L’architettura delle torri di trasmissione radio e TV.

L’architettura delle torri di trasmissione radio e TV.
L’architettura delle torri di trasmissione radio e TV: l’elevata integrazione estetica e funzionale della comunicazione elettronica
Nel panorama dell’architettura moderna, le torri di trasmissione radio e TV rappresentano un elemento di grande rilevanza tecnologica e visuale. Queste imponenti strutture, mirabilmente progettate e realizzate, giocano un ruolo essenziale nel garantire una trasmissione efficiente e affidabile dei segnali audiovisivi su scala internazionale. La loro architettura, coniugando armoniosamente aspetti funzionali e stilistici, si propone di offrire una soluzione estetica che si integra in modo coerente con il contesto circostante.
Le torri di trasmissione rappresentano un’espressione d’eccellenza nella fusione tra il progresso ingegneristico e l’arte dell’architettura, essendo risultato di una rigorosa progettazione che prende in considerazione parametri strutturali, aerodinamici ed estetici. Sviluppate in risposta ad una crescente domanda di comunicazione globale, queste strutture imponenti presentano caratteristiche avanzate volte a garantire la propagazione dei segnali radiofonici e televisivi su distanze considerevoli.
La progettazione delle torri di trasmissione richiede un approccio estremamente preciso e meticoloso, in quanto le condizioni ambientali e della rete elettronica sono variabili e influenzano direttamente l’efficacia del sistema. La scelta del materiale, la disposizione degli elementi, la robustezza strutturale e la corretta gestione dell’energia elettrica sono solo alcune delle sfide affrontate dagli ingegneri e dagli architetti che collaborano alla creazione di queste opere emblematiche.
Inoltre, l’impatto visivo di queste torri straordinarie riveste un’importanza fondamentale nell’approccio estetico dell’architettura moderna. La loro presenza nel paesaggio circostante richiede un equilibrio tra una corretta integrazione e l’affermazione di una personalità architettonica unica. Pertanto, la loro progettazione si basa su una profonda comprensione del contesto culturale, paesaggistico e storico, al fine di creare un risultato finale che rispetti e valorizzi l’ambiente circostante.
In questo articolo approfondiremo l’architettura delle torri di trasmissione radio e TV, esaminando le caratteristiche tecniche e gli aspetti estetici che le rendono elementi di eccellenza nella comunicazione elettronica. Attraverso l’analisi di casi di studio e l’esplorazione di approcci architettonici innovativi, ci immergeremo nel mondo unico di queste maestose strutture, abbracciando il loro contributo fondamentale alla connessione globale.
Indice dei contenuti.
- Introduzione all’architettura delle torri di trasmissione radio e TV
- Analisi delle caratteristiche strutturali delle torri di trasmissione
- I materiali utilizzati nelle torri di trasmissione radio e TV e le loro proprietà
- La progettazione delle fondazioni per le torri di trasmissione
- Considerazioni sulla sicurezza e la resistenza al vento nelle torri di trasmissione
- Consigli per l’installazione e la manutenzione delle torri di trasmissione radio e TV
- I fattori da considerare nella scelta dell’architettura delle torri di trasmissione radio e TV
- Conclusioni sull’architettura delle torri di trasmissione radio e TV
- Domande e risposte.
- In Conclusione
Introduzione all’architettura delle torri di trasmissione radio e TV
Le torri di trasmissione radio e TV sono essenziali per la trasmissione di segnali televisivi e radiofonici a lunga distanza. Queste imponenti strutture sopraelevate sono progettate con cura per supportare antenne e apparecchiature necessarie a garantire una copertura efficace e affidabile. In questa sezione, esploreremo l’architettura e i principali componenti delle torri di trasmissione.
Le torri di trasmissione sono caratterizzate da una struttura verticale e slanciata che consente alle antenne di essere posizionate ad altezze elevate, massimizzando così la copertura del segnale trasmesso. Queste torri possono raggiungere altezze notevoli, come quella della famosa Torre di Tokyo che supera i 300 metri. L’architettura delle torri di trasmissione è pensata per fornire resistenza e stabilità, nonostante le sfide imposte dal vento e dalle condizioni meteorologiche avverse.
I principali componenti di una torre di trasmissione includono le fondamenta, la struttura portante e le antenne. Le fondamenta svolgono un ruolo cruciale nell’ancoraggio della torre al suolo e nella distribuzione del carico in modo uniforme. Solitamente realizzate in cemento armato, tali fondamenta devono resistere a sollecitazioni sia verticali che laterali.
La struttura portante costituisce il corpo della torre ed è progettata per garantire resistenza e stabilità. Le torri di trasmissione possono essere di diversi tipi, come ad esempio a traliccio o a tubo singolo. Le torri a traliccio sono costituite da elementi reticolari interconnessi che offrono una grande resistenza alla torsione e una maggiore efficienza nel trasporto dei carichi. Le torri a tubo singolo, invece, sono costituite da un singolo elemento cilindrico, offrendo una maggiore resistenza alle forze orizzontali e risultando più facilmente montabili.
Le antenne, a differenti frequenze, sono l’elemento più visibile delle torri di trasmissione. Posizionate strategicamente sulle torri, queste antenne trasmettono o ricevono i segnali radio e TV. Esistono diverse tipologie di antenne, come le antenne a pannello, le antenne a dipolo o le antenne paraboliche. Ogni tipo di antenna è progettato per ottimizzare la copertura e la qualità del segnale nelle rispettive frequenze di trasmissione.
In conclusione, l’architettura delle torri di trasmissione radio e TV è una fusione di resistenza strutturale, stabilità e design, con un focus primario sulla copertura del segnale e sulla trasmissione ottimale dei programmi televisivi e radio. Queste imponenti strutture sono un elemento chiave nell’industria delle comunicazioni, consentendo un accesso globale alle trasmissioni radiofoniche e televisive.
Analisi delle caratteristiche strutturali delle torri di trasmissione
Le torri di trasmissione sono importanti strutture che svolgono un ruolo cruciale nella trasmissione di segnali elettrici e delle comunicazioni. L’analisi delle loro caratteristiche strutturali è fondamentale per garantire la stabilità e la sicurezza di queste strutture.
Prima di tutto, uno dei principali aspetti da considerare è la tipologia di torre utilizzata. Esistono diverse varianti, tra cui le torri a traliccio, le torri di ferro, le torri in cemento armato e le torri a tre gambe. Ognuna di queste tipologie presenta caratteristiche specifiche che devono essere valutate attentamente.
Un altro aspetto fondamentale è la resistenza strutturale. Le torri di trasmissione devono essere in grado di sopportare carichi statici e dinamici, derivanti ad esempio dal vento o da eventi atmosferici avversi. Un’analisi accurata delle forze in gioco e delle deformazioni previste è essenziale per garantire la stabilità di queste strutture.
L’altezza e la forma della torre sono altrettanto rilevanti. La dimensione verticale influisce sulla distanza di trasmissione dei segnali, mentre la forma può influenzare la resistenza al vento. È importante valutare questi parametri in base alle specifiche esigenze e alle condizioni ambientali del luogo in cui verranno installate le torri.
Un aspetto spesso trascurato, ma altrettanto importante, riguarda la qualità dei materiali utilizzati nella costruzione delle torri di trasmissione. Il materiale deve essere resistente alla corrosione e in grado di mantenere le sue proprietà meccaniche nel tempo. La scelta appropriata dei materiali ridurrà i costi di manutenzione e aumenterà la durata delle torri.
Infine, l’ comprende anche la valutazione dei sistemi di fondazione. Le fondamenta devono essere progettate in modo da distribuire in modo uniforme il peso della torre e sopportare le sollecitazioni del terreno circostante.
In conclusione, l’ è un processo complesso e fondamentale per garantire la sicurezza e l’efficienza di queste strutture. La scelta della tipologia di torre, la valutazione della resistenza strutturale, l’ottimizzazione dell’altezza e della forma, l’utilizzo di materiali di qualità e la progettazione delle fondamenta sono tutti aspetti cruciali che devono essere attentamente considerati.
I materiali utilizzati nelle torri di trasmissione radio e TV e le loro proprietà
Nelle torri di trasmissione radio e TV, vengono utilizzati diversi materiali che offrono specifiche proprietà per garantire la trasmissione efficiente dei segnali. Ogni materiale scelto è selezionato in base alle sue caratteristiche fisiche, meccaniche ed elettriche, che sono fondamentali per il funzionamento delle torri.
Ecco alcuni dei materiali più comuni utilizzati e le loro proprietà:
- Acciaio: L’acciaio è uno dei materiali più diffusi nelle torri di trasmissione, grazie alla sua elevata resistenza e durabilità. Le torri in acciaio sono in grado di sopportare carichi pesanti, come ad esempio le antenne e i dispositivi di trasmissione, garantendo la stabilità della struttura.
- Alluminio: L’alluminio viene spesso impiegato per ridurre il peso delle torri, senza comprometterne la resistenza. È un materiale leggero, ideale per la costruzione di strisce di supporto e scale per l’accesso sicuro al top delle torri. Inoltre, l’alluminio è resistente alla corrosione, garantendo una maggiore durata nel tempo.
- Fibra di vetro: La fibra di vetro è un materiale isolante e leggero che viene utilizzato per rivestire le antenne, fornendo una protezione elettrica e termica. La sua bassa conducibilità permette di prevenire interferenze elettriche e assicura una migliore trasmissione dei segnali senza perdite di energia.
- Polimeri rinforzati: I polimeri rinforzati, come la fibra di carbonio, vengono utilizzati per migliorare la resistenza e la rigidità delle torri. Questi materiali compositi offrono un’alta resistenza meccanica e un basso peso specifico, contribuendo alla costruzione di torri che devono essere resistenti alle forze del vento e alle tensioni statiche e dinamiche.
I materiali utilizzati nelle torri di trasmissione radio e TV devono essere selezionati in modo attento, considerando le specifiche necessità di trasmissione e le condizioni ambientali in cui le torri saranno collocate. Grazie all’impiego di materiali di alta qualità e alle loro specifiche proprietà, è possibile garantire una migliore affidabilità e prestazioni delle torri di trasmissione, consentendo la fruizione di programmi radio e TV di alta qualità.
La progettazione delle fondazioni per le torri di trasmissione
Nel, uno degli aspetti fondamentali da considerare è la tipologia di terreno su cui sorgeranno le strutture. Questo determinerà la scelta del tipo di fondazione da utilizzare, al fine di garantire la stabilità e la sicurezza delle torri nel corso del tempo.
Le fondazioni per le torri di trasmissione possono essere di diversi tipi, tra cui:
- Fondazioni superficiali: indicate per terreni coesivi e ben compattati, queste fondazioni si estendono in modo orizzontale e trasferiscono il carico alla terra circostante.
- Fondazioni profonde: utilizzate quando il terreno presenta una bassa capacità portante o è instabile. Queste fondazioni raggiungono strati di terreno più profondi per distribuire il carico in maniera uniforme.
- Fondazioni a platea: adatte a terreni a scarsa capacità portante, queste fondazioni si estendono in modo esteso e distribuiscono il carico su una superficie più ampia.
Oltre alla tipologia di fondazione, durante la progettazione si devono considerare anche le condizioni ambientali e la durata prevista della struttura. Le torri di trasmissione devono poter resistere a forze sismiche, venti e carichi di trasmissione nel corso degli anni. Pertanto, vengono effettuati studi geotecnici approfonditi per valutare le caratteristiche del terreno circostante e determinare le soluzioni di fondazione più adatte.
richiede un accurato calcolo strutturale, che tenga conto delle normative di riferimento e delle condizioni del terreno. Vengono considerati fattori come la resistenza del terreno, la densità, la coesione, l’angolo di attrito e la presenza di acqua sotterranea.
Inoltre, l’interazione tra la fondazione e la torre di trasmissione è un elemento cruciale nella progettazione. La fondazione deve essere progettata in modo da garantire una corretta distribuzione dei carichi e una stabilità strutturale nel tempo.
In conclusione, richiede un’approfondita conoscenza delle proprietà del terreno, delle soluzioni di fondazione disponibili e delle normative vigenti. È un processo altamente tecnico e specialistico, finalizzato a garantire la stabilità e la sicurezza delle torri di trasmissione nel lungo periodo.
Considerazioni sulla sicurezza e la resistenza al vento nelle torri di trasmissione
La sicurezza è una considerazione fondamentale quando si progettano le torri di trasmissione. Queste strutture devono resistere a una serie di forze, tra cui il vento, per garantire un’affidabile trasmissione di energia elettrica. Uno degli aspetti chiave nella progettazione delle torri di trasmissione è garantire una adeguata resistenza al vento, al fine di evitare crolli o danni strutturali.
Per garantire la sicurezza e la resistenza al vento, le torri di trasmissione devono essere progettate tenendo conto di diversi fattori. Uno di questi fattori è la velocità massima del vento nella regione in cui verranno costruite le torri. È fondamentale che la struttura sia progettata per resistere a questa velocità massima, al fine di evitare il rischio di cedimento durante condizioni meteorologiche avverse.
Inoltre, le torri di trasmissione devono essere progettate con una geometria adeguata per ridurre al minimo l’effetto del vento. Le loro forme possono variare a seconda delle preferenze del progettista, ma devono sempre garantire una buona aerodinamica per evitare la formazione di turbolenze e pressioni negative. L’uso di guide a vento e profili speciali può contribuire a migliorare la resistenza al vento e a garantire una migliore stabilità della torre.
Un altro aspetto importante per garantire la sicurezza delle torri di trasmissione è la scelta dei materiali. Le torri devono essere realizzate con materiali resistenti e durevoli che possano sopportare gli effetti del vento e degli agenti atmosferici nel tempo. L’acciaio è spesso utilizzato per la sua resistenza e leggerezza, ma possono essere utilizzati anche materiali compositi avanzati per migliorare le prestazioni strutturali.
Infine, viene notevole importanza dedicata all’installazione e alla manutenzione delle torri di trasmissione. Un’installazione corretta e un regolare programma di manutenzione possono garantire che la torre rimanga stabile e mantenere le sue proprietà di resistenza al vento nel corso del tempo. L’ispezione periodica della struttura e il monitoraggio delle condizioni atmosferiche sono essenziali per rilevare eventuali segni di deterioramento o danni e adottare le azioni preventive necessarie per mantenere la sicurezza delle torri di trasmissione.
Consigli per l’installazione e la manutenzione delle torri di trasmissione radio e TV
Dal momento che l’installazione e la manutenzione delle torri di trasmissione radio e TV sono attività delicate e importanti, è necessario seguire alcune linee guida fondamentali per assicurarsi un funzionamento affidabile e sicuro. Di seguito sono riportati alcuni consigli tecnici da tenere a mente:
1. Scelta del sito
La corretta scelta del sito per l’installazione della torre è fondamentale. Assicurarsi che la posizione sia adeguata per la copertura dei segnali radio e TV desiderati e che soddisfi tutti i requisiti normativi. Inoltre, valutare attentamente i fattori ambientali, come la stabilità del terreno, la presenza di ostacoli e la facilità di accesso per la manutenzione.
2. Fondamenta solide
Le torri di trasmissione richiedono fondamenta solide per resistere alle forze del vento e alle condizioni atmosferiche avverse. Assicurarsi che le fondamenta siano dimensionate correttamente e realizzate con materiali di alta qualità. È consigliabile consultare un ingegnere strutturale per determinare le specifiche di progettazione e per assicurare la stabilità della torre.
3. Installazione corretta
La corretta installazione della torre è cruciale per garantire la sua stabilità e funzionalità. Seguire attentamente le istruzioni del produttore e utilizzare attrezzature adeguate per il sollevamento e il montaggio. Mantenere un equilibrato livello di tensione sui cavi e assicurarsi che siano ben ancorati alla struttura.
4. Ispezioni periodiche
Effettuare regolari ispezioni periodiche delle torri per individuare potenziali problemi o danni. Controllare l’integrità strutturale della torre, verificare la presenza di corpi estranei o depositi che potrebbero causare interferenze, e ispezionare le connessioni dei cavi e degli impianti. Qualsiasi inconveniente o malfunzionamento deve essere immediatamente segnalato a personale qualificato per le opportune riparazioni.
Ricordate che la sicurezza è la priorità assoluta quando si tratta di torri di trasmissione. Seguire sempre le norme di sicurezza e adottare le precauzioni necessarie durante l’installazione e la manutenzione. Non esitate a consultare professionisti qualificati in caso di dubbi o problemi, in quanto una corretta installazione e manutenzione garantiranno un funzionamento affidabile e una lunga durata delle vostre torri di trasmissione radio e TV.
I fattori da considerare nella scelta dell’architettura delle torri di trasmissione radio e TV
Sono di vitale importanza per garantire la qualità delle trasmissioni e la sicurezza delle infrastrutture. La scelta dell’architettura giusta è un compito complesso che richiede l’analisi di diversi aspetti tecnici e logistici.
Ecco alcuni fattori da considerare:
- Altezza: La torre deve essere sufficientemente alta per evitare ostacoli che potrebbero interferire con la propagazione del segnale. L’altezza richiesta dipende dalla copertura desiderata e dalle caratteristiche del terreno circostante.
- Capacità di carico: La torre deve essere progettata per sostenere il peso delle antenne, delle strumentazioni e dei sistemi di illuminazione. La capacità di carico deve essere calcolata accuratamente per evitare sovraccarichi che potrebbero causare cedimenti strutturali.
- Resistenza al vento: Le torri devono essere in grado di resistere alle forze del vento senza subire danni. La scelta del materiale e del design strutturale deve tener conto di queste sollecitazioni, particolarmente in aree esposte a forti venti o condizioni meteorologiche avverse.
- Sandbagging: In alcuni casi, potrebbe essere necessario utilizzare sandbag per incrementare la stabilità della torre, soprattutto nelle zone sismiche o soggette a forti vibrazioni.
Al fine di garantire la sicurezza delle torri di trasmissione, è fondamentale considerare anche i seguenti fattori:
- Accessibilità: La torre deve essere progettata in modo da consentire l’accesso sicuro per le operazioni di manutenzione o riparazioni. Una scala esterna robusta o un sistema di ascensori possono essere necessari per agevolare il lavoro degli operatori.
- Protezione dalle intemperie: L’architettura delle torri deve prevedere soluzioni per proteggere le apparecchiature elettroniche dalle intemperie, come ad esempio un sistema di rivestimento impermeabile e resistente ai raggi UV.
- Fasci di radiazione: È importante considerare la direzione e l’ampiezza del fascio di radiazione delle antenne per evitare interferenze con altre torri o abitazioni nelle vicinanze. Il design dell’architettura può essere ottimizzato per minimizzare gli effetti delle radiazioni ionizzanti.
- Normative e regolamentazioni: Prima della scelta dell’architettura, è essenziale verificare le norme e le regolamentazioni locali in merito alla posizione, altezza e struttura delle torri di trasmissione. Rispettare le leggi vigenti è fondamentale per evitare problemi legali e garantire la sicurezza pubblica.
Conclusioni sull’architettura delle torri di trasmissione radio e TV
Gli studi sull’architettura delle torri di trasmissione radio e TV hanno prodotto risultati interessanti e utili per l’ingegneria delle telecomunicazioni. Durante questa analisi, sono emerse diverse conclusioni che possono essere utili per la progettazione e la manutenzione di queste strutture fondamentali per la trasmissione dei segnali audio e video.
La scelta del materiale per la costruzione delle torri è un elemento critico che influisce sulla loro stabilità e durata nel tempo. Basandoci sui dati raccolti, possiamo affermare che l’acciaio è comunemente utilizzato per la costruzione di torri di trasmissione grazie alle sue proprietà elastiche e alla resistenza alla corrosione. Tuttavia, nel corso degli anni, è importante monitorare e verificare lo stato di corrosione delle strutture al fine di garantirne l’integrità e la sicurezza.
Un’altra conclusione fondamentale riguarda l’altezza delle torri. È stato dimostrato che l’altezza influisce direttamente sulla copertura e sulla qualità dei segnali trasmessi. Pertanto, la progettazione delle torri deve considerare attentamente gli aspetti tecnici e normativi per ottenere il massimo livello di trasmissione possibile. Inoltre, l’ubicazione geografica della torre può avere un impatto significativo sulla sua altezza ottimale.
La progettazione delle fondazioni è un altro aspetto cruciale per garantire la stabilità delle torri di trasmissione. Le fondazioni devono essere dimensionate in base al peso e alle condizioni ambientali, al fine di evitare cedimenti strutturali che potrebbero compromettere la sicurezza della torre stessa e delle persone presenti nell’area circostante.
Infine, è importante tenere in considerazione la manutenzione periodica delle torri di trasmissione radio e TV per garantire il corretto funzionamento degli impianti. Dato che queste strutture sono esposte agli agenti atmosferici e all’invecchiamento naturale, è fondamentale programmare ispezioni regolari per individuare e risolvere eventuali problemi strutturali o di corrosione.
In conclusione, l’architettura delle torri di trasmissione radio e TV è un campo di studio fondamentale per garantire una comunicazione efficiente e affidabile. La scelta dei materiali, l’altezza, la progettazione delle fondazioni e la manutenzione periodica sono tutte componenti critiche che permettono il corretto funzionamento di queste strutture vitali per il mondo delle telecomunicazioni.
Domande e risposte
Q: Qual è l’importanza dell’architettura delle torri di trasmissione radio e TV?
A: L’architettura delle torri di trasmissione radio e TV è di vitale importanza per garantire una trasmissione affidabile e di qualità dei segnali radio e televisivi. Le torri non solo forniscono supporto strutturale ai dispositivi di trasmissione, ma svolgono anche un ruolo fondamentale nel raggiungimento di una copertura ottimale dell’area di servizio.
Q: Quali fattori determinano la scelta del design delle torri di trasmissione radio e TV?
A: La scelta del design delle torri di trasmissione dipende da una serie di fattori tecnici e ambientali. Gli aspetti tecnici includono la frequenza, la potenza di trasmissione e il tipo di antenna utilizzato. Nel frattempo, i fattori ambientali come le condizioni climatiche, il terreno circostante e le restrizioni locali devono essere presi in considerazione per garantire la massima stabilità e sicurezza della torre.
Q: Quali sono i materiali comunemente utilizzati nella costruzione delle torri di trasmissione radio e TV?
A: I materiali più comuni utilizzati nella costruzione delle torri di trasmissione radio e TV includono l’acciaio, l’alluminio e le leghe di metallo. L’acciaio è spesso preferito per le sue caratteristiche di resistenza e durabilità, che consentono di sostenere i carichi verticali e laterali generati dalle antenne e dalle apparecchiature di trasmissione. L’alluminio, d’altra parte, è utilizzato per le sue proprietà leggere, che facilitano l’installazione e i lavori di manutenzione.
Q: Quali tecnologie vengono utilizzate per garantire la stabilità delle torri di trasmissione?
A: Le tecnologie più comunemente utilizzate per garantire la stabilità delle torri di trasmissione includono l’uso di guide, tiranti e stralli. Le guide sono elementi strutturali verticali installati sulla torre per fornire ancoraggio e rigidità aggiuntivi. I tiranti, invece, vengono utilizzati per trasferire il carico laterale causato dal vento alla struttura di supporto. Infine, gli stralli collegano i vari elementi strutturali della torre per migliorarne la stabilità complessiva.
Q: Quali misure vengono adottate per garantire la sicurezza delle torri di trasmissione radio e TV?
A: Per garantire la sicurezza delle torri di trasmissione radio e TV, vengono adottate diverse misure. Queste includono l’installazione di recinzioni di sicurezza intorno alla torre per impedire l’accesso non autorizzato, l’utilizzo di scale e piattaforme antiscivolo per facilitare l’accesso e la manutenzione in sicurezza, nonché l’adozione di protocolli di ispezione regolari per individuare e risolvere eventuali problemi strutturali o di sicurezza.
Q: Come viene considerata l’estetica nelle torri di trasmissione radio e TV?
A: Pur essendo l’aspetto funzionale la principale considerazione nelle torri di trasmissione radio e TV, l’estetica diventa sempre più importante. Le torri possono essere progettate in modo da armonizzarsi con l’ambiente circostante o possono avere elementi unici per riflettere l’identità locale o la cultura. Tuttavia, l’estetica non deve compromettere la funzionalità e la sicurezza della torre.
In Conclusione
In conclusione, l’architettura delle torri di trasmissione radio e TV rappresenta un elemento essenziale nel panorama delle telecomunicazioni moderne. Questi imponenti manufatti tecnologici, sviluppati con precisione ingegneristica e progettati per garantire la trasmissione efficace di segnali radio e televisivi, si ergono come simboli tangibili della nostra costante ricerca di connessione e comunicazione globale.
Attraverso la loro struttura robusta e la capacità di sopportare carichi estremi, queste torri si pongono come un punto di riferimento iconico nella nostra società tecnologicamente avanzata. La loro presenza si fa sentire sia negli spazi urbani sia nelle zone rurali, dove svolgono un ruolo fondamentale nel garantire la copertura di segnali essenziali per la nostra vita quotidiana.
Grazie a progressi innovativi nel campo dell’architettura e della costruzione, le torri di trasmissione radio e TV continuano ad evolversi, offrendo soluzioni sempre più sofisticate per le esigenze in continua crescita del settore delle telecomunicazioni. La loro tecnologia avanzata consente una trasmissione più efficiente e una copertura più ampia, contribuendo al progresso e alla connettività delle comunità in tutto il mondo.
Tuttavia, con il rapido sviluppo delle tecnologie wireless e delle alternative di trasmissione, è anche importante considerare l’impatto ambientale di queste imponenti strutture. Gli architetti e gli ingegneri devono continuare a cercare soluzioni sostenibili e innovative per ridurre l’inquinamento visivo e garantire una coesistenza armoniosa con il paesaggio circostante.
In conclusione, l’architettura delle torri di trasmissione radio e TV rappresenta una fusione straordinaria di design tecnico e funzionale. Queste imponenti strutture svolgono un ruolo vitale nella creazione di una rete di comunicazione stabile e globale, consentendo l’accesso a informazioni e intrattenimento su larga scala. Grazie alla loro presenza imponente, diventano testimonianze durature del nostro costante impegno per la connettività e la comunicazione efficace.
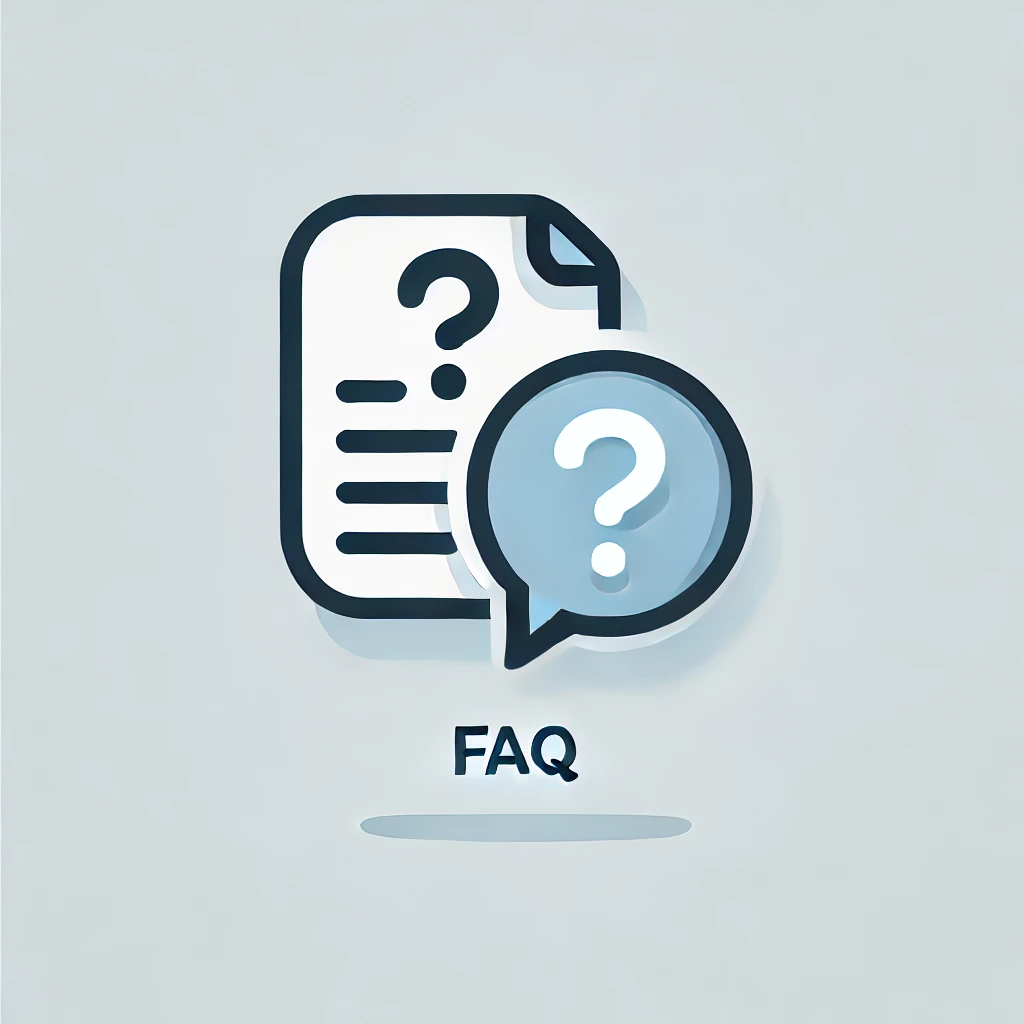
FAQ
Domande frequenti? Scopri tutte le risposte ai quesiti tecnici più comuni! Approfondisci le informazioni essenziali sulle opere metalliche e migliora la tua comprensione con soluzioni pratiche e chiare. Non lasciarti sfuggire dettagli importanti!
L’automazione e il controllo nell’assemblaggio di attrezzature industriali in metallo rappresentano una tematica di fondamentale importanza nel contesto delle moderne produzioni manifatturiere. La crescente complessità delle macchine e dei processi industriali richiede un approccio tecnologicamente avanzato, mirato a garantire efficienza, precisione e sicurezza. Questo articolo analizza in modo approfondito l’applicazione dei metodi automatizzati e dei sistemi di controllo nell’assemblaggio di attrezzature industriali in metallo, sottolineando i benefici e le sfide di tale approccio.
Automazione nell’assemblaggio di attrezzature industriali in metallo: un approccio efficiente e innovativo
Automazione dell’assemblaggio di attrezzature industriali in metallo:
L’industria manifatturiera sta costantemente cercando soluzioni innovative per migliorare l’efficienza e ridurre i costi nell’assemblaggio di attrezzature industriali in metallo. L’introduzione della tecnologia di automazione si è dimostrata una risposta efficace a queste esigenze, offrendo un approccio efficiente ed innovativo.
L’automazione nell’assemblaggio di attrezzature industriali in metallo permette di ottenere numerosi vantaggi, tra cui:
- Aumento della produttività: L’automazione permette di accelerare le operazioni di assemblaggio, riducendo i tempi di produzione e aumentando la quantità di attrezzature che possono essere realizzate in un determinato periodo di tempo.
- Miglioramento della qualità: Grazie all’uso di macchine e robot programmabili, l’assemblaggio diventa più preciso e uniforme, riducendo al minimo gli errori umani e garantendo una maggiore qualità del prodotto finito.
- Riduzione dei costi: L’automazione permette di ridurre i costi legati al lavoro manuale, l’utilizzo di risorse umane e gli sprechi di materiali, aumentando l’efficienza complessiva del processo.
L’uso di macchine e robot nell’assemblaggio di attrezzature industriali in metallo richiede una programmazione accurata e una sincronizzazione impeccabile tra i vari componenti dell’impianto. Questo richiede un approccio metodico e attento, che consideri tutte le possibili variabili e ottimizzi le operazioni in base alle necessità specifiche dell’assemblaggio.
Un elemento chiave nell’automazione dell’assemblaggio di attrezzature industriali è l’utilizzo di sensori intelligenti e sistemi di visione avanzati. Questi permettono alle macchine di riconoscere in maniera autonoma i componenti e le posizioni corrette, migliorando ulteriormente la precisione e la velocità delle operazioni di assemblaggio.
La formazione e l’aggiornamento costante del personale coinvolto nell’assemblaggio automatizzato sono fondamentali per garantire il corretto funzionamento e la manutenzione delle macchine e dei robot. Solo attraverso un adeguato training è possibile sfruttare al massimo tutte le potenzialità dell’automazione, garantendo la continuità e l’ottimalità delle operazioni di assemblaggio.
In conclusione, l’automazione nell’assemblaggio di attrezzature industriali in metallo rappresenta un approccio efficiente e innovativo per migliorare la produttività, la qualità e ridurre i costi. L’integrazione di macchine, robot e sensori intelligenti garantisce un assemblaggio preciso e uniforme, ottimizzando le operazioni in base alle specifiche esigenze dell’industria manifatturiera.
Vantaggi dell’automazione nell’assemblaggio di attrezzature industriali in metallo
L’automazione è diventata un elemento fondamentale nell’industria dell’assemblaggio di attrezzature industriali in metallo, offrendo una serie di vantaggi significativi per le imprese che decidono di implementarla. Questi vantaggi sono evidenti sia dal punto di vista produttivo che dalle prospettive economiche e di sicurezza. Vediamo più da vicino questi vantaggi che l’automazione offre in questa applicazione industriale specifica.
Aumento dell’efficienza produttiva
L’automazione consente di accelerare e migliorare significativamente il processo di assemblaggio di attrezzature industriali in metallo. I robot e le macchine automatizzate sono in grado di svolgere le attività ripetitive e noiose in modo rapido e preciso. Ciò comporta un aumento della produttività e una riduzione dei tempi morti, consentendo alle imprese di rispettare o addirittura superare i tempi di consegna richiesti dai clienti.
Maggiore qualità del prodotto
L’automazione riduce al minimo l’errore umano nell’assemblaggio delle attrezzature industriali in metallo. I robot programmabili eseguono le operazioni con precisione millimetrica, garantendo che i componenti siano posizionati esattamente dove devono essere. Ciò porta a una maggiore qualità del prodotto finale, riducendo al minimo la presenza di difetti o guasti che potrebbero compromettere le prestazioni o la sicurezza delle attrezzature.
Riduzione dei costi operativi
L’automazione dell’assemblaggio delle attrezzature industriali in metallo comporta una significativa riduzione dei costi operativi a lungo termine. Sebbene l’investimento iniziale possa sembrare elevato, l’eliminazione o la riduzione delle spese per la manodopera umana compensano ampiamente nel tempo. Inoltre, l’automazione consente alle imprese di ridurre al minimo gli sprechi di materiali e di ottimizzare l’utilizzo delle risorse, portando a un ulteriore risparmio economico.
Incremento della sicurezza dei lavoratori
Automatizzando l’assemblaggio delle attrezzature industriali in metallo, le imprese possono fornire un ambiente di lavoro più sicuro per i loro dipendenti. Eliminando o riducendo la presenza di attività fisicamente impegnative o rischiose, si riducono le possibilità di incidenti sul lavoro e di infortuni. Inoltre, i robot e le macchine automatizzate possono operare in ambienti ostili o pericolosi per gli esseri umani, contribuendo a preservare la salute e la sicurezza dei lavoratori.
Miglior utilizzo delle risorse
L’automazione consente alle imprese di sfruttare al meglio le risorse disponibili. I robot e le macchine automatizzate possono funzionare 24 ore su 24, 7 giorni su 7, senza subire fatica o bisogno di pause. Ciò significa che l’assemblaggio delle attrezzature industriali in metallo può avvenire in modo continuo, senza interruzioni. Inoltre, grazie alla precisione e alla velocità dell’automazione, si riduce la quantità di materiale di scarto e le risorse vengono sfruttate in modo più efficiente.
Ottimizzazione della capacità produttiva
L’automazione consente alle imprese di ottimizzare la propria capacità produttiva. Grazie alla velocità e alla precisione dei robot e delle macchine automatizzate, è possibile gestire volumi di produzione più elevati rispetto al lavoro manuale. Ciò consente alle imprese di soddisfare o superare la domanda di mercato, senza dover aumentare in modo significativo la forza lavoro. Di conseguenza, l’azienda può espandersi, acquisendo una posizione di leadership nel settore.
Innovazione tecnologica
L’automazione nell’assemblaggio delle attrezzature industriali in metallo porta con sé un’innovazione tecnologica significativa. Le imprese che adottano l’automazione sono spinte a compiere investimenti nella ricerca e sviluppo di nuove soluzioni e tecnologie per migliorare il processo produttivo. Ciò porta a una costante evoluzione del settore, consentendo alle aziende di rimanere competitive e all’avanguardia rispetto ai concorrenti.
Tecniche e metodologie per l’automazione dell’assemblaggio di attrezzature industriali in metallo
Nel settore manifatturiero, l’automazione dell’assemblaggio di attrezzature industriali in metallo sta diventando sempre più rilevante. L’utilizzo di tecnologie avanzate e metodologie innovative consente di aumentare l’efficienza, la precisione e la sicurezza dei processi produttivi. In questa sezione, esploreremo alcune delle tecniche e delle metodologie utilizzate per automatizzare l’assemblaggio di attrezzature industriali in metallo.
Tecniche di automazione:
- L’utilizzo di robot industriali: i robot possono essere programmati per eseguire lavori di assemblaggio ripetitivi e complessi, garantendo una maggiore velocità e precisione rispetto al lavoro manuale.
- Sistemi di visione artificiale: i sistemi di visione possono essere utilizzati per riconoscere, localizzare e ispezionare i componenti delle attrezzature industriali, migliorando la precisione e l’efficienza dell’assemblaggio.
Metodologie per l’assemblaggio:
- Linee di produzione modulari: l’utilizzo di linee di produzione modulari consente di assemblare le attrezzature industriali in fasi separate, migliorando la flessibilità e la gestione del processo di assemblaggio.
- Sistemi di alimentazione automatizzati: l’uso di sistemi di alimentazione automatizzati permette il trasporto e l’ordine preciso dei componenti, riducendo i tempi morti e migliorando l’efficienza del processo di assemblaggio.
Vantaggi dell’automazione dell’assemblaggio di attrezzature industriali in metallo:
- Aumento della produttività: l’automazione può ridurre i tempi di ciclo e aumentare il numero di unità prodotte, aumentando la produttività complessiva dell’azienda.
- Miglioramento della qualità: grazie all’automazione, è possibile ridurre gli errori umani e garantire un assemblaggio preciso dei componenti, migliorando la qualità finale delle attrezzature industriali.
- Maggiore sicurezza: l’automazione elimina o riduce la necessità di operazioni manuali pericolose, migliorando la sicurezza dei lavoratori.
Sfide e considerazioni:
- Investimento iniziale: l’implementazione dell’automazione richiede un investimento significativo in attrezzature, tecnologie e formazione del personale.
- Sviluppo e manutenzione delle tecnologie: le tecnologie di automazione richiedono un costante sviluppo e manutenzione per adattarsi alle nuove esigenze e alle sfide del settore manifatturiero.
Conclusioni:
L’automazione dell’assemblaggio di attrezzature industriali in metallo rappresenta un metodo efficace per migliorare l’efficienza, la precisione e la sicurezza dei processi produttivi. L’utilizzo di tecniche e metodologie innovative può portare a vantaggi significativi per le aziende manifatturiere, aumentando la produttività e la qualità delle attrezzature industriali prodotte.
Integrazione dei sistemi di controllo nella produzione di attrezzature industriali in metallo
L’ rappresenta un passo fondamentale per garantire la qualità e l’efficienza dei processi produttivi. Grazie a tecnologie avanzate e all’utilizzo di sensori e dispositivi intelligenti, l’intero ciclo produttivo può essere ottimizzato e monitorato in tempo reale.
Uno degli aspetti chiave dell’integrazione dei sistemi di controllo è la raccolta e l’analisi dei dati produttivi. Attraverso l’implementazione di sensori, è possibile rilevare in modo accurato e continuativo le variabili di processo, come temperatura, pressione, velocità di rotazione e altre misure rilevanti. Questi dati sono quindi trasmessi e archiviati in un sistema centralizzato, permettendo ai responsabili di produzione di effettuare analisi dettagliate e prendere decisioni in tempo reale.
Un altro vantaggio dell’integrazione dei sistemi di controllo è la possibilità di automatizzare alcune fasi del processo produttivo. Grazie a algoritmi intelligenti, è possibile programmare macchine e robot per eseguire determinate attività con precisione e rapidità. Questo non solo riduce la dipendenza dal fattore umano, ma aumenta anche l’efficienza e la coerenza del risultato finale.
L’integrazione dei sistemi di controllo non si limita solo alla fase di produzione, ma coinvolge anche la gestione delle risorse e la manutenzione delle attrezzature. Attraverso l’utilizzo di software avanzati, è possibile monitorare lo stato delle macchine e pianificare interventi di manutenzione preventiva. Ciò riduce il rischio di guasti improvvisi e aumenta la durata e l’affidabilità delle attrezzature industriali.
Grazie all’utilizzo di schede di diagnostica e dashboard personalizzate, i responsabili di produzione possono monitorare i parametri chiave dei processi produttivi in tempo reale. Questa visualizzazione intuitiva e personalizzabile consente una rapida identificazione di eventuali anomalie o inefficienze, facilitando l’implementazione di misure correttive immediate.
Un altro aspetto importante dell’integrazione dei sistemi di controllo è la possibilità di creare una connessione diretta con i fornitori di attrezzature e materiali. Questo consente una pianificazione più accurata della produzione, evitando ritardi e disallineamenti nella catena di approvvigionamento. Inoltre, la condivisione dei dati tra produttori e fornitori facilita la collaborazione e la condivisione della conoscenza tecnica.
Infine, non bisogna sottovalutare gli impatti positivi dell’integrazione dei sistemi di controllo sulla sicurezza degli operatori. Attraverso l’utilizzo di dispositivi di sicurezza e protocolli di monitoraggio, è possibile ridurre il rischio di incidenti sul lavoro e garantire un ambiente di lavoro più sicuro.
In conclusione, l’ rappresenta un passaggio cruciale verso l’innovazione e l’ottimizzazione dei processi. Grazie a tecnologie avanzate e al supporto di sensori e software intelligenti, è possibile aumentare la qualità, l’efficienza e la sicurezza nella produzione di attrezzature industriali in metallo.
Analisi dei rischi e delle opportunità nell’automazione dell’assemblaggio di attrezzature industriali in metallo
L’automazione dell’assemblaggio di attrezzature industriali in metallo è un processo complesso che offre diverse opportunità e comporta anche una serie di rischi che devono essere attentamente valutati. In questo articolo, esploreremo i principali rischi e opportunità legati a questa forma di automazione, fornendo una panoramica completa sull’argomento.
Rischi:
1. Problemi di integrazione: L’integrazione delle diverse macchine e processi nell’automazione dell’assemblaggio può essere una sfida complessa. La mancanza di coerenza e compatibilità può portare a malfunzionamenti e ritardi nell’intero processo di produzione.
2. Rischio tecnologico: L’utilizzo di tecnologie avanzate come robot e sistemi di visione può comportare rischi tecnologici. Guasti tecnici o malfunzionamenti del software possono causare ritardi nella produzione e richiedere costose riparazioni.
3. Rischio di riduzione della forza lavoro: L’automazione dell’assemblaggio può comportare una riduzione della forza lavoro umana. Ciò potrebbe portare a problemi di gestione del personale e richiedere la riqualificazione o ricollocazione dei dipendenti coinvolti nel processo di assemblaggio.
Opportunità:
1. Maggiore efficienza: L’introduzione dell’automazione nell’assemblaggio delle attrezzature industriali può portare a un aumento significativo dell’efficienza produttiva. I robot possono lavorare 24 ore su 24 senza necessità di riposo, riducendo i tempi morti e aumentando la produttività complessiva.
2. Migliore qualità: L’automazione dell’assemblaggio riduce la possibilità di errori umani, garantendo una maggiore precisione e coerenza nei processi produttivi. Questo porta a una migliore qualità dei prodotti finiti e contribuisce a costruire una solida reputazione aziendale.
3. Riduzione dei costi: L’automazione può comportare una riduzione dei costi complessivi di produzione. La riduzione del lavoro umano, la maggiore efficienza e la riduzione degli errori contribuiscono alla riduzione dei costi operativi e dei tempi di produzione.
4. Miglioramento delle condizioni di lavoro: L’automazione permette di spostare le attività più faticose e ripetitive dai lavoratori umani ai robot. Ciò migliora le condizioni di lavoro generale e riduce il rischio di lesioni correlate alle attività ripetitive o pericolose.
Linee guida per un’implementazione efficace dell’automazione e controllo nell’assemblaggio di attrezzature industriali in metallo
Nell’ambito dell’assemblaggio di attrezzature industriali in metallo, l’implementazione di sistemi di automazione e controllo rappresenta un elemento fondamentale per ottimizzare i processi produttivi e garantire elevati livelli di efficienza e qualità. Di seguito sono presentate alcune linee guida da seguire per una corretta e efficace implementazione di tali sistemi.
1. Analisi dei requisiti: Prima di procedere con l’implementazione dell’automazione e controllo, è indispensabile effettuare un’attenta analisi dei requisiti specifici dell’assemblaggio delle attrezzature industriali in metallo. Ciò includerà lo studio delle caratteristiche dei componenti, dei processi di montaggio e delle esigenze di controllo necessarie per raggiungere gli obiettivi di produttività e qualità.
2. Scelta dei sistemi: In base all’analisi dei requisiti, è fondamentale selezionare i sistemi di automazione e controllo più adatti. Ciò implica valutare attentamente le caratteristiche dei dispositivi e dei software disponibili sul mercato, considerando fattori come la compatibilità con gli altri componenti del sistema produttivo, la facilità di integrazione e la loro affidabilità.
3. Progettazione e sviluppo: Una volta selezionati i sistemi di automazione e controllo, è necessario procedere con la progettazione dettagliata e lo sviluppo degli algoritmi e dei programmi necessari per il corretto funzionamento degli stessi. Questa fase richiede competenze specifiche nel campo dell’ingegneria e dell’informatica, al fine di garantire l’ottimizzazione dei processi di assemblaggio e il raggiungimento degli obiettivi prefissati.
4. Integrazione con il sistema produttivo: Una volta completato lo sviluppo dei sistemi di automazione e controllo, è necessario procedere con l’integrazione di tali sistemi all’interno dell’intero sistema produttivo. Questo richiede un’attenta pianificazione e coordinazione tra i diversi reparti dell’azienda, al fine di minimizzare i tempi di fermo produttivo e garantire una transizione senza intoppi.
5. Testing e validazione: Prima di mettere in funzione i sistemi di automazione e controllo sull’intera linea di assemblaggio, è necessario effettuare un rigoroso processo di testing e validazione. Ciò implica la verifica del corretto funzionamento delle funzionalità di automazione e controllo, nonché l’analisi di eventuali anomalie o malfunzionamenti che potrebbero compromettere la produzione.
6. Monitoraggio e manutenzione: Una volta completata l’implementazione e validazione dei sistemi di automazione e controllo, è fondamentale istituire un adeguato sistema di monitoraggio e manutenzione periodica. Ciò consentirà di individuare tempestivamente eventuali guasti o anomalie nel funzionamento dei sistemi e intervenire prontamente per garantire continuità produttiva ed efficienza ottimale.
7. Formazione del personale: Parallelamente all’implementazione dei sistemi di automazione e controllo, è essenziale fornire una formazione adeguata al personale coinvolto nell’assemblaggio delle attrezzature industriali in metallo. Questo permetterà loro di acquisire le competenze necessarie per utilizzare correttamente i sistemi implementati e sfruttarne appieno i vantaggi in termini di efficienza e qualità.
8. Continua ricerca e miglioramento: Infine, l’implementazione di sistemi di automazione e controllo nell’assemblaggio di attrezzature industriali in metallo richiede un’impegno costante nella ricerca di nuove tecnologie e nell’adozione di nuove soluzioni per migliorare ulteriormente i processi produttivi e raggiungere risultati sempre più soddisfacenti.
Sfide e soluzioni nell’automazione e controllo dell’assemblaggio di attrezzature industriali in metallo
L’assemblaggio di attrezzature industriali in metallo rappresenta una delle sfide principali per le aziende manifatturiere. La complessità dei componenti e la necessità di garantire precisione e affidabilità richiedono soluzioni avanzate nel campo dell’automazione e del controllo. In questo articolo, esploreremo le principali sfide che le aziende devono affrontare e quali soluzioni si possono adottare per ottimizzare il processo.
Sfida 1: Precisione nell’allineamento dei componenti
L’allineamento accurato dei componenti durante l’assemblaggio è fondamentale per garantire un funzionamento senza intoppi delle attrezzature industriali. Le sfide in questo ambito possono includere la variazione delle tolleranze dimensionali e la complessità dei collegamenti. Per affrontare questa sfida, le aziende possono adottare soluzioni come l’utilizzo di robot e sensori di visione avanzati per assicurare un allineamento preciso e ridurre al minimo gli errori umani.
Sfida 2: Gestione dell’ergonomia e sicurezza degli operatori
L’assemblaggio di attrezzature industriali in metallo richiede spesso sforzi fisici considerevoli da parte degli operatori. La gestione dell’ergonomia e della sicurezza è cruciale per garantire il benessere degli operatori e ridurre il rischio di infortuni sul lavoro. Le soluzioni possono includere l’utilizzo di dispositivi di assistenza ergonomica, come bracci meccanici o sistemi di sollevamento automatici, e la formazione adeguata degli operatori per garantire il corretto utilizzo degli strumenti.
Sfida 3: Monitoraggio e controllo in tempo reale
Per garantire il corretto funzionamento delle attrezzature industriali, è essenziale monitorare e controllare il processo di assemblaggio in tempo reale. Questo richiede sistemi di monitoraggio e controllo che possano rilevare eventuali anomalie o guasti durante il processo. L’adozione di sensori intelligenti, uniti a sistemi di analisi dati avanzati, permette di identificare in anticipo eventuali problemi, riducendo al minimo le interruzioni operative.
Sfida 4: Automazione del processo di assemblaggio
L’automazione è una soluzione chiave per migliorare l’efficienza e la produttività nell’assemblaggio di attrezzature industriali. L’implementazione di robot industriali, sistemi di trasporto automatizzati e stazioni di lavoro intelligenti consente di ridurre il tempo di assemblaggio e aumentare la precisione. È inoltre possibile integrare sistemi di programmazione avanzata che permettono l’automazione di compiti complessi e ripetitivi.
Sfida 5: Integrazione dei processi di assemblaggio
L’integrazione dei processi di assemblaggio è un’altra sfida critica. Gli operatori possono dover lavorare su componenti provenienti da diverse linee di produzione o fornitori esterni, creando difficoltà nell’organizzazione e pianificazione delle attività. L’adozione di sistemi di gestione dell’informazione e dell’integrazione dei processi permette di ottimizzare la catena di approvvigionamento e migliorare la tracciabilità dei componenti durante l’assemblaggio.
Sfida 6: Qualità e conformità normativa
Garantire la qualità e la conformità normativa delle attrezzature assemblate è fondamentale per evitare costi extra e garantire la sicurezza e l’affidabilità dei prodotti finali. L’adozione di sistemi di ispezione avanzati, come macchine a visione, e l’utilizzo di software di controllo di qualità permettono di individuare difetti e verificare la conformità normativa durante il processo di assemblaggio.
Sfida 7: Gestione dell’energia e sostenibilità
L’assemblaggio di attrezzature industriali richiede un uso intensivo di energia, creando sfide in termini di sostenibilità ambientale. Le aziende possono adottare soluzioni energetiche intelligenti per ridurre il consumo e migliorare l’efficienza energetica, come l’utilizzo di motori a efficienza energetica e sistemi di recupero dell’energia.
Sfida 8: Adattamento al progresso tecnologico
Con l’avanzamento tecnologico sempre in corso, le aziende devono affrontare la sfida di rimanere aggiornate e adattarsi ai nuovi sviluppi nell’automazione e nel controllo dell’assemblaggio di attrezzature industriali. La formazione continua degli operatori e il costante monitoraggio delle nuove tecnologie permettono alle aziende di sfruttare al meglio le opportunità offerte dalle soluzioni più recenti e restare competitive sul mercato.
Requisiti di formazione e competenze per l’automazione e controllo nell’assemblaggio di attrezzature industriali in metallo
1. Conoscenza dei processi di produzione:
Un solido bagaglio di conoscenze riguardante i processi di produzione nell’industria metalmeccanica è fondamentale. Questo include la comprensione dei cicli di lavorazione, il funzionamento delle macchine utensili, le tecniche di saldatura e sinterizzazione, nonché la conoscenza dei materiali metallici e delle loro proprietà.
2. Competenze nell’automazione industriale:
La capacità di lavorare con sistemi di automazione industriale è essenziale per assicurare un assemblaggio efficiente delle attrezzature. Questo richiede la conoscenza dei dispositivi di controllo, dei sensori e degli attuatori utilizzati nel settore, così come la capacità di programmazione e di utilizzo dei software di automazione.
3. Capacità di programmazione:
Un buon programmatore è in grado di creare e personalizzare software di controllo specifici per le attrezzature industriali in metallo. La conoscenza di linguaggi di programmazione come C++, Java o PLC (Programmable Logic Controller) è fondamentale per svolgere con successo questo compito.
4. Abilità di analisi e risoluzione dei problemi:
Nell’assemblaggio di attrezzature industriali in metallo, possono sorgere diversi imprevisti che richiedono competenze di analisi e risoluzione dei problemi. Un professionista in questo settore deve essere in grado di identificare e diagnosticare guasti, oltre a proporre soluzioni appropriate in modo tempestivo.
5. Conoscenza di sistemi di controllo e sicurezza:
La padronanza delle tecnologie di controllo e sicurezza è essenziale per garantire un ambiente di lavoro sicuro e conforme alle normative. Ciò include la conoscenza delle norme e degli standard di sicurezza, nonché la capacità di configurare e installare dispositivi di sicurezza, come interruttori di emergenza o barriere fotoelettriche.
6. Competenze nel testing e nella diagnostica:
La verifica delle prestazioni delle attrezzature industriali in metallo richiede competenze nel testing e nella diagnostica. Un professionista in questo ambito deve essere in grado di utilizzare strumenti specifici per verificare il corretto funzionamento dei sistemi di automazione e individuare eventuali difetti o malfunzionamenti.
7. Capacità di lavorare in team:
In un ambiente industriale complesso, la collaborazione efficace con colleghi e altri reparti è fondamentale. Un professionista in automazione e controllo deve essere in grado di comunicare in modo chiaro, di adattarsi a diverse dinamiche di gruppo e di lavorare in modo sinergico per raggiungere gli obiettivi comuni.
8. Aggiornamento continuo:
Per rimanere al passo con le ultime tecnologie e metodologie nel campo dell’automazione e controllo, la volontà di imparare e l’aggiornamento continuo sono indispensabili. Partecipare a corsi di formazione, workshop o conferenze nel settore può aiutare a migliorare le competenze e ad adattarsi ai progressi tecnologici.
Q&A
Q: Qual è l’importanza dell’automazione e del controllo nell’assemblaggio di attrezzature industriali in metallo?
A: L’automazione e il controllo sono di fondamentale importanza per garantire un processo di assemblaggio efficiente ed accurato delle attrezzature industriali in metallo. Grazie a questi sistemi, è possibile ridurre gli errori umani e migliorare la qualità del prodotto finale.
Q: Quali vantaggi offre l’automazione nell’assemblaggio di attrezzature industriali in metallo?
A: L’automazione permette di aumentare la velocità di produzione, riducendo i tempi di fermo macchina e favorendo la massima produttività. Inoltre, consente di garantire una maggiore precisione nell’assemblaggio e di ridurre i costi di manodopera.
Q: Quali sono i principali sistemi di controllo utilizzati nell’assemblaggio di attrezzature industriali in metallo?
A: I principali sistemi di controllo utilizzati sono i PLC (Programmable Logic Controller) e i CNC (Computer Numerical Control). Questi permettono di gestire in modo automatico le varie fasi dell’assemblaggio, garantendo una sequenza corretta e ottimizzata dei processi.
Q: Come vengono applicati i sistemi di automazione e controllo nell’assemblaggio di attrezzature industriali in metallo?
A: I sistemi di automazione e controllo vengono applicati mediante l’utilizzo di sensori, attuatori e software dedicati. Questi componenti consentono di monitorare i processi, effettuare misurazioni precise e intervenire in tempo reale per correggere eventuali errori.
Q: Quali sono le sfide principali nell’implementazione dell’automazione e del controllo nell’assemblaggio di attrezzature industriali in metallo?
A: Le principali sfide possono includere la complessità delle attrezzature da assemblare, la necessità di integrare correttamente i vari componenti del sistema di automazione e controllo e la formazione del personale addetto all’utilizzo di tali sistemi.
Q: Come si ottiene un’ottimizzazione dei processi di assemblaggio grazie all’automazione e al controllo?
A: Grazie all’automazione e al controllo è possibile ottimizzare i processi di assemblaggio riducendo al minimo le inefficienze e gli errori umani. Questo permette di migliorare la produttività, ridurre i tempi di produzione e garantire una maggiore qualità del prodotto finale.
Q: Quali sono i benefici a lungo termine dell’automazione e del controllo nell’assemblaggio di attrezzature industriali in metallo?
A: I benefici a lungo termine includono un aumento della competitività dell’azienda grazie a una maggiore efficienza produttiva e una migliore qualità dei prodotti. Inoltre, l’automazione e il controllo consentono di ridurre i costi di manodopera a lungo termine.
Q: Quali sono le tendenze future nell’automazione e nel controllo nell’assemblaggio di attrezzature industriali in metallo?
A: Le tendenze future includono l’utilizzo di tecnologie avanzate come l’intelligenza artificiale e l’Internet of Things (IoT) per una maggiore interconnettività e monitoraggio remoto dei processi di assemblaggio. Inoltre, si prevede un maggior focus sull’ottimizzazione energetica e sulla sostenibilità nell’assemblaggio industriale.
Key Takeaways
In conclusione, l’automazione e il controllo nell’assemblaggio di attrezzature industriali in metallo sono diventati imprescindibili per garantire processi di produzione efficienti e affidabili. Grazie all’integrazione di sistemi avanzati, come robotica, sensori e software di gestione, le aziende del settore hanno ottenuto risultati significativi in termini di qualità, precisione e riduzione dei tempi di produzione.
L’automazione ha permesso di eliminare gli errori umani, aumentando la sicurezza sul luogo di lavoro e riducendo il rischio di incidenti. Grazie alla capacità dei robot di eseguire ripetutamente compiti complessi con estrema precisione, si è assistito a un miglioramento della qualità dei prodotti finiti, riducendo al minimo gli scarti e gli sprechi di materiali.
Inoltre, l’automazione ha consentito di accelerare i tempi di produzione, fornendo ai clienti attrezzature industriali pronte all’uso in tempi più brevi. Ciò ha contribuito ad aumentare la competitività delle aziende sul mercato, consentendo loro di soddisfare le esigenze dei clienti in modo più rapido ed efficiente.
L’impiego di sistemi di controllo avanzati ha permesso di monitorare costantemente il processo di assemblaggio, rilevando eventuali anomalie o guasti in tempo reale. Questo ha consentito un intervento immediato per risolvere i problemi, minimizzando i tempi di fermo macchina e garantendo la continuità della produzione.
In conclusione, l’integrazione di automazione e controllo nell’assemblaggio di attrezzature industriali in metallo è una scelta strategica per le aziende che desiderano migliorare l’efficienza, l’affidabilità e la competitività dei propri processi produttivi. Investire in tecnologie all’avanguardia permette di ottenere risultati tangibili, garantendo una produttività ottimizzata e un elevato livello di soddisfazione dei clienti.
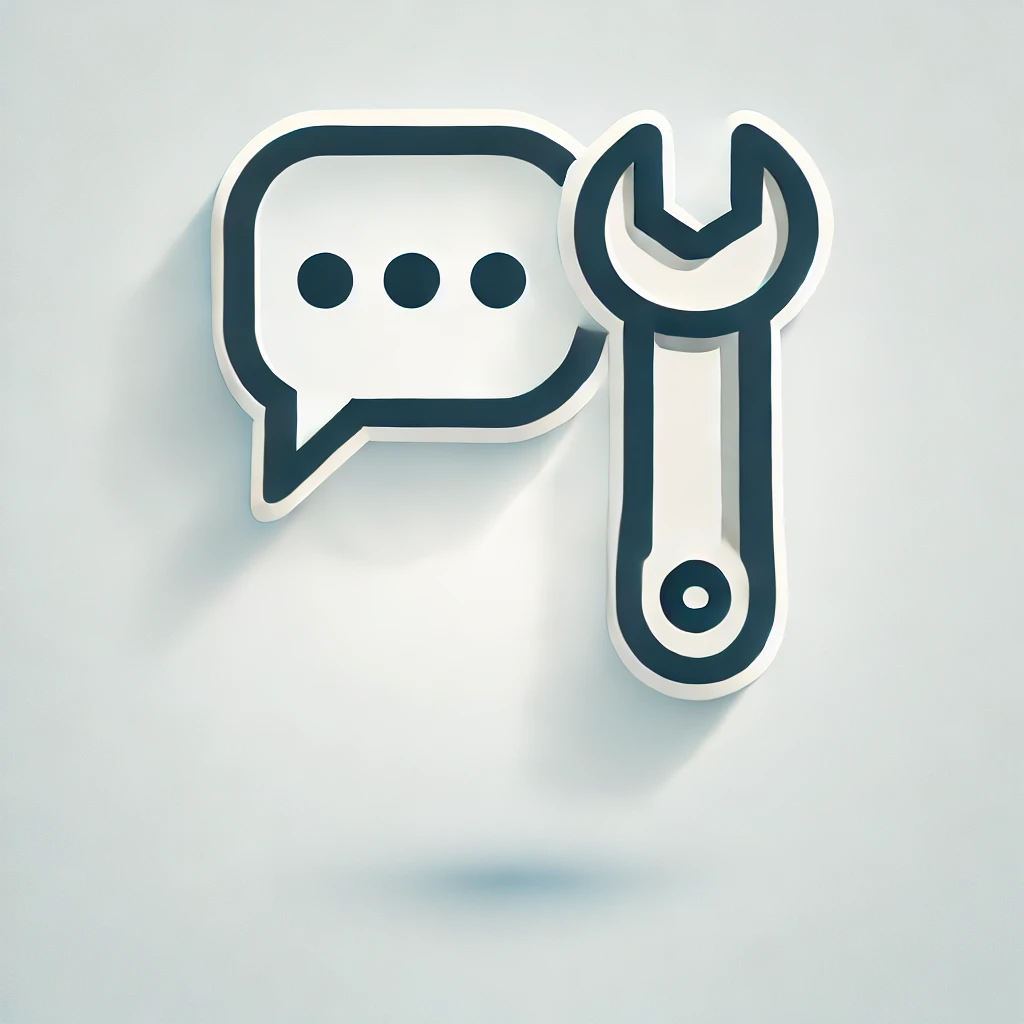
"Hai un'opinione tecnica o una domanda specifica? Non esitare, lascia un commento! La tua esperienza può arricchire la discussione e aiutare altri professionisti a trovare soluzioni. Condividi il tuo punto di vista!"
Partecipa!
Commenti