superfici devono essere pulite e prive di contaminanti per una corretta ispezione.
- Illuminazione Adeguata: L’ispezione deve essere effettuata in condizioni di luce adeguata.
- Strumenti di Misura: Utilizzo di strumenti di misura come calibri, micrometri e specchi per valutare le dimensioni e la forma dei difetti.
Test Non Distruttivi (NDT)
Controllo con Liquidi Penetranti (PT)
Questo metodo è utilizzato per rilevare difetti superficiali non visibili ad occhio nudo. Consiste nell’applicazione di un liquido penetrante sulla superficie del componente, seguito da un risciacquo e dall’applicazione di un rilevatore che rende visibili i difetti.
Procedure per il Controllo con Liquidi Penetranti:
- Applicazione del Penetrante: Applicare il liquido penetrante e lasciarlo agire per il tempo specificato.
- Rimozione del Penetrante in Eccesso: Pulire la superficie per rimuovere il penetrante in eccesso.
- Applicazione del Rivelatore: Applicare il rivelatore per evidenziare i difetti.
- Ispezione e Documentazione: Ispezionare la superficie e documentare i risultati.
Controllo con Ultrasuoni (UT)
Il controllo con ultrasuoni è utilizzato per rilevare difetti interni nei materiali. Un trasduttore ad ultrasuoni invia onde sonore nel materiale e rileva le onde riflesse dai difetti interni.
Procedure per il Controllo con Ultrasuoni:
- Preparazione della Superficie: Pulire la superficie del componente.
- Applicazione del Couplant: Applicare un gel couplant per migliorare la trasmissione delle onde sonore.
- Scansione con il Trasduttore: Muovere il trasduttore sulla superficie del componente per rilevare i difetti.
- Interpretazione dei Segnali: Analizzare i segnali riflessi per identificare e localizzare i difetti.
- Documentazione dei Risultati: Registrare i risultati dell’ispezione.
Radiografia (RT)
La radiografia utilizza raggi X o raggi gamma per esaminare l’interno dei materiali. Le differenze di densità nel materiale creano un’immagine che può essere analizzata per rilevare difetti interni.
Procedure per la Radiografia:
- Posizionamento del Campione: Posizionare il campione tra la sorgente di radiazioni e il rilevatore.
- Esposizione: Esporre il campione ai raggi X o gamma per il tempo necessario.
- Sviluppo dell’Immagine: Sviluppare l’immagine radiografica.
- Analisi dell’Immagine: Analizzare l’immagine radiografica per rilevare difetti interni.
- Documentazione dei Risultati: Registrare i risultati dell’ispezione.
2. Verifiche Dimensionali
Le verifiche dimensionali sono fondamentali per garantire che i componenti strutturali rispettino le specifiche progettuali e le tolleranze dimensionali. Queste verifiche includono misurazioni di lunghezze, diametri, angoli e planarità.
Procedure per le Verifiche Dimensionali:
- Utilizzo di Strumenti di Misura: Calibri, micrometri, laser scanner e altri strumenti di misura di precisione.
- Misurazioni di Controllo: Misurare dimensioni critiche e confrontarle con le specifiche progettuali.
- Documentazione delle Misurazioni: Registrare tutte le misurazioni e confrontarle con le tolleranze specificate.
- Correzione degli Errori: Identificare e correggere eventuali discrepanze dimensionali.
3. Frequenza dei Controlli e Ispezioni
Controlli Periodici
- Controlli Giornalieri: Verifiche visive e dimensionali di routine durante il processo di produzione.
- Controlli Settimanali: Ispezioni più dettagliate, inclusi test non distruttivi, per monitorare la qualità dei componenti.
Controlli Finali
- Ispezione Completa: Verifica finale di tutti i componenti prima dell’assemblaggio e della spedizione.
- Test di Conformità: Esecuzione di test di conformità per garantire che tutti i componenti rispettino le specifiche tecniche e le normative applicabili.
4. Documentazione e Tracciabilità
La documentazione accurata e la tracciabilità sono essenziali per dimostrare la conformità alle normative e garantire la qualità del prodotto finale.
Elementi della Documentazione:
- Rapporti di Ispezione: Documentazione dei risultati di tutte le ispezioni e controlli.
- Certificati di Conformità: Certificati che attestano la conformità dei materiali e dei componenti alle specifiche.
- Tracciabilità dei Componenti: Registrazione dei lotti di produzione e dei numeri di serie per garantire la tracciabilità completa dei componenti.
Tabelle di Riferimento
Tipi di Controlli e Frequenza Raccomandata
Tipo di Controllo | Frequenza | Metodo di Esecuzione |
---|---|---|
Controllo Visivo (VT) | Giornaliero | Ispezione Visiva Manuale |
Liquidi Penetranti (PT) | Settimanale | Applicazione di Penetranti e Rivelatori |
Ultrasuoni (UT) | Mensile | Scansione con Trasduttore |
Radiografia (RT) | Trimestrale | Esposizione a Raggi X/Gamma |
Verifiche Dimensionali | Ogni Fase Critica | Misurazioni con Strumenti di Precisione |
Tolleranze Dimensionali per Componenti Strutturali
Tipo di Componente | Tolleranza Dimensionale (mm) |
---|---|
Travi e Colonne | ±1 mm |
Piastre e Lamiere | ±0.5 mm |
Fori per Bulloni | ±0.2 mm |
Lunghezze Totali | ±2 mm |
Questi dettagli e tabelle offrono una guida pratica e specifica per i controlli e le ispezioni secondo la norma UNI EN 1090-2:2024, assicurando che tutte le fasi della costruzione di strutture in acciaio e alluminio siano conformi ai più alti standard di qualità e sicurezza.
Documentazione e Tracciabilità
Norme per la gestione della documentazione tecnica e la tracciabilità dei materiali e dei componenti utilizzati. Viene enfatizzata l’importanza della corretta registrazione delle informazioni per la manutenzione futura.
Documentazione e Tracciabilità nella Norma UNI EN 1090-2:2024
La norma UNI EN 1090-2:2024 sottolinea l’importanza della gestione accurata della documentazione tecnica e della tracciabilità dei materiali e dei componenti utilizzati nelle strutture in acciaio e alluminio. Questo è fondamentale per garantire la conformità alle normative, facilitare la manutenzione futura e assicurare la qualità complessiva delle costruzioni. Di seguito sono descritti in dettaglio i principali aspetti relativi alla documentazione e alla tracciabilità secondo la norma.
1. Gestione della Documentazione Tecnica
Tipi di Documentazione Richiesta
- Progetti e Disegni Tecnici: Dettagli completi delle strutture progettate, incluse tutte le specifiche tecniche e i calcoli strutturali.
- Specifiche dei Materiali: Documenti che indicano le proprietà e le caratteristiche dei materiali utilizzati, inclusi certificati di conformità.
- Procedure di Fabbricazione: Dettagli sui metodi di fabbricazione adottati, comprese le tecniche di saldatura, taglio, foratura e assemblaggio.
- Report di Controllo Qualità: Risultati delle ispezioni e dei test effettuati durante e dopo la produzione.
- Certificati di Collaudo: Certificati che attestano la conformità delle strutture agli standard di qualità e sicurezza previsti.
Formati e Metodi di Conservazione
- Formati Digitali: Preferiti per la facilità di archiviazione e accesso. I documenti devono essere conservati in formati standard come PDF, DWG (per disegni tecnici), e XML (per dati strutturati).
- Archiviazione Sicura: Utilizzo di sistemi di gestione documentale (DMS) per garantire la sicurezza, l’accessibilità e l’integrità dei documenti.
- Backup e Ripristino: Procedure regolari di backup per evitare la perdita di dati e garantire il ripristino in caso di incidenti.
2. Tracciabilità dei Materiali e dei Componenti
Tracciabilità dei Materiali
- Codici di Tracciabilità: Assegnazione di codici univoci a tutti i materiali utilizzati (es. lotti di produzione, numeri di colata).
- Etichettatura: Etichette chiare e resistenti applicate su ogni materiale per facilitarne l’identificazione durante tutte le fasi di produzione e montaggio.
- Registrazione dei Movimenti: Documentazione dettagliata di tutti i movimenti dei materiali dall’arrivo in cantiere fino all’installazione finale.
Tracciabilità dei Componenti
- Numeri di Serie: Assegnazione di numeri di serie univoci a tutti i componenti strutturali.
- Database di Tracciabilità: Creazione e mantenimento di un database che registra tutte le informazioni sui materiali e componenti, inclusi i dettagli di produzione, i risultati dei controlli qualità e le date di installazione.
- Tracciamento delle Modifiche: Documentazione di tutte le modifiche apportate ai componenti durante la fabbricazione e l’assemblaggio, inclusi i motivi delle modifiche e le approvazioni necessarie.
3. Importanza della Corretta Registrazione delle Informazioni
Manutenzione Futura
- Storico delle Ispezioni e delle Manutenzioni: Registrazione di tutte le ispezioni, manutenzioni e riparazioni effettuate sulle strutture.
- Piani di Manutenzione: Creazione di piani di manutenzione preventiva basati sui dati storici e sulle raccomandazioni dei produttori.
Conformità Normativa
- Audit e Verifiche: Preparazione per audit periodici e verifiche da parte delle autorità competenti attraverso una documentazione completa e accessibile.
- Tracciabilità della Conformità: Dimostrazione della conformità alle normative attraverso la tracciabilità completa dei materiali e dei componenti utilizzati.
Tabelle di Riferimento
Esempio di Tabella di Tracciabilità dei Materiali
Codice Materiale | Descrizione Materiale | Fornitore | Certificato di Conformità | Data di Arrivo | Lotto di Produzione | Note |
---|---|---|---|---|---|---|
S355-01 | Acciaio S355 | Acciaieria XYZ | Cert. n. 12345 | 01/02/2024 | Lot. n. A1001 | Uso per colonne principali |
AL6061-02 | Alluminio 6061 | Metalli ABC | Cert. n. 67890 | 05/02/2024 | Lot. n. B2002 | Uso per travi secondarie |
Esempio di Tabella di Tracciabilità dei Componenti
Numero di Serie | Tipo di Componente | Materiale | Data di Produzione | Certificato di Collaudo | Ispezioni Effettuate | Note |
---|---|---|---|---|---|---|
C1001 | Trave IPE 300 | S355 | 10/03/2024 | Cert. n. 54321 | UT, VT | Installata il 20/03/2024 |
C2002 | Piastra 20 mm | AL6061 | 15/03/2024 | Cert. n. 98765 | PT, VT | Installata il 22/03/2024 |
Esempio di Piano di Manutenzione Preventiva
Componente | Frequenza Manutenzione | Tipo di Manutenzione | Data Prossima Manutenzione | Note |
---|---|---|---|---|
Trave IPE 300 | Annuale | Ispezione Visiva, UT | 20/03/2025 | Verificare integrità strutturale |
Piastra 20 mm | Semestrale | Ispezione Visiva, PT | 22/09/2024 | Verificare corrosione |
Questi dettagli e tabelle offrono una guida pratica e specifica per la gestione della documentazione e della tracciabilità secondo la norma UNI EN 1090-2:2024, assicurando che tutte le fasi della costruzione di strutture in acciaio e alluminio siano conformi ai più alti standard di qualità e sicurezza.
Implicazioni per Progettisti
- Aggiornamento delle Competenze: I progettisti dovranno aggiornare le loro competenze e conoscenze per allinearsi ai nuovi requisiti della norma. Sarà fondamentale comprendere le nuove metodologie di calcolo e i criteri di progettazione.
- Adozione di Nuove Tecniche: La norma introduce nuove tecniche e metodi di controllo qualità che i progettisti dovranno integrare nei loro progetti. Questo comporterà un’attenzione maggiore ai dettagli e alla precisione.
- Collaborazione con i Costruttori: Una stretta collaborazione con i costruttori sarà essenziale per garantire che i progetti siano realizzabili secondo i nuovi standard. Questo richiederà una comunicazione efficace e un coordinamento continuo.
Implicazioni per Costruttori
- Adeguamento delle Procedure di Fabbricazione: I costruttori dovranno aggiornare le loro procedure di fabbricazione per conformarsi ai nuovi requisiti della norma. Questo potrebbe includere l’adozione di nuove tecnologie e attrezzature.
- Formazione del Personale: Sarà necessario formare il personale sui nuovi metodi di controllo qualità e sulle tecniche di produzione introdotte dalla norma. Questo garantirà che tutti i membri del team siano allineati con gli standard richiesti.
- Miglioramento della Documentazione: La gestione accurata della documentazione tecnica e della tracciabilità diventerà una priorità. I costruttori dovranno implementare sistemi efficaci per registrare e monitorare le informazioni relative ai materiali e ai componenti.
Conclusioni
La norma UNI EN 1090-2:2024 rappresenta un importante passo avanti nella standardizzazione della progettazione e costruzione di strutture in acciaio e alluminio. Per progettisti e costruttori, ciò comporta una necessità di aggiornamento e adattamento delle proprie pratiche e procedure. Sebbene le nuove richieste possano inizialmente rappresentare una sfida, esse offrono anche un’opportunità per migliorare la qualità e la sicurezza delle strutture costruite, garantendo al contempo una maggiore conformità agli standard europei.
Adeguarsi alla UNI EN 1090-2:2024 sarà cruciale per rimanere competitivi nel settore della costruzione e per assicurare che le strutture progettate e realizzate siano sicure, durevoli e conformi alle normative vigenti.
Puoi approfondire in modo detagliato entrando nel merito di cosa dice questo punto espresso prima: Materiali e Componenti: Specifiche sui materiali utilizzati, compresi i requisiti di qualità e le proprietà meccaniche. Include anche dettagli sui componenti standard e sulle tolleranze accettabili.
Procedura Standard per la Conformità alla Norma UNI EN 1090-2:2024
La norma UNI EN 1090-2:2024 classifica i livelli di esecuzione delle strutture in acciaio e alluminio in quattro categorie principali (EXC1, EXC2, EXC3, EXC4), ciascuna con requisiti crescenti in termini di controllo della qualità e della sicurezza. Di seguito è fornita una procedura standard dettagliata, comprensiva di requisiti numerici e tabelle per ogni livello di classificazione.
Classificazione dei Livelli di Esecuzione (EXC)
- EXC1: Strutture semplici con requisiti di sicurezza minimi (es. recinzioni, strutture temporanee).
- EXC2: Strutture comuni con requisiti di sicurezza moderati (es. edifici commerciali e industriali).
- EXC3: Strutture complesse con requisiti di sicurezza elevati (es. ponti, edifici alti).
- EXC4: Strutture critiche con requisiti di sicurezza molto elevati (es. infrastrutture strategiche).
Procedura Standard
1. Gestione della Documentazione Tecnica
Documentazione Necessaria per Tutti i Livelli (EXC1-EXC4)
- Progetti e Disegni Tecnici: Dettagli completi delle strutture progettate.
- Specifiche dei Materiali: Documenti indicanti le proprietà dei materiali.
- Procedure di Fabbricazione: Dettagli sui metodi di fabbricazione adottati.
- Report di Controllo Qualità: Risultati delle ispezioni e dei test.
- Certificati di Collaudo: Certificati di conformità agli standard di qualità.
Formati e Conservazione
- Digitale (PDF, DWG, XML): Preferiti per facilità di archiviazione.
- Backup Regolari: Procedura per evitare perdita di dati.
2. Tracciabilità dei Materiali e dei Componenti
Tracciabilità per Tutti i Livelli (EXC1-EXC4)
- Codici di Tracciabilità: Codici univoci per tutti i materiali.
- Etichettatura Chiara: Etichette applicate su ogni materiale.
- Registrazione dei Movimenti: Documentazione dettagliata di tutti i movimenti dei materiali.
Esempio di Tabella di Tracciabilità
Codice Materiale | Descrizione Materiale | Fornitore | Certificato di Conformità | Data di Arrivo | Lotto di Produzione | Note |
---|---|---|---|---|---|---|
S355-01 | Acciaio S355 | XYZ | Cert. n. 12345 | 01/02/2024 | Lot. n. A1001 | Uso per colonne principali |
3. Produzione e Fabbricazione
Requisiti di Produzione per Livelli EXC
Livello EXC | Saldatura | Taglio | Foratura | Assemblaggio |
---|---|---|---|---|
EXC1 | MMA, controlli visivi | Taglio Oxy-Fuel, ±2 mm | Foratura a Trapano, ±0.2 mm | Bullonato, coppia standard |
EXC2 | MIG/MAG, PT | Taglio Plasma, ±1 mm | Foratura CNC, ±0.1 mm | Saldato, prep. standard |
EXC3 | TIG, UT, PT | Taglio Laser, ±0.5 mm | Foratura CNC, ±0.05 mm | Saldato, prep. accurata |
EXC4 | TIG, UT, RT | Taglio Laser, ±0.3 mm | Foratura CNC, ±0.02 mm | Saldato, prep. alta qualità |
4. Controlli e Ispezioni
Controlli e Ispezioni per Livelli EXC
Livello EXC | Controlli Visivi (VT) | Liquidi Penetranti (PT) | Ultrasuoni (UT) | Radiografia (RT) |
---|---|---|---|---|
EXC1 | Ogni giorno | – | – | – |
EXC2 | Ogni settimana | Mensile | – | – |
EXC3 | Ogni giorno | Settimana | Mensile | Trimestrale |
EXC4 | Ogni giorno | Settimana | Settimana | Mensile |
Esempio di Tabella di Controlli
Tipo di Controllo | Frequenza | Metodo di Esecuzione | Note |
---|---|---|---|
Controllo Visivo | Giornaliero | Ispezione Visiva Manuale | Verifica difetti superficiali |
Liquidi Penetranti | Settimanale | Applicazione PT | Rilevamento difetti superficiali non visibili |
Ultrasuoni | Mensile | Scansione con UT | Rilevamento difetti interni |
Radiografia | Trimestrale | Esposizione RT | Rilevamento difetti interni |
5. Verifiche Dimensionali
Verifiche Dimensionali per Livelli EXC
Livello EXC | Precisione Dimensionale | Finitura dei Bordi | Allineamento |
---|---|---|---|
EXC1 | ±2 mm | Media | ±2° |
EXC2 | ±1 mm | Buona | ±1° |
EXC3 | ±0.5 mm | Ottima | ±0.5° |
EXC4 | ±0.3 mm | Eccellente | ±0.2° |
Esempio di Tabella di Verifiche Dimensionali
Componente | Tolleranza Dimensionale (mm) | Finitura Interna | Allineamento |
---|---|---|---|
Trave IPE 300 | ±1 mm | Media | ±1° |
Piastra 20 mm | ±0.5 mm | Ottima | ±0.5° |
6. Manutenzione e Conformità
Piani di Manutenzione Preventiva
Componente | Frequenza Manutenzione | Tipo di Manutenzione | Data Prossima Manutenzione | Note |
---|---|---|---|---|
Trave IPE 300 | Annuale | Ispezione Visiva, UT | 20/03/2025 | Verificare integrità strutturale |
Piastra 20 mm | Semestrale | Ispezione Visiva, PT | 22/09/2024 | Verificare corrosione |
7. Documentazione della Manutenzione
Registro di Manutenzione
Data | Componente | Tipo di Manutenzione | Descrizione | Tecnico | Note |
---|---|---|---|---|---|
20/03/2024 | Trave IPE 300 | Ispezione Visiva | Nessun difetto rilevato | Mario Rossi | – |
22/09/2024 | Piastra 20 mm | Ispezione PT | Corrosione lieve rilevata | Luigi Bianchi | Corrosione trattata |
Questa procedura standard fornisce una guida completa per garantire la conformità alla norma UNI EN 1090-2:2024, considerando i vari livelli di classificazione EXC. Assicura che tutte le fasi della produzione, fabbricazione, controllo, ispezione e manutenzione delle strutture in acciaio e alluminio siano eseguite secondo i più alti standard di qualità e sicurezza.
Conclusioni
La norma UNI EN 1090-2:2024 rappresenta un importante aggiornamento nelle specifiche per materiali e componenti nelle costruzioni in acciaio e alluminio. Per progettisti e costruttori, è essenziale comprendere e applicare queste specifiche per garantire la conformità, la sicurezza e la durabilità delle strutture. L’attenzione ai dettagli nei materiali, alle proprietà meccaniche e alle tolleranze di fabbricazione contribuirà a migliorare la qualità complessiva delle costruzioni e a soddisfare i rigorosi requisiti delle normative europee.
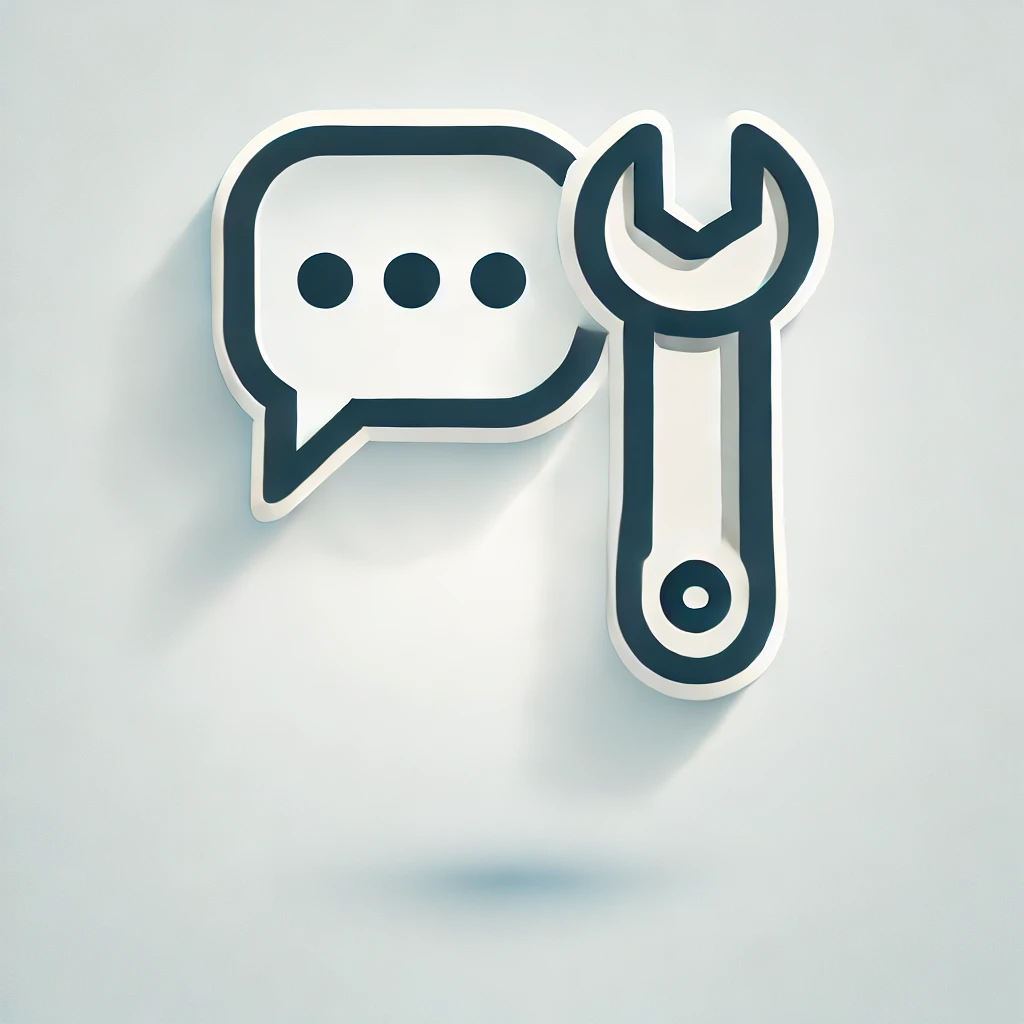
"Hai un'opinione tecnica o una domanda specifica? Non esitare, lascia un commento! La tua esperienza può arricchire la discussione e aiutare altri professionisti a trovare soluzioni. Condividi il tuo punto di vista!"
Partecipa!
Commenti